As a leading Icelandic chemical analysis innovator, DTE specializes in real-time analysis of molten metals, driving digital transformation in the aluminum industry. Their solutions provide cutting-edge solutions for continuous monitoring and optimization of the production process, enabling companies to enhance operator safety, efficiency and sustainability in the aluminum industry.
Interview with Karl Matthíasson, CEO & Founder of DTE.
Easy Engineering: What are the main areas of activity of the company?
Karl Matthíasson: Our primary focus lies in developing and providing solutions that combine state-of-the-art chemical analyzers for real-time compositional analysis of molten metals and our cloud platform IRIS which transforms the data from the analyzers into actionable insights. Additionally, we offer consulting services and engage in research collaborations to continually advance our technology and foster industry-wide innovation.
E.E: What’s the news about new products/services?
K.M: DTE continues to innovate, with recent developments aimed at accelerating the development of our next-generation solutions. We’re bolstering our talent pool with specialists in software development and engineering, enhancing our capability to tailor solutions to meet the evolving demands of the market and exceed customer expectations.
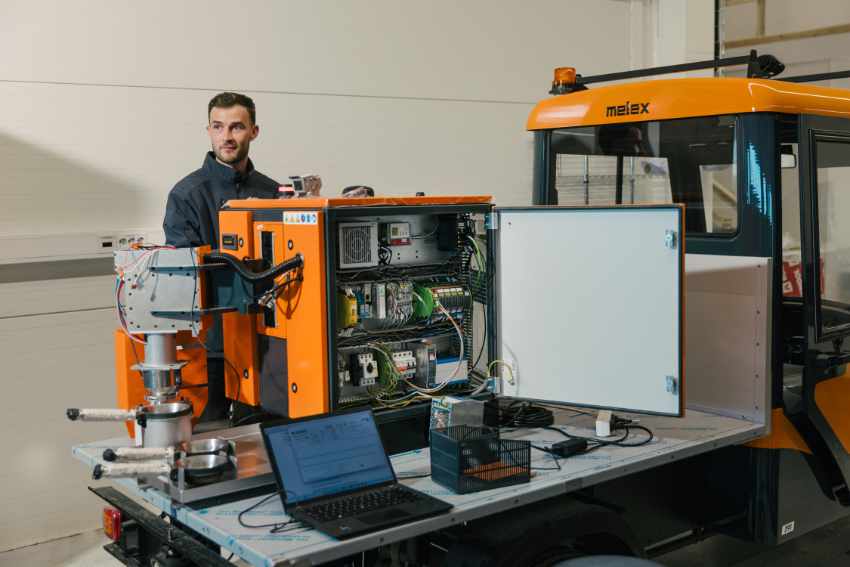
E.E: What are the ranges of products/services?
K.M: DTE’s product range encompasses cutting-edge chemical analyzers designed for real-time compositional analysis of molten metals. Our LP-LIBS liquid metal analyzers come in various models, including potroom, crucible, furnace and launder solutions. These analyzers provide live data to our IRIS live process intelligence platform, enabling comprehensive process control capabilities at every stage of the process and empowering our clients to make informed decisions and enhance operational efficiency. Furthermore, DTE’s solutions automate the sampling and analysis process, eliminating the need for operators to handle molten metals, which mitigates significant risks and increases operator safety.
E.E: What is the state of the market where you are currently active?
K.M: The market where DTE is active, primarily in the aluminum industry, is experiencing rapid evolution driven by increasing demand for sustainable and efficient practices. address these market needs by providing real-time insights and process optimization capabilities. This includes not only the primary aluminum sector but also the secondary aluminum market, where recycling plays a pivotal role in sustainability efforts. DTE’s technology enables real-time monitoring of melt composition during the recycling process, empowering recyclers to optimize the use of materials and maximize the recycled content in each batch. By increasing the recycled content in products batch-by-batch, our solutions contribute to lowering production costs and reducing the carbon footprint, aligning with the industry’s sustainability objectives.
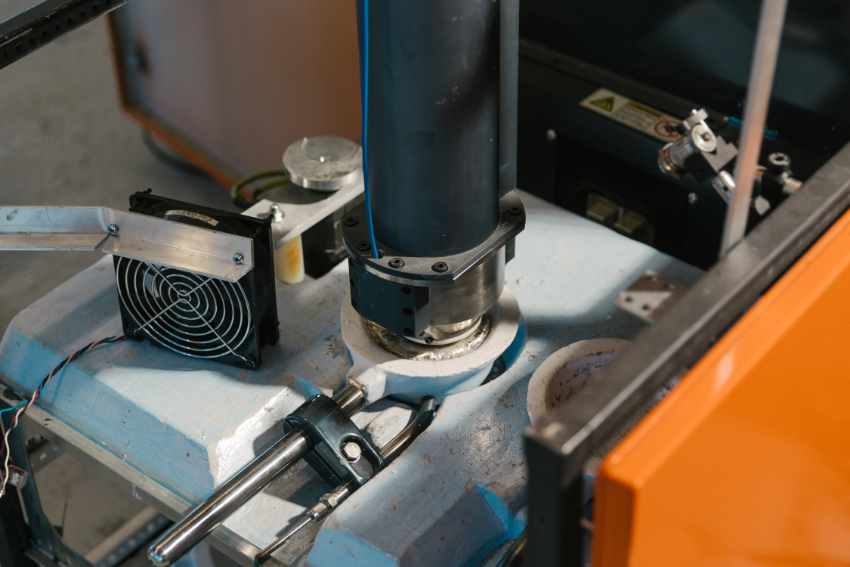
E.E: What can you tell us about market trends?
K.M: Market trends in the aluminum industry indicate a growing emphasis on digital transformation, automation and sustainability. Companies are seeking innovative technologies to improve efficiency, reduce waste, increase safety and minimize environmental impact, aligning perfectly with our core offerings and growth strategy.
E.E: What are the most innovative products/services marketed?
K.M: Our analyzers utilize Laser-Induced Breakdown Spectroscopy (LIBS), specifically designed for molten metal analysis, known as liquid-phase LIBS (LP-LIBS). LP-LIBS offers advantages like direct liquid metal analysis without sample preparation, enhancing safety and ensuring consistent results, crucial for real-time decision-making in industrial processes.
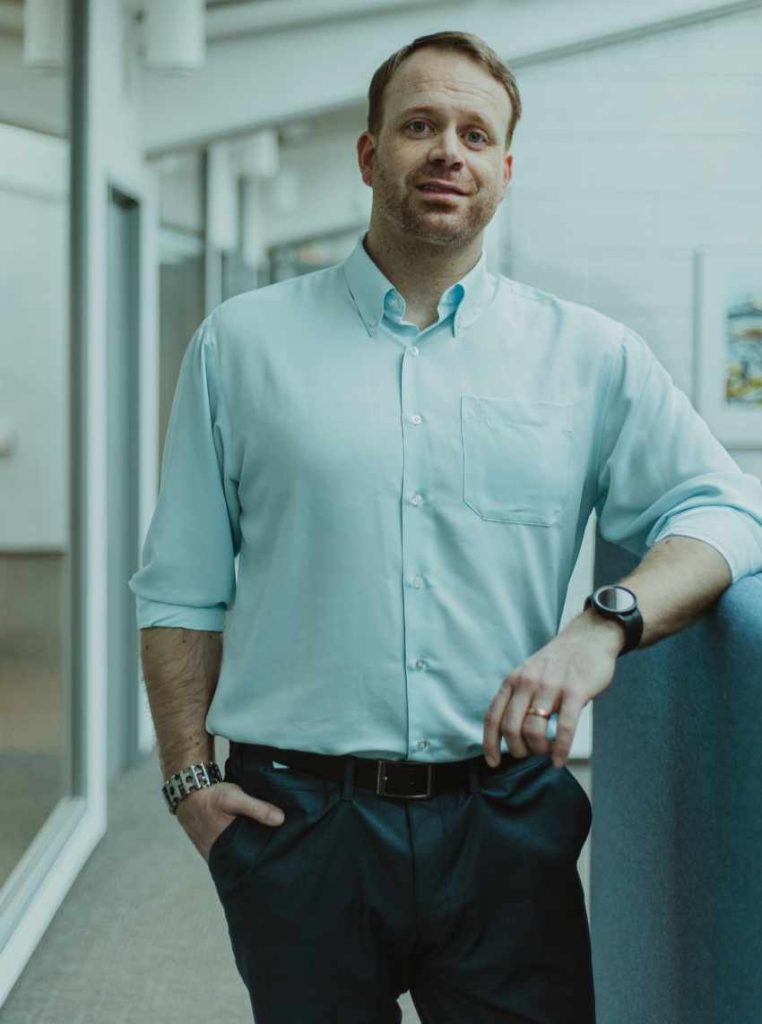
E.E: What estimations do you have for 2024?
K.M: We anticipate continued growth and innovation throughout 2024, driven by our expansion into a new headquarters, significant staff growth, and ongoing advancements in product development. With our focus on digital transformation and sustainability, we’re poised to make substantial contributions to the aluminum industry and exceed customer expectations.