For a great many industries, conveyor belts are critical components. They are also much more complex than most people realise. Their reliability and efficiency can literally make or break an operation. Despite technology accelerating faster than ever before, basic conveyor belt design and the methods used to make them have changed surprisingly little in the past few decades. Until now that is, because in Drachten, in the beautiful Friesland region of The Netherlands, the scientists and engineers of Dunlop Conveyor Belting have been busy creating a new and unique design of conveyor belt. A design that is already starting to change traditional thinking on conveyor belt design.
Dunlop Ultra X is proving to be not only far more durable and tougher than conventional ply belting but also surprisingly competitive on price. Here, conveyor belt specialist Leslie David discovers how lateral thinking and modern technology have made this new type of belt such a huge success.
The conveyor belt market
To be reliable and cost-effective, industrial rubber conveyor belts not only have to cope with abrasive wear but also resist damage caused by ripping, tearing and the impact of heavy, sharp objects falling from height. The market is dominated by low-grade ‘economy’ belting imported from South East Asia. In fact, it is not uncommon for European belt manufacturers to import from Asia and re-sell under their own brand in order to supplement their production and allow them to offer low price belting to their customers in Europe.
As a matter of strategic policy, Dunlop Conveyor Belting in the Netherlands have consistently refused to do this. Instead, their approach continues to be based on ‘lowest lifetime cost’. Rather than trying to compete at the low end of the market, they only supply belts that provide a much longer than average working life. Although this strategy has always served them well, their research & development team continued to search for a super-tough belt that can also compete at the economy end of the market. And in Ultra X they appear to have found the solution.
Designed for the task
Even the strongest, heaviest belts can be ripped, torn or punctured by heavy, sharp materials falling from height or becoming trapped and penetrating them. “Accidental damage is something that all conveyor operators have to contend with” says Rob van Oijen, Dunlop‘s manager of application engineering. “Objects get trapped and belts can be destroyed very quickly. Many conveyor operators seem to accept that this is an unavoidable situation and resort to low grade ‘sacrificial’ belts. We do not agree. We see sacrificial belts as a totally false economy because when you calculate the cost of lost production due to stoppages for frequent repairs and the almost constant buying and fitting of replacement belts, it works out to be a far more expensive way of doing things”.
A common misconception is that increasing the cover thicknesses and/or the number of plies will improve resistance to damage but in reality, it is simply not the case. In fact, belts that are too thick can cause other problems such as lack of troughability and steering and handling difficulties. All the evidence points to the fact that for belts on conveyors where ripping and tearing is a problem the only truly effective solution is to fit a specifically engineered conveyor belt that has a construction that has been designed for the purpose. Such belts can have a level of resistance against ripping and tearing and impact that is several times higher compared conventional fabric multi-ply construction belts. However, some of these ‘extra tough’ belts are not nearly as tough as they are claimed to be. It is also fair to say that such belts usually have a price tag that can be beyond an acceptable budget level in the shorter term.
Back to the drawing board
The big challenge that faced the Dunlop engineers was to design a belt that had a much higher resistance to impact, ripping and tearing while at the same time be more economically priced. Fortunately for them, their belts were already widely-recognised as having the hardest wearing and longest lasting rubber covers. This allowed the engineers to concentrate on the carcass construction and specifically the reinforcing fabric that is the basis for the strength of pretty much every conveyor belt.
The result was a unique super-strength ‘breaker weft construction’ single-ply belt based on an tremendously tough patented fabric made exclusively in their Fenner Dunlop sister company’s in-house fabric weaving facility in the USA. The specially woven carcass incorporated crimped warp polyester yarns to provide high strength and low stretch combined with strong ‘binder’ and ‘filler’ yarns to create the necessary strength and stability under load.
Throughout its development, Dunlop engineers repeatedly tested sections of belt carcass to destruction using a variety of methods including measuring tear resistance according to the international EN ISO 505 standard. By the time they reached the final testing stages, they were exceeding all expectations. Ultra X possessed more than 3 times greater longitudinal rip resistance, up to 5 times better tear resistance and a far superior resistance to impact compared to even the highest quality conventional 3-ply or even 4-ply fabric-ply belting. In conveyor belt terms at least, they had found The Holy Grail.
Less can be more – a question of strength
So far, Dunlop have made Ultra X available in two strengths – Ultra X1 (Type 330), which is designed for users of EP315/2 and 400/3 conventional ply belts and Ultra X3 (Type 550), which is designed to replace EP500/3, 500/4, 630/3 and 630/4 ply belts. The fact that Ultra X is a single-ply construction belt designed to replace conventional two, three and four-ply belts has certainly raised a few eyebrows. The first question in most minds is how on earth can a single-ply belt can provide sufficient tensile strength and yet still have much higher high levels of rip, tear and impact resistance? Rob van Oijen was more than happy to provide this explanation:
“We keep coming back to the unique fabric that we are using because it is able to withstand the kind of punishment that would destroy a normal belt. Ultra X also has amazing tensile strength. The longitudinal tensile strength of the X1 is 330N/mm and the X3 has a longitudinal strength of 550N/mm. We stepped away from the conventional multi-layer belting for good reason. A single-ply construction requires a finger-splice joint to be made and although they take about 30% longer to make, the enormous advantage of finger splice joints is that they retain up to 90% of the belt’s static tensile strength. By comparison, a 2-ply step splice only retains a maximum of 50% and a 3-ply step joint only achieves a maximum tensile strength of 67%”.
“The higher level of splice efficiency combined with the tensile strength of the X1 and X3 effectively creates equivalent tensile strengths and belt safety factors that are more than comparable to 3 or 4 layer conventional belting. Another advantage of the finger splice is that, crucially, in dynamically stressed conditions (when the belt is working and under load) the resistance to dynamic fatigue the finger splice is again vastly superior to a stepped splice”.
Rob freely admits that finger splices are more costly but, in his experience, this reduces quite significantly with growing experience and the much longer operational lifetime being experienced more than compensates for the higher splicing cost. “The technical and economic arguments in favour of finger splicing are unquestionable. The cost of making the splice is a small fraction of the cost of a system shutdown or the many thousands that have will have been spent buying and installing the belt in the first place. In my view, it surely makes no sense to try and ‘save’ a few hundred euros by opting for the less durable step splice or by not having the work carried out by the most skilled service provider available”.
To help their customers, Dunlop supply the splice kits including finger pattern templates, materials and tools, a guide manual and a training film. They even provide training and supervision where they feel it is warranted. For those determined to avoid finger splicing, the good news is that Ultra X also possesses excellent mechanical fastener retention. There certainly does not appear to be any question mark against the overall strength of Ultra X because, as their promotional film proudly states, an Ultra X3 single ply belt is able to pull up to 56 tonnes in weight.
Endless opportunities
Yet another advantage is that Ultra X is flexible enough to be used on smaller drive pulley diameters, “The X1 drive pulley diameter for over 60% rated tension can be as small as 315mm and the X3 drive pulley diameter, again for over 60% rated tension, can be as small as 400mm” says Sales & marketing director Andries Smilda. “Ultra X can run on the kind of mobile machinery that has always been notorious for having small pulley diameters where the dynamic stress placed on the inner carcass and splice joint by the continual flexing over small diameter pulleys seriously limits what can be fitted. Ultra X overcomes that problem”.
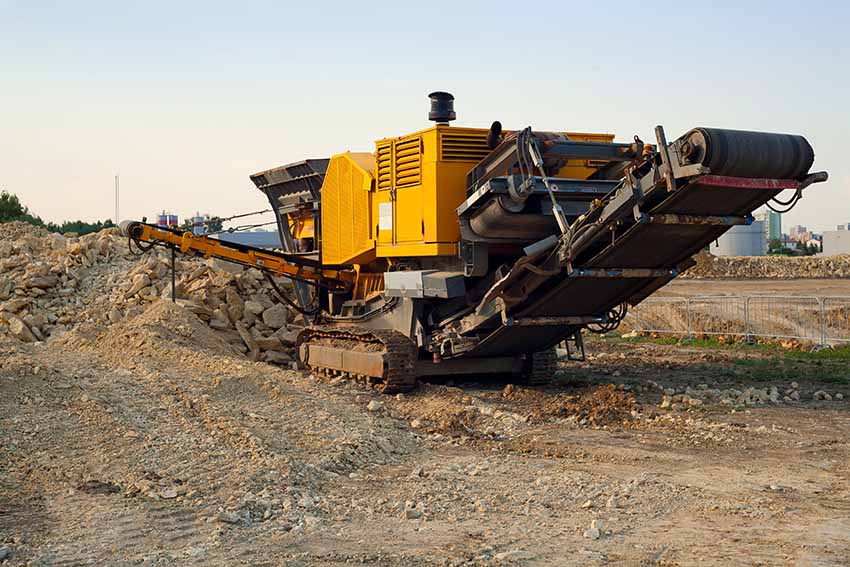
Under the radar
When Dunlop first launched Ultra X two years ago it was a deliberately low-key affair and under the radar of most of the market. Andries Smilda explains that they had many reasons for taking such a cautious approach. “We knew from the years of research and intensive laboratory testing that we were onto something special. But Dunlop being Dunlop we still wanted to prove it in the field so we worked with several tried and trusted end-users”. “Having since sold many tens of thousands of meters has confirmed beyond doubt that Ultra X is all that we thought it would be and more. We have not had one single complaint or technical issue”.
Most significantly of all, Dunlop’s claims seem to be supported by the evidence. Ultra X is now the belt of choice for a growing number of OEM’s who have reported that Ultra X has more than doubled the average belt lifetime on their machines. In France, since replacing conventional multi-ply belts with Ultra X, a large aggregates quarry saw an 87% improvement in productivity thanks to a dramatic reduction in stoppages caused by broken splices and other repairs. In Spain, one delighted cement plant operator experienced a 50% increase in operating life who maintains that they still look as if they were only fitted a few weeks ago.
Competing on quality and price?
Dunlop are very open about the need to be able to offer prices that are at least comparable (and often lower than) multi-ply belting. “We would never would ever comprise on quality for the sake of competing on price. That is simply not our culture and it is not necessary anyway because there are several reasons why we can price Ultra X so competitively,” says Mr. Smilda.
“Firstly, the single-ply carcass is made from fabric that we manufacture in-house. That is a big, big advantage in terms of quality and cost. Having a single-ply construction also helps to maximise efficiency of production because there are fewer calendar runs. And having no rubber skim between the plies not only results in a thinner, stronger carcass, it also keeps the cost down. We are also making longer production runs at a maximum width of 2000mm”.
A cultural change?
For many people, the idea that a mono-ply construction belt can provide the necessary longitudinal tensile strength while possessing considerably more resistance to ripping, tearing and impact is difficult to comprehend. This is especially so given that it is also being price-competitive; something Dunlop is not usually recognised for. However, if conveyor operators can look beyond traditional thinking then I strongly suspect that Ultra X really could be a real winner for them.
Author: Leslie David