ABAGY is AI & machine-vision-based software for industrial robots.
One of the major cost components in implementing a robot application is programming and integration, accounting for approximately 50-70% of the total expenses. This aspect has been a bottleneck hindering the widespread utilization of robots.
With ABAGY, the need for robot programming is eliminated. ABAGY automatically generates a robot program to produce a specific product. It takes minutes instead of hours, days, or even weeks.
Furthermore, the system employs machine vision to scan the parts and dynamically adjusts the robot’s trajectories based on the actual position and variations of the product.
ABAGY is revolutionizing the industrial robotics market by expanding the applicability of robots beyond serial production and into high-mix scenarios. The company challenges the conventional belief that robots are only suitable for mass-producing thousands of identical products, such as those found in the automotive or electronics industries. With ABAGY’s software, manufacturers can use the robots for custom projects or even one-of-a-kind parts.
Interview with Kate Degai, CMO at ABAGY.
Easy Engineering: What are the main areas of activity of the company?
Kate Degai: Although our technologies are versatile and capable of working with various production processes, our current focus is on robotic welding. This decision is primarily driven by the global shortage of welders. By the year 2024, the shortage of welders in the USA is projected to exceed 400,000 jobs. This shortage is due to factors such as the majority of welders being over 35 years old, coupled with the unpopularity of dangerous and demanding work among younger individuals.
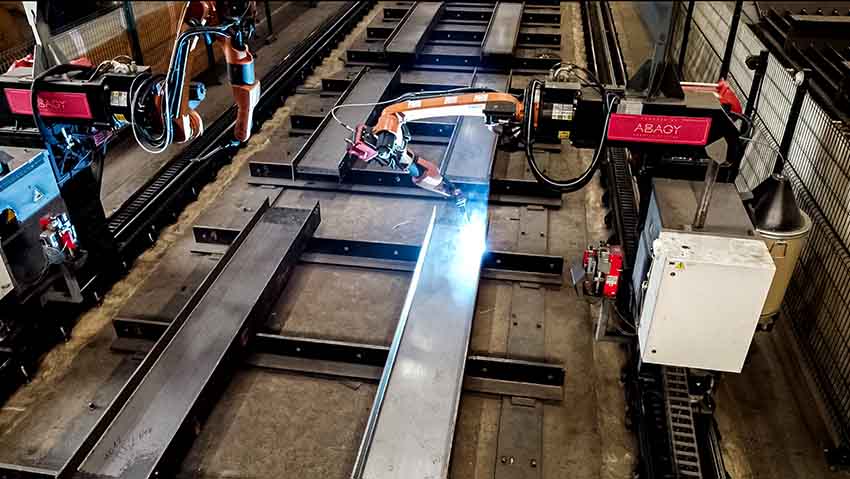
E.E: What’s the news about new products?
K.D: We are actively expanding our presence in the US market, and as part of our efforts, we have established a demo center near Chicago, IL. Our client and partner base in the USA continues to grow steadily. Also, we can announce our participation in the upcoming Fabtech event in September, where we will showcase our technologies.
E.E: What are the ranges of products?
K.D: We offer two main options: a turnkey solution for new robotic cells and a retrofit option for upgrading existing robotic cells.
Until 2022, ABAGY offered manufacturers a turnkey solution that included hardware and software.
In 2022, it was also decided to develop a product that would Retrofit already existing robotic cells, since the number of requests from those who wanted to increase the utilization of the robotic cell was significant.
The new product became possible due to the fact that ABAGY is compatible with various robots and welding equipment (Fanuc, Kuka, Yaskawa, Kawasaki, Panasonic, Miller, Lincoln, Fronius, Esab, Kempi, Ewm, Lorch, etc.).
Now, if a company wants to increase robotic cell utilization, all they need is to install ABAGY’s machine vision and software.
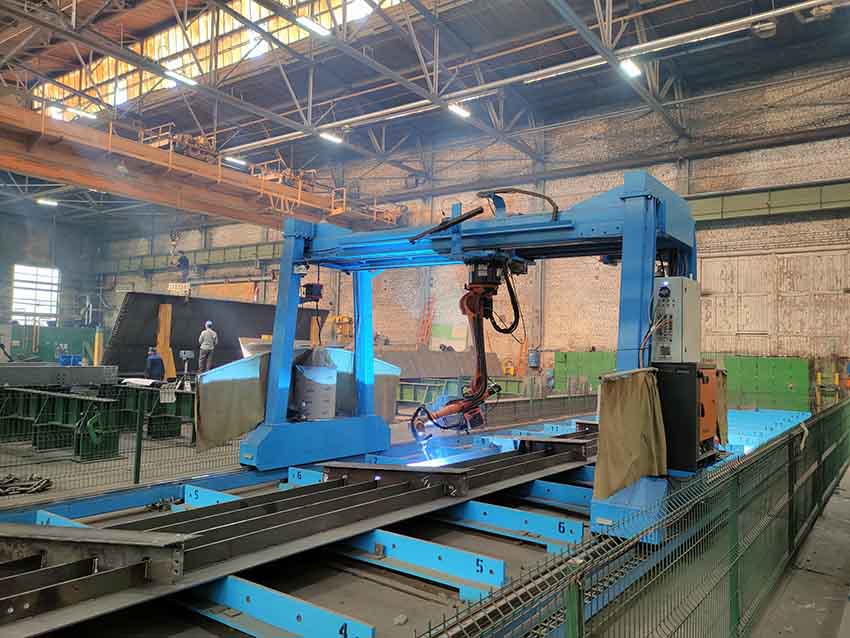
Case studies
Turnkey Solution. Steel Bridge Manufacturer
The company produces bridge structures 18-20 meters in length. From the point of view of traditional robotics, each of these is unique, since they are pre-assembled by hand and often don’t come out perfect. Also, due to their size, they can deform during the welding process when heated. Previously, all products were welded by hand, but a smart system with machine vision made it possible to use robots.
As a result:
- 2 robots instead of 10 welders
- 50+ part types per month in a single cell
- 3x cost reduction
- 5x throughput
After the first robotic cell, 2 more cells were installed.
Robotic Cell Retrofit. Processing Equipment Manufacturer
Sabetha Kansas production facility already had a robotic cell in use. However, it was used for a limited number of parts, because the programming was tedious. After implementing a new system with AI and machine vision, the setup time has been reduced dramatically – only 10-15 minutes for a new product – and the robot can now be used for many more products. That’s a big win for a manufacturer with high-mix production.
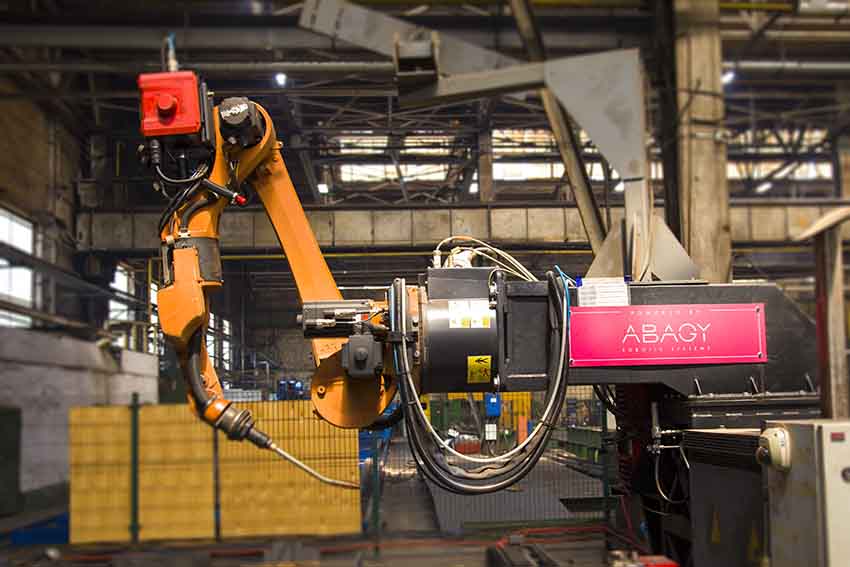
As a result:
- Any products. In the first month of the robotic cell’s operation company created 50 different technical charts;
- 10x programming time reduction. Previously, programming a robot for one rotor took 90-120 minutes. Now it takes 9-10 minutes;
- Ease of use. Now even a welder can set tasks for a robot in a few minutes.
E.E: At what stage is the market where you are currently active?
K.D: There is something called the “Industrial Robot Paradox.” While robots increase manufacturing effectiveness by five to 10 times, which has been proven for many years by car manufacturers, robots are still used only in 1% to 2% of cases. The International Federation of Robotics (IFR) estimates that the average global manufacturing robot density is 141 robots per 10,000 employees. In other words, only 1.41% of factories in the world use robots. Robot density in the United States was 274 units per 10,000 employees in 2021, i.e. 2.74%.
The Industrial Robot Paradox arises from various factors, primarily technological limitations that have hindered wider robot adoption. However, the recent emergence of new technologies enabling autonomous robots has presented a solution to this issue. Additionally, the pressing shortage of skilled labor has created a strong motivation for the implementation of robots. This combination of factors signifies a pivotal moment in the history of robotics.
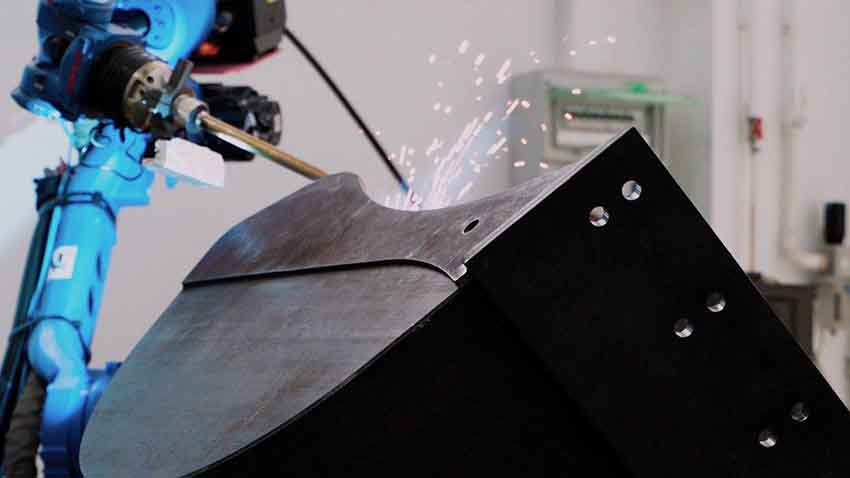
E.E: What can you tell us about market trends?
K.D: The biggest trend in robotics is adaptive, autonomous robots that do not require programming and, as a result, are applicable to high-mix, low-volume production. We see significant changes. Previously, it was difficult for us to explain to robot manufacturers what this technology even is because they have never seen the promise of working with it. But the environment is changing. Robot manufacturers have estimated that the high-mix market is significantly larger than the automotive industry. And more importantly, manufacturers in high-mix industries believed in it.
E.E: What are the most innovative products marketed?
K.D: We see the rapid development of vision devices, as well as the emergence of new functions for robots and welding sources. Hardware is getting smarter. As a result, our algorithms become more advanced.
AI is a very powerful tool, but it is extremely dependent on the amount and quality of data that the algorithms have to learn. And there are not enough good data sets, so it will take time to collect them.
Currently, there is a lot of buzz surrounding ChatGPT, and we also conducted some experiments with it. We tasked ChatGPT with writing programs for the Yaskawa robot and then tested them in our laboratory. The results yielded two successes and two failures. This experiment revealed that ChatGPT, in its present form, is far from being a viable replacement for advanced software like ABAGY. The latter has the ability to intelligently use machine vision and adapt to unexpected changes in part geometry, a feature currently missing from ChatGPT. As LLMs continue to evolve, it will be interesting to see how they can complement and enhance industrial robotics solutions.
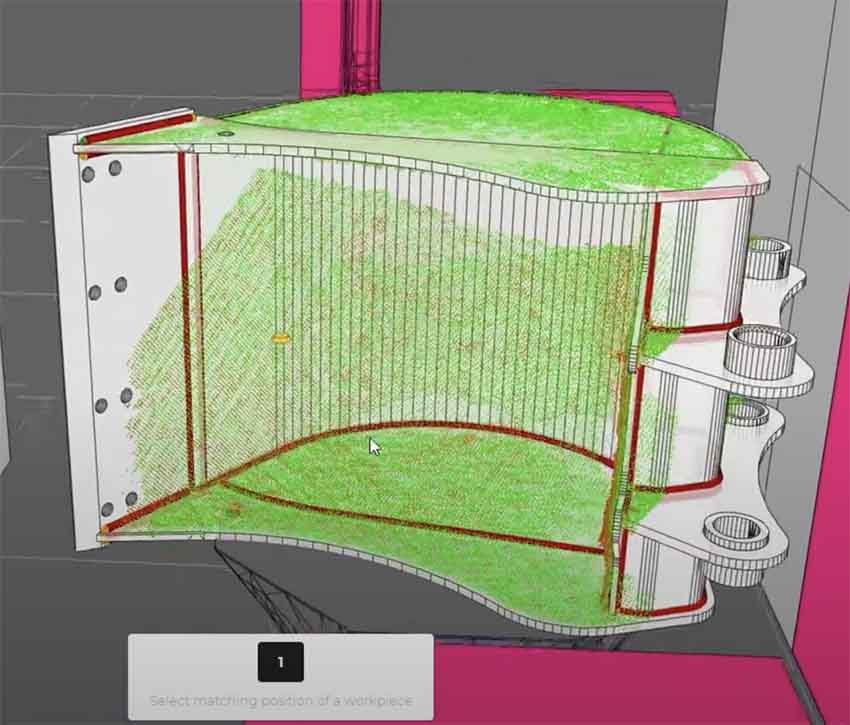
E.E: What estimations do you have for 2023?
K.D: We hold a positive outlook and anticipate a rise in installations within the United States. While the current economic situation poses challenges, two strategies are viable: either cutting costs to save or taking a proactive approach by investing in more effective tools. Despite the economic difficulties, it appears that more companies are opting for the latter approach.