Valvengineering was formed in 2007 to bring to market a range of hygienic valves qualitatively superior to the offerings currently on the market. The target markets are the pharmaceutical sector, fine chemicals, food and beverage, nutraceuticals and cosmetics. By manufacturing in Italy, they are able to ensure a higher product quality and a better response for customized valves. Valvengineering focusses on design, marketing, assembling and testing the valves that they sell. 99% of the components for the valves are manufactured by Valvengineering’s sister company Cosmec Italia, with whom they are co-located and who produces parts for the company and also for many other machine manufacturers in Valvengineering’s local area.
In this way all production process are in-house, which is a huge advantage for control of scheduling and quality. The company is completing their ISO Quality system certification which should be active from next January.
Easy Engineering: What are the most successful products in your line-up?
VALVENGINEERING: Our most successful and best-known product is the Compact series butterfly valve which combined with the high quality mechanical engineering of its production, has a number of distinctive design features which make it greatly appreciated by end users. This is a range of hygienic butterfly valves (which can also be offered as dosing valves, tablet valves or tablet dosing valves as it is a completely modular solution) available in sizes ranging from DN100 to DN300. These are offered with st/st 316L product contact parts and 304 all other parts. On demand they can also be supplied with Hastelloy C-22, st/st 904 and Alloy 59. Unlike most competitor products they are offered with TC ferrules as standard which means that no expensive proprietary flange connection is needed. This keeps costs down for the customer, and ensures the maximum flexibility when mating with other components in the stack up.
Other connections are also available. Various elastomers are available for seal materials and we offer full guidance to the user regarding the choice of elastomer for any given application. The valves can be manually operated or else we offer a complete range of automation options including pneumatic or electric actuators, positioners, limit switches and pilot valves and ATEX certification where necessary. The quality of finish is outstanding with a mirror polish of Ra<0.4um. Valves can also be supplied with passivation or Electropolish finish. A Full documents and certification package is available for all valves with material traceability information, FDA conformity, spare parts information, drawings and user manual. These comments regarding choice of elastomers and product finish apply equally to all valves in our range.

Another key product in our range is the Composite fine dosing valve which is now the preferred solution for pack-off systems in many large pharma machinery makers where dosing accuracy of 25g is required. Its distinctive patented design enables the user to set up highly optimized filling protocols which enable maximum dosing precision in minimum time. Unlike competitor products, the valve is available with various options such as a bridge breaker.
We offer many types of dosing valves and Feeder valves and can offer something for every imaginable powder flow control application up to and including feeder valves for vacuum transfer systems.
We have a hygienic butterfly valve specifically designed for full vacuum applications which also features particularly long seal lifetime
We have recently launched a Hygienic in-line lumpbreaker which is proving very popular with customers. This features an extremely robust chassis machined from solid including the screen and has an integrated motor support which covers the rotating drive shaft.
We have also upgraded and relaunched our range of powder sampling valves, so that we now offer both intrusive and non-intrusive valves in both manual and pneumatic operation. This year we have added a Reactor sampling system which is the best on the market.
Last, and by no means least we offer a complete range of silicone flexible connections including conical connections. These connect to the host by means of standard TC clamp which means they are an extremely practical and cost effective solution.
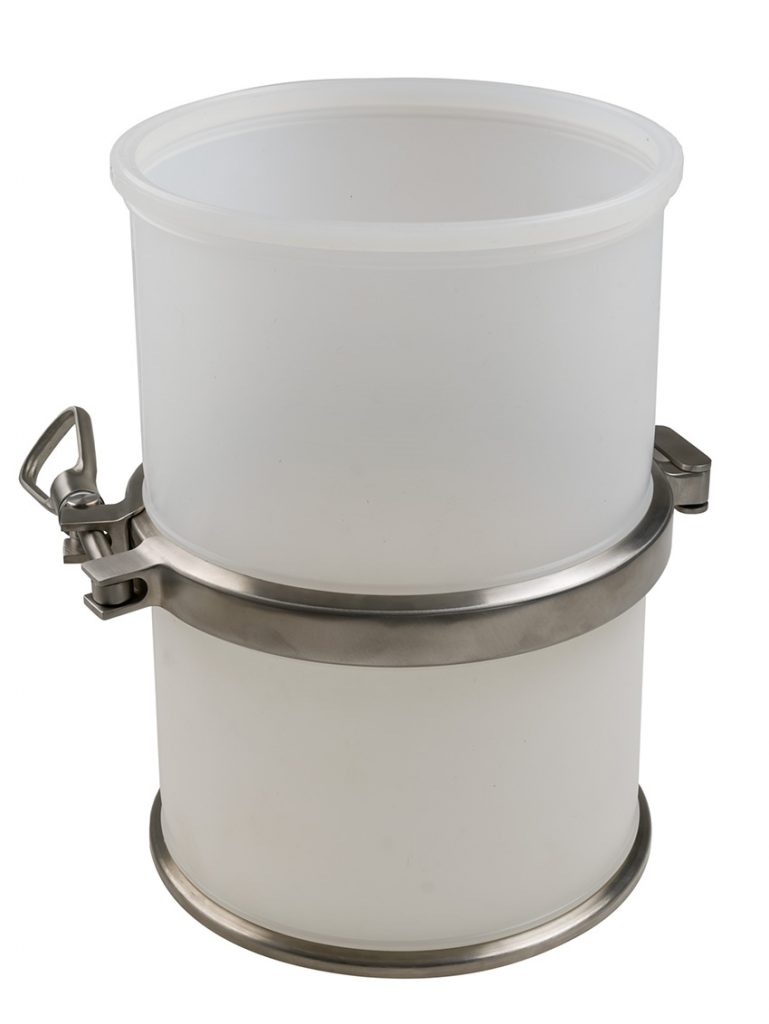
E.E: Tell us about the team in your company and how important is the human factor?
VALVENGINEERING: We are a small team of mostly young enthusiastic guys, highly motivated to giving customer satisfaction by thorough engineering and attentive logistics and quality control. We have a mixture of qualified engineers, experienced machining specialists and apprentices.
E.E: What can you tell us about products distribution?
VALVENGINEERING: Our products are distributed mostly via a network of distributors in US, UK, Spain, France & Singapore. In other markets we have a constantly growing number of direct customers. Our Outside Sales Manager looks after direct accounts in Italy, Switzerland and Germany. Key accounts and direct customers in other countries are managed by our head office.
E.E: What’s the client feedback for the best-selling products?
VALVENGINEERING: Our customers all recognize the superior design and build quality of our products compared to our competitors’. In addition, we make every effort always to act in an open, transparent and fair dealing manner, and for this too we have received compliments.
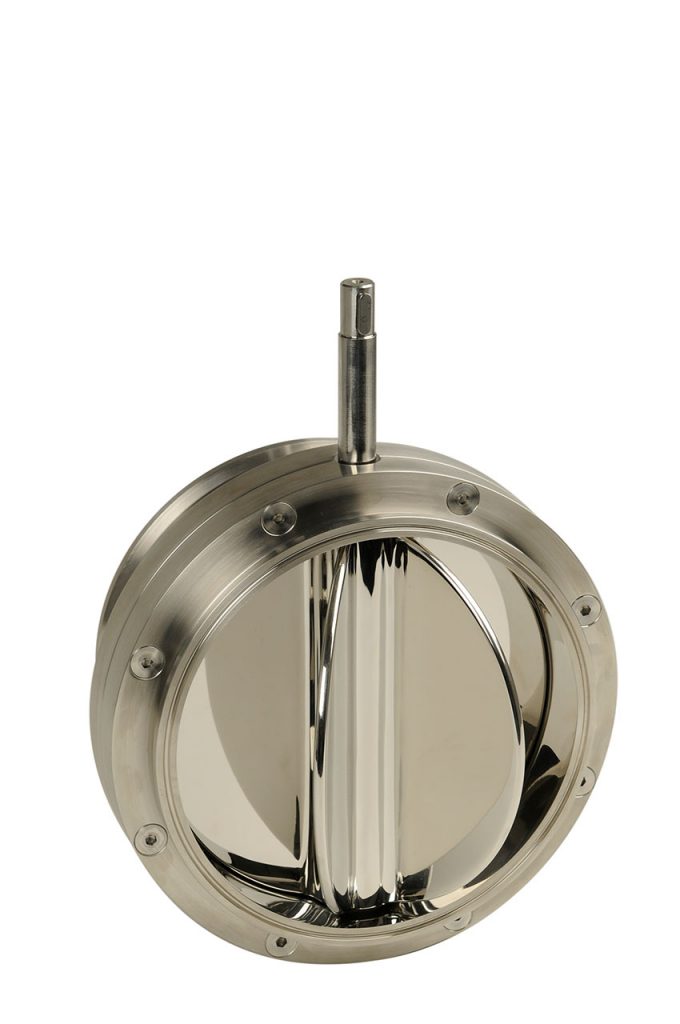
E.E: How does this feedback impact development of new products?
VALVENGINEERING: New product development is strongly driven by feedback from customers but even more so by requests from customers for particular features. This is not always easy but is often educational! Having produced many customized products in the past means that it happens quite often when a customer has a particular special request that we have already done something similar before and are able to propose convincing tried and tested solutions.
E.E: Tell us about the research and development in your company?
VALVENGINEERING: The Research and development process is concerned mostly with improvements to valve design to improve performance and simplify manufacture where this is compatible with maintaining product quality. We are always looking to improve valve performance in difficult environments, and in addition we are developing a split containment valve for API charging and discharging.
E.E: What is your company philosophy and what drives your company forward?
VALVENGINEERING: Our chief concern always is to aim for customer satisfaction with the product and with their experience working with us. We believe very firmly in building relationships of trust with our customers which enables us to focus on optimizing our product offering for them.
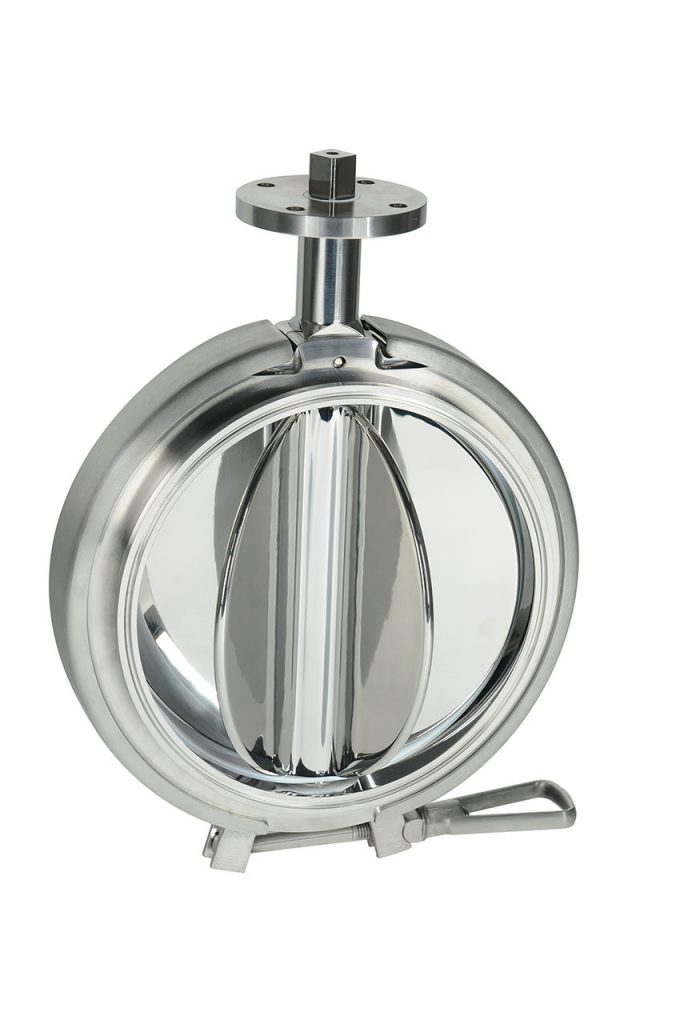
E.E: What guarantees success in your area of activity?
VALVENGINEERING: Nothing guarantees success, but we do our best through hard work and good relationships. A key ingredient to achieving successful projects is to gather as much information about the project as possible in terms of product and process conditions and the end user’s expectations about performance. It often happens that customers approach us asking for one type of valve, but after analysis of the process requirements we end up offering a different type of valve. This all helps build the customers’ confidence in our technical competence and good faith.
E.E: Give us some details about the after-sales service & customer support?
VALVENGINEERING: Aftersales service and customer support are managed either directly or via our distributors. For customers in Europe, we have on a number of occasions intervened directly on site, sometimes at very short notice. In all cases we have managed to resolve the problems that had presented themselves and in most cases, it as been an opportunity to improve relations with the customer rather than the opposite as our commitment to technical expertise and customer satisfaction is shown to be a fact and not just words in a mission statement.