Tridelta Meidensha GmbH is a mid-sized company in Thuringia, producing Metal Oxide Surge Arresters for overvoltage protection in Medium Voltage and High Voltage electrical power systems up to 800kV. The company is looking back to a long company history reaching back to 1889, where insulators for electrical systems have been produced.
In the sixties, Tridelta began to produce silicon carbide surge arresters and later zinc oxide surge arresters in porcelain housings for continuously rising customer demands and voltage levels. Today, they are one of the leading manufacturers of surge arresters with sophisticated production technologies, state-of-the-art materials and cutting-edge designs. Additionally, their portfolio comprises a variety of surge arrester mechanical and electronical accessory devices for condition assessment and maintenance.
Easy Engineering: Which are the most digitalized products / solutions?
TRIDELTA: Our “smartCOUNT” is the latest development of a series of surge arrester monitoring devices for predictive maintenance. This device tracks down faulty surge arresters based on characteristic surge arrester leakage current patterns, just before they fail and cause a blackout on the power transmission line.
E.E: What are the characteristics of these products / solutions?
TRIDELTA: The device consists of a surge arrester mounted Datalogger and a Transponderpad for data extraction. The Datalogger is capable to cover an impressive range of currents from leakage currents down to one micro amp up to transient discharge currents of 100 kilo amps. It´s power supply works self-sufficiently by harvesting the energy of the pure measuring signal whist the device keeps its power consumption at a few nano-amps by using state of the art ARM Cortex M3 ultra-low-power microcontroller technology. The so called Transponderpad uses a radio technology called NFC for data transmission which previously has been developed for contactless payment with smartphones. Configuration and Data handling takes place with a smartphone and the smartCOUNT App using the NFC interface. Data can be accessed by phone, downloaded to PC or uploaded to the smartCOUNT Cloud, where important physical values are conditioned, displayed and evaluated. The Cloud includes an intelligent algorithm to detect suspicious patterns, alerts the user and marks according devices in a well organized overview of the surge arrester fleet.
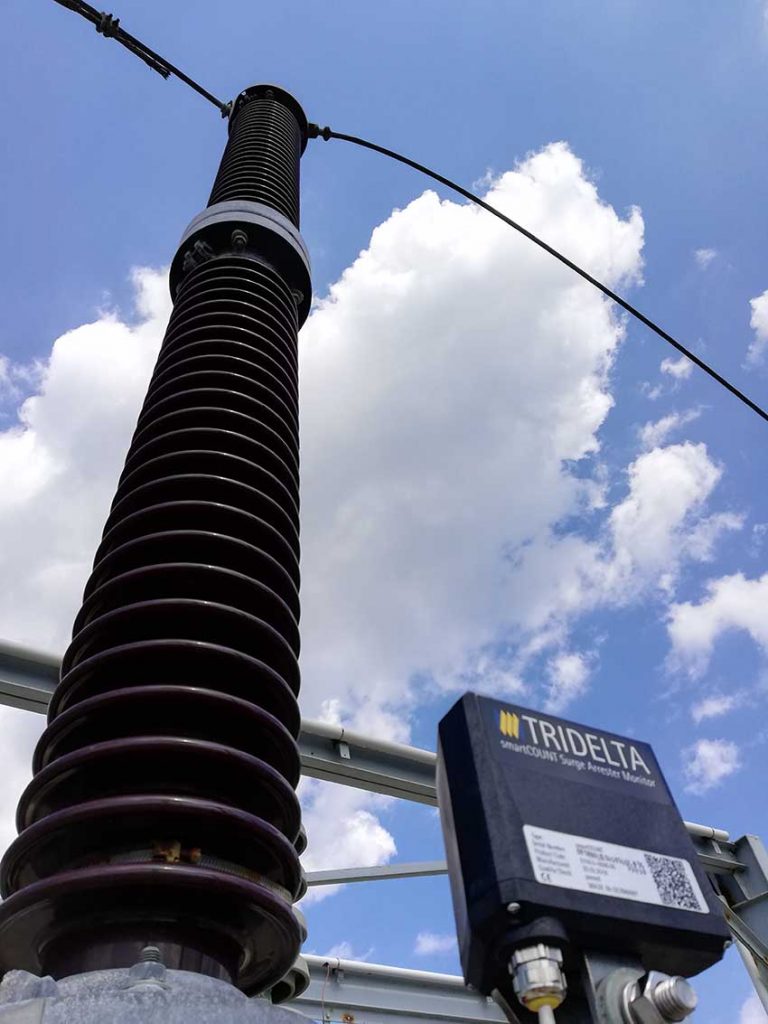
E.E: What are the benefits for the users?
TRIDELTA: Predictive Maintenance means to be able to replace equipment before it fails. This is of great importance for utilities around the world, because outages cause damages on extremely expensive transformers and other high voltage equipment, high maintenance effort and penalties due to missing energy delivery.
With our smartCOUNT it´s possible to really detect ageing or fault affected surge arresters and decide for replacement and to reduce scheduled shutdowns and unplanned outages.
E.E: In what type of projects are they used?
TRIDELTA: Typically for:
- Old and new substation surge arresters to monitor their health and predict their end of life;
- Transmission Lines, where surge arresters protect hundreds of kilometres of overhead lines from flashing over due to lightning strike;
- Electrical highspeed trains up to 300km/h;
- Nuclear power plants, hydro power plants and other;
- High voltage power supplies of big consumers like steel industry;
- High voltage test stations in harsh climatic environments.
E.E: Do you plan to implement digitalization in other products / solutions?
TRIDELTA: Yes, currently we roll out the next project, based on the smartCOUNT with IoT functionality.
E.E: How important is digitalization in your field?
TRIDELTA: Still the High Voltage Industry is pretty conservative but with our products we push the development and acceptance of new technologies forward. Also we are part of the IEC standardization group TC37.
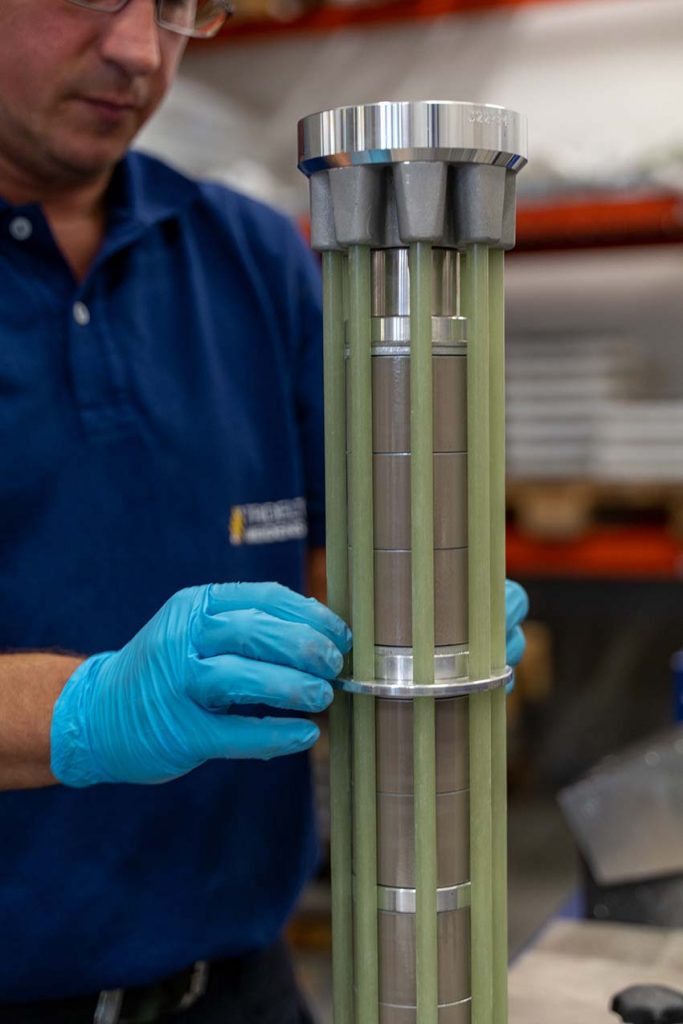
E.E: In which directions do you think digitalization is heading towards?
TRIDELTA: Clearly to fully cover overall industries. In the energy sector it´s hard because digitalized energy equipment entails a big risk of unauthorized access to important security functions. Therefore, suppliers like we are must pay big attention to responsible design and application. Furthermore, many specialized solutions for measuring equipment, communication protocols and data systems exist, there is a clear need of uniformity and standardization. The focus on digital systems on HV equipment will be conformity and security.
E.E: What was the employee feedback regarding the digitalization process?
TRIDELTA: We have a great interest in those new technologies within our company, we brought up regular presentations in the company to present and explain the latest findings and developments.
E.E: What industries do you think will be more digitalized in the future?
TRIDELTA: Its definitely electrical power industry and automotive.
E.E: Did the current situation made your company implement digitalization sooner than predicted?
TRIDELTA: Yes, the pressure from the market for a device like this rose day by day. We struggled hard to push through the development, anyway we afforded a 18 month pilot test in various countries and environmental conditions to check the quality of the device in service under real life circumstances.

E.E: What are your forecasts for the first half of 2021?
TRIDELTA: Well, we just got a big order for a project in Vietnam. The increasing number of reference projects gives the worldwide customers more and more confidence and with that more success to us. Until now we have sorted out several suspicious surge arresters suffering from humidity ingress and material ageing together with our customers around the globe, just with our device.