GRUNWALD is a family-owned mechanical engineering company and one of the world’s leading suppliers of format flexible cup and bucket filling machines. Since the company’s foundation in 1956, more than 3,000 filling, dosing and packaging machines were supplied to the food and dairy industry, as well as various sectors of the food industry worldwide. The share in exports amounts to 90 %. Grunwald employs more than 200 people at their location in the South of Germany.
Interview with Vedran Jakopaš, Area Sales Manager at GRUNWALD.
Easy Engineering: What are the main areas of activity of the company?
Vedran Jakopaš: The main area of activity of our company is the production of cup- and bucket filling machines with intelligent solutions, mainly for the food industry sector When speaking about food industry, we first of all deliver to the dairy industry, but quite closely followed by all other industries, like delicatess products (sauces, ketchup, mayo, mayo-based salads) and convenience food products. Beside already mentioned products, we build machines for filling of: butter, margarine, sauces, soups, ready meals and meat products (like pate and pet food), jam and honey, and all other generally pumpable products. We also do some special application for filling of bulky products, like cereals, nuts, dried fruit jelly products and sweets. One product we also have big experience with is hummus, which has a very uprising trend worldwide, gaining popularity practically daily.
E.E: What’s the news about new products/services?
V.J: We have a broad spectrum of machine sizes to choose for our customers, based on the speed and additional equipment. This basically means we have some standard features which are common for the majority of the machines we supply, which can be upgraded by a number of different application-oriented additional features.
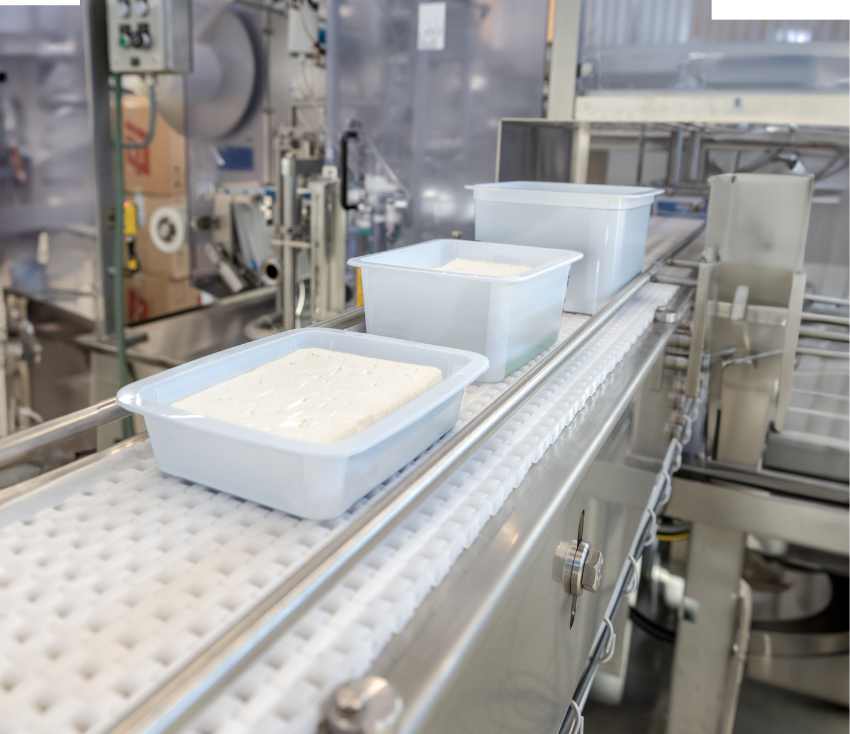
We are happy to have a very strong engineering team, doing their best in resolving these every-day tasks with their ideas and ultimately providing our customers with the right solutions. Flexibility of our machines and ease of use have always been our top priorities in provision of solutions, but also every possible reduction of non-productive times (time for cleaning, time for making the format/product changeover, etc.).
E.E: What are the ranges of products/services?
V.J: We focus ourselves on filling and packaging systems for filing different products into cups and/or buckets. We provide a big range of machinery, from small 1 or 2-lane rotary type machines with basic necessary functions to big rotary machines with a lot of additional equipment as well as high-capacity linear machines with additional features like integrated secondary packaging systems. Of course, the same applies to our bucket fillers.
In addition, it is equally important to provide our customers with service and spare parts supply. Our sales and after-sales activities are global, with our own teams and a worldwide network of agencies and partners. We offer various options to our customers, including individual service and maintenance visits and customizable service contracts. We take pride in our flexibility and believe our customers appreciate it.
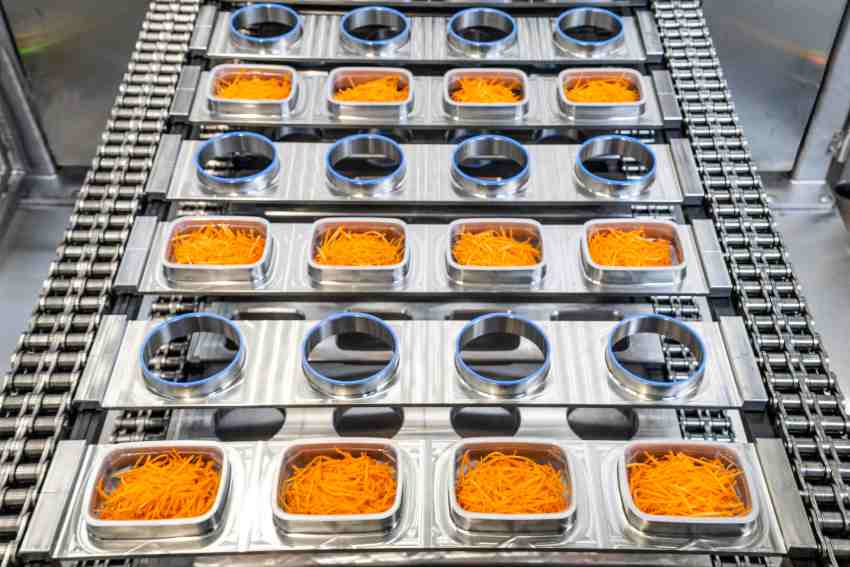
E.E: What is the state of the market where you are currently active?
V.J: I’m personally responsible for the South-East European market. This area was not very well-known for high level automation in the past, but in the recent past this trend has slowly reached these areas as well. We see this by increasing numbers of inquiries and general interest coming from the area, especially for the high-level automation and high hygiene level machines. In other words, machines are requested, filling and packaging systems, in which we demonstrate our strength and expertise since many years.
E.E: What can you tell us about market trends?
V.J: The packaging industry trends are now focused on sustainable and environmentally friendly materials, including mono-materials and paper. As a packaging machine builder, we face challenges in material handling and sealing properties. Previously, multilayered materials enhanced single material properties but were difficult to recycle. Now, with monomaterials, we must adapt our technology to ensure safe packaging. Our development center enables us to test materials, develop solutions, and simulate filling processes, allowing us to innovate and shape future packaging trends while reducing environmental impact.
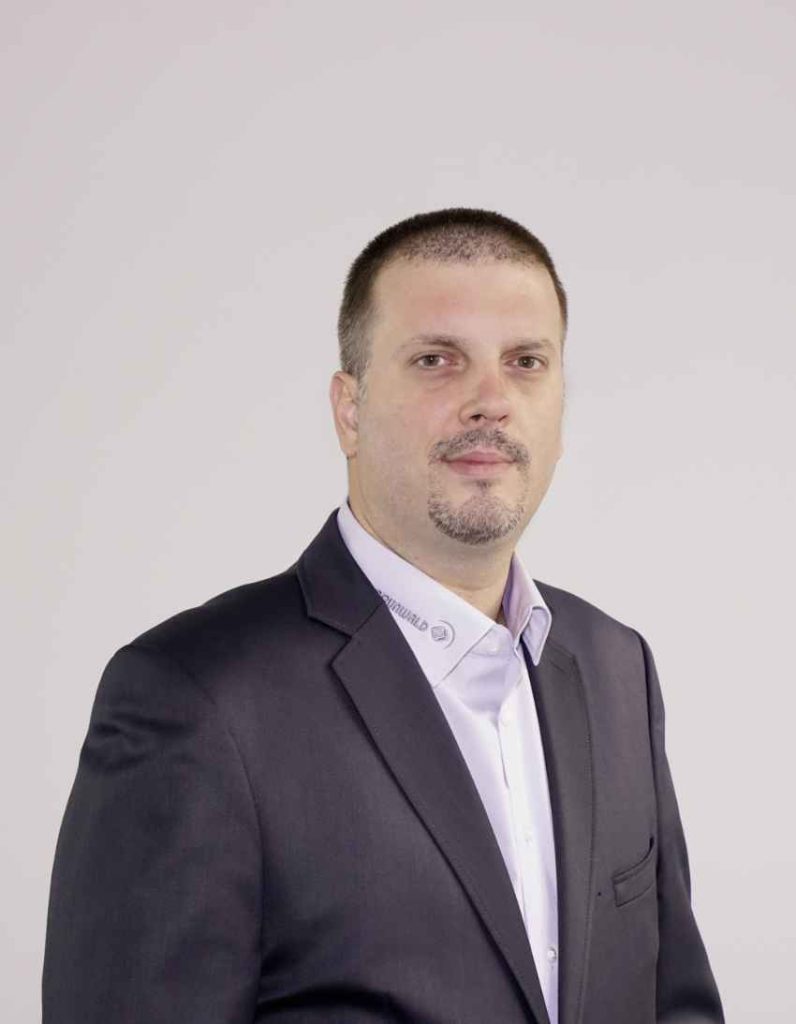
E.E: What are the most innovative products/services marketed?
V.J: Our development of ULTRA-CLEAN filling machines, both rotary and inline machine models, with pulsed UV systems for sterilization of packaging materials (cups and lids) which comply with min. log4 sterilization criteria according to strict VDMA standard of hygiene levels classification, and all other high-level hygiene features, like CIP/SIP cleaning. Beside this 2-phase UV system is the most important development. Another very important feature of our ULTRA-CLEAN machines is the integration of a fully automatic clean air tunnel with fully automatic cleaning system, which raises the already high UC hygiene standard to a higher level. These are two hygiene standards of our inline machines for several years and they are also available on a rotary-type machine ROTARY 20.000UC and represent a completely new and revolutionary ULTRA-CLEAN machine concept, setting a new benchmark.
As a result, the machines are now standard in the dairy industry, as confirmed by our numerous customers, using them on a daily basis.
Another milestone is our development for the delicatessen industry, but which is also mandatory when we speak about product protection against oxidation. Our new gas injection system offers clear advantages when compared to traditional evacuation/gas injection systems (MAP). We have found the solution to remove the negative effect of traditional MAP system, which is significant loss of production speed due to necessary cycle time for evacuation and subsequent gas injection. Due to the newly developed gas injection system, it is now possible to run production at full cycle speed of 40 cycles/min. and achieve residual oxygen content of less than 0.5 % in the cup headspace. New trend products with less or no preservatives can only be packed safely with a minimum percentage of remaining oxygen in the cup. This technology is now increasingly used also in the dairy industry for some products. As for this technology we do not need a vacuum pump anymore, this also has a very positive influence on power consumption, increased production and machine efficiency, all of which now have a big impact on decision making.
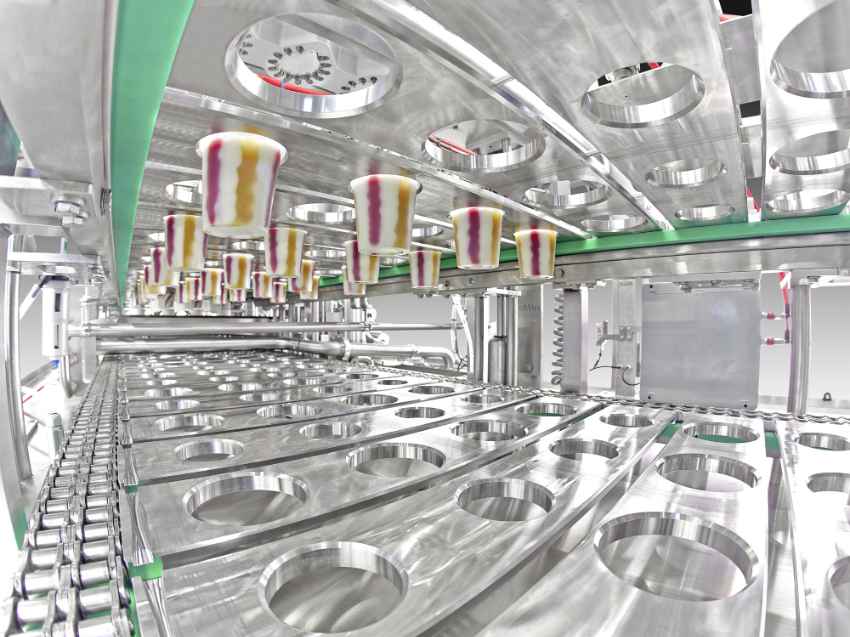
E.E: What estimations do you have for the beginning of 2024?
V.J: After a successful 2023, we are seeing a translation of the order into 2024. The demand for new technologies continues to grow, as evidenced by the overwhelming response at recent exhibitions in Australia, France, and Germany. We received numerous new projects, ideas, and inquiries from both existing and new customers, which is a clear indication of the trust they have in the quality and performance of our filling and packaging systems. With these fantastic results, we are excited for an even more successful year in 2024, which will enable us to further grow and improve.