Implementation of a packing solution in an existing production line of polycarbonate sheets.
Atis 160 + dispensador de tacos + alimentador auto – YouTube
Easy Engineering: What were the needs of the client?
PLASTICBAND: Our client needed an automatic line to apply polystyrene blocks and wrap all-in-one. Our client wanted to save time and extra movements of such a long and delicate product just to place blocks under the bundles to pick them up and load them, they also needed to protect and hold the sheets with stretch film to avoid any mark on the product.
E.E: Why did the client choose your products / solutions?
PLASTICBAND: Among other offers, we were the only company offering a full solution system from the end of their production line to the picking and loading area.
They liked our orbital wrappers because the versatility and speed as well as the small footprint despite is a big format machine but what they really needed was an engineering solution.
PLASTICBAND manufactures all machines in Barcelona with European quality standards, we also meet other countries requirements like UL.
Our commitment with the environment makes us to work every day in implementing green solutions in our factory like solar panels for the used electricity in our factory, use filtered rainwater for the strap lines and more.
E.E: What products / solutions were used?
PLASTICBAND: Side driven conveyors to move the material until the infeed driven conveyor, automatic polystyrene blocks dispenser, industrial wrapper, driven outfeed conveyor.
All synchronized by photocells and custom-made program for our client needs.
E.E: Please describe how was the project implemented?
PLASTICBAND: In our engineering projects we work closely with the factories workforce involved in manufacturing and packaging, we have meetings to hear what their needs are; then we develop a first project, once validated we start designing the line, we specify details and when the line is manufactured, we do a FAT with the client.
After all tests have been passed and approved our technicians go to their place to install and train customer’s operators.
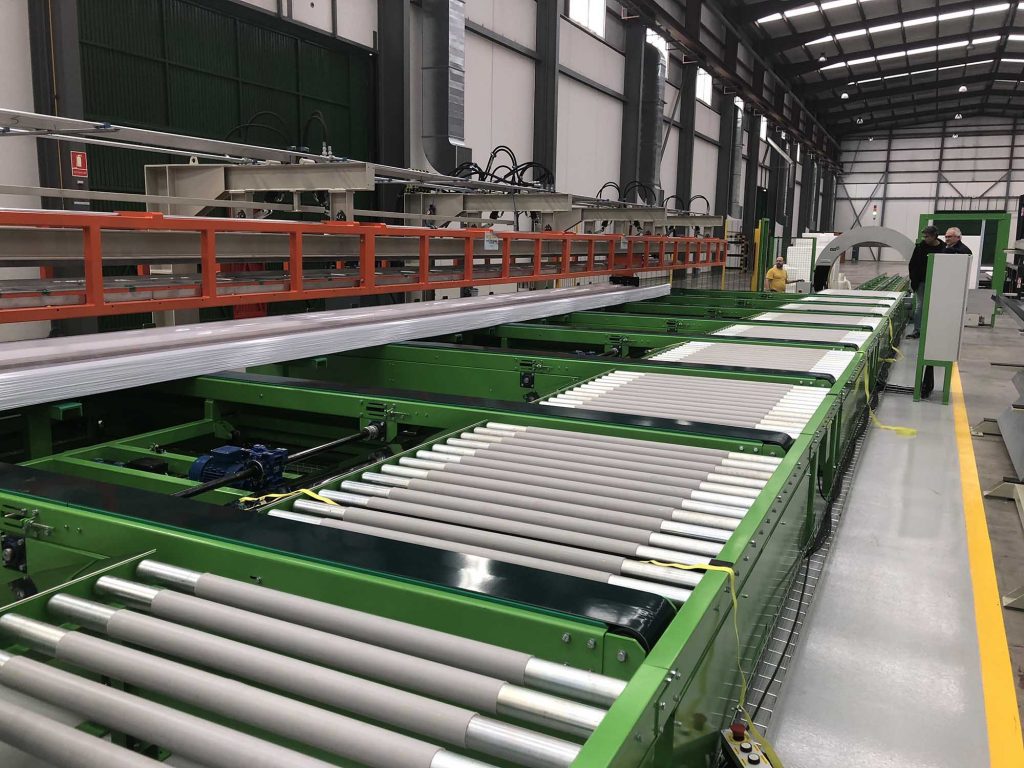
E.E: Were there any products with special characteristics used?
PLASTICBAND: We try to standardize all our solutions at the maximum, this improves our manufacturing times because we work under already developed bases and we only must customize and adapt it to our client’s needs.
E.E: How did your products / solutions improve productivity for the client?
PLASTICBAND: They achieved a productivity improvement of more than a 50%. The operators that sporadically were placing blocks and wrapping, are now in the production and quality areas, so they can deliver their orders quickly and better, so they are now more competitive.
E.E: How important was the project / projects for the client?
PLASTICBAND: They took a leap forward in the automatization of their factory.
They passed from being a traditional factory using a lot of operators in the packaging area to have only the necessary personnel and use their workforce in the most important part that is manufacturing.
E.E: What was the client feedback after implementation?
PLASTICBAND: They were very happy about the efficiency; they are collaborating with us opening their doors to bring other customers to see how their line is.
This customer is currently working with other 2 new lines from Plasticband now.
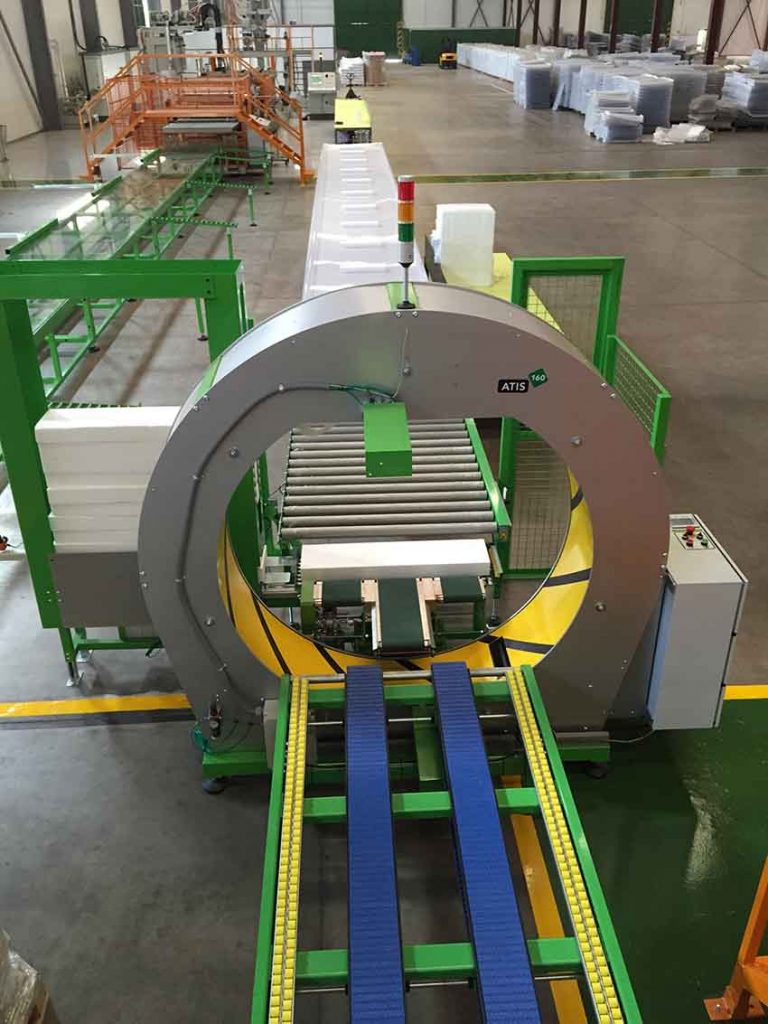
E.E: Did the current situation made your company implement differently than usual?
PLASTICBAND: At that moment there were not Covid restrictions, we did all visits and installations as usual.
Nowadays, yes, current situation and travel restrictions have speeded up the use of digital technologies in all companies.
We have passed from in-person meetings and FATs to video calls, of course when the installation in site is necessary, our technicians or the technicians from our distributors go in-person to install and implement the packaging lines.
E.E: What are your forecasts for the second half of 2021?
PLASTICBAND: We are very optimistic about 2021, automatic lines are increasing, and of course customized lines using our ATIS range will grow.
Of course, we do not forget our semiautomatic models NELEO that are tough machines used worldwide in many markets to wrap a wide variety of products like cabinets, doors, furniture, floors, aluminum profiles, tires, coils and more.
We have a wide net of distributors that assist locally our clients in all their projects, from a basic semiautomatic to a complex engineering project.
Ask us about your nearest distributor.