Falcor Group operates throughout Italy in the field of ecology and specializes in solutions for the compaction of waste. Through its five dedicated divisions, it supports companies by providing targeted solutions for the management of work and packaging waste (such as paper, cardboard, plastic, aluminum and others), optimizing the logistics process and safeguarding the environment. The different Falcor services, which operate through dedicated teams, are the guarantee of a 360° operating cycle that starts from consulting and design, up to after-sales service and waste intermediation.
Interview with Marcella Piccini, Marketing Manager at Falcor Group.
Easy Engineering: What are the ranges of products and what types of services do you offer?
Marcella Piccini: Falcor Group offers solutions for waste compaction. Thanks to the partnership with leading manufacturers in the sector, we can offer a complete range of balers and compactors to compact a wide variety of materials (cardboard, plastic, fabric, aluminum, wood, polystyrene, wet waste, glass …).

We have a division dedicated to the design of customized systems. Our projects arise from careful listening to the customer and from an in-depth analysis of the space and environment. Thanks to close cooperation with the customer, we can develop an efficient solution. We select the most suitable compactor and around it we develop the plant project, customizing it with elements such as loading hoppers, conveyor belts, chutes that best meet the customer’s needs. For these elements we make use of partner companies that make them according to our indications.
Once the project has been approved, we follow all the construction phases starting from the delivery of each of its parts, to assembly on site, up to commissioning and testing its operation.
We also have a service and maintenance division, which follows the customer in after-sales. Our commitment is to always resolve any operating problems of our machines in the shortest possible time. Thanks to an operational assistance network throughout Italy, we guarantee our customers prompt intervention, to restore normal press operation without further inconvenience to the user.

E.E: Which are the most innovative products / services and what special features do they have?
M.P: We are convinced that technological innovation is very important in the field of waste compaction also. Our balers, if equipped with modem and data SIM card, are implemented with an Intelligent System called BRA-IN, developed by our partner Bramidan, which allows you to remotely monitor the balers, receive notifications from the machines, order the collection of bales and access historical data of the machine. Furthermore, the Remote Service Tool system allows Bramidan authorized technicians to monitor and modify a large number of press functions, remotely adjusting hydraulic, mechanical and electronic components to ensure optimal operation.
E.E: How important are these features for the users in their work?
M.P: Thanks to the BRA-IN system, the user can remotely control the machines and have a complete overview knowing in real time where they are located, how they work, the filling percentage, the number of bales produced. The user can download excel reports and automate calls to binders.
The data relating to the machines are immediately and always available with a considerable time saving.

E.E: How do your products / solutions impact cost effectiveness for the users?
M.P: Waste management has very high costs. These costs are given by the number of collections that are requested from the collection companies, by the rental of skip bins in which to throw the waste, by the hours of work employed by employees to move or treat the waste.
Our approach is to understand how waste management takes place in the company and find the best solution. The solution, in addition to reducing the request for waste collection thanks to the fact that volumes are significantly reduced with compaction, must optimize the time dedicated by operators to waste management operations. In this way the company will be able to significantly reduce costs.
E.E: What kind of work do users who use these products / services do?
M.P: The use of compactors can be extended to many sectors of use. For this reason, the people who can work with the presses have different roles. They can be the end-of-line workers in a factory, the warehouse workers or the clerks of a private shop or the large-scale retail trade. However, our machines are safe and very easy to use.
E.E: How do your products increase profitability for users?
M.P: In addition to cost savings, recyclable waste has intrinsic value.
Cardboard, plastic, fabric, polystyrene can be resold for recycling. In the case of polystyrene, Falcor Group has the possibility to collect and purchase the compacted EPS blocks at the best price on the market at that time.
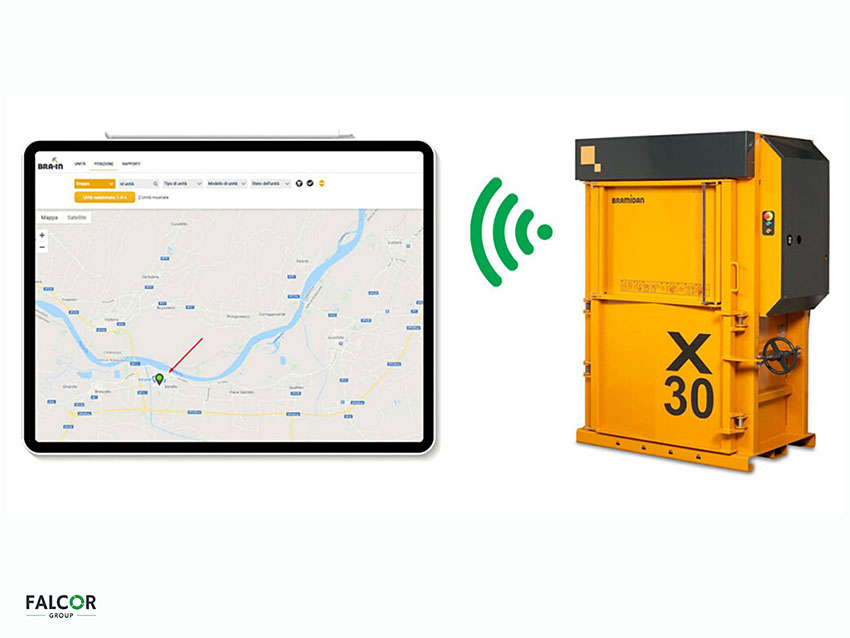
E.E: How do your products help solve users’ problems?
M.P: One of the first problems complained by customers is the amount of space occupied by waste and the speed with which the skip bins are filled: our presses reduce the material into compact bales and solve the problems of spaceoccupied by waste and the order of the environments.
Then there are more specific problems. Among the numerous examples I could do there are the time lost by the operators to break the cardboard boxes, which are instead inserted whole inside the presses and no longer need to be handled manually; or the time that the operator dedicates to the collection of the material at the point of waste inside the company, and then flows it outside into a bin: a problem that can be solved by installing a press directly at the source of the waste.
One of the most important goals for companies today is to reduce the carbon footprint. The use of compactors makes less truck trips necessary to transport waste and translates into a reduction in CO2 emissions into the atmosphere.