Companies frequently use transport racks for their deliveries. Shrinkage, bottlenecks, and constant re-procurement are often a considerable problem. A start-up has now developed a solution to create transparency and reduce loss.
Founded in 2018, Munich-based start-up BOX ID Systems offers end-to-end tracking solutions to identify and localize various logistics assets in the industrial supply chain across Europe, digitally and cost-efficiently: from site to site, on company premises and indoors. “Glass manufacturers use the racks to bring their goods, such as insulating glass or windows, to their customers: they arrive full and return empty,” says Christian Trösch, Sales Manager at BOX ID Systems. “Since the availability of empty racks is important to remain able to deliver, a certain number of pieces must always be available in production.”
Tracker and Software form a Complete Solution
According to the manufacturer, the BOX ID System is a complete solution that includes a specialized software platform, tracking devices and efficient data, device, and user management, including functions to support automation and process improvement. Logistics processes are thus carried out efficiently and cost-optimized, and critical processes run transparently. “With the trackers and the software, we are mapping a complete solution that replaces error-prone, manual rack management with a smart, digital one. The solution creates a fair and transparent data basis for all parties using the traceable racks,” says Wolfgang Vogl, CEO of BOX ID Systems.
The benefits for the user are among others:
- Shrinkage reduction and, associated with this, cost savings for rack re-procurement,
- Fast return of empties,
- Avoidance of bottlenecks due to missing racks in production,
- Reduction of manual effort in rack management.

Upgrading Made Easy
The glass industry is already using the solution to track racks for flat and insulating glass. According to BOX ID Systems, the racks are equipped with cost-effective and durable trackers that record the current location and all movements of a rack throughout Europe.
The battery-powered trackers have a runtime of approximately five to seven years and can be mounted on existing racks as a retrofit solution. “Our active trackers can be easily screwed onto the racks. The pool can be managed digitally using our software,” says Trösch. Evaluation and use of the localization play the decisive role. “Where is the rack currently located and how did it get there? A Bavarian manufacturer with a delivery radius of about 200 kilometers can track the causes when he sees his rack in southern Spain, for example.”
Rack Management Software
The data can be accessed via an easy-to-use web application. The software offers various functions that simplify rack management. It enables a continuous, automatic inventory of the rack stock – this makes it possible to see directly how many racks are at the various customers.
The unique selling proposition (USP) of the complete solution is characterized as follows:
- Retrofit solution for simple equipping of the existing rack inventory,
- Europe-wide tracking as well as long-life trackers with a service life of several years,
- Easy access to the location of the racks via a web application – even by the driver on the road,
- BOX ID software for rack inventory management, which includes the following functions: automatic inventory overview of all racks across all customer and production locations, easy location and tracking of individual racks, as well as special rack management functions, such as clearance management or the recording of the number and duration of racks at customer sites,
- The solution can be complemented by other data sources such as QR code label scan.

Inventory Check and Laytime
The loss of racks at the plants is noticeably reduced. A misuse by the supplied customers can be easily recognized if they use the racks for their own deliveries, for example. Suppliers usually must manage the empties manually on slips of paper – but the system is prone to errors due to, for example, numbering errors or a lack of overview. A shrinkage in the warehouse would always require an annual, cost-intensive repurchase.
The individual racks can be tracked directly. The glass manufacturer thus has an overview at all times of the rack distribution at the customers and on its own production sites. “Racks often disappear for various reasons: For example, some customers have no motivation to return the racks because they have forgotten to do so, they use the racks for their own purposes, or another company also takes them from a construction site by mistake,” says Trösch.
Transparent Succession Process
The solution is designed to encourage a manufacturer’s customers to return the racks. According to BOX ID Systems, a cost- and rent-free rack can entice customers to use it themselves. For this reason, various companies charge deposit fees or a rental fee, starting on an agreed date. The BOX ID system helps with the follow-up process to determine the layaway period, mark racks as due for rental and initiate business activities that are important in rack management. “The company can address the customer accordingly – based on the exact information,” Trösch says. “Misunderstandings can likewise be prevented if manufacturers and customers have different opinions about the lay days or number of returned racks.”
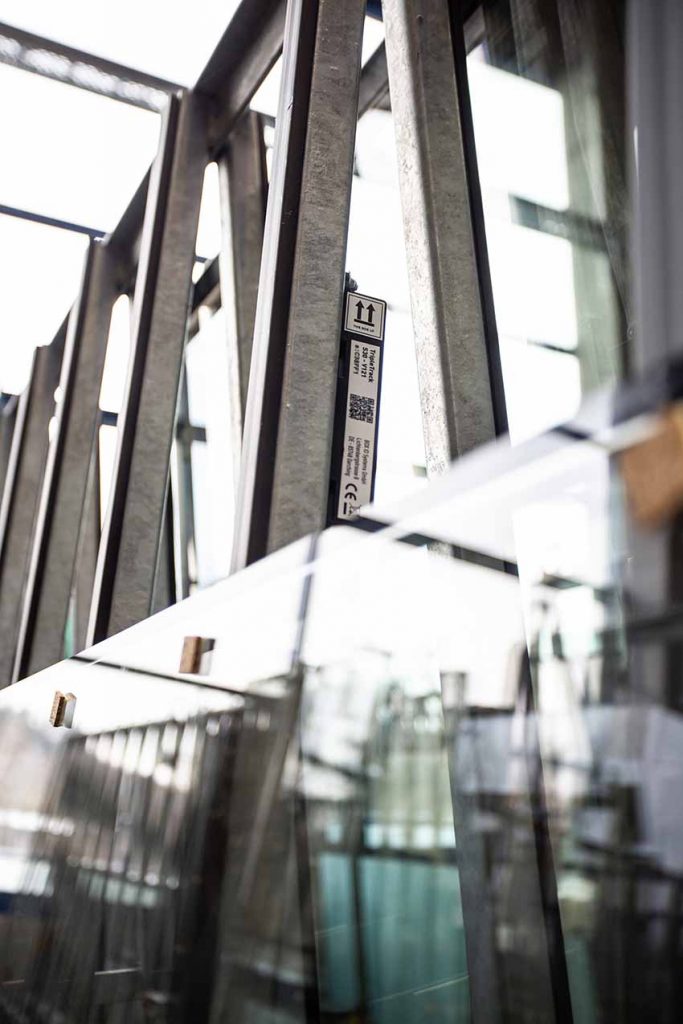
Scan as an Additional Function
Another option: QR codes can also be attached to the racks in addition to the active trackers, if desired. Customers use these to report their racks as ready for pickup, or drivers report the rack as delivered, which immediately appears in the software.
A driver can check for empty racks near him while on the road via his smartphone as soon as a rack is manually or automatically marked as ready for pickup in the BOX ID software. “The QR code is part of the package if desired and allows to interact with the rack. The scan can be used for various processes and actions,” says Trösch. “For example, the customer can report the rack as ready for pickup, or the driver can digitally acknowledge the delivery.”
This is what the Partners say
BOX ID Systems in action
- WEHA-THERM – Customer
Glass producer Weha-Therm has already fully digitized its rack inventory. “With the BOX ID solution, we can keep an eye on our rack inventory at all times,” says Daniel Freund, Managing Director of Weha-Therm.
- HELIOT – Network Operator
The responsible network operator Heliot, exclusive Sigfox network operator for the DACH region, also assures digital traceability. “The energy-saving Sigfox 0G network, which is available throughout Europe, enables the racks to be tracked in a straightforward manner, for years and maintenance-free,” says Thomas Scheibel, CEO of Heliot Europe.