CastAlum is an internationally acclaimed die caster and machinist based in Welshpool, Mid Wales. Over twenty years they have developed a range of capabilities, manufacturing high pressure and squeeze cast parts, as well as machined and fully assembled products. These have been supplied to customers in the UK and Europe, but also as far afield as Canada and Mexico. Their diverse set of competencies, coupled with a high standard of engineering prowess, has seen them supply prestigious marques including vehicles from VAG, BMW, Ford, General Motors, Fiat, Renault, Mercedes, Jaguar Land Rover, and McLaren.
Founded in 2000, CastAlum began supplying cast-only parts to a single customer. Over the years, they have grown not only in terms of the number of customers and castings being supplied, but also in the complexity of the components being produced. This increase in knowledge and engineering expertise has enabled the company to target high-end, higher added-value parts. Steering gear housings originally formed the bulk of the business, but added proficiencies has enabled the company to specialise in more transmission-type components.
This specialism and innovation has come at an opportune time in the automotive industry, as OEMs seek ever more inventive solutions to compliment the rapidly expanding Electric Vehicle (EV) and hybrid market. CastAlum has recently successfully launched large manufacturing programs in each of these markets, and is expected to ramp up production significantly in 2022.
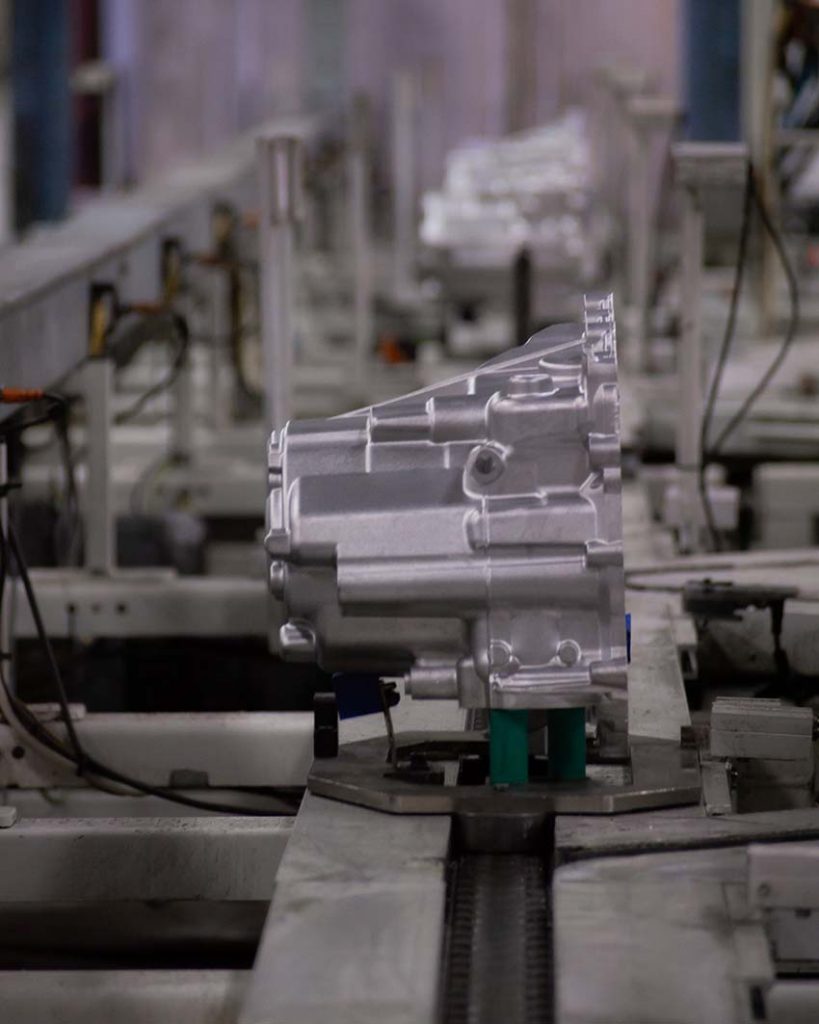
Despite the continued addition of secondary processes, the business has continued to master and improve every aspect of the die casting process. There are eleven high pressure die casting cells ranging from 1000-2000 tonne locking-force, plus three squeeze casting cells with a locking force ranging from 1600-1800. Squeeze components are heavier, denser parts that are heat treatable, making this process well suited to products such as steering knuckles and power take-off covers and housings where elevated mechanical properties are required.
All cells are fully automated, fitted with their own integral bulk-melting tower furnace and robotics, delivering in most cases a finished part to the operator. Secondary processes available on site include shotblasting, x-ray, and of course the machining centre. This latter capability was added in 2009 and has expanded since to include fourteen Heller CNCs, an automated conveyor, with several complimentary inline processes.
CastAlum’s most recent claim to fame is being the first aluminium caster in the UK (and possibly Europe) to introduce additive material capabilities to its own premises. This investment and understanding of this emerging technology has several advantages. Managing heat in the die casting process is a constant battle, with aluminium being heated to 700 degrees, and then being injected into the cavity at fast speeds and under enormous pressure, before being cooled down and extracted, ready for the process to begin again. An ineffective cooling process can cause significant quality defects, leading to costly downtime. The application of additive material technology to steel tooling, with the optimisation of cooling geometry and heat transfer, has allowed CastAlum’s engineers to manage temperature through conformal cooling, resulting in a raft of improved metrics throughout the process.

At present, the additive manufacturing production unit is serving the company’s needs, but in future it may well provide opportunities in the domain of additive manufacturing beyond the world of automotive casting. In addition, the success of this programme means the engineering team are now looking to launch another project around additive manufacturing and additional CNC milling capacity. At present, parts are cast before being sent away for heat treatment, while the objective of this new project will be to essentially cast a heat-treated product in-house.
While known predominantly in the industry as a supplier to the automotive market, CastAlum has also recently brought its experience to new territory through the manufacture of a heatsink for another local company who specialise in the production of drive systems. The surge towards electric vehicles, and the huge demand that that places on suppliers such as CastAlum, shows no sign of abating anytime soon. However, with programs continuing to be affected by global issues such as the semi-conductor shortage and other logistical challenges, diversification across multiple industries presents a new set of opportunities for the business.
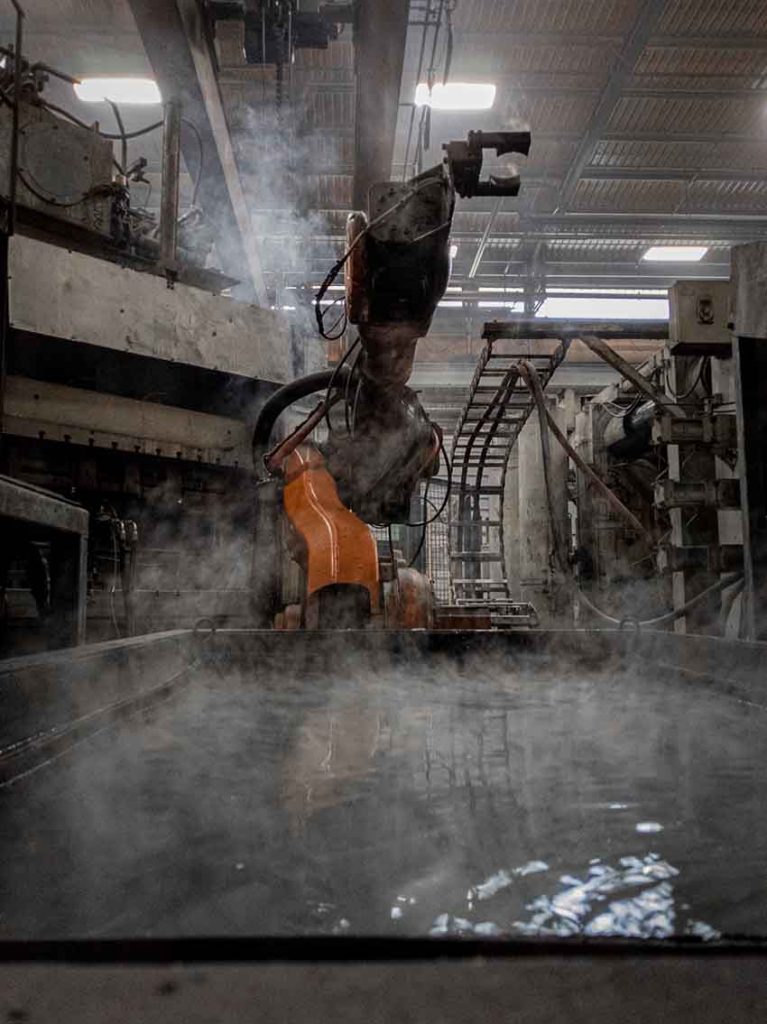
The combination of high demand from the automotive sector, and the prospect of growth in other markets, means there is no let-up in terms of investment into the capacity, skills, and innovation within the business. Nowhere is this more apparent than the arrival of a brand new, 2000 ton die casting machine cell, anticipated to arrive in the first month of 2022, with the groundworks for this latest addition to Castalum’s facility having already been completed. Greater shot blast capacity is also being brought on site, all to enable the business to serve the forecasts for the coming year.
Constants throughout CastAlum’s two decades of operation have been a steady, consistent growth in capabilities and the advancement of technology in all aspects of its work. The mission of the business is not to be the cheapest, but to build a reputation on being the best in class. This is evident when observing the past and current range of programs that the company picks up, which are rarely new ones. More often than not, they are existing programs where customers have been unable to achieve their casting objectives, and so turn to CastAlum, who have a long history of overcoming engineering challenges and delivering the most complex components.

This display of engineering prowess is due in no small part to the excellence of the onsite engineering team. This includes those responsible for the running of the plant, as well as those in supporting departments such as tooling, maintenance, and the engineering process. The recent addition of a Training and Development Manager, and a longstanding apprenticeship scheme, are testament to the company’s commitment to developing and promoting internally. With production demands rising rapidly, the company is currently in the process of recruiting new personnel to compliment the new production capacities that are being installed.
With EV-related programs due to double in production over the course of the coming months and leading into 2022, the next twelve months are expected to be a time of substantial expansion for CastAlum in terms of personnel, capacity, and output. With millions of its parts already in vehicles around the world, this manufacturer continues to hold onto it’s places as a supplier and employer of choice within the industry.