For pharmaceutical or medical, food or cosmetic products, droppers are indispensable for dispensing small amounts of liquid. In addition to absolute ease of use, it is reliability and precision that are, above all else, crucial for allowing liquids to be dosed according to requirements.
Droppers, such as for medication administered in liquid form, are a classic among dosing systems. Their role is clearly defined, their use is designed for maximum simplicity. The market is commensurately transparent, distinguishing itself through its high stability, manageable number of manufacturers, and rather limited possibilities in terms of future product optimizations. The manufacturing material polyethylene continues to dominate. The manufacturing parameters among the different droppers are defined by the specific dosing requirements and by the European Pharmacopoeia (Ph. Eur.).
Every serious manufacturing company worldwide adheres to the highest quality standards during every step of the process, such as those prescribed by the international quality specifications ISO 9001, ISO 13485, and ISO 15378. Competitive advantages are limited to the reliable use of the dropper and the productivity of the plant solutions. Cavities of up to forty pieces in one cycle in addition to a significant reduction in cycle times results in a higher level of productivity and a higher availability of production systems.
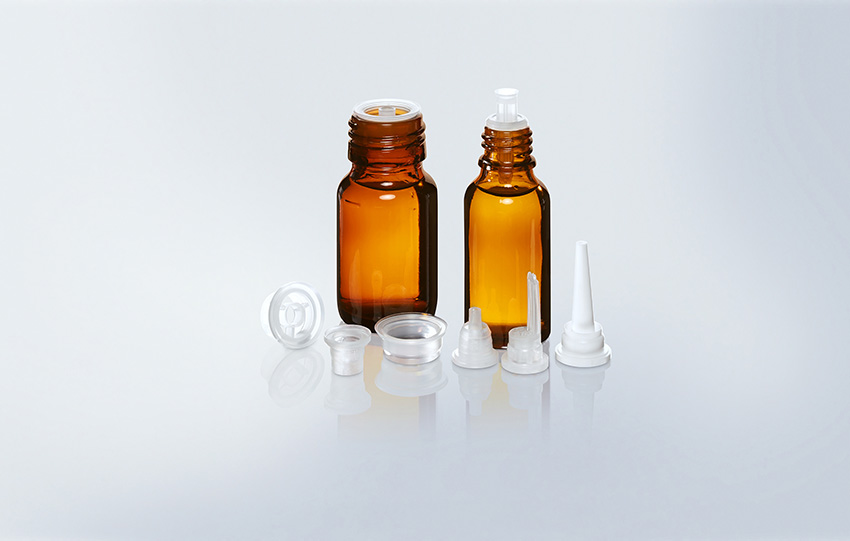
Precise adherence to dosing quantities
Customers from the pharmaceutical and medical industries as well as from the food and cosmetic sectors expect a product, in this case the different dropper dosing systems, to be reliably made but, even more so, to be reliable and precise in their dosing. The applicable requirements for the pharmaceutical and medical industries are set out in the Ph. Eur. Customers from these industries depend to the utmost on adherence to these prescribed product standards by their suppliers. The precision to which the required dosing quantities can be adhered to, while also offering the greatest possible operational simplicity of the dosing system by the end customer, continues to play the decisive role.
Compliance with these dosing requirements is so important that it determines the specifications of the corresponding manufactured products. Consequently, droppers differ in terms of how they are used and whether they must possess high, medium, or low dosing precision. The application requirements themselves therefore determine which product model is ultimately used.
Adherence to the value corridor
The high precision, particularly required for the dosing of medically effective drops, is defined by its deviation from the dosing requirement. The permissible tolerance is stipulated by the European Pharmacopoeia (Ph. Eur.) to be plus/minus 15 percent.
Adherence to this value corridor is determined by a series of tests of ten single doses, of which each resulting mean value may not deviate more than ten percent above or below. Moreover, there is also the additional requirement of an equally reliable and consistent drop speed. In order to ensure users, the necessary countability, this is set at a maximum of two drops a second.

The challenges that these requirements create are easily recognizable. Not all liquids are the same – drop geometry accordingly varies in its dimensions. Correspondingly high is the number of variants that can be made available to the customer when selecting a suitable dosing system for them. A central influencing variable here is the respective viscosity of the liquid, which can be more watery or oily in its consistency; there is also the potential for alcohol content or suspended matter that can influence the drop behavior and/or size. An additional determining factor is the surface tension of the dosed liquid.
Varying applications for vertical and horizontal droppers
When high dosing precision is required, vertical droppers are generally used. Accordingly, these are positioned at a ninety-degree angle to the dosing medium. The vertical orientation of the bottle during application allows the drop size and speed to be optimally defined in advance. Vertical droppers are also generally used to ensure medium dosing precision. Instead of having the upward protruding drip tube (as seen on the precise dosing version), they have a drip tube that ends almost flush to the sealing plate.
For more relaxed demands on dosing precision, the cheaper to manufacture horizontal dropper is usually used. Horizontal droppers are simply considered „dosing aids“ in their areas of application. These can be used in all cases in which the effects of possible incorrect dosing remain relatively low, such as for cough mixtures, nutritional supplement drops, essential oils, and cosmetics. Because the angle of the bottle is always different when administering the drops (the prescribed spectrum is between 40 and 60 degrees), this inherently results in larger discrepancies – in the individual drop volumes alone – that prevent high dosing precision.
Selecting by drop ascertainment
Regardless of whether a vertical or horizontal dropper is used, here at Heinlein Plastik-Technik, the manufacturer of dosing systems, each „new” (i.e., previously untested by us) liquid undergoes a so-called „drop ascertainment “. This drop ascertainment can be performed on an original product or based on a customer’s dosing and packaging requirement. This „collection “of dosing systems primarily differs in terms of three aspects/functional dimensions:
- Drop tube diameter
- Drip channel diameter
- Air hole diameter
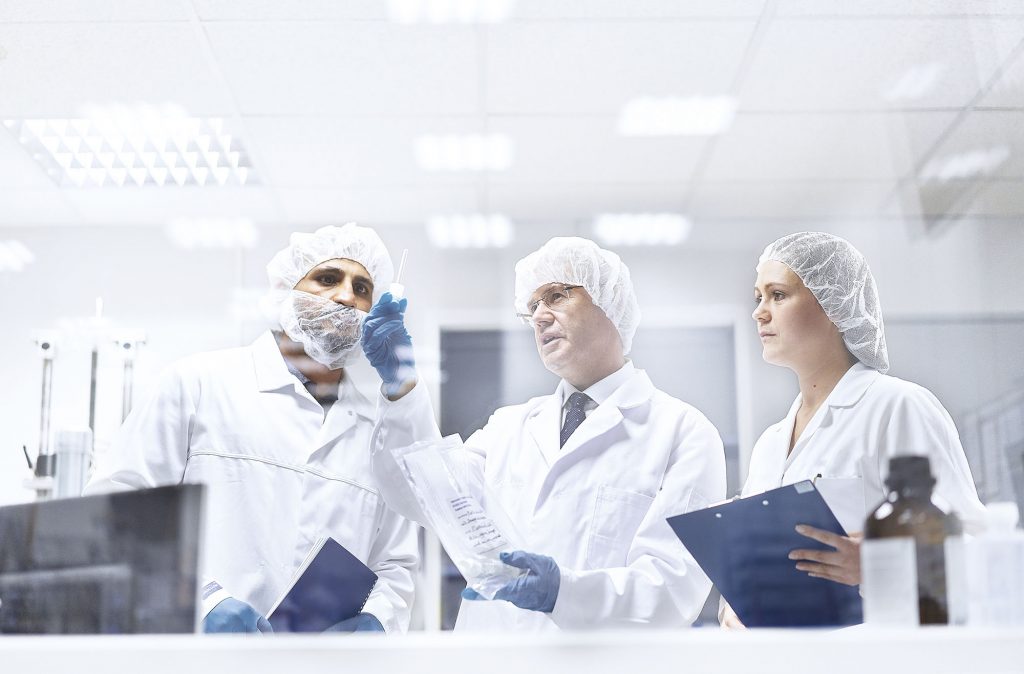
There are also other dosing system versions that – beyond the inclusion of these functional dimensions – can be used for customer-specific requests or specific liquids and applications.
GL 18 openings ensure compatibility
The common denominator among all dropper models is the bottle thread defined in accordance with DIN standard 168 with the GL 18 thread. This is mainly used for the closures on glass bottles or containers. The diameter of the outside thread is between 15.48 mm (minimum core diameter) and 18 mm (maximum outside diameter) and between 18.40 mm (maximum outside diameter) and 16.08 mm (minimum core diameter) for the inside thread. This ensures that the requirements of GL 18 openings are met and that the bottle is sealed tight when closed to protect the contents. The exclusive use of GL 18 openings for Heinlein Plastik-Technik systems also offers the advantage of guaranteeing absolute compatibility among bottles and closure systems for customers. This is true for both the various screw and tamper-evident closures as it is for child-proof closures.
Alongside such combined variants, integrated dropper closure systems also play an increasingly larger role in the market. The demand for integrated dropper closure systems over the past few years has consistently grown.
Heinlein Plastik-Technik GmbH is specialized manufacturer of high-quality primary plastic packaging closures and dosing systems for the pharmaceutical industry. The company, headquartered in Ansbach, Germany, employs 170 people and serves customers in over 60 countries. An innovator in its field, Heinlein works closely with its customers to develop the next generation of pharma packaging, using its strong research and development (R&D) compatibilities in combination with 60 cutting-edge injection moulding and assembly machines. With the fourth generation of the Heinlein family now running the business, the company has developed a strong focus on sustainability. Heinlein supplies customers on all continents with approximately 1 billion plastic components annually.