Blasting large-scale components is a painstaking process – and not entirely without its hazards. With specially designed blasting robots, such work can be carried out faster and safer, as well as more economically and with a higher quality.
In the field of surface technology, steel components must have a certain cleanliness and a defined surface profile before painting or coating, which is usually achieved by blast cleaning. Similarly, blasting is the predominant means of removing residues from castings prior to further mechanical processing. Manual blasting is a very tedious and harmful to health, as workers are exposed to high physical stress, noise and dust – particularly in the case of large components, such as cranes, rail vehicles and motor blocks of ships. Until now, automated blasting has mainly been performed with wheel and pressure blasting equipment. However, the scope of application of these blasting techniques is limited to simple components of a certain type, size and material.
While multi-axis industrial robots with a large operating scope would be significantly better suited, their use is not practical due to the abrasive environment posed by blasting. Abrasive blast particles and dust damage such equipment and impair both their functionality and service life. Although covers can provide better protection, they also restrict the operating scope of fixed industrial robots, so that components often must be repositioned in the course of the blasting process. On the other hand, robots specially developed for blasting meet all task requirements. Combined with a cabin, they can even be used as a manipulator for blast cleaning large single components or complex shape workpieces.
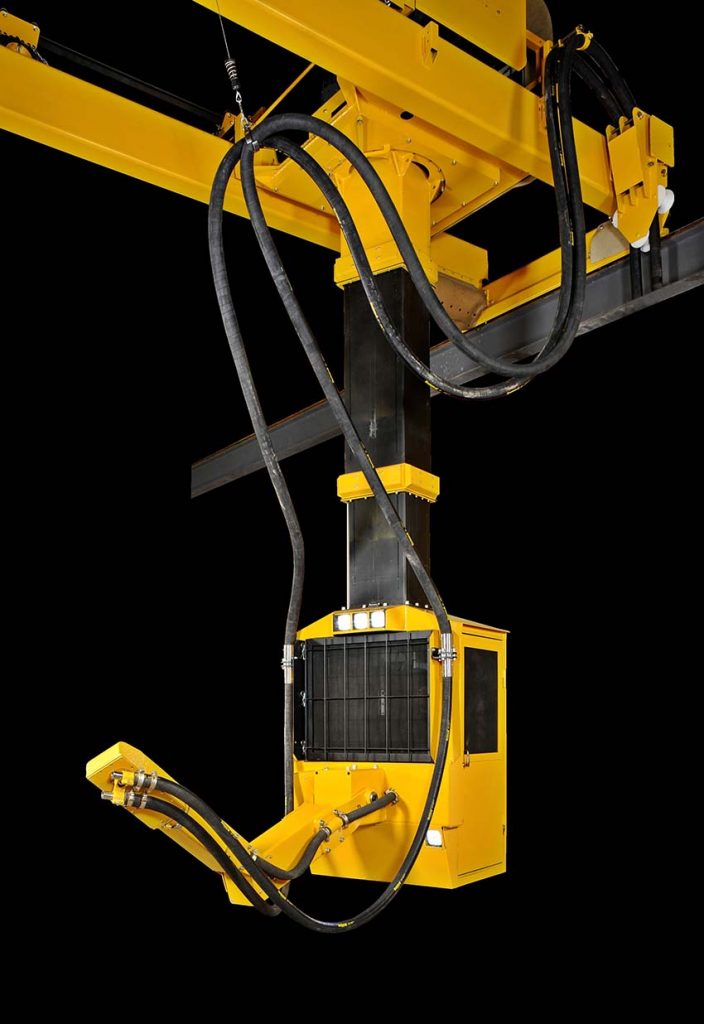
Advantages of Blast Robots
Above all, blasting robots are beneficial because they assure greater occupational safety. Operators work comfortably within a control cabin or control room, where they are protected from the hazardous environment of the blasting chamber. As with many of today’s machines and devices, the blasting robot is operated and controlled with joysticks. The control cabins and control rooms are well insulated, fully climate-controlled, and slightly pressurized to prevent the ingress of noise and dust.
Blasting robots can be gantry type or wall mounted. Gantry type robots move similarly to overhead cranes. This allows the robot arm to reach all around the work-piece exterior and even blast clean the interiors of workpieces. For example, in the rail industry the robot arm can blast clean the interior of passenger coaches through the windows or the interior of hopper cars by driving through the manholes on top of the hopper car.
Wall mounted robots can be used together with overhead transportation systems or turntables. With overhead conveyor systems, there are typically two wall mounted robots, one on each wall. This allows for the workpiece to be blasted efficiently from both sides. A single wall mounted robot can be used in tandem with a turntable. The turntable can also act as an axis for the robot, so that the robot controls the turning of the workpiece.
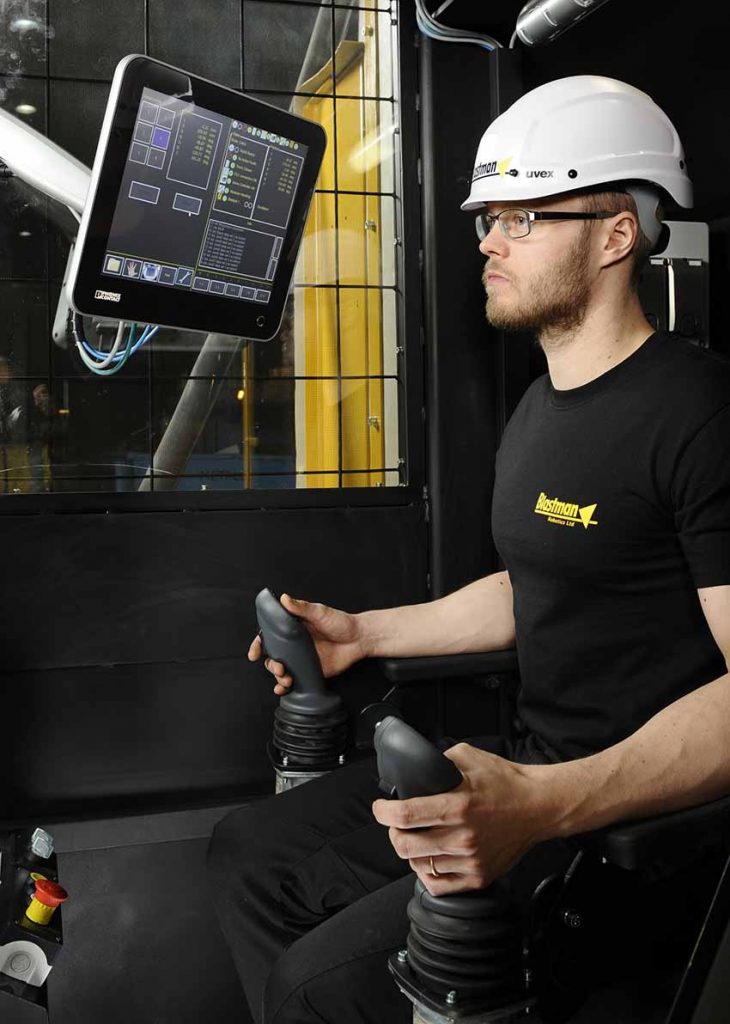
In the case of series production, the blasting robot does its work completely automatically. Automatic operation leads to constant and repeatable cleaning results. The blasting sequences are very easily programmed by means of a teach-in process, whereby the operator cleans the component once by manually operating the joysticks. While doing this, all the system’s movements and functions are recorded in sequence to create a blasting program that can then be used to clean more of the same component. If blast cleaning of the component once by manually operating the robot is not possible, programming can also be carried out with a portable handheld panel. In this case, the robot’s movements are recorded by means of a point-to-point process, which produces highly efficient and accurate blasting programs.
Offline programming is even more efficient, as it eliminates any need to interrupt production. Performed on a separate PC, offline programming consists of entering the component’s 3D data, as well as those of the blasting chamber, into a special simulation program. All the robot’s movements are then simulated on the computer, where the operator can simulate the blasting result and check for any possible collisions. At the same time, this technique enables cleaning processes to be optimized offline in terms of quality and duration, thereby significantly enhancing the cost-effectiveness of robotic blast cleaning.
High-performance blasting
Another major advantage of the blasting robots is that they are inexhaustible, even at high output rates. Due to the powerful recoil forces caused by the abrasive jet leaving the nozzle, the nozzle diameters for manual blasting at 6 to 7 bar cannot be more than 10 to 12 mm. Modern blasting robots, on the other hand, can handle nozzles up to 19 mm in diameter at blasting pressures of up to 10 bar, without any restrictions. This alone means that their blasting performance is many times greater than that of manual blasting – and can be increased by adding a second nozzle to the robot arm. With basic conditions, a blasting performance of over 200 m²/hour can be achieved, while an average worker is unable to manage even 15 m²/hour. For many companies, it is also becoming increasingly difficult to find personnel willing to perform such strenuous work under the given hazardous environmental conditions.
Fast and flexible cleaning
Compared to other blasting equipment and methods, blasting robots easily adapt to components of different shapes and sizes. Gantry-type robots, which feature up to 8 axes, can move around the entire blasting chamber and treat areas that wheel blasting units would be unable to reach, and which would therefore need to be subsequently blasted manually. The robots also perform other tasks, in addition to blast cleaning. These include the use of compressed air to remove abrasives and dust from a workpiece after blast cleaning. This allows the workpiece to be available sooner for further processing, while freeing up the blasting chamber more quickly for more components, thereby further shortening overall processing cycles.
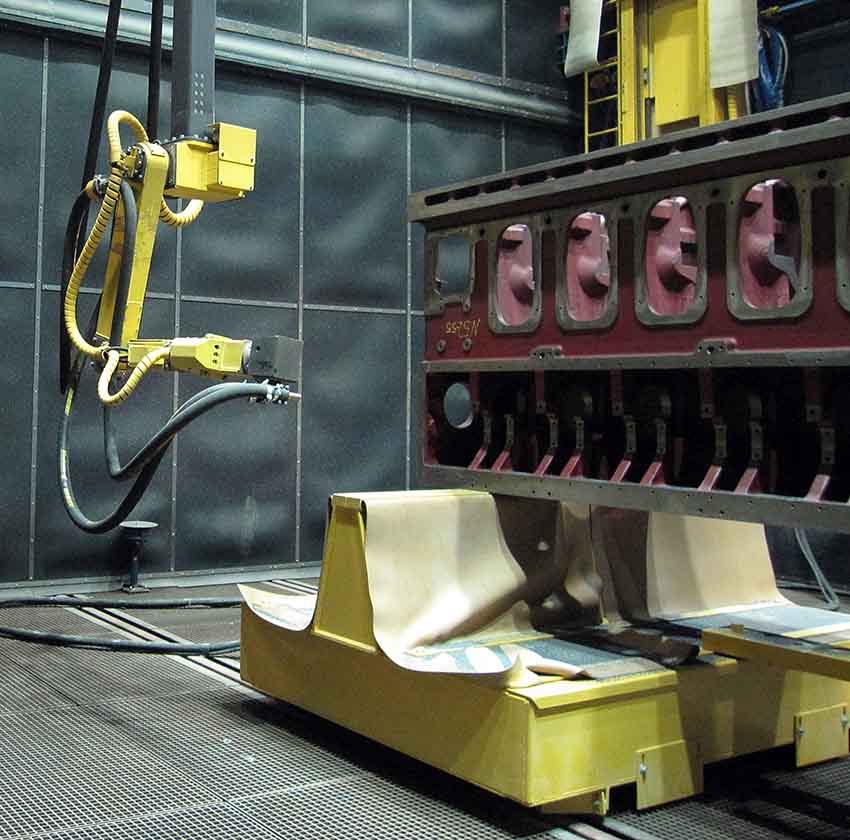
Since the early 1980s, Blastman Robotics has been applying innovative engineering ideas and the right choice of materials to the task of manufacturing highly durable robots specially designed for automated blast cleaning. In fact, the oldest systems supplied by Blastman Robotics that are still in operation are over 25 years old. Depending on the application, the abrasive can vary: Everything can be used, from large, sharp-edged steel grit to heavily dusty aluminium oxide and garnet sand.
Highly versatile
Blasting robots are the most efficient means of cleaning large components and surfaces. Their use is particularly cost-effective both in cases where manual blasting would be very time consuming and in those that involve components which would otherwise require additional follow-up blasting by hand. Examples of such applications include blast cleaning passenger coaches and freight cars, as these parts feature many large and difficult-to-reach surfaces. Blast cleaning of their interior surfaces can be performed and completed according to specifications by guiding the robot arm through the rail car’s openings. Since such cars are typically produced in series, the automated functionality of blasting robots provides added benefits to manufacturers. Blastman Robotics has already supplied more than 100 fully automated blast cleaning robots to the rail car industry alone.
Blasting robots are also the preferable means of removing agglomerated sand from casted components, such as rotor hubs for wind turbines and motor blocks for marine diesel engines. Such stubborn deposits are removed in a targeted manner with a mix of coarse steel grit and shot at abrasive impact velocities of up to 200 m/s. Other examples for the use of blasting robots include components from the commercial vehicle sector, such as agriculture, construction and earth-moving equipment (ACE). Also, individual parts or components with a small number from the construction industry or mechanical and plant engineering, such as bridge segments or turbine housings, are also processed today by blasting robots with a manipulator function. In addition, blasting robots with direct control cabins can be very flexibly operated in the processing of a diverse range of products. They are also ideally suited to dealing with the wide variety of surfaces that arise when maintaining and repairing used components.
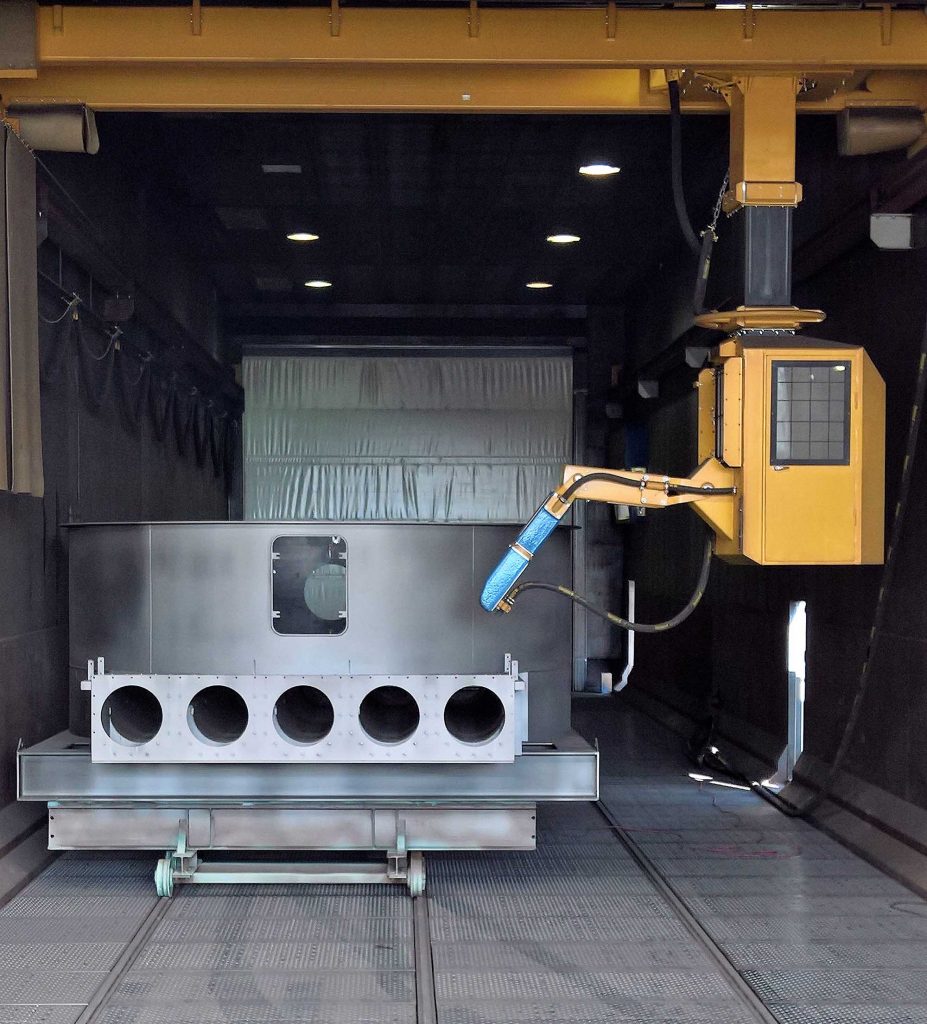
Blastman Robotics has a broadly based portfolio of blast cleaning robots to suit individual applications. Depending on the number, shape and size of the components to be cleaned, they range from a simple four-axis stand-alone blasting robot to an assimilated eight-axis gantry-type model – which can reach every corner of the blast chamber. Each Blastman Robot is manufactured to meet the requirements of the customer. The base model and operating principle of different robot models stays the same, but for example the gantry can range from 4 to 30 metres. The size of the axes depends on the size of the workpiece and Blastman always takes the customer’s needs to consideration to provide an optimal robotic blast cleaning solution.