Coolmag Thermo Conductive designs and manufacture thermal compound solutions for thermal management, from potting resins to plastic compounds. The company also supports customers with firsts applications or prototypes and with the implementation within their manufacturing process.
Since they started back in 2020, the company has been collaborating with customers in order to include thermal management as a strategic stand-out element within their R+D & design stages and helping them during the hole process (prototype and production).
It’s crucial not only to be aware of the different applications methods and thermal management basics (3D heat dissipation, air=evil, thermal conductivity & diffusivity values, etc.) but also, to analyze and replace every single element that it’s negatively contributing to the global thermal management challenge.
Interview with Xavier Mirabet Belda, Global Sales Manager at Coolmag Thermo Conductive.
Easy Engineering: What are the main areas of activity of the company?
Xavier Mirabet Belda: Although wherever there is a thermal issue, Coolmag can potentially fit, our activity is in the Power Electronics Industry. Industrial and Electro mobility applications are the mainly areas whereas Thermal management it’s the main topic now, as Power density demand is increasing.
So, we talk about chokes, transformers, filters but also On Board & Off Board Chargers, Inverters, Converters, Battery Packs and so on.
E.E: What’s the news about new products?
X.M.B: Our main focus is to increase our resins properties as much as possible, looking for the highest TC value without compromising other properties like viscosity, electrical properties, etc.

We recently launched two brand new products:
COOLMAG SA 30: 2K Silicone based, 3W/mK product with outstanding properties, to meet the most demanding applications.
COOLMAG PLAST PA 20: Plastic compound PA based, 2,5 W/ that combines thermal conductivity and electrical insulation in standard pellet form suitable for thermoplastic injection molding and other processes (e.g., extrusion), allowing design freedom in applications previously restricted to common plastics and even metals, like coil bobbins, battery packs or electronic enclosures.
E.E: What are the ranges of products?
X.M.B: We got two different product families:
- Resins: PU & Silicone Resins for Potting, Injection and Gap Filler applications
- Plastics: PA based compounds for injection/molding applications.
We will be adding a new family in the upcoming months, combining thermal /magnetic properties. Stay tuned!
E.E: At what stage is the market where you are currently active?
X.M.B: Potting resins have been commonly used in power electronics, mainly for electrical & environmental protection purposes.
But no electromobility is pushing power density to the limits, so temperature has become a “hot topic”, a serious bottleneck to be able to do things better, safer, smaller and increase the power.
Traditional passive methods and old potting solutions are not enough, and more efficient and sustainable solutions are needed.
This has a big impact on the R&D process, since new thermal solutions allow not only to optimize and improve existing designs but to do things that have never been possible to do before.
Also, EV industry numbers are extremely huge so that means dealing and managing a lot of chemicals. Making 2 or 3 prototypes it is an easy one…but producing thousand units per week, that’s a challenge! That’s why industrialization process is crucial to succeed.
That’s the reason why we support our customers during the hole process, from prototyping to industrialization, sharing our experience and knowledge in order to make the process as easy as possible.
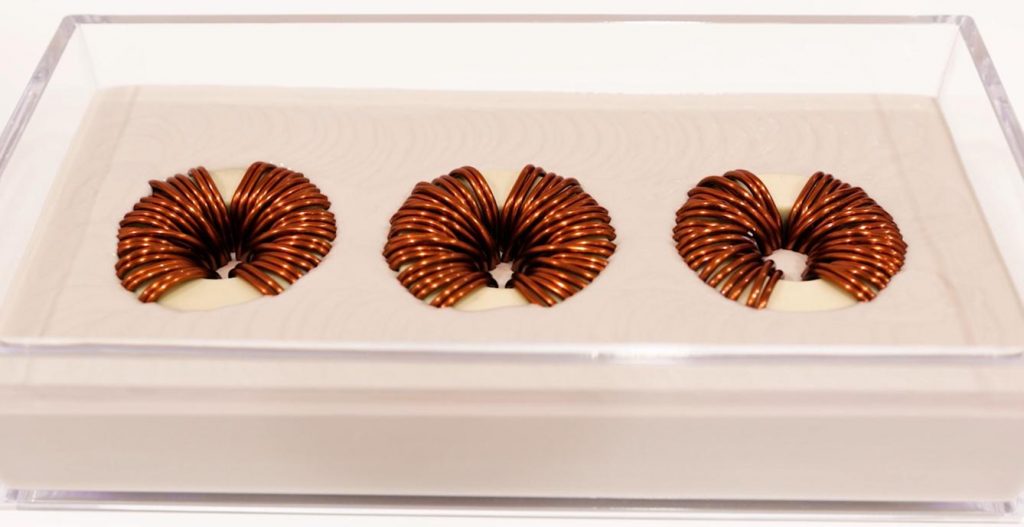
E.E: What can you tell us about market trends?
X.M.B: Each industry has his own challenges (Wireless vs wired charging, ultra-high charging stations, long range batteries, etc.) but at the end, market trends are pretty much the same: it’s all about power density, reliability and safety…so that means temperature. We should also include sustainability, as is going to be a big challenge specially for the chemical industry.
Our main target is to provide thermal solutions, covering the hole three topics. No matter what the application is, if there is a thermal issue, Coolmag can potentially fit.
E.E: What are the most innovative products marketed?
X.M.B: We are one of the few companies that designs and manufactures its own thermal compounds but also offers a full pack service, including application assistance and Taylor made Solutions. This is a must now!
We are trying to increase our thermal conductivity on our daily basis without compromising the other ones (like electrical properties) but also, we are now working on two brand new families that can be a game changer:
The first one is a combination between the thermal properties of Coolmag with electromagnetic shielding properties and the second one will allow traditional ferrites to be replaced by a much more flexible polymeric compound but with the same properties… so fragility it is not going to be an issue anymore.
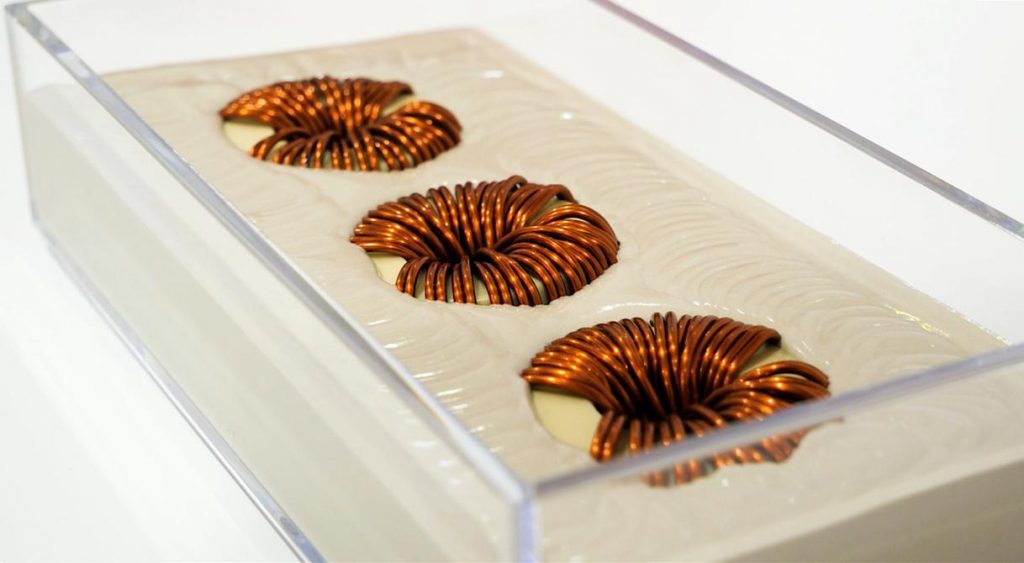
E.E: What estimations do you have for 2023?
X.M.B: For us, this year is key to consolidate ongoing and awarded projects (especially automotive projects), since most of them will start production in 2024/2025, but our customers need to have final designs ready before the end of the year.
We expect to increase our production x 2 comparing to the last year and hopefully we would have our new factory ready by the end of the year, so our production capacity, which can currently reach 60 tons per month will be increased exponentially.
Never before thermal management played such an important role in power electronics…now is the time!