Interview with Kai Sievers, CEO of ENDEGS Group.
Easy Engineering: Tell us a short story of origin of the company.
Kai Sievers: I have founded ENDEGS in 2007 as I wanted to further contribute to protecting the environment. At this time, many industrial facilities just vented their hazardous emissions into the air – thus, harming people and environment both. I asked myself: why can we so often smell a refinery long before we see it? And can’t we do something about that? Exactly this is our daily task since founding ENDEGS: taking actions to improve the air quality. In 2008, we have developed our first mobile incinerators that efficiently burn gases, gas compounds and vapors and of course we keep helping our customers today. Since the founding of our company, we have successfully completed over 1.400 projects and have overcome many difficult challenges.
E.E: Which are the fields of activity where you are operating?
K.S: In recent years, people have started to react more sensitively to industrial odors as they are seldom harmless and never healthy. The times when smoke pouring out of industrial facilities was a symbol of prosperity are far from over. Whether it is by harming the health of workers at the facilities or people in the surrounding neighborhoods or by increasing the global carbon footprint – industrial odors and hazardous emissions affect the health and safety of everyone.
ENDEGS provides safe, environmental-friendly and efficient solutions for the reduction of industrial emissions. With our technologies, we enable facilities from many industries – such as oil & gas, shipping, refineries, chemical & petrochemical, food and fertilizer – to lower their emission of gases and vapors that are dangerous to human health and environment at the same time. This way, we contribute to enhancing the air quality, increasing the health and safety of workers and neighbors and lowering the global greenhouse gas (GHG) footprint – because a substance that is not emitted can do no harm.

E.E: What are the ranges of products and what types of services do you offer?
K.S: We offer our clients a wide range of mobile technologies. Our portfolio for the reduction of emissions includes mobile incinerators, mobile vaporizers and the ATEX Zone 0 robot for rent. With these solutions, we can assist our customers in reducing their emissions – from degassing projects to the temporary replacement of vapor recovery systems to the safe cleaning of industrial tanks. All of our units are easily portable and can be deployed directly at the facilities of our customers. ENDEGS services are not only highly flexible, but can also be deployed rapidly – that is particularly important for emergency cases when every minute counts. All ENDEGS technologies can be applied individually or together in combination.
E.E: Which are the most innovative products / services and what special features do they have?
K.S: ENDEGS mobile vapor combustion units (VCU) are capable of burning all types of emissions – including hydrocarbons, VOC (volatile organic compounds) and HAP (hazardous air pollutants) – with no open flame and a combustion rate of more than 99.99 %. By developing our first mobile vapor combustion unit back in 2008, we have in fact invented the first portable, autonomously operated mobile incinerator world-wide. Thus, we have enabled mobile degassing and emissions treatment for the very first time. With our VCUs, we can offer the safe and sustainable degassing of all components used in industrial facilities such as containers, tanks, pipelines, ships, vessels and barges as well as the temporary replacement of vapor recovery systems in refineries during downtimes.

With the ENDEGS nitrogen services, we enable the treatment of systems and system components that contain flaming liquids and gases. Liquified gases under pressure like LNG, propane or ammonia are complex to work with as they are highly flammable. Our fleet of mobile vaporizers with nitrogen tanks is ideally suited for handling those substances by purging and inerting them, allowing the degassing of components that contain such complex products as well.
We also offer the rental of the ATEX Zone 0 robot. The robot is remote-controlled, guaranteeing complete safety for workers during the cleaning of industrial tanks as it can be operated from a safe distance. The ATEX Zone 0 robot can be used in many industries and for a wide range of materials as it is small and very mobile. It is controlled via two joysticks and a monitor, showing every movement in real time.
E.E: Which are the most significant projects in the history of the company?
K.S: Last year, we have carried out one of our biggest projects yet. During a refinery turnaround in Germany, we have executed the TA-Luft conform degassing of several components and equipments. For almost three months, we were stationed at the refinery with three combustion units to degas a broad range of columns, heat exchangers, mobile liquid storage tanks and other components. The biggest challenge during this project was purely the organization of the materials we used: besides the units, we also applied a total of 1.9 km of mobile piping and hoses. During refinery turnarounds, we ensure that the downtimes of the facilities are reduced to a necessary minimum – daily operations can continue undisturbed or with only a minimum of interference. Thus, the business can keep going during the entire degassing process and our customers can significantly save time and money.

E.E: What projects were the most challenging?
K.S: One of our major and most challenging projects was probably the deployment of our mobile vaporizer during a major emergency situation in Germany. In the north of Germany, two trains collided – one of the trains was loaded with propane. As I have mentioned earlier, propane is a liquified gas and therefore has a high risk of explosion. Four of the railcars that were loaded with the highly flammable gas derailed, resulting in a very acute risk of inflaming and ignition of the propane. An explosion would have been catastrophic. To end this hazardous situation, we have deployed our mobile vaporizer with nitrogen tank on very short notice. We inerted the damaged railcars with nitrogen to flush the propane out of the tank and guided it safely to the flare. After that, it was possible to burn off the propane safely. We have already faced many a difficult challenge since 2007. But thanks to our fantastic team and the long and reliable relationships with our clients, we have yet mastered every single one of them!
E.E: What was the research behind the products/solutions and how important is R&D?
K.S: Innovation is a very important topic to us and is indeed necessary to keep reducing emissions continuously and efficiently. When it comes to product innovation, we always pay close attention to customers and their needs and demands. Do they, for example, work with a project that our services cannot be applied to? Then of course we do everything we can to find a solution and extend our technologies to that specific product. Therefore, many of our innovative ideas emerge from our daily work “in the field”. Naturally, research and development are of equal importance as innovation for developing new technologies and services.

E.E: What products / solutions are you going to launch in the future?
K.S: As I have already said, we always aim to optimize our technologies and adapt them to newly emerging needs and trends. As industrial degassing has become a standard nowadays, the challenge we face currently is to adapt the technologies so they can be deployed in wider areas of application. An example for this is the introduction of our new fleet of vaporizers with nitrogen tanks that – in combination with our mobile incinerators – enables the degassing of components containing more complex and highly flammable products. Of course, we will continue to launch optimized and adapted products that address exactly this issue of adapting technology to new applications.
E.E: How important are the after-sales services?
K.S: After-sales service has a high priority for us within ENDEGS and has played a crucial part in our success story. We deliver different after-sales services during the cycle of the project – generally, our after-sales service consists of a professional, project related communication and support to the client. So, it is less money oriented for our kind of service. It starts for us after contract closure. We immediately assign a project management team taking care of all the necessary tasks. To name just a few examples, this includes support in dealing with authorities, emission calculations for internal and external reportings as well as HAZOP meeting participation. During the project, we take care of everything and deliver a worry-free package to the client. After the project, the client receives a comprehensive reporting about the key facts and figures from the operation including emission measurement reports, financial reportings and operational reportings. The strong bond between the client and our teams that was created from the after-sales services leads to new sales with a probability of around 95 %.
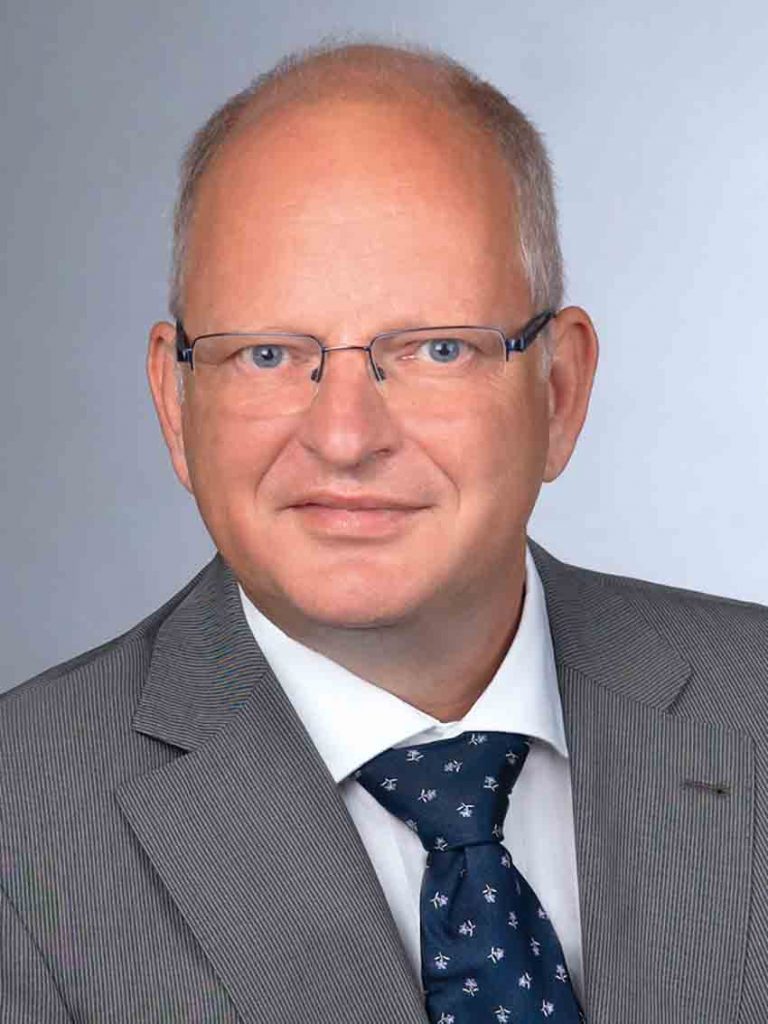
Kai Sievers, CEO ENDEGS
E.E: Tell us about social responsibility and what part does it play in the company?
K.S: Social responsibility is of the uttermost importance for ENDEGS as our most important goal is to help protecting the environment as well as human health and safety. We dedicate all of our passion to significantly reducing the global emissions to contribute as much as we can to the goal of reducing the global GHG footprint as our mission is clear: lower emissions.