Miraitek4.0 offers manufacturing companies an IIoT software platform providing all useful information for factory management – from simple flow monitoring, to energy consumption details collection, maintenance planning and quality management. The platform’s various applications allow for the collection and analysis of data and the implementation of models and actions to optimize production.
Miraitek has partnered with smartFAB, a Milan based innovative startup, to create business value from manufacturing data. smartFAB’s web-based Industrial Analytics platform puts people at the center of decision-making and empowers manufacturers of all sizes to identify and predict production losses, such as waste, quality, throughout, and energy consumption.
In line with market needs and the evolution of technologies, Miraitek4.0 also offers products with machine learning and artificial intelligence algorithms to meet specific customer needs for predictive maintenance and quality improvement. The information can be used by different hierarchical levels within the organisation and can be integrated with data from outside the production department to obtain a holistic view of the business quickly and easily.
Miraitek4.0 is a spinoff of the Politecnico di Milano. It is a dynamic, responsive and reliable company supporting customers throughout their digital transformation process thanks to its highly skilled team and its special relationship with some of the main automation technology providers. Miraitek4.0 offers services to assess the digital maturity of business processes, defines and integrates tools for the digital transformation process of plants and trains staff, thus boosting companies’ productivity and competitiveness in an increasingly global market.
Easy Engineering: How do you see sustainability and what are your efforts in this direction?
We see sustainability as the balance between social, economic, and environmental objectives that meets the needs of the present without compromising the ability of future generations to meet their own needs. To us, that means building lasting customer relationships by developing innovative products and solutions that leverage human and machine intelligence to help manufacturers to maximize quality and efficiency and minimize waste and consumption.
Examples including detecting anomalies in process data that lead to defects or other quality issues or anomalies in equipment performance that cause increased energy consumption.
E.E: Tell us about the sustainable solutions that you offer (if any).
As you know, Industry 4.0 is a combination of new technologies, including Industrial Internet of Things (IIoT), cloud computing and data analytics, that is revolutionizing the way companies design, manufacture, and distribute their products. Industry 4.0 enables collaboration between departments, partners, and people, more flexible industrial processes, and autonomous and intelligent manufacturing. It has the potential to improve productivity and competitiveness, create new business models and safer workplaces, as well as increase energy and resource efficiency. In short, it offers a pathway to sustainable manufacturing.
Using high-tech IoT devices leads to higher productivity, reduced consumption, and improved quality. Integrating IoT, quality control and operational data from enterprise systems, such as MES, ERP, creates whole new levels of visibility and insights from previously siloed information. By applying machine learning algorithms, manufacturers can detect errors and anomalies immediately, rather than at later stages when the time and cost of intervention are greater. Combining human and machine intelligence to create a collaborative intelligence increases accuracy as well as confidence and trust. With minimal investment, production personnel can set up a smartphone connected to the cloud to monitor, analyze and predict manufacturing processes from virtually anywhere.
Miratek4.0, IoT platform, and smartFAB, Industrial Analytics platform, have joined forces to deliver an integrated solution for smart manufacturing. Through this partnership the companies provide an integrated solution that collects data from devices and equipment, connects IoT and operational data, combines human and machine intelligence, and utilizes machine learning and other forms of artificial intelligence to generate real-time insights, improve employee engagement, and enhance decision-making.
The combined solution provides tools for monitoring energy consumption and resource efficiency to minimize production costs and run a cleaner factory, identifying the root cause of quality issues to reduce waste and increase customer satisfaction, and performing predictive maintenance to minimize equipment downtime. The tools allow manufacturers to increase productivity, optimize processes, reduce waste, and enhance growth. In the context of sustainable manufacturing, this means manufacturing products through economically-sound processes that minimize negative environmental impacts while conserving energy and natural resources and enhancing employee engagement and decision-making.
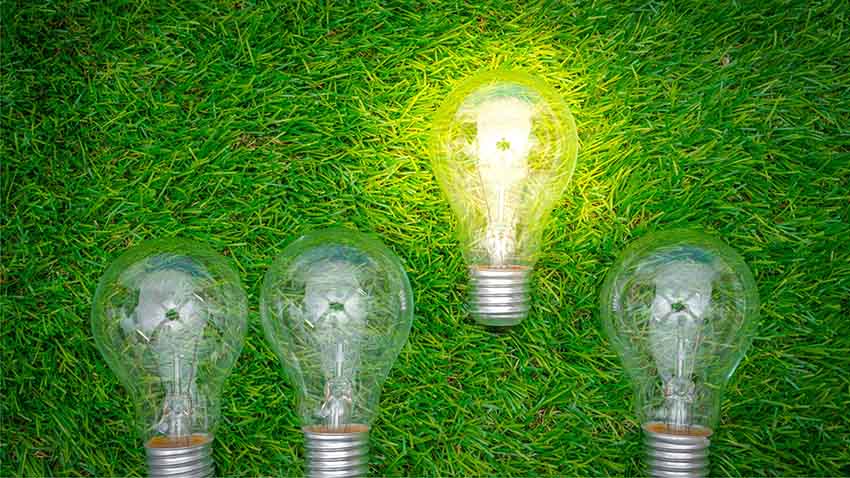
E.E: Do you offer solutions for reinvigorating old equipment with new solutions?
IIoT technologies provide a wealth of information that allow manufacturers to better maintain their equipment, take steps to prevent downtime, and extend asset life. While the ultimate objective for many manufacturers might be digitization across the factory floor, as well as throughout its supply chain, falling costs and flexible new technologies have shifted the conversation from investing in new equipment to reinvigorating legacy tools and from vendor-supported upgrades and custom integration to cost effective IIoT architectures, including smart sensors, retrofit kits, edge gateways, and video cameras. While these technologies might not offer full digitalization, they are a low-cost alternative that can extend the shelf life of equipment and positively influence all parameters of sustainability.
E.E: Tell us about sustainability in production & distribution.
According to the US Environmental Protection Agency, sustainable manufacturing can be defined as “the creation of manufactured products through economically-sound processes that minimize negative environmental impacts while conserving energy and natural resources.”
A sustainable approach offers opportunities from design to distribution and implementing sustainable manufacturing practices helps organizations lower resource and production costs, improve sales and brand recognition, lower regulatory compliance costs, and offer greater access to financial and human resources.
But despite the opportunities and benefits, achieving sustainable manufacturing faces numerous barriers, especially for SMEs. Barriers to adopting sustainable manufacturing practices include lack of technical and managerial awareness, financial misperception, and poor systems for monitoring and evaluation.
Here are ways that companies can overcome these barriers and progress further on the path to sustainability:
- Address sustainability in a coordinated, integrated, and formal manner, rather than in an ad hoc, unconnected and informal manner.
- Focus on increased competitiveness and revenues rather than primarily focusing on cost-cutting, risk reduction and improved efficiency.
- Use innovation, scenario planning and strategic analysis to go beyond compliance.
- Integrate sustainability across business functions.
- Focus more on the long term.
- Work collaboratively with external stakeholders.
E.E: Tell us about R&D and innovation.
Our goal is to make analytics accessible to manufacturers of all sizes and people of all skill sets. Hence, we spend a lot of time thinking about the transformation of data into business value and actionable insights that speak to the needs of shop floor workers and, at the same time, are aligned with a more holistic approach to information management and sustainable manufacturing principles.
E.E: Tell us about preserving resources and driving circularity.
Miraitek4.0 and smartFAB take a comprehensive approach to circularity that is built around a framework that, on the one hand, drives circularity in our own operations and, on the other, enables our customers to become more circular. What’s more, we aim to innovate towards new circular business models, covering all stages of the product lifecycle, and offer solutions that enable our customers innovate towards new circular business models, such as servitization models.
We have designed out waste and consumption in our products and services. We enable our customers to become more circular by generating actionable insights that enable them to improve product quality, reduce waste and consumption to a minimum, and extend the use cycle of their assets. Through the application of big data analytics, manufacturers can get a better handle on predictive maintenance and real-time optimization as well as recognize patterns to enhance manufacturing processes and increase the efficiency of their supply chain thus contributing significantly to the first pilar of circularity, reducing waste to a minimum.
A global food processing company reduced waste and energy consumption by identifying the root cause of process deviations so they could prevent process deviations rather than cure them. In another example, a semiconductor manufacturer reduced the consumption of energy and other resources by utilizing data to predict quality at the end of each process step thus enabling them to scrap product at the point of defect rather than the end of the production line.
E.E: How do you drive focus on sustainability of operations?
Embarking on a digitalization transformation can seem overwhelming, the road to sustainability equally so. Yet the two can flourish together: Digital transformation can turn sustainability into a winning business strategy. Organizations are increasingly turning to digital transformation initiatives to optimise efficiency and productivity as well as significantly reduce unnecessary their environmental impact. For manufacturers to truly make an impact they must think beyond product design and optimise their end-to-end production processes to minimise waste and maximise efficiency and productivity. The power of machine learning in enhancing the quality of the manufacturing process is getting increasingly recognized. AI and machine learning are becoming must-have popular tools for manufacturers to improve throughput, increased asset life, and optimize energy consumption.
Miraitek4.0 and smartFAB facilitate the dual transformation by helping our customers embrace the data revolution and use technology to increase sustainable practices. Providing them with the technological capabilities to break down data silos and harvest insights from the data they collect to receive the right information to make precise decisions at the right time. Our combined technologies put people at the center of decision making so they can use their creativity, analysis, communication, and teamwork to innovate solutions to the opportunities uncovered through digitalization. What’s more we work together with our customer to identify sustainability as a business objective and build sustainability goals in all of our projects. Sustainable manufacturing strategies are made possible because of better data, more accessible technology, and human creativity. We believe firmly that digital solutions have an important role to play in helping businesses develop sustainability strategies.
E.E: Tell us about sustainable energy solutions used.
Industry uses more than one-third of the energy consumed in the United States and Europe, yet manufacturers have traditionaly approached energy as a cost to be managed. While efficiencies gained through process optimization naturally result in energy savings across the production line, energy savings are often secondary to optimizing other production parameters, such as quality, throughput, and scrap rates.
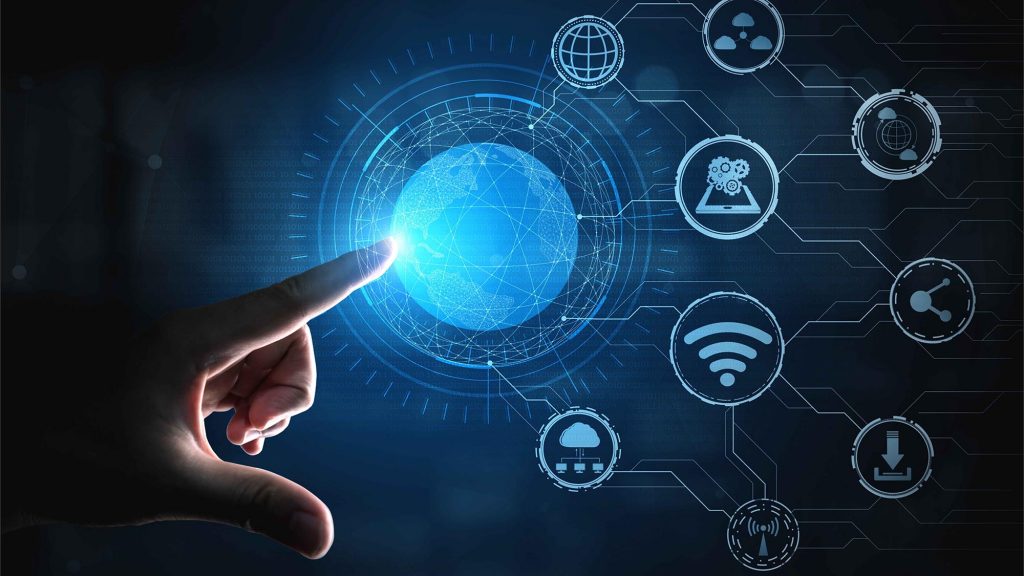
This is changing. How manufacturerers manage their energy use is an increasingly important differentiator for consumers, investors, and corporate customers. Leading firms in many sectors are developing energy strategies and developing new ways of using renewable energy. Hence, reducing energy costs and consumption is becoming an important target on its own.
AI-driven analytics applied to reduce energy consumption can uncovers hidden consumption, define new production parameters to reduce consumption, and improve global operating performance. An equipment manufacturer that monitors energy consumption can gain insights on machine usage and assess how an asset is consuming power as well as observe equipment performance and detect underlying mechanical problems.
The Miraitek4.0 and smartFAB platform collects data from equipment and Enterprise systems helping manufacturers achieve direct and indirect energy savings through managed energy usage, optimal machine use, reduced equipment failures, optimized process cycles, and reduced rework.
E.E: How do you see sustainability in the future?
Industry has an enormous carbon footprint. Through innovation, advanced analytics, digitalization, and process efficiencies this carbon-intensive sector can help shape a more sustainable future. Companies that design their business model prioritizing sustainability can help address global environmental issues while positioning themselves to succeed in the long term as the world encounters new challenges.
We see two variables in the equations.
Digital – Purpose-led, delivering for all stakeholders as a requisite for company success.
Circular – Combing technological innovation, environmental sustainability, energy efficiency and the use of renewable resources into a broad vision that redesigns the way we address scarce resources, global warming and waste mangement.
Sustainability is the future, hence innovating sustainably is the future of manufacturing. This will require innovation within sustainable business practices and manufacturing technology and regenerative thingking.
https://www.linkedin.com/company/11683820