The high-precision five-axis machining center Kern Micro HD has established itself on the market since its introduction in 2019. Just this year – 2022 – at least 40 machines will be delivered. Now it is setting new standards again. In order to further increase the productivity of the high-end machine for a wide variety of applications, the company’s engineers have developed innovative additional options that guarantee major advantages.
Making benchmarks better is as difficult as it is important. The machine builder Kern Microtechnik puts a lot of energy into the development of its machines – especially the technological benchmark Kern Micro HD. For Technical Director Sebastian Guggenmos, this means: “We are constantly in contact with our customers, partners and scientific research, take up suggestions and realize them in our new developments.”
Among other things, Kern has succeeded in integrating a new generation of shaft-cooled spindles, which can fully exploit its strengths, especially in combination with the superior microgap technology of the Kern Micro HD. Known as the CSC spindle (Compact Shaft Cooled) and equipped with HSK 40, it reduces shaft growth, extends spindle service life, increases the performance of the Kern Micro HD and shortens the tool spindle’s already short run-in times by another 80 percent.
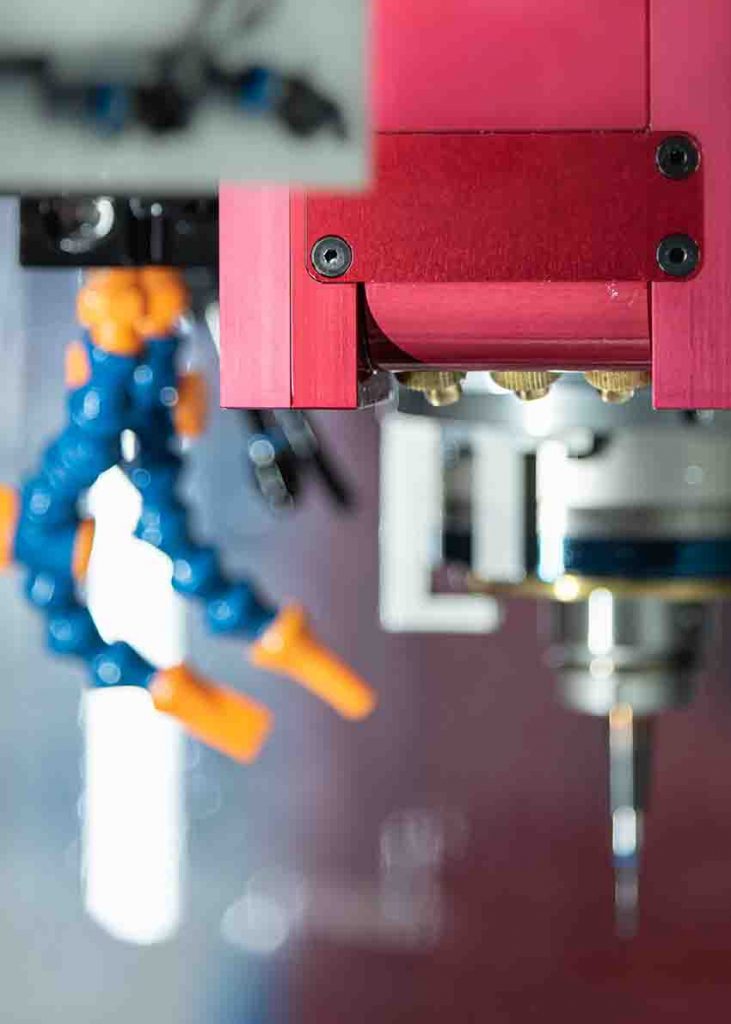
Sebastian Guggenmos is enthusiastic about the improvements achieved and concludes: “The spindle is absolutely temperature-stable after a very short time, even with large speed jumps. With this feature, the highest accuracy values can be achieved immediately on the workpiece and for our customers this significantly increases the precious machining time. In addition, the often so important probing processes for workpiece inspection can be made much more efficient. ”
The basis for the improvements in the spindle is a newly designed, integrated cooling process. The bearing-less rotary joint of the shaft cooling system is extremely compact. Thus, the dimensions of the CSC spindle remain almost unchanged compared to the standard spindle. “On request, it can also be installed in existing machines,” says the managing director and mentions the increased speed of 45,000 min-1 as an additional, rather smaller advantage. It is about 3000 min-1 above the default value, which means an additional, small increase in productivity during the machining process.
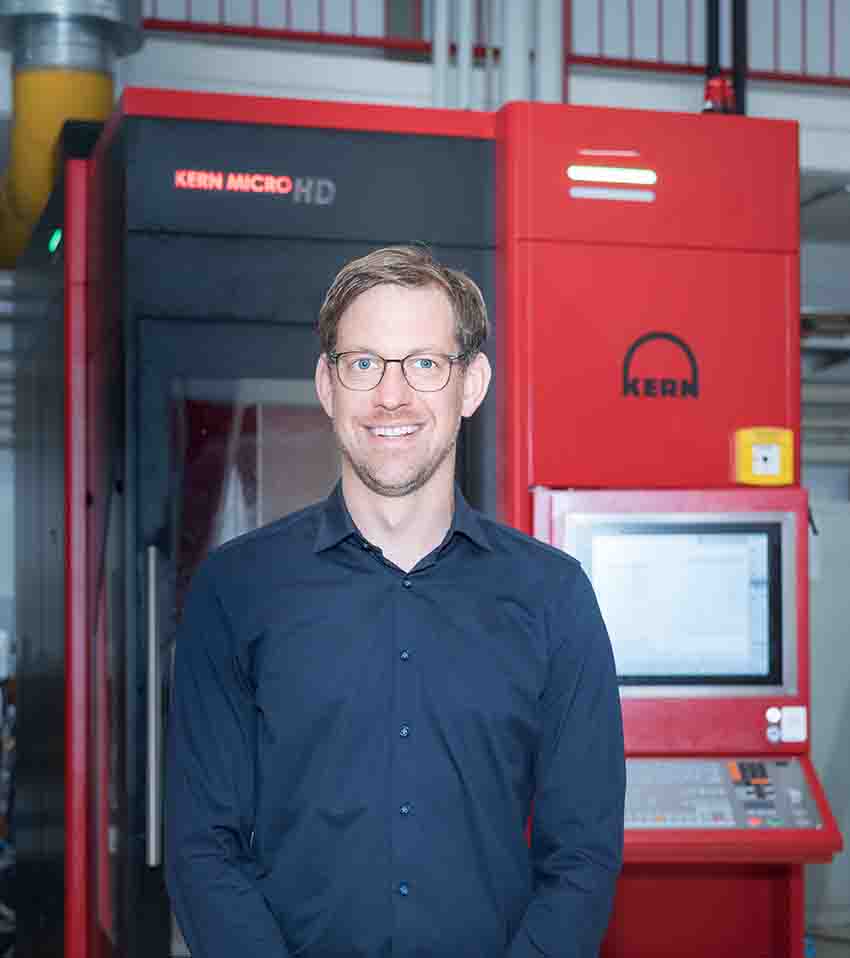
Sebastian Guggenmos is pleased about the many new developments that are now available for the Kern Micro HD. The Kern Managing Director knows how important it is to be able to offer innovative improvements: “The technical advantage and the ability to make the difference is extremely valuable, especially in times of crisis. “
Photos: Kern Microtechnik GmbH
Processing Priorities – fast and easy
Equally interesting for many operators is the option to set priorities intuitively and quickly with the new software feature “Advanced Setting”. While the three parameters speed, accuracy and surface quality are equally balanced in the standard, they can now be adjusted as required.
For example, if the operator wants to optimize roughing, prioritizing the processing speed helps. This allows roughing to be accelerated by up to 30 percent compared to standard operation, which raises the productivity of the machining center to a new level.
If the finish depends on maximum shape efficiency or on surface quality in the nano range, the user can set the appropriate focus in the program.
The selection can already be made during programming. A mouse click with a change of a parameter is sufficient, and the desired cycle is integrated.
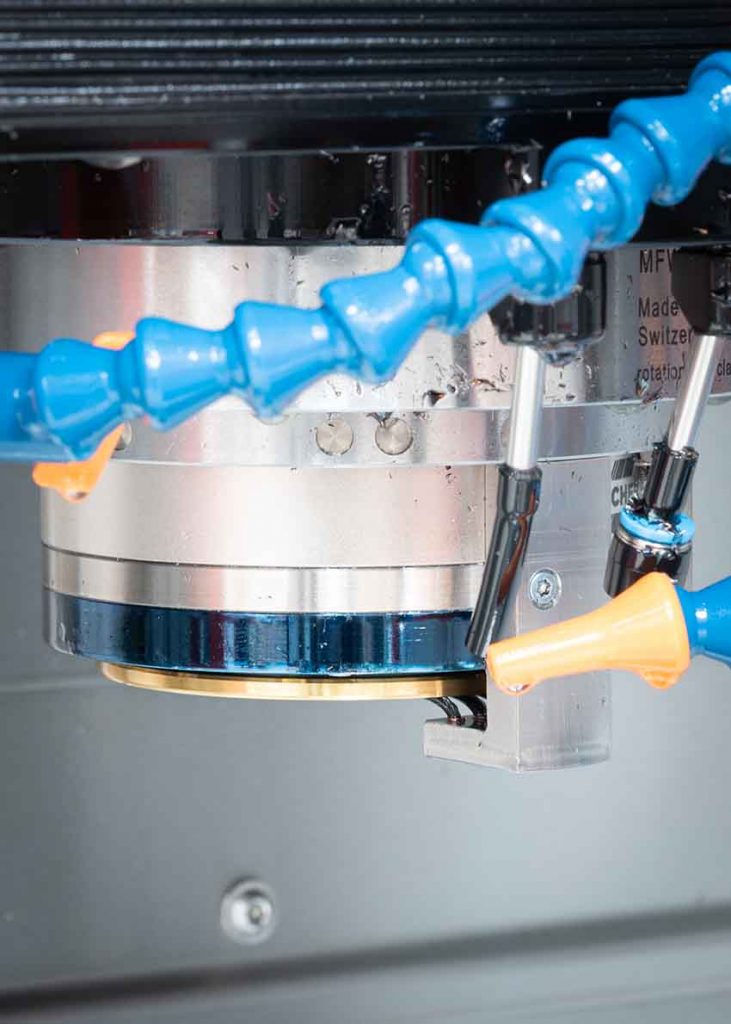
The cooling of the new CSC spindle shortens the already short run-in times of the tool spindle in the Kern Micro HD by another 80 percent.
Automatically adjust coolant nozzles
As another option, Kern offers coolant nozzles that automatically adjust to the tool tip. This eliminates the need for manual readjustment. The nozzles correspond to the stored tool database and the tool length entered there. This way, the coolant (whether oil or coolant) always does its job exactly where it is best – at the Tool Center Point. An additionally integrated blow-out function also ensures reliability of the coolant nozzles in the long term. As a result, the tools are spared, and their service life is increased.
Last but not least, for new Kern Micro HDs it will be possible to retrofit “coordinate grinding” – an option that is already very popular today. Until now, this was not possible because of several differently structured individual components.
Advantage through innovation
Kern has succeeded in integrating three real technical innovations into the Kern Micro HD, thus setting the benchmark for high-precision machining centers. At a glance:
- The shaft-cooled CSC spindles ensure greater productivity and accuracy on the part
- With the easy-to-use software feature “Advanced Setting”, roughing processes can be accelerated by up to 30 percent compared to standard operation.
- New coolant nozzles adjust automatically and thus guarantee constant cooling at the Tool Center Point.

Kern Microtechnik GmbH
KERN Microtechnik GmbH, Eschenlohe, employs 200 people and operates successfully in more than 30 countries worldwide. The focus is on two business areas: The development and manufacturing of high-precision machining centers and the contract manufacturing of milled parts in the micro and nano range.
Milling centers from KERN are used in KERN’s contract manufacturing series production. This enables KERN to not only manufacture high-precision machines, but also to support their customers with the necessary process know-how. Customers become technology partners and are a part of the “KERN family”. Advice for ideal operation and process integration are always included – from an idea to the finished part. This enables KERN customers to increase their profit and competitiveness.
The product portfolio of contract manufacturing includes prototype, single part and serial production as well as mounting assemblies and support in the construction phase. The parts are machined by milling, drilling, EDMing and grinding.
Kern Microtechnik GmbH
Irma Gschmeißner
Olympiastraße 2
82438 Eschenlohe
Tel.: +49 (0)88 24 / 91 01-0
Fax: +49 (0)88 24 / 91 01-124