DC SWISS SA have been designing and manufacturing medium and high-end threading tools in the heart of the Bernese Jura, the cradle of micro-mechanics and machine tool production in Switzerland since 1940.
As a major player in the global threading tool market, DC SWISS SA has positioned itself as a specialist in a sector where quality, reliability and performance are essential. Excellence in product quality, technical support and customer training are priorities for this flourishing industrial company. The high-performance DC threading tools meet the strictest technological standards and are the result of numerous studies and expertise gained by the company over many years. Each tool undergoes multiple tests to guarantee optimum quality and to offer you the following portfolio:
- Taps from 0.3mm to 160mm
- Thread formers from 0.5mm
- Thread milling cutters from 2mm
- Thread whirl cutters from 0.3mm
- Thread gauges from 0.3mm (up to 3mm with internal testing and calibration according to ISO 17025)
- High performance thread cutting dies
- Acessories for thread machining
- Your custom-made threading solution for your individual application
Miniaturisation
You will always find a competent contact person, whether at the parent plant in Switzerland, at one of our subsidiaries in Germany, Italy, United Kingdom or at one of our technology partners or distributors situated around the World. Thanks to our presence on all continents in more than 50 countries, some with several partners, we respect the characteristics of the different countries. Each country has it’s own identification and different industries, but wherever machining takes place, threads are also needed. Success is a question of the right tool and all companies have to guarantee the precision and stability of their threaded connections. If, for example, you are active in microtechnology, medical technology or the watchmaking industry, we welcome you to DC SWISS, the world’s No. 1 in the field of micro-threads. We can offer you the most precise tools to cut, form or whirl a thread. We ask you to think also about the control of the threads, where we, as a manufacturer with an accredited test laboratory according to ISO 17025, guarantee SCS certification for a complete quality system on thread gauges from 0.3 to 3mm: Thread plug gauges, thread ring gauge, thread plug check gauges as well as calibration thread gauges for the calibration of your measuring machine. One global market trend is the progressive miniaturisation of devices of all kinds. The power density of computers and mobile phones is constantly increasing, active implants are getting smaller and the mechanical interface is moving with them, so you are in good hands with us for the smallest and safest threading solutions.

Download the catalogues https://www.dcswiss.com/en/download/
Lighter and stronger
Materials are constantly being developed further and, as a rule, their mechanical properties are improved. Weight reduction in aviation, in the automotive industry or in public transport leads to mobility that is more energy- and resource-efficient. Lighter titanium and magnesium alloys and high-performance polymers are increasingly finding their way into everyday goods. This increases the demands on the tools for machining and enables DC SWISS to continuously develop further. Our main catalogue, with more than 8500 standard articles, is divided into 2 volumes according to the machining technology: TC- Thread Cutting around tapping and thread forming and TM – Thread Milling for the use of CNC technology. Our classic thread cutting programme comprises 17 product lines specifically geared to the materials in 15 standard thread forms: M, UNC, UNF, G, NPT… Only a few months ago we released a new separate brochure for the aero sector, which guarantees conformity to the aerospace thread norm ISO 3161 / ISO 5855 with conforming radius requirements to the design norm. In connection with material development, you will of course also find solutions for thread machining of lead-free brass.
For high-tensile and abrasive materials with tensile strengths between 850 and 1400N/mm2, we have launched the new generation of the “H” line for AMB 2022. These taps all have a target-oriented cutting geometry, cutting edge conditioning and optimal DC “VH” coating for the process-reliable machining of alloyed steels, tempered steels and high tensile alloy steels. When the going gets tough, you will find the best solution here, these tools are also the most preferable for short chip brass + phosphor bronze + gunmetal, duroplastics and glass-fibre reinforced plastics.
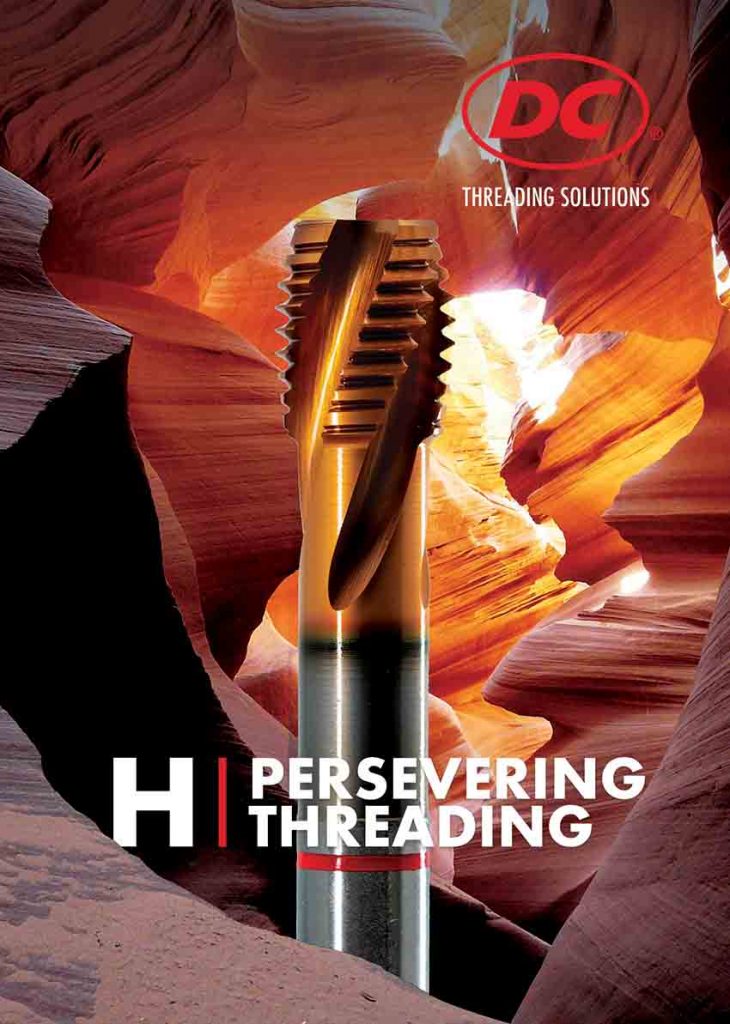
The perfect thread – GWi5000
Like thread milling cutters, thread whirl cutters are designed for machining internal threads on CNC machining centers. As a universal precision threading tool, the variety of applications can be achieved with one type of tool: Through-hole and blind-hole threads, right-hand or left-hand threads plus different thread sizes with the same pitch as well as different thread tolerances – all with one tool. The high quality of the thread and the optimum shape of the chips are additional advantages that make thread whirl cutters stand out compared to other methods.
As THE specialist for your threading applications, DC SWISS offers you the thread whirl cutters made of high-quality carbide summarized in 4 product lines:
- Series 1000: The smallest, single tooth, for Ø 0.3-1.4mm and depth up to 2.5xD
- Series 2000: Multi-tooth, 1 cutting plane, for Ø0.5-6mm and depth up to 2.5xD
- Series 3000: Multi-tooth, double profile, Ø0.8-20mm and depth up to 4xD
- Series 5000: The perfect thread for highest demands
The latest generation of 5000’s enables the production of the perfect thread: No burr formation between flanks and core diameter, optimum surface finish quality and the best chip evacuation enabled by our perfect internal coolant system. The thread whirler not only cuts the thread profile but also the pre-drilled core diameter to the corresponding nominal dimension in one single step. This quality of thread is particularly important medical component production, subsequent deburring as an additional step is saved, thus increasing economic efficiency. The ground solid carbide tool with internal cooling and our VS coating has excellent heat resistance and is unequalled in both thread quality & high-speed machining.
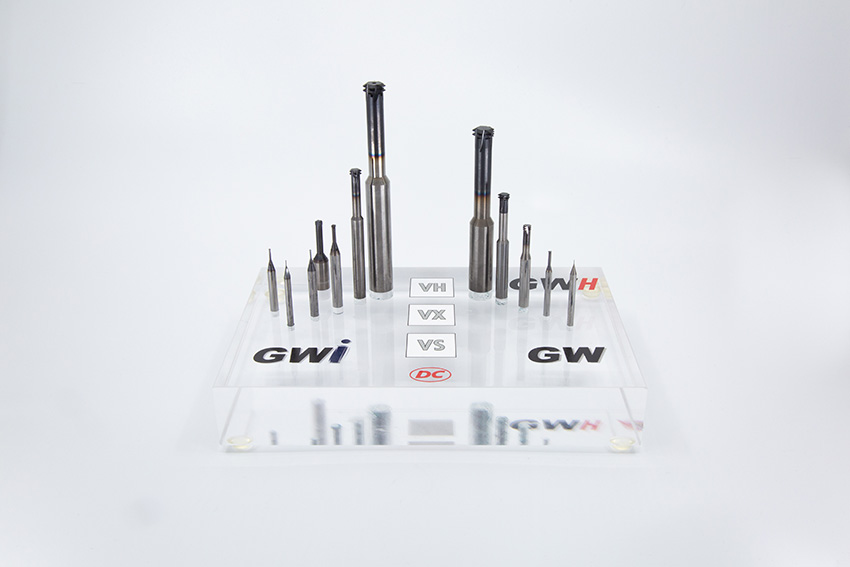
Be ready today for tomorrow with the QTap – The perfect Allrounder
Today’s subcontractors are often working under the pressure of a deadline when processing different materials. Especially in an increasingly volatile environment where the time window between the customer’s order and delivery needs to be as short as possible. Frequent tool changes to satisfy small batch sizes are a cost burdon to the company and result in tied-up capital due to the large and varied number of tools required in the company. The new QTap provides a remedy: this multi purpose tap with perfect chip control sets new standards in the NC-tapping process. The integration of its functionality, versatility and performance are characterised in this latest tool from DC SWISS. Available in spiral point for through holes & a strong spiral flute design for blind holes, QTap offers optimum chip removal and allows the customer to machine in a conventionally or rigid synchronous method in carbon steels, heat-treatable steels, stainless steels, aluminium, cast iron and brass. For larger batch sizes the Qtap line up is available with internal cooling which always serves to increase performance.

DC SWISS SA
CH-2735 Malleray,
+41 32 491 63 63