Extreme flexibility and customization, innovative design, continuous self-learning thanks to the adoption of Artificial Intelligence: with the new centreless grinder Monza KZN, Monzesi shows the ambition to present a machine without precedents on the market.
Monzesi unveiled last July the new Monza KZN centerless grinder, that crowns research and development work that has lasted more than a year and carried out jointly by engineers of the company with universities and research centres. The new model inaugurates a new chapter for Monzesi, offering a completely new product compared to the previous lines but also to the machines present on the market, transforming the very concept of centerless grinding and literally allowing you to build and customize the machine around the workpiece.
“Our goal was to make a machine that was not only perfectly flexible and automated in its every movement, but also equipped with an exasperated intelligence given by Artificial Intelligence and self-learning”, announces Riccardo Pessina, GM of Monzesi. “The new Monza KZN lives its own life, learning process after process to improve its performance continuously”. A new concept of grinding also born from the collaboration with the Italian National Research Council on a path that has already led to the filing of two patents, the first of a series of innovations which will be patented as the machine thanks to AI will increase its capabilities to the users.
Perfect flexibility.
The project behind the new Monza KZN was born from the will of Monzesi to discover what was missing in the world of centerless grinding, to create a machine that wasn’t just a basic upgrade of pre-existing lines but something completely new.
“The design of a centerless grinder typically tends to offer the optimum performance for a certain type of need, whether it’s throughfeed or infeed, having maximum repeatability or high rigidity, or strong material removal in a given time unit. This, naturally, sacrificing performance on other fronts.”, tells Davide Falletto, Monzesis Sales and Marketing Manager. “Our goal was to achieve building a machine that would combine the best performance for each type of processing.”
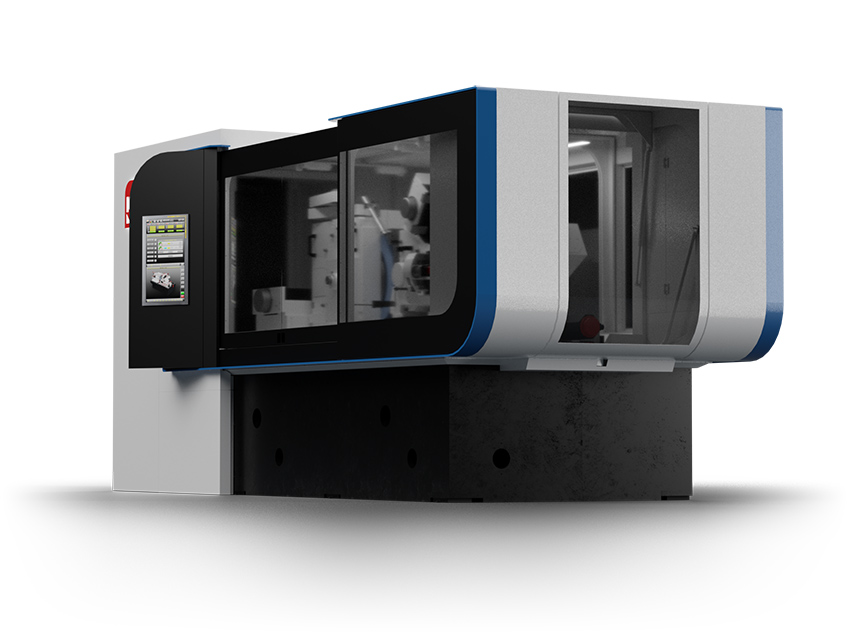
That’s why Monzesi has worked in several directions. At first, collecting feedback from customers who work with their machines every day, to understand their desires not only regarding Monzesi products but centerless grinding in general. A benchmark was created for what the market offers concerning centerless grinding, precisely to identify what was still missing. “We have thus decided to reinforce all those aspects that we already knew in our machines”, continues Davide Falletto, “everything has been improved using the best components on the market that offer the highest possible accuracy. The machine we were able to design and produce allows you to build a custom solution around the workpiece, offering in the same machine the maximum performance for each application of the customer, whether you’re talking about infeed or throughfeed, to ensure maximum repeatability, stock removal rates and rigidity. Every movement and every adjustment is automatically checked by the CN, avoiding any intervention by the operator.” The new Monza KZN is therefore designed to satisfy the process requirements in every kind of industry thanks to its flexibility pushed to the max, with a particular indication for high levels of accuracy and tolerances, cycle time reduction and large volumes for the automotive and bearing industry.
Versatile technological soul
To assure the maximum of stability and rigidity, for the new Monza KZN a new monobloc machine basement has been designed in polymeric cement, which offers a very high capability to absorb vibrations. “The slide carriages have been equipped with very large and robust prismatic guides, with the largest section available on the market to ensure high load capacity”, explains Dario Targa, responsible of Monzesis Technical Office. “According to the process requirements it is therefore possible to include different technologies, like roller guides for the ideal positioning of the carriages in the infeed-processing or other types of sliding for throughfeed.”
A new system to control the progress of the carriages supports the traditional encoder on the motor with a linear transducer, which provides absolute accuracy with a direct feedback regarding the carriage movements, allowing micrometric corrections and bypassing all of the motor-drive kinematics. “The grinding wheel head has been designed to be much larger and with two different types of supports,”, continues Targa, “hydrodynamic bushings to have more resistance and angular-contact bearings which ensure a better rigidity avoiding axial oscillations of the spindle. Forced lubrication applied also to the regulating wheel head allows to avoid temperature changes that can lead to deformations and elongation of machine components.”
The support of the regulating wheel head was equipped with hydraulic locks and with an axis motor allowing automatic adjustments resulting in a perfect cylindricity on the workpiece. The same has been applied to adjust the inclination of the head in throughfeed processing.
The dressing slides were enlarged and strengthened ensuring a better shaping accuracy for the grinding wheel. The grinding wheel slide has the ability to handle dual dressing technology – with electrospindles to perform geometric details, with the classic fixed diamond, or both. In the regulating wheel the dresser has been applied directly on the head, allowing the dressing to be repeated without the need for any further modifications regarding the position.
The new generation needle sprayer finally allows to orient the water with very high precision at the point of contact and it can be equipped with an axial motor suitable for tracking the wear of the grinding wheel and ensure continuous and precise cooling. The development of the new Monza KZN has therefore led to the filing of a patent for a blade with automatic height adjustment and a pressurized cleaning system. A second patent is being filed in collaboration with the Italian National Research Council, at exclusive use of Monzesi.
Continuous Self-Learning
Of course the evolution of the new Monza KZN also concerns the software, designed by technicians and coordinated by Cristiano Tagliabue (Electronic Manager), with a large 21.5″ vertical panel, offering to the operator all the necessary buttons on every page to get the whole process under control.
Great attention was paid to the design, resulting in an ideal combination of aesthetics and functionality thanks to numerous openings and doors designed to easily give access to all parts of the machine. This also useful for the predictive maintenance and use of the augmented reality and thanks to that Monzesi will be able to guide the customer remotely during maintenance work, with big savings in travel and hourly costs.
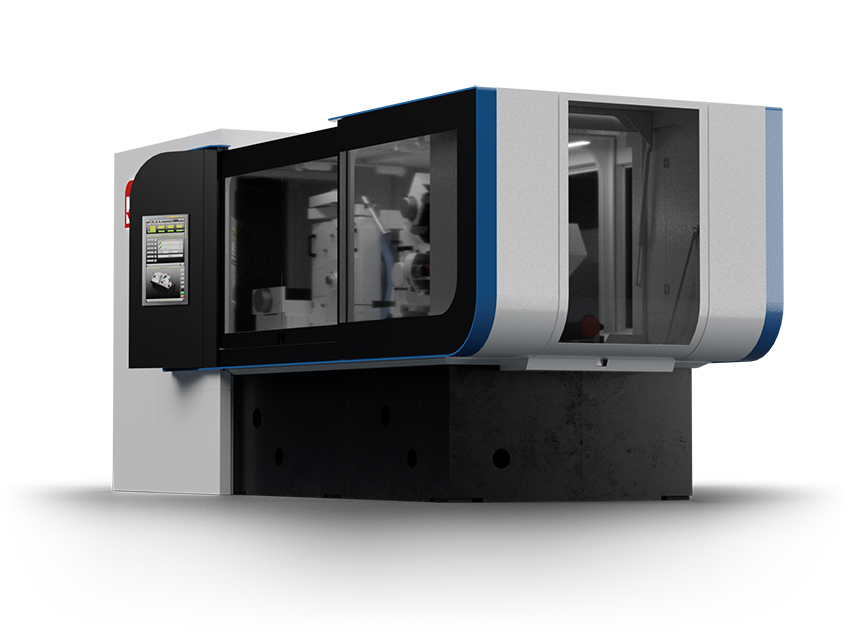
The machine can be equipped with an NC of Fanuc or Siemens and is is clearly in full 4.0 optics thanks to a series of sensors placed in strategic points, which provide all parameters related to performance, consumption, production and service status of the machine.
The information is stored in the NC of the machine or sent to the cloud. The availability of the data has two main functions: monitor all machine parts in operation for preventive maintenance and feeding the AI of the machine for continuous self-learning.
“The machine is supplied with an archive that merges all of our centenary experience,”, remarks Hossein Safarzadeh, R&D Manager of Monzesi, “but then moves on in self-learning mode, which means that with the progress and change of the processes made by the customer the grinding machine memorizes and learns to automatically improve the piece processing. The solution has room for continuous improvement in an Artificial Intelligence area. With the Italian National Research Council, we are developing an algorithm that processes the transmitted data and may check independently whether the processing parameters for that piece are correct or if they need to be improved.” Just as a craftsman does, who – thanks to his experience and the continuous work – increases his own mastery every day. But all done by a fully automatic centerless grinding machine, which thanks to the AI increases its skills day by day, bringing benefits to customers and at the same time enriching the know-how of Monzesi, in order to continue to develop new solutions and help the machine on its way of endless refinement.