Since its inception in 1960, ELGi has adopted innovation as a critical differentiator, keeping pace with global compressor technology trends and evolving customer needs. This approach has primarily contributed to “what we are” and “where we are” today. ELGi stands tall as one of the global leaders in the compressed air industry. Customer value and quality have been intrinsic to our DNA. We aspire to be a dominant player in the global air compressor market, and innovation will be critical in achieving our aspiration.
Interview with Dr. K. Venu Madhav, Director – Technology at Elgi Equipments Limited.
Easy Engineering: How important are innovation and R&D for actual and future products?
K. Venu Madhav: Innovation and R&D form one of the core strategic pillars of ELGi. The company has focused on innovation, building fruitful research, and business partnerships that have resulted in developing indigenous compressors and related components. With decades of experience, we believe in constantly evolving to meet our customers’ changing needs across business segments and countries.
Today, our 130+ member strong technology innovation team is spearheaded by proficient specialists and engineers who are experts in diverse subsystem domains and have niche technical skills. They constantly work on improving our product quality and its reliability. Every day we improve and change small things which make a difference in the performance of our machines. ELGi also invested further in research and development, leading to the establishment of our research center in Bangalore, India, which boasts state-of-technology equipment and uses simulation as the base for design thinking and creating products for the future.
E.E: What are the needs of the users in the markets that you are active?
K.V.M: While we continue doing business in 120-plus countries across the world, Europe, North America, India, Indonesia, Thailand, and Australia are our key strategic geographies where our focus will remain strong.
Regardless of geography, one of the biggest portions of the life cycle costs of a compressor is its electricity consumption. Customers focus on reducing their energy consumption via highly energy-efficient products.
At ELGi, we have continuously improved the energy efficiency of our compressor models over the last 20 years, helping our customers reduce their energy footprint and contributing to a greener environment. Our customers seek compressed air solutions that expel less oil into the atmosphere. When there is no oil in the compressed air system, it is more environmentally friendly. Hence, we introduced a water-injected compressor in 2019. In addition, many of our product solutions contribute to the environmental well-being of the planet.
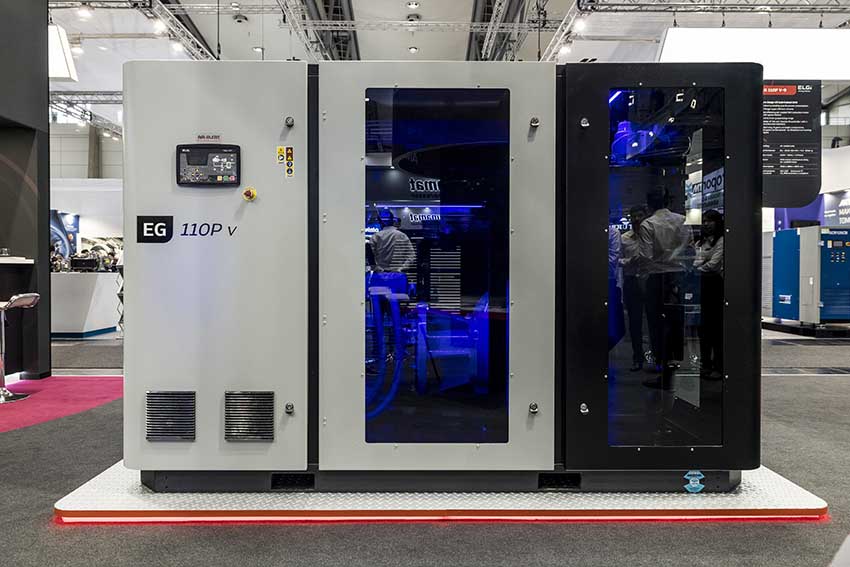
E.E: What products/solutions does your company bring that are the most innovative?
K.V.M: We recently introduced our innovative compressed air solutions at Hannover Messe 2023 in Germany, reiterating our commitment to providing our customers with products at low life cycle costs. Some of the products on display were – ELGi’s OF90-160 Range of two-stage dry screw and water-cooled oil-free air compressors are available in fixed and variable speed options with a nominal power of 90 to 160kW. Compliant with class zero ISO 8573-1 air purity standards, the range can also be equipped with an integrated and stand-alone Heat Recovery System (HRS), recovering up to 90% of the heat generated during the compression process, and has improved performance within the 4.5 – 10 bar -operating range. These units can also be installed outdoors with protection kits.
ELGi’s EG90-160P Range with a 4.5-12.5 bar operating range in the ELGi EG Series portfolio offers superior performance with a lower cost of ownership and increased reliability, translating to increased uptime and improved productivity in manufacturing applications. With significant energy efficiency improvements and an advanced two-stage aired design, this new oil-lubricated compressor range is available at fixed and variable speeds.
ELGi’s EG11-45 PMSM Range of new oil-lubricated, air-cooled compressor with a 4.5-12.5 bar operating range features a new Permanent Magnet Synchronous Motor (PMSM) with industry-leading, energy-efficient, direct drive air ends designed for variable load. With significant energy efficiency improvements, this game-changing PMSM permits the extension of improved turndowns without compromising efficiency when employed with Variable Frequency Drive (VFD) applications, reducing energy consumption, and increasing free air delivery.
E.E: What are the challenges that users encounter in their line of work?
K.V.M: Compressed air is vital in industrial and economic development, powering production equipment worldwide. However, compressed air inefficiencies reduce operational performance, which leads to significant financial losses. About 50% of the compressed air generated is estimated to be lost due to inappropriate uses, system losses, artificial demand, and air leakages. Aside, customers are also facing a steady rise in energy costs, regulatory and value chain demands for lower emissions, and the continued need to improve operational costs and, more importantly, energy efficiency.
E.E: How does innovation help them in these situations?
K.V.M: ELGi’s Air audit program could be one example. Air Audit, a comprehensive service by ELGi aimed at identifying inefficiencies in a compressed air system, enables industries to overcome several challenges. The ELGi Air Audit program helps our customers to optimize their compressed air systems, reduce energy costs, and improve operational efficiency.
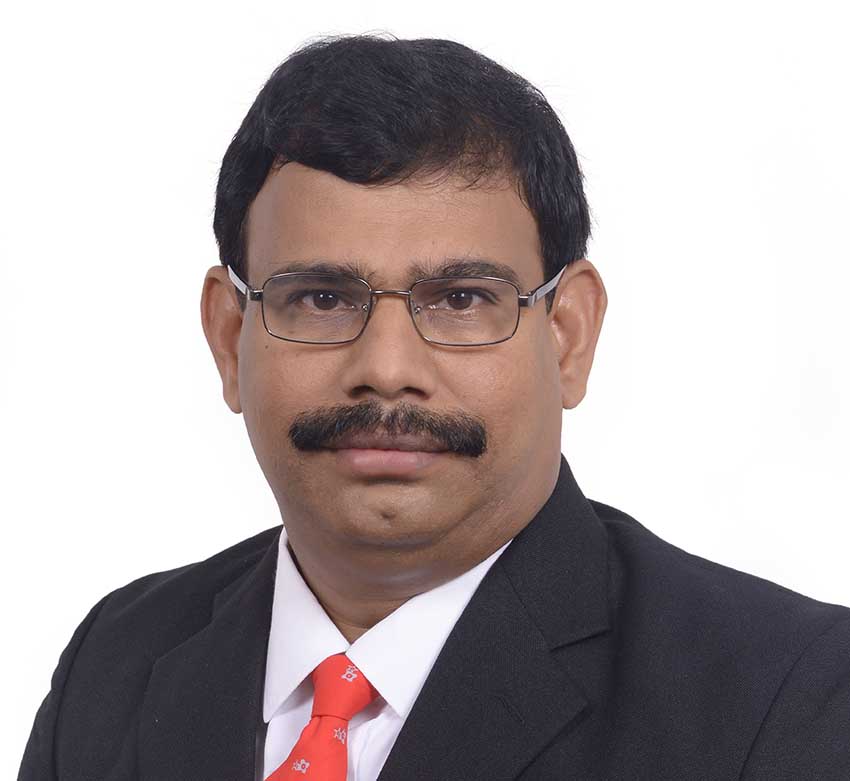
E.E: How is digitalization changing your field of activity?
K.V.M: To help our customers remotely monitor their air compressors 24 x 7 from anywhere in the world and improve energy efficiency and uptime, ELGi has introduced Air~Alert, an IoT-enabled monitoring and alert system compatible with ELGi’s range of air compressors. ELGi’s Air~Alert monitors a compressor’s critical parameters to minimize downtime and maximize efficiency. Predictive alerts are a step closer to prognostics for detecting and preventing failures. With Air~Alert, our customers are assured of highly accurate advanced predictive machine downtime alerts and minimized unplanned downtime.
E.E: What tasks/processes can users do easier and more efficiently with your products/solutions because of innovation?
K.V.M: Going back to Air Alert again as an example – energy cost accounts for about 75% or more of the life cycle cost of a compressor. Enabled by Air~Alert’s monitoring, smart analysis helps save up to 30% on energy costs. Compressor utilization data (load and unload operating hours) from Air~Alert provide valuable insights into determining if a Variable Frequency Drive (VFD) will help save energy costs based on demand on the compressor. The data will also help optimize operating pressure bands and resize an air compressor based on plant compressed air needs. Additionally, the compressor usage data from Air~Alert also enables insights into identifying leakage in the compressed air system and thereby helps save energy costs.
Air~Alert’s intelligent data analysis triggers predictive warnings of fault occurrence well in advance, saving precious time and the expense of unexpected downtime. Air~Alert can assist in forecasting most of the commonly occurring failures in advance, which helps to minimize downtime and unplanned repair expenses. With Air~Alert, manual logging of service or on-site checking of compressors for service due can be eliminated.
Air-Alert delivers essential trend graphs and information on key operating parameters such as discharge pressure, oil temperature, VFD speed, total running hours, trips, and alerts through a live online interface on a web portal, allowing remote access from anywhere in the globe. In one quick view, it also gives comprehensive information and impending servicing requirements for compressor health, usage, fault, and trip notifications. The system also sends a monthly summary report to the users on overall health and operating parameters, including upcoming planned service requirements.
E.E: Tell us some tips & tricks about prevention/maintenance for your products/solutions?
K.V.M: Delayed Maintenance: Timely maintenance of the compressor and replacement of consumables and maintenance kits as per the recommended maintenance schedule will go a long way in ensuring the compressor’s trouble-free operation and efficient performance. Delaying the maintenance of the compressor and not replacing the consumables like an air filter, oil filter, air/oil separator element, and the coolant/lubricant on time will increase pressure drop across these filters and, in turn, increase the energy consumption and reduce the capacity of the compressor.
Selection and sizing of compressor: It is very critical to select the right type and capacity of the compressor during the initial plant setup. For example, selecting a lubricated compressor and installing downstream filters to remove the oil particles instead of an oil-free compressor will result in energy loss due to pressure drop across the downstream filters, which can be avoided. Similarly, oversized (higher capacity) compressors will run in unloading conditions for longer durations and consume more energy.
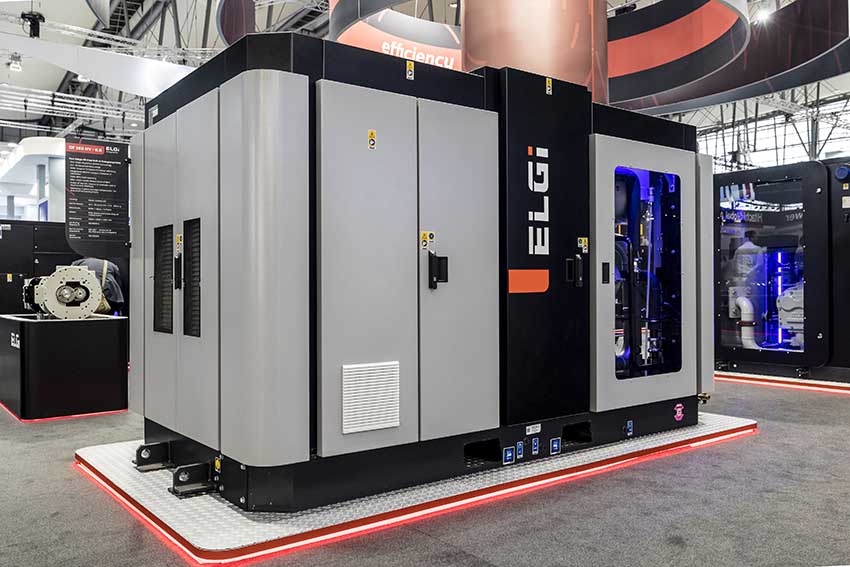
Selection of air accessories: The selection of the right accessories for the air compressor plant plays a vital role in reducing the energy consumption of the compressed air system. If not carefully selected, the size and type of downstream filters, dryers, and receivers will lead to excessive power consumption and hamper the production process.
Piping layout: The design has a long-time effect on the compressed air system. An inefficient piping layout design will lead to excessive pressure drop and increased leakage, resulting in the energy cost of the compressed air system shooting up over the period.
With increasing energy costs, the performance and efficiency of your compressed air systems have never been more important. ELGi’s Air audit may help users identify potential opportunities for energy savings in their compressed air system, thereby reducing the total operational cost. Our Audit Report includes identifying all the big, medium, and small opportunities for energy savings in the compressed air system and providing recommendations on short, medium, and long-term measures for energy conservation, along with financial estimates and analysis for their implementation. The audit involves a wide range of sophisticated, portable diagnostic and measuring instruments to generate refined data and facilitate complex analysis to give a more reliable basis for identifying energy-saving opportunities, evaluating performance, energy-saving measures, and economic viability. In addition, ELGi’s Air audit will benefit customers by reducing the wear and tear and maintenance costs during the lifetime of the entire compressed air system.