3D Lab, headquartered in Warsaw, Poland, is a pioneering company specializing in the field of Additive Manufacturing and metal powder production. Their core expertise lies in developing advanced equipment for the production of high-quality, spherical metal powders, designed for various applications in industries such as aerospace, healthcare, and jewelry. The company focuses on innovative solutions that encompass the entire production process, from atomization to post-processing of metal powders, ensuring the highest standards of quality and efficiency.
Interview with Jakub Rozpendowski, CEO of 3D Lab.
Easy Engineering: What are the main areas of activity of the company?
Jakub Rozpendowski: Our primary activities include the development and manufacturing of equipment for metal powder production. We offer a range of products like ATO Lab Plus, ATO Noble, and various feeding systems, each tailored to specific manufacturing needs. These products cater to both research and industrial applications, providing solutions for the production of a diverse range of metal powders, including reactive and non-reactive materials. We also represent 3D Systems and 2OneLab. We offer a range of 3D printing devices, catering to various needs and specifications. Additionally, we provide specialized services to support processes in production environments. This includes training and implementation of these advanced technologies to ensure smooth integration and optimal use in specific production settings. We frequently provide various technologies that are optimized for collaborative functioning, designed as turnkey solutions. These solutions are tailored to ensure seamless integration and efficient operation across different processes and environments.
E.E: What’s the news about new products/services?
J.R: The introduction of the ATO Induction Melting System (IMS) and the ATO Cast has significantly expanded the capabilities of the ATO Lab Plus, offering new possibilities in the realm of Additive Manufacturing.
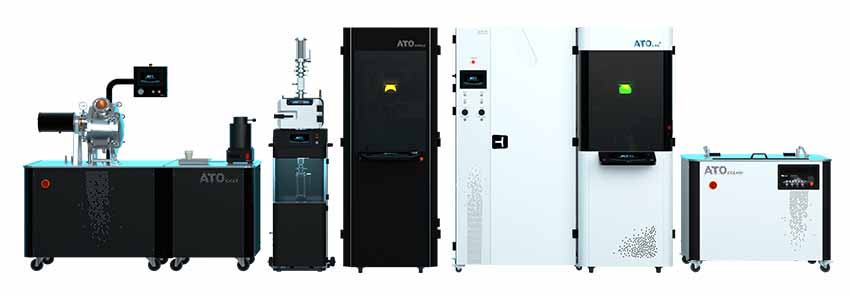
The ATO IMS is an induction melting powered ultrasonic atomization module, designed to seamlessly integrate with the ATO Lab Plus. This module is particularly adept at atomizing lower melting point metals, enhancing the range of materials that can be processed. It offers the flexibility of using either a crucible or one of the ATO Rod Feeders.
The ATO Cast is a device used in Additive Manufacturing for creating custom alloys with high purity. It functions as a vacuum casting furnace and is highly effective in producing a variety of alloys. This capability makes it extremely valuable in both research and production environments. The design of the ATO Cast focuses on reducing contamination of materials, ensuring that the chemical composition of the alloys remains unaltered. As a result, it becomes an essential tool for materials engineers who are investigating new combinations and possibilities of alloys.
The ATO IMS, with its ability to use crucibles, and the ATO Cast, with its casting capabilities, create a synergy that expands the range of materials available for Additive Manufacturing. These machines fosters a circular manufacturing approach. By allowing for the efficient reuse and recycling of materials, they significantly diminish material waste and associated costs. This is not only economically beneficial but also crucial for reducing the environmental footprint of the production process. In an era where sustainability is increasingly paramount, the ATO IMS and ATO Cast set a precedent for responsible and eco-conscious manufacturing, aligning with global trends towards more sustainable industrial practices.
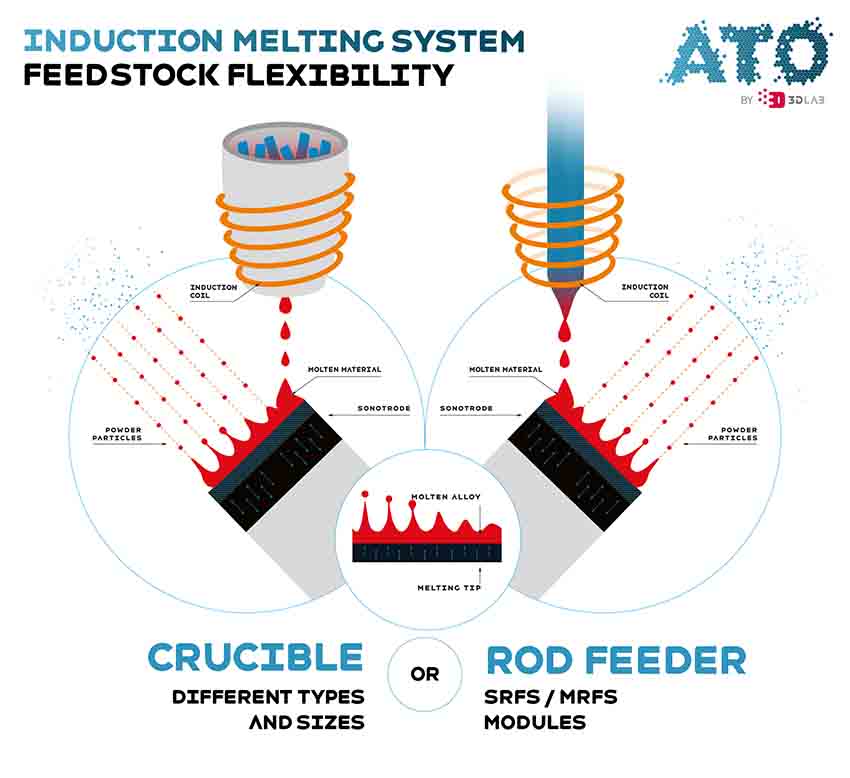
E.E: What are the ranges of products/services?
J.R: Our product range includes:
- ATO Lab Plus: ultrasonic lab-size metal powder atomizer.
- ATO Noble: atomizer designed for atomizing precious metals.
- ATO Cast: vacuum casting furnace for creating custom alloys and own casting.
- ATO Sieve: ultrasonic sieving station for sieve powder to desired PSD.
- ATO Clean: ultrasonic cleaner, offering an efficient, hands-free cleaning procedure for the atomizer components.
- Feeding Systems modules like Wire Feeding System (WFS), Single Rod Feeding System (SRFS), Multi Rod Feeding System (MRFS) and Induction Melting System (IMS) for ensure feedstock form flexibility.
- ATO Frequency Systems – ultrasonic modules for production different metal powder PSD.
- Wide range of 3D printers in many technologies including: DM, SLM, SLS, SLA, MJP, CJP, DLP, FDM.
- Peripherals: EDM, heat treatment, compress air stations, inert gas installations, welding machines, chillers, vacuum cleaners etc.
E.E: What is the state of the market where you are currently active?
J.R: Additive Manufacturing market and related technologies is experiencing significant growth and innovation. The demand for high-quality, customized metal powders for Additive Manufacturing is on the rise, driven by various industries like aerospace, healthcare, automotive, and jewelry. This demand is fostering advancements in metal powder production, atomization technology, and equipment efficiency.
The market trend is towards more compact, efficient, and versatile equipment that can cater to the specific needs of Additive Manufacturing. There is a growing focus on producing metal powders with high flowability and narrow Particle Size Distributions, essential for high-quality Additive Manufacturing applications. Additionally, the industry is increasingly embracing sustainable manufacturing practices, with a focus on recycling and minimizing waste.
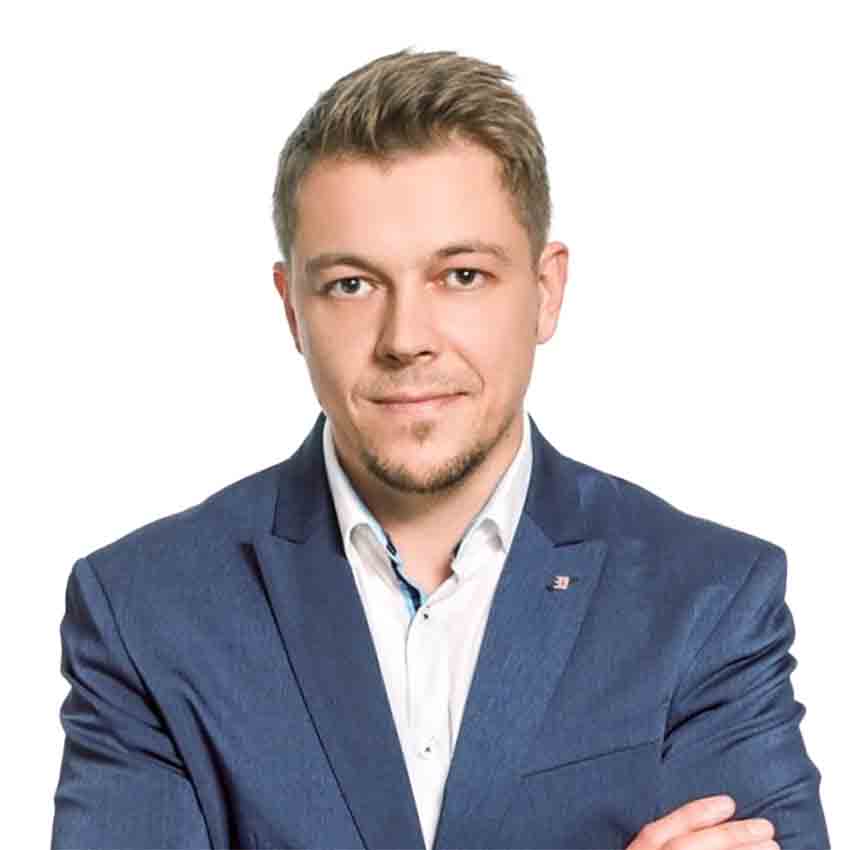
Overall, the state of the market is dynamic, with a strong push towards technological innovation, sustainability, and meeting the evolving needs of a diverse range of industries reliant on Additive Manufacturing.
E.E: What can you tell us about market trends?
J.R: The market is trending towards more sustainable manufacturing practices and the development of new alloys to meet specific industry needs. There is also a growing focus on producing finer, more consistent powders to improve the quality of 3D printed components.
E.E: What are the most innovative products/services marketed?
J.R: ATO Lab Plus: This is a state-of-the-art ultrasonic metal powder atomizer. It’s designed for the efficient production of both reactive and non-reactive metal powders on a smaller, self-sufficient scale. ATO Lab Plus stands out due to its compact design, which makes it suitable for use even in limited spaces, and its capability to produce high-quality powders with high flowability and a narrow Particle Size Distribution.
Induction Melting System (IMS): This is an optional module designed to enhance the capabilities of the ATO ultrasonic metal atomizers. The IMS is dedicated to ultrasonic atomization, efficiently powdering metals and alloys into fine, homogenous powder. It’s designed to atomize materials with low melting point minimizing elements evaporation, irregular shape feedstock, and is ideal for both research labs and Additive Manufacturing centers.
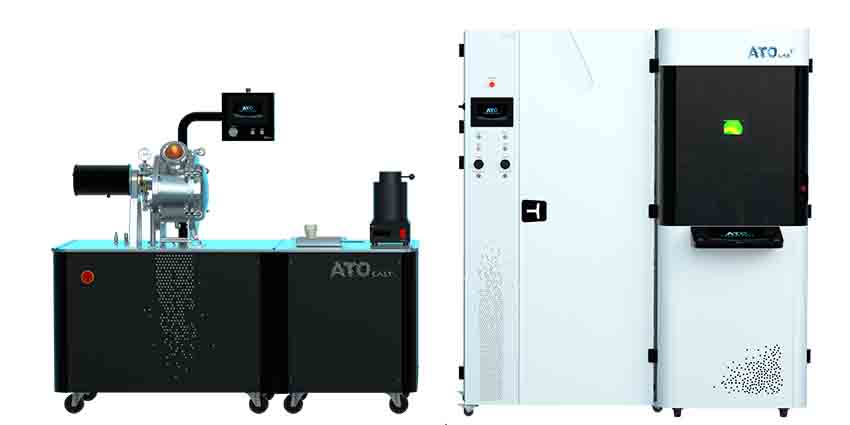
E.E: What estimations do you have for the beginning of 2024?
J.R: As we move into 2024, we anticipate a continued upward trajectory in the Additive Manufacturing sector. We expect to see an increased demand for specialized metal powders and a greater emphasis on custom solutions for specific industry applications. Our focus will be on expanding our product range and enhancing our technologies to keep pace with these evolving market demands.