ENDEGS developed the world’s first fully equipped, trailer-mounted, autonomously operating mobile incinerator. The company takes care of all hazardous substances in the explosion groups IIA, IIB and IIC, with a combustion efficiency of almost 100 percent.
ENDEGS is the market leader in terms of incineration performance. The capacity of their Mobile Vapour Combustion Units is scalable from 01. to 50 MW as needed.
Interview with Kai Sievers, CEO of ENDEGS Group.
Easy Engineering: Tell us about some of the most successful projects from this year.
Kai Sievers: Our portfolio includes a broad range of various emissions reduction services. Followed, we shortly introduce you the top 3 projects from this year.
Over the summer, we carried out one of our biggest projects yet. During a refinery turnaround in Germany, we executed TA-Luft conform degassing for several components and equipments.
For one of our regular and long-term clients, we also carried out the degassing of an inland barge that contained ammonia in order to prepare the vessel for regular inspection and maintenance. We have furthermore TA-Luft and ADN conform degassed an inland barge that contained butane.
Another one of our successful projects was of a bit of a different nature: we have rented out our ATEX Zone 0 robot to the UK for the first time – our client executed a no men entry tank cleaning.
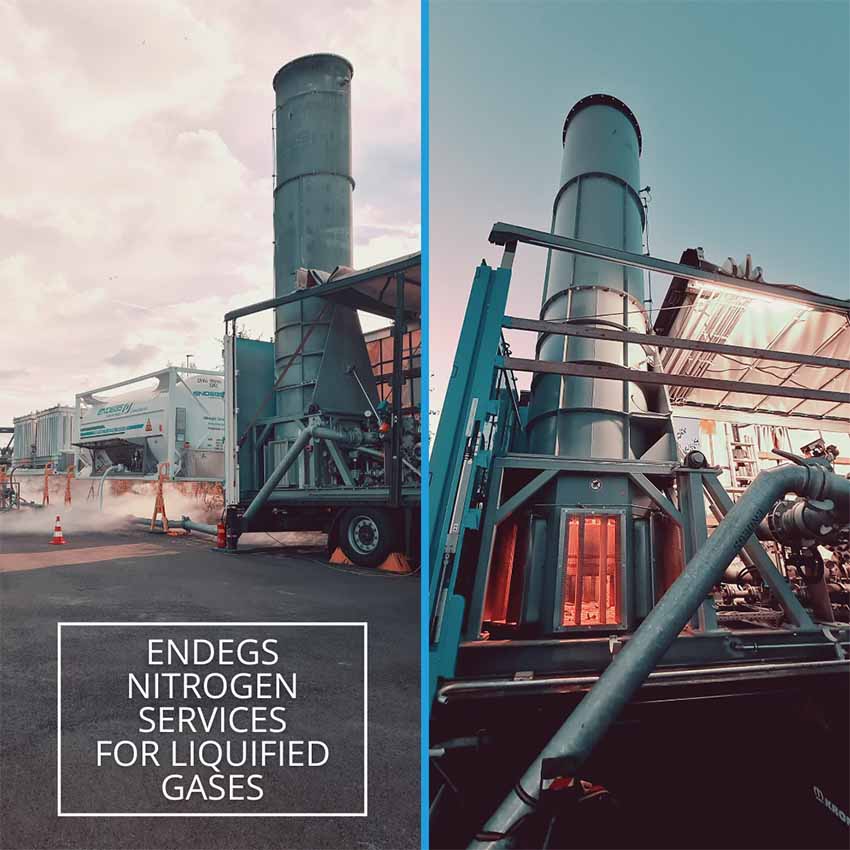
E.E: What were the challenges that you encountered?
K.S: In general speaking, the challenges in our industry are almost always the same. Our clients expect the best quality at the highest safety standards for acceptable cost. Therefore, we have to deliver reliable technology, reliable processes and a lean but effective organization to make it happen.
When we take a look into the projects mentioned above, the challenges during the turnaround project in Germany – which was probably our biggest one yet – was purely the organization of materials we applied: 3 combustion units, 1.9 km of mobile piping and hoses to only name a few things. For over two and a half months, we carried out the degassing of several equipments in the refinery. Among those was a broad range of columns, heat exchangers, mobile liquid storage tanks and more.
The challenges at inland barges with pressurized products like ammonia or butane (similar to LNG, propylene and others) – which are liquified products under high pressure – are different. It is purely a challenge of timing: an efficient degassing and purging process at minimal usage of N2.
At project number 3, the use of an ATEX Zone 0 robot for a no men entry tank cleaning is a completely different challenge – it is about to change the mindset in our industry away from dangerous manual work to the usage of advanced technology. Cleaning industrial tanks manually is a task that endangers the health of the personnel as they have to work in the hazardous ATEX Zone 0. Even despite safety suits and masks, they are exposed to a significant health risk.
E.E: How did you overcome the challenges? What ranges of products/solutions helped the beneficiary in the project/projects?
K.S: For these challenges, we applied three of our most used solutions: our mobile vapor combustion units (VCU), our mobile atmospheric N2 vaporizers with nitrogen tanks and the rental service for the ATEX Zone 0 robot. In the turnaround project, we used a total of three different VCUs and for the degassing of the inland barges with ammonia and butane, we combined our mobile units with the N2 vaporizer. It is also possible to combine combustion units with the robot for rent.
Our VCUs enable us to efficiently treat volatile organic compounds (VOC) and hazardous air pollutants (HAP) of all types of tanks, containers, pipelines, ships, barges and sea vessels so that they can be loaded, unloaded or reused. The mobile vaporizers with nitrogen tanks enable the purging and rendering insert of systems and system components that handle flaming liquids and gases. It is therefore ideally suited for working with complex products like hydrogen, ammonia, butane or LNG/CNG. The ATEX Zone 0 robot enables the efficient cleaning of industrial tanks– no workers have to risk their health in the dangerous ATEX Zone 0 anymore. The robot is remote-controlled and can be operated out of a cabin from safe distance with joy sticks.
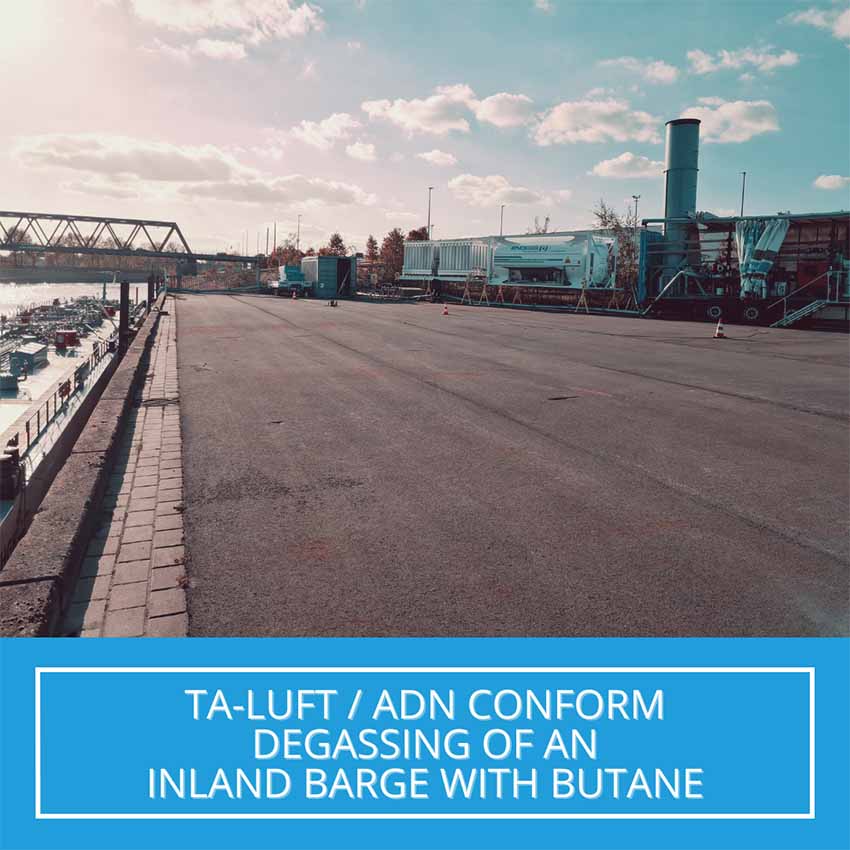
E.E: How were these products/solutions used to optimize the client’s business?
K.S: During a turnaround, our units ensure that the downtimes of facilities are reduced to a necessary minimum. Therefore, daily operations can continue undisturbed or with only a minimum of interference. As the business can keep going as usual during the entire degassing process, our customers can significantly save time and money. This is especially important when a project includes the temporary replacement of a stationary vapor recovery unit. Vapor recovery units and vapor treatment systems have to be inspected regularly to ensure their functionality in treating and removing vapors and pollutants in refineries and tank farms. This means a downtime for the VRU – and a facility without a functioning VRU is no longer allowed to operate. To prevent a downtime for the entire facility, our VCUs can treat vapors in the stead of the VRU during malfunctioning or maintenance, ensuring that the operations and business are not interrupted.
Our mobile N2 vaporizer is suited for the maintenance of pipelines, pipings, tanks, ships and bulk containers and can also be applied for emergencies, turnarounds and damages of ships or tanks.
In comparison to the manual cleaning of industrial tanks, leveraging the remote-controlled robot for rent is not only safer, but much more efficient and cheaper as well. For one, the chemical protection suites and respirators with air supply that are required for manual tank cleaning are very expensive. Furthermore, tank cleaning personnel are only allowed to stay in a tank for about two hours at the most. Therefore, as many as 18 workers are needed for three eight-hour shifts – and 18 hazmat suits and oxygen tanks per day. The ATEX Zone 0 robot only requires two workers for an eight-hour shift; neither needing protective equipment, neither being exposed to hazards and neither coming out of a hot tank drained and exhausted.
E.E: What innovative features do the products / solutions have?
K.S: The innovations at ENDEGS are a combination of cutting-edge technology combined with the knowledge and experience how to use them in an efficient way to reach the highest quality and safety standards at acceptable cost. Our innovative mobile VCUs make us the only company in Europe that burns all kinds of gases, gas compounds and vapors of the hazard groups IIA, IIB and IIC with a combustion rate of more than 99,99 % and no open flame at low noise during the operation. We even made mobile emissions treatment possible for the very first time by inventing and patenting the first fully equipped, autonomously operated, trailer-mounted vapor combustion unit world-wide. As one of the 100 most innovative medium-sized companies in Germany in 2021 and 2022, we seek to constantly improve our technologies. That we have extended our portfolio of VCUs that now includes units with four different combustion powers (3, 5, 10 and 20 MW) for different applications is proof for that.
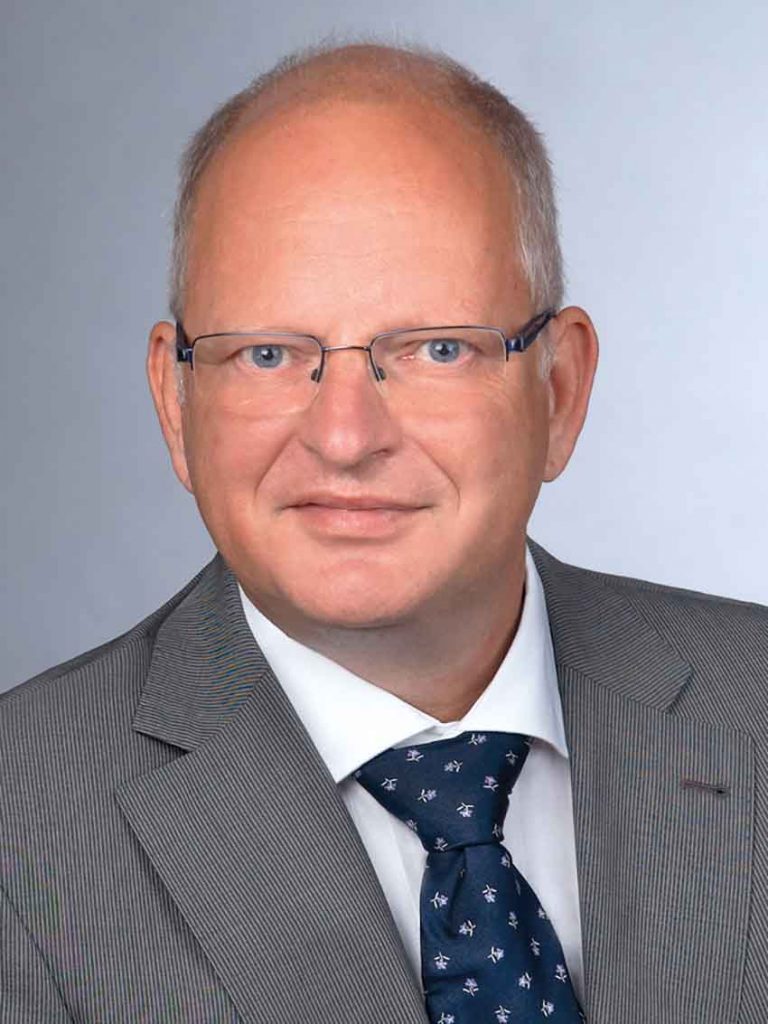
Kai Sievers, CEO of ENDEGS Group
Another innovation is our fleet of mobile atmospheric N2 vaporizers with nitrogen tanks which can be used for a new range of products that need to be degassed in an efficient way as for example cool down services (LNG) or heat up of BOG (boil off gas during cool down of LNG).
The innovation of the ATEX Zone 0 robot is in itself – the robot enables tank and industrial cleaning companies to increase their efficiency at lower cost and on a higher safety level. Due to its small size, mobility and versatile robot arm movements, the ATEX Zone 0 robot can be used in many industries for many different materials. For example, the robot can be used, among many other applications, for pit cleaning, petro-chemical cleaning, chemical cleaning, decommissioning cleaning, cesspit and septic tank cleaning and vacuuming applications. The rental service of the robot is a unique offer from ENDEGS to tank cleaning companies and can be perfectly combined with the nitrogen services or the VCU emission treatment or all together.
E.E: What products / solutions are you going to launch in the future?
K.S: At ENDEGS, we are always open minded and listen to our clients. We are deeply involved in strategies and processes to increase efficiencies in the maintenance of their plants. Therefore, we innovate year by year in new applications and products to treat or make the innovative portfolio available in new countries.
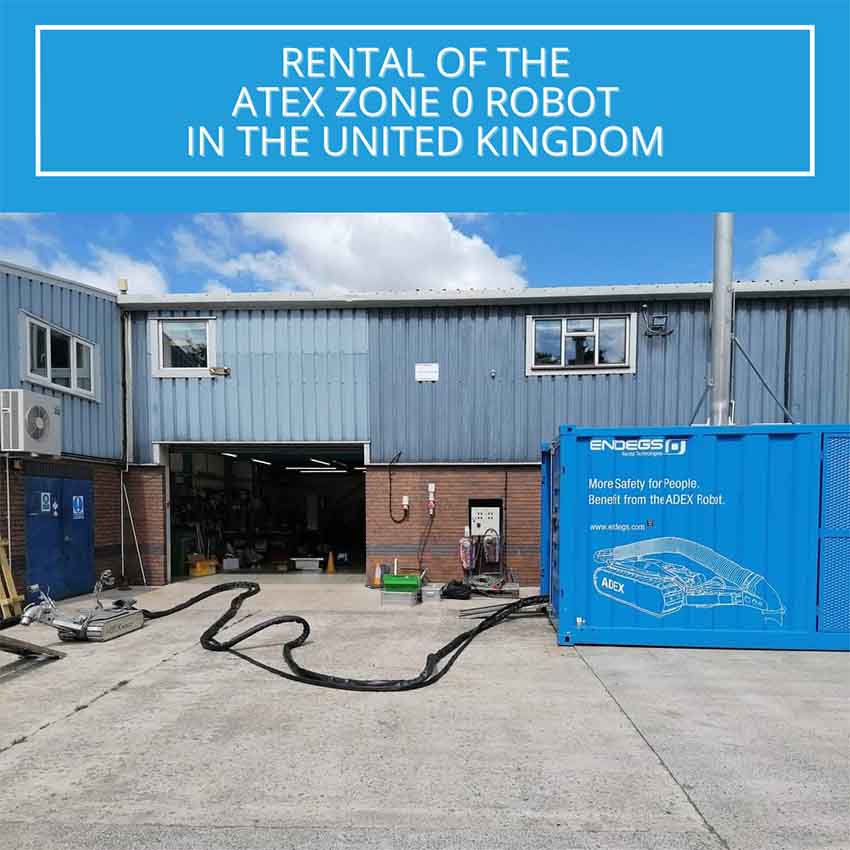
E.E: How will these products / solutions help future clients?
K.S: The output in every of our solutions has the aim to deliver a worry-free package to our clients. This includes the technology, the know-how – but also all our support to keep the operations of the client legally compliant. In the next years, we expect changes in the product mixes away from fossil fuels and an increase in new products like ammonia, LNG and also green fuels (e-fuels). We will further see revamps in the current infrastructure and the supply chain to transport the new products. In every step of the supply chain, there is a possibility to make use of our innovative solutions to increase the efficiency of the process while, on the other site, improving the environment.
E.E: What are your estimations for the end of the year?
K.S: Our vapor combustion units, N2 vaporizers and the ATEX Zone 0 robots for rent are well booked until the end of the year as we experience an even greater demand for sustainable emissions control. It is now widely known that we must contribute to reducing VOC & HAP emissions and that this benefits our environment significantly. Therefore, we constantly work to improve our technologies and services to contribute even further to the reduction of global emissions.