Conveyor belts are critical components that can be surprisingly complex. Their reliability and efficiency can make or break an operation. At the same time, they are a very significant overhead. For more than 50 years, Netherlands-based Dunlop Conveyor Belting have been one of the leading and most well respected manufacturers of high-performance conveyor belting in the world. Who better, therefore, to provide a regular feature in Easy Engineering that helps to provide some expert advice and guidance? Here, Rob van Oijen, Dunlop’s manager of application engineering looks at a common problem affecting conveyor belting, which is ripping, tearing and impact.
The most destructive force
Even the strongest, heaviest multi-ply and steelcord belts can be punctured and ripped by a foreign object becoming trapped. A belt can quite easily be ripped apart longitudinally over its entire length in a matter of minutes. I recall an incident where a wooden broomstick became trapped at the conveyor head. It penetrated a steelcord belt and ripped 4 kilometres of belt from end to end. The cost of repairing and replacing belts, both in monetary terms as well as lost production, can have very serious consequences indeed. Despite this, most manufacturers make little or no mention of the rip and tear resistance of their belts.
Rip and tear resistance – testing
The ability to withstand the forces that rip and tear belts is often more important than any other physical attribute. A ‘rip’ is best described as what happens when a sharp object punctures the belt and cuts the belt lengthwise as it is pulled against the trapped object. In contrast, a ‘tear’ is what happens when a section of belt is pulled apart in opposing directions, much like when a telephone directory is torn apart by hand as a feat of strength.
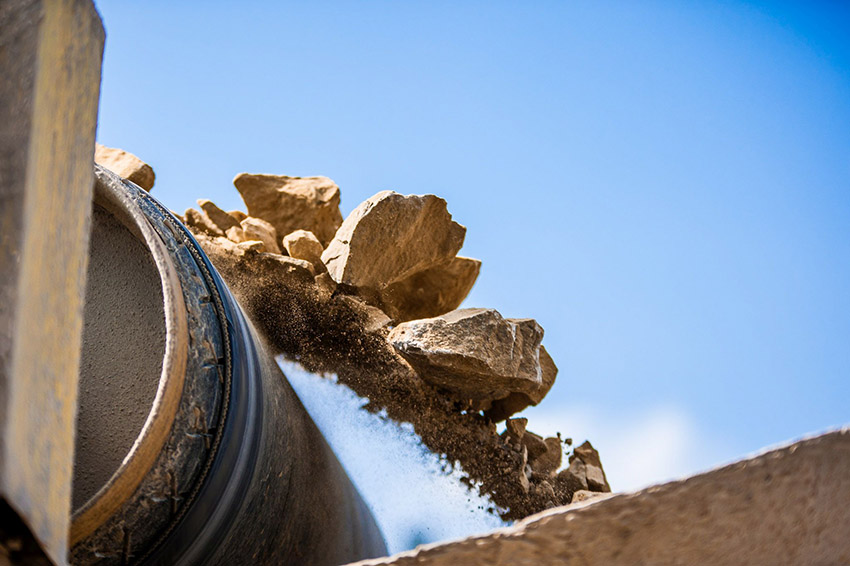
Surprisingly, despite its significance as a key performance indicator, there are currently no internationally accepted test methods or standards for testing rip resistance, which is perhaps one reason why belt manufacturers rarely mention the subject. However, in Dunlop we regard rip and tear strength as very important KPI’s. What our laboratory technicians do is pull sections of belt through a right-angled piece of metal under extreme force and carefully measure and record the level of force exerted. The technicians have nicknamed the specially designed equipment they use for this harsh treatment ‘Jack the Ripper’.
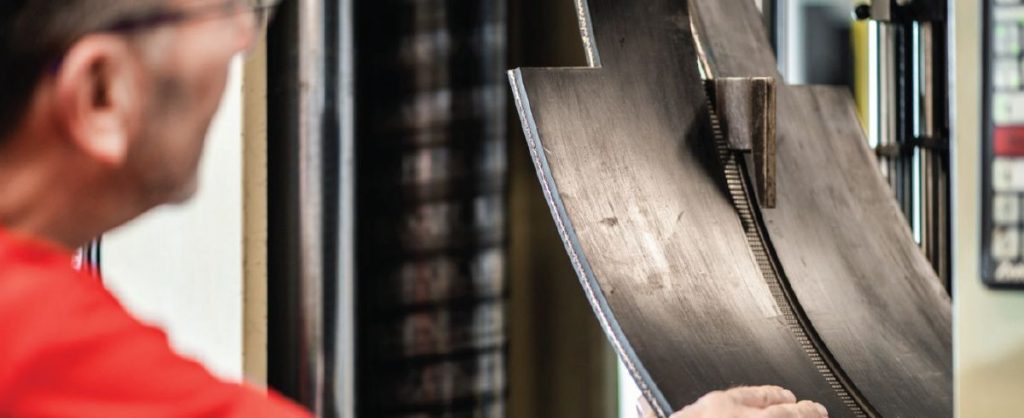
Unlike rip resistance, an international standard for tear strength does exist. The ISO 505:2017 test method measures the propagation resistance of an initial tear in textile conveyor belts, either in full thickness or of the carcass only. The test is intended for application to multi-ply (fabric) belts in installations where there is a risk of longitudinal tearing.
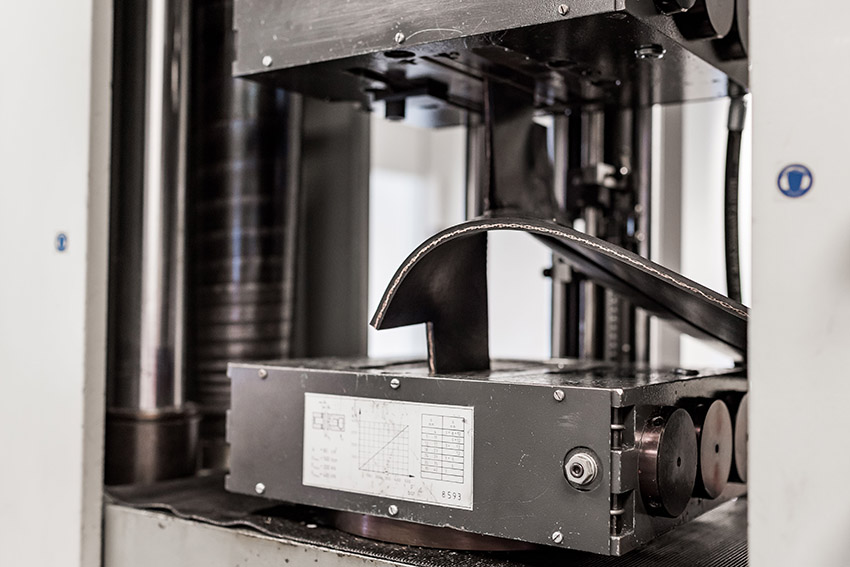
Although it is a defined method of testing there are no standardised performance requirements. The test, often referred to as the ‘trouser test’, basically consists of mounting two cut ends of a test piece of belting in the jaws of a tensile testing machine. An initial tear made in a test piece, which is then pulled apart in opposing directions. The force necessary to propagate the tear is then measured. Examination and analysis of the multi-peak tear resistance test traces is made in accordance with ISO 6133.
Finding the best solution
Because of the huge differences between the types of materials being conveyed, the design of the actual conveyor systems and their working environments, there is no ‘silver bullet’ answer to the damage caused by ripping, tearing and impact. It is a common misconception that increasing the cover thicknesses and/or the number of plies improves resistance because that is simply not the case. In fact, belts that are too thick can cause other problems such as lack of troughability and steering and handling difficulties. Especially in Eastern Europe for some reason, it is not uncommon to see belt specifications of 1000/6 10+4 or even heavier. Whenever I see specifications like these, I can be pretty confident that there is an underlying problem with ripping and tearing.
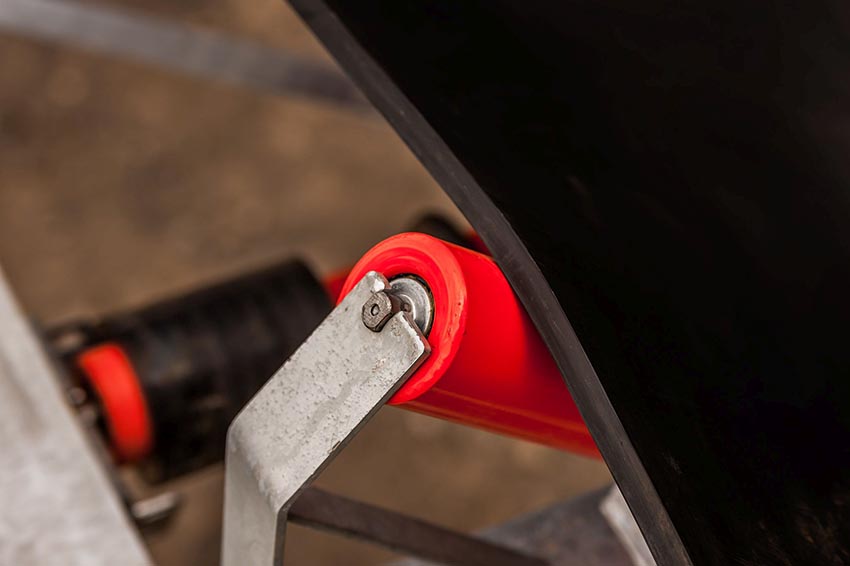
Another answer might seem to be simply replacing the multi-ply belt with a steelcord belt, but this is also extremely unlikely to provide the solution. Conveyors using steelcord belts have to specifically designed. Because of their innate tensile strength and low elongation (stretch), steelcord belts are really only suited to conveying over longer distances. In any case, their Achilles heel is that although the actual steel cords themselves are very strong, they cannot prevent a trapped foreign object from penetrating through the rubber covers, between the cords and ripping the belt longitudinally.
Engineered for the task
All the experience and evidence point to the fact that for multi-ply belts on conveyors where ripping and tearing is a problem the only genuinely effective solution is to fit a conveyor belt that has a construction that has been specifically engineered for the purpose. Such belts can have a level of resistance against ripping and tearing and cope with the impact of heavy objects falling from a high drop height that are several times higher compared to belts that use a conventional fabric ply construction.
Belts that have been engineered to resist ripping, tearing and impact use uniquely designed fabric plies that allow the nylon strands to stretch. As the trapped object is being pulled through the belt, the strands of the special ply construction gather together into a bundle that can eventually become strong enough to stop the belt.
Strange as it may seem, special synthetic plies are usually more effective than steel when it comes to actually minimising the length of a rip. I am an engineer, not a salesman, but I can tell you in all honesty that the two best examples that I have ever come across are Dunlop UsFlex and Dunlop Ultra X. They are both totally unique to Dunlop and both belt types have at least three or more times the resistance to ripping and tearing compared to conventional belt. To find out more simply go to: https://www.dunlopcb.com/cover-grades/rip-impact/
Using breaker plies to increase rip resistance
For steelcord belts, the best solution tends to be the use of breaker plies, which provide a significantly increased resistance against longitudinal ripping. Ultimately, the use of breakers is one of damage limitation.
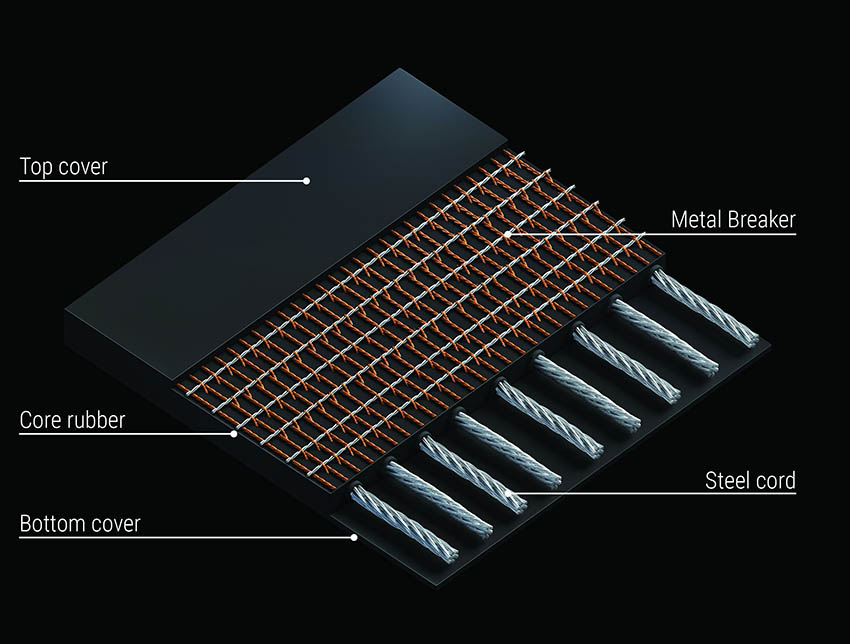
The breaker ply performs two functions – firstly it can help prevent the penetration of the belt by a foreign object. Secondly, the breaker ply acts as a barrier if an object does actually penetrate between the steel cords and starts to rip along the length of the belt. Breaker plies are embedded in the rubber covers during the manufacturing process. There are numerous types and strengths of breaker used. The lighter weight versions are designed to simply absorb and dissipate energy whereas stronger, heavier weight breakers can actually stop the belt and limit the amount of damage even more effectively. These are commonly referred to as ‘Rip Stop’ breakers.
Not worth the sacrifice
Rather than look for belts that are capable of handing the demands, many operators decide to opt for what they see as the cheaper option by fitting low grade, ‘sacrificial’ belts that are then repaired and replaced at frightening regularity.

But when you add the cost of constant repairs, the labour costs involved with fitting replacement belts and the cost of lost production to the cost of buying replacement belt after replacement belt, it simply does not make economic sense.
Author: Rob van Oijen, Manager Application Engineering for Dunlop Conveyor Belting