SAMYLABS is a Basque company founded at the end of 2016 in the BIC Ezkerraldea business development center in Barakaldo, Bizkaia, with the aim of developing 3D printers in metal laser technology. It is the first Spanish company to design, manufacture and market printers of this technology.
Easy Engineering: Which are your best-selling products / solutions?
SAMYLABS: Our flagship product is the SAMYLABS ALBA300 metal 3d printer, a compact machine that can print high-quality metal parts, and is designed to operate both in the workshop and in the office or laboratory, simple to use, easy to clean and that meets with the most stringent security requirements.
E.E: Why do users choose your products / solutions?
SAMYLABS: Our machine is probably one of the best, if not the best price-quality ratio of the market. With a significantly lower cost than other manufacturers, we deliver a professional machine, with very good finishes and excellent print quality. Our solution does not require additional payments, such as annual fees. On the other hand, at a technological level, we do not depend on any third party. We have developed everything, from lamination software to mechanical design, including electronics and process technology. This gives us great autonomy and flexibility, as well as being the reason why we can offer such a competitive price. Finally, our machine is completely open, something very interesting for those companies and center that want to test with technology and go further.
E.E: What special features do your products / solutions have?
SAMYLABS: Our SAMYLABS ALBA 300 machine offers excellent print quality. High-density end pieces prepared for any type of effort or subsequent treatment are obtained. The machine allows you to print parts in a wide variety of alloys, such as A316L, C300, Inconel, Cobalt Chrome, Aluminum or Titanium. Has a powerful 300W laser unit, as well as a high-quality optical path. It is a tremendously compact machine that includes inside the refrigeration system and everything necessary to print. It reaches an excellent level of inertization and has a powerful filtering and recirculation unit. Its software, integrated into the machine itself, allows the operator to work directly on the machine without the need for a desktop computer. The machine also supports the option to work from a technical office, networked or upload files through the USB port. Also allows to change the process parameters and paths in real time, while the machine is printing.
Generates detailed process logs, for later analysis and makes work easier working with a significant reduction in the size of machine files.
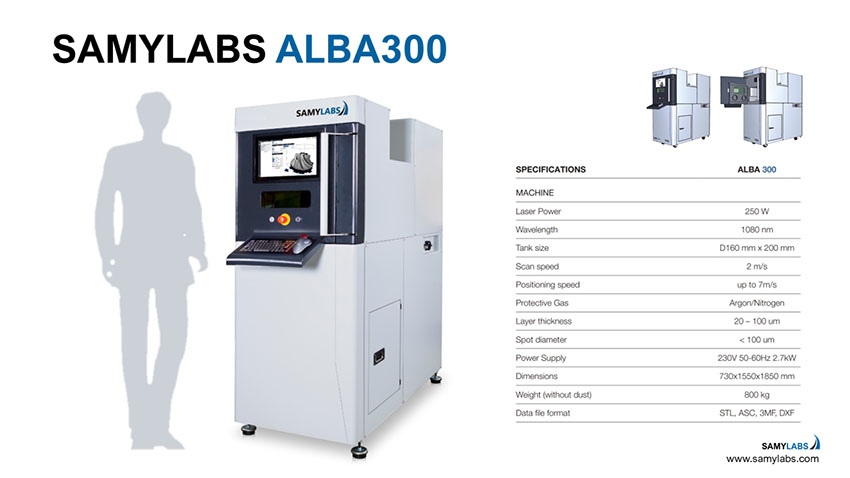
E.E: Tell us a short tutorial of how a task is done more efficiently with one of your products / solutions.
SAMYLABS: Our software presents the operator with a friendly interface where he will be able to print a part following 5 easy steps.
- Load the parts you want to print and compose the print scene
- Calculate the best print orientation
- Calculate the necessary supports to carry out the printing success
- Simulate and quote the work

E.E: How did your products / solutions improve efficiency for the users overall?
SAMYLABS: Additive manufacturing is a niche technology, which is more competitive than traditional technology only in certain applications. By this I mean that for most conventional processes, traditional subtractive technology will continue to be used.
But on occasions, when very complex or difficult-to-machine shapes are required, materials that are very difficult to work with such as INCONEL are required, or the print run is very limited… in these cases, additive manufacturing technology is tremendously more advantageous.
It is a young technology and there are still many use cases to be discovered, but to date it is being used in the medical-dental prosthetic sector. For example, it makes it possible to reduce the cost of manufacturing implants by practically half.
It is also of interest for the manufacture of mold inserts, which require complex internal cooling pipes that can only be done with this technology.
A very large and virgin sector are all those pieces made to date with electrical penetration or 3D laser engraving.
Laser additive manufacturing technology, from the point of view of energy cost, is very good. To give you an idea, our machine when it is working does not consume more than a domestic iron (about 2400W). Comparatively with other technologies, only in electricity there are significant savings. To this you must add that it is not necessary to manufacture a negative, and therefore amortize several machines (the one that makes the negative and the one that transfers the negative to the final piece). This means significant savings both in manual operations and in amortization of equipment.
Of course, the printing of prototypes, unique pieces of modeling or printing on very exotic or difficult-to-work materials is also important.
E.E: Give us some examples of projects in which your products / solutions were used?
SAMYLABS: At this point I love to tell the case of a client that we have in Catalonia manufacturing wine corkage marking stamps.
It is an example that I think he perfectly captures those cases of special niches to be discovered that I am telling you about.
This client manufactures metal stamps, which are heated by induction, to roll the wine corks over the stamp and heat transfer the drawing with the logo of the wine brand to the cork.
To date, the traditional way of making these stamps consists of machining a graphite (negative), to later use an electrical penetration machine that attacks a steel sheet with the negative and transfers the drawing.
This operation means that you need a high-precision machining center, an electrical penetration machine, the cost of graphite, electricity, the machine change operation…
On the other hand, with additive manufacturing, it is as simple as putting several plates (substrate) on the printing plate and growing the drawing on them.
In less time, with less expense, with a single operation and a single machine, it is possible to remove 4 stamps, in what used to take to attack a stamp. In addition, even higher resolution is achieved in the drawing.
We also have other success stories in the manufacture of inserts, spare parts that are not in stock or very complex parts that are impossible to manufacture with other technology.

E.E: What products / solutions were used in these projects?
SAMYLABS: To print you not only need the machine. You need an ecosystem. This ecosystem usually consists of a vacuum cleaner, a screener, a cabinet with humidity control to preserve the dust and of course tools for post-processing. Metallic dust generates a lot of static electricity and when you have to clean the machine you cannot use any vacuum cleaner. You need a special vacuum cleaner prepared to suck up the dust you are working with.
In the same way, once you have printed a piece, it is necessary to clean and recover the excess powder for the next print and it is very important that the powder does not oxidize. For this reason, a special sieve is required. The same to preserve the powder.
The technology itself leaves a rough finish and many of the parts require post processing. More even in areas where it has been necessary to put supports. Postprocessing is key to providing a quality piece. Here polishing machines, saws, etc. are necessary depending on the application. From SAMYLABS we also provide this ecosystem and advise our clients on everything they need.

E.E: What was the feedback from users?
SAMYLABS: Everyone agrees that it is an easy to use and clean machine with friendly and very flexible software. Also consider that the price of the machine is very competitive and the print quality is very good for the technology.
Of course, there are also clients who complain about some elements of the technology such as having to generate supports, or the need to post-process the parts afterwards.
Media have sold us a false image, in which 3D printing is putting the model in the machine and pressing the print button and that’s it. That is a big lie. In the traditional technique, that is not the case either. In the same way that it is necessary to use CAD/CAM software to generate the trajectories and there must be a specialized operator, exactly the same thing happens in additive manufacturing.
It is a new technology, which requires a design oriented to its peculiarities. The same part for a given purpose can be designed in different ways, and one of the ways will be extremely difficult to print, or very easy.
People who come from the workshop and suffer from the requirements of traditional technologies, appreciate the versatility that this new technology gives.
E.E: How can users work more sustainably with your products / solutions?
SAMYLABS: Make a good design, which minimizes the number of supports is the key.
If this rule is respected, using the machine is very simple. Then it is only required to be tidy, keep the workspace clean, and safety above all safety.

There are materials that are not dangerous in terms of explosion, but others such as aluminum or titanium, you must be very careful. Of course, these materials require a different ecosystem that is much more strict.
E.E: What are your forecasts for the first half of 2023?
SAMYLABS: From a commercial point of view, we hope to be able to sell a couple more machines in Spain and abroad.
From a development point of view, right now we are working on improving the features of our equipment with a higher print volume, and new control features such as closed-loop printing.