ASSAN ALÜMINYUM, one of the leading flat rolled aluminum manufacturers in the world, has ordered 4 additional aluminum coil annealing furnaces, which are equipped with an even more efficient Vortex® 2.0 system. The company already owns 17 furnaces with SECO/WARWICK Vortex system.
Vortex 2.0 – a new level of quality in aluminum heat treatment
Vortex® is a highly effective system for aluminum coil annealing. In the latest version 2.0, the furnace is equipped with an improved nozzle system, which in turn produces increased heat transfer efficiency.
“Our R&D department (SECO/LAB) investigated different nozzle configurations and diameters. As a result of many tests, we achieved the goal of significantly reducing the load heating time. This is a big saving for users, because a shorter cycle ensures greater efficiency and, above all, savings. Vortex systems provide higher production volume with less energy consumption. Therefore, these furnaces are both economical to operate and environmentally-friendly at the same time,” explains Piotr Skarbiński, Vice President of the CAB and Aluminum Products Segment at the SECO/WARWICK Group.
17 Vortex systems in Turkey
SECO/WARWICK solutions for aluminum heat treatment are equipped with dedicated control systems and load transport equipment, which can be offered in various configurations, adapted to the specific requirements of production processes in end-user plants. Vortex is a guarantee of better heating temperature uniformity and the lack of local overheating on the coil surface, which significantly affects the final quality of the heat-treated material. The Vortex system, in addition to operating with a temperature uniformity +/- 3oC, provides a significant reduction in the total process time compared to traditional systems offered by competitors. It is therefore not surprising that SECO/WARWICK has already delivered seventeen such furnaces to Assan Alüminyum.
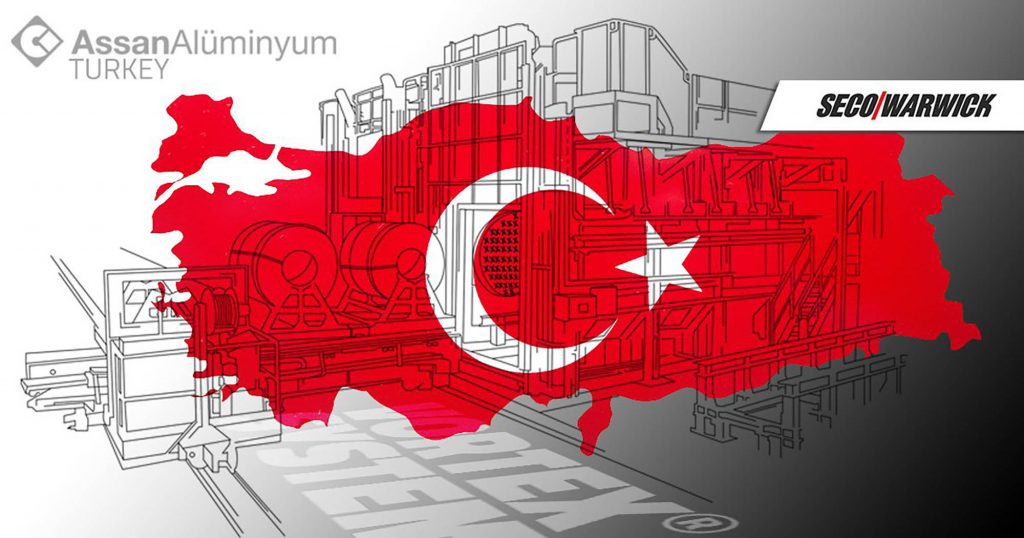
Assan ALÜMINYUM is one of the largest flat-rolled aluminum producers in the industry, providing products for industries such as construction, automotive, HVAC and packaging. It has been collaborating with SECO/WARWICK for many years, developing its production plant as a partner.
“In line with our core value of sustainability, we planned a series of sustainable expansion investments. As a part of these plans, we have chosen four, three-zone Vortex 2.0 systems which will fully meet the current needs related to aluminum heat treatment. The Vortex aluminum coil annealing furnace is a solution we know well. Its advantages related to improved energy and time efficiency cannot be underestimated. SECO/WARWICK is our long-term Partner, because the combination of ecology and economy is integral to the SECO/WARWICK philosophy and technology. The new, more efficient nozzle system will improve efficiency while maintaining excellent load parameters. This project is important in terms of the exchange of experience and knowledge with our partner, SECO/WARWICK,” commented Murat Akkaş, Senior Manager, Execution, Investment Projects at Assan ALÜMINYUM.
Vortex furnaces work for the largest aluminum heat treatment companies in the world. SECO/WARWICK supplies these systems to companies in Europe, Asia and both Americas.