Success through growth, growth through success
Modern industrial production depends on constant technological progress. Without it, the urgently needed growth is not possible. Without growth, there is no investment. Without investment, the competition will soon be faster and cheaper.
Our little episode at the beginning shows where this can lead. Outdated work processes cause problems. The production is faulty, the employees are already exhausted in the morning and the management is dissatisfied. A downward spiral that goes on and on.
An assistance system and comprehensive digitalization can help here. Because it supports the worker on the shop floor. But there are quite a few of them on the market. Which features are important? What should such a digital colleague be able to do? And which technical gadgets can a company do without at the moment?
Skills and characteristics
To answer these questions, the company’s needs must first be outlined. How large are the components? At which points do errors occur? Which parts of the process should be optimized? If it is a problem in quality assurance, for example, different measures need to be taken than if there are delays in incoming goods or a high complaint rate.
Let’s return to our example. The problems are clearly in manufacturing. The error rate quickly destroys potential gains. A digital assistance system must be able to provide support at this point. In addition, the workload seems high, as the individual work steps require deep concentration. The result is more mistakes. The intelligent colleague must also provide relief at this point.

Fast and reliable recognition: The assistant must be able to recognize a workpiece. As quickly as possible, absolutely reliably and unambiguously. A selection from a database via a screen is impractical. The most sensible way, because it is the fastest as well as the most intuitive, is an optical detection. The worker places the workpiece on the table. The digital colleague recognizes it and can assist immediately.
Practical instructions: A complex workpiece is assembled in several steps. These must be precisely coordinated, carried out in the right order and be exact. Deviations and errors lead directly or indirectly to problems, sometimes already in the advanced manufacturing process, often only when the components are put into operation. A digital assistance system guides the worker through the individual steps. The steps to be carried out are explained by means of animation or short videos on a screen. This helps new employees enormously and is also a useful support when there are a large number of variants.
Control and correction: Piece by piece, the worker assembles the individual components, screws, solder or glues where necessary. The digital assistance system watches him and checks whether a work step has been carried out correctly. In case of an error, the system gives a corresponding hint. The worker can then correct it immediately. In this way, complaints and returns can already be avoided during production.
Bonus – Visual Support: Especially for tasks that require a high degree of concentration, it is problematic to have to keep looking at the screen. It is more helpful if the necessary instructions are visible directly on the workpiece. This is possible in two ways:
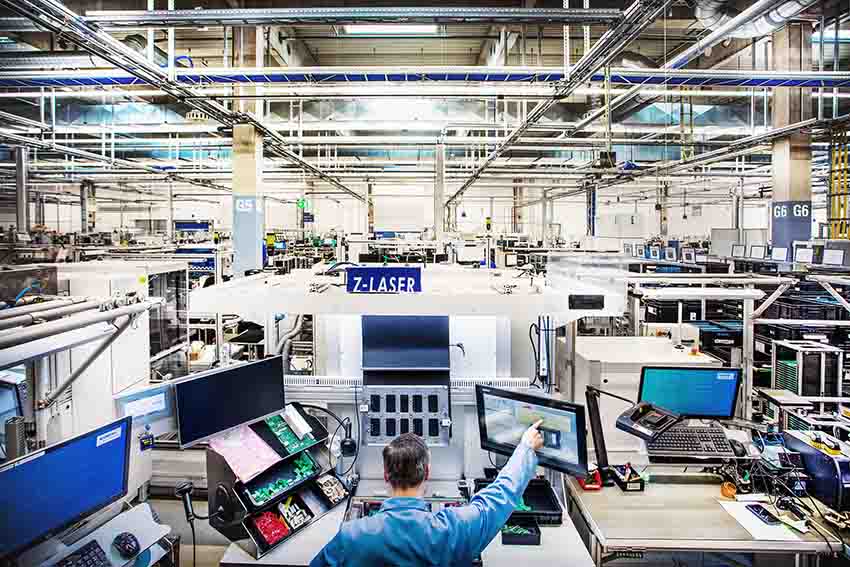
The more elaborate variant would be augmented reality. All relevant information is projected directly into the worker’s field of vision via glasses. The disadvantages of this method are the costs and the effort required for digital porting. The required computing power and the battery life of the glasses are also a problem.
A laser system projects the assembly points, instructions (arrows or lines) but also the outlines of entire components directly onto the workpiece. The projection remains even if the worker moves his hand. Interruptions and resulting errors are avoided.
Bonus – Self-learning Systems: Digital assistance systems of the latest generation are smart. They recognize workpieces regardless of their position, can compare them in real time and match them with examples from their internal database. However, all kinds of malleable materials, such as fabrics, pose a major challenge for rapid detection. Since these are always present in a different shape, the digital assistance system finds it difficult to identify them unambiguously. Self-learning systems provide a remedy. These are designed in such a way that after thorough training with hundreds of possible fabric samples, they can deduce for themselves what further variants would look like in order to reliably recognize them.

Support from Smart Klaus
A digital assistance system that meets all these requirements is the Smart Klaus from the company Optimum datamanagement solutions GmbH. The German-based company has been on the market for more than 25 years and has since consistently optimized and expanded the optical identification, image processing and worker support of its digital assistance system. Smart Klaus is enormously flexible and is used with its visual identification capabilities not only in production, but also in incoming inspection and quality assurance.
Numerous well-known companies from all industries are among Optimum’s customers and use the Smart Klaus. This is because the intelligent colleague not only provides support, but can also record new information. This information can be processed and made available to different departments of a company as needed. In this way, knowledge is made available to all – and comprehensive digitization is made possible in the first place.
Digitization with Smart Klaus – an example
Our example company from the beginning of the report acquires Smart Klaus as a digital colleague for its workplaces. From now on, he accompanies all processes, guides, checks and corrects. Productivity increases, the error rate decreases, profits rise. The boss is satisfied and the foreman is also much more relaxed. This also removes the high pressure from the employees, who are correspondingly more concentrated and motivated.
But that is not all. On request, Smart Klaus documents every single production step and stores the relevant information in a database. Warehouse and logistics are informed immediately and can prepare accordingly, which speeds up packaging and shipping considerably.

This information is not only of interest internally. The customer is also informed immediately when his order has been processed and is being prepared for dispatch. In addition, he receives data on the flawless production of the individual components on request. Returns and complaints are thus virtually eliminated. The Smart Klaus not only speeds up production, but also the entire manufacturing process thanks to consistent digitalization.
Digital support for every business
Growth is the foundation of our economic system. But the constant striving for more always presents companies with challenges. New technologies have to be integrated into existing workflows. An expansion of the infrastructure becomes necessary. Training for employees’ costs time and money. And those who rely on the wrong technology soon lose out.
With Smart Klaus, these challenges are no problem. Integration into the workplace is quick and easy thanks to intuitive controls and visual feedback. An extensive training period is not necessary. Employees receive extensive instruction, either face to face or digitally via Teamviewer. Those who want to be at the forefront of manual production in the next few years will not be able to avoid the digital colleague.

OPTIMUM DATAMANAGEMENT SOLUTIONS GMBH
Adress: Neureuter Straße 37a
Phone: +49 721 570 44 95-0
Email: sales@optimum-gmbh.de