Inspecto is a company born out of a specific need at the beginning of the Covid pandemic. The founders, Christophe Renaud and Daniele Brunetti, run a company specialized in the design and construction of heavy equipment, mainly for nuclear power plants. The inability of the client’s inspectors to travel and the need to continue fabrication activities prompted the founders to investigate a remote inspection system that could meet the industry’s strict safety criteria. This is where the “embryo” demo of the current INSPECTO DQI platform was born. It is a digital ecosystem to manage inspections, audits, quality control in their entirety.
Interview with Daniele Brunetti, Co-Founder of Inspecto SAS.
Easy Engineering: What are the main areas of activity of the company?
Daniele Brunetti: INSPECTO is specialized in the consultancy for quality processes digitalization, engineering activities and business development. However, its main focus has expanded to include the development and implementation of INSPECTO DQI platform. The applications of the software are among the most varied, born for industry, nuclear, energy, oil&gas and marine. We like to boil it down to “any activity that needs to be monitored” and hope that gives an idea. We were born in the engineering sectors, but we realized how this can be applied to the most varied sectors, from pharmacy to catering, from healthcare to insurance.
E.E: What’s the news about new products?
D.B: INSPECTO DQI platform is the latest innovation, offering a comprehensive solution for inspections, audits, quality control and documentation management. Users can seamlessly access the web platform from any device—whether it be a PC, smartphone, or tablet—without the need for installation. A straightforward and intuitive interface, underpinned by a comprehensive architecture, facilitates the rapid creation of projects tailored to specific requirements. This includes the development of Gantt charts outlining activities and inspections planned or already completed. Users have the capability to upload pertinent documents and designate team members with access privileges based on distinct profiles, corresponding to various project phases.
Throughout planned activities, individuals can efficiently complete inspection templates digitally, address non-conformities, and allocate diverse corrective and preventive actions—all while digitally signing pertinent documents. The platform accommodates video inspections, even those unscheduled, by seamlessly collecting photos and videos automatically. The amassed documents and media, coupled with downloaded documentation, can be effortlessly utilized to generate intervention or manufacturing files with just a few clicks.
Furthermore, we are developing Artificial Intelligence (AI) modules to support operators in day-to-day activities.
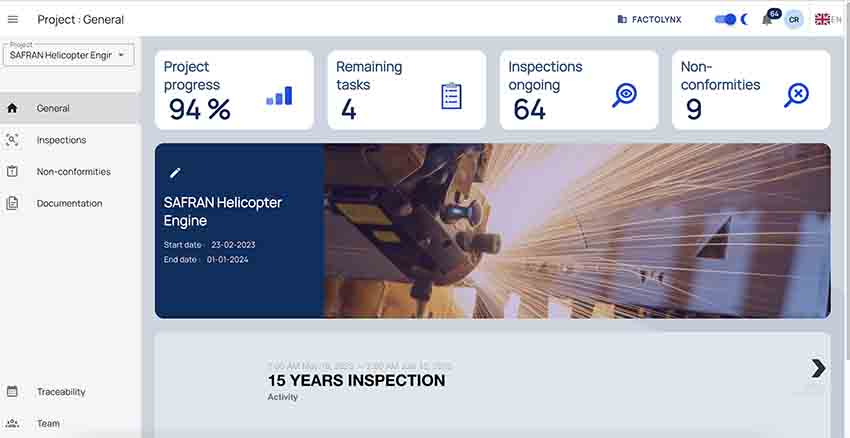
E.E: What are the ranges of products?
D.B: INSPECTO specializes in comprehensive 360-degree consulting services. Within the realm of activities related to the digitalization of quality processes, our platform is a product with a broad and ever-evolving range of functionalities, as well as virtually limitless applications. Our commitment to continuous improvement ensures that INSPECTO DQI remains at the forefront of innovation in the digital quality management landscape.
E.E: At what stage is the market where you are currently active?
D.B: We are fully operational and already engaged with more than 50 medium size clients across various sectors, from industry to inspection companies and freelance inspectors. We are also conducting pilot tests with some large corporate groups who need global and multi-country deployments. Upon reviewing the software, they are impressed by the significant advantages that its implementation can offer.
E.E: What can you tell us about market trends?
D.B: The market trend suggests a growing need for digital solutions in quality control, inspections, and documentation management. INSPECTO is at the forefront of addressing this trend with its comprehensive digital ecosystem.
Digitalization can be intimidating at times, but the truth is that it must be approached correctly because it brings significant benefits. Digitizing a process means not only abandoning traditional paper-based systems or the like but also accelerating and making the process itself more reliable and traceable. Easy access to data and the ability to prevent risks align with common sense and continuous improvement, essential for the survival of companies. Supporting employees with innovative technological tools doesn’t imply replacing them; it means providing tools to make their work easier and reduce psychological pressure related to the risk of errors. These are the current and inevitably future trends.
E.E: What are the most innovative products marketed?
D.B: The most innovative product is the INSPECTO DQI. It represents a sophisticated but user-friendly digital ecosystem, revolutionizing the landscape of inspection, audit, and quality control activities. The platform seamlessly integrates local or remote inspections alongside other critical functionalities. These include the dematerialization of control forms, digital management of non-conformities, corrective and preventive actions, and allocation and monitoring of specific tasks, all comprehensively accessible through a unified dashboard.
The system, geared toward continuous improvement, processes project data to provide vital information and performance indicators (KPIs) related to inspection statistics and the overall project situation. It facilitates root cause analysis of non-conformities, enabling the implementation of preventive actions and mitigating future supply challenges. Every operation within INSPECTO DQI is meticulously tracked, ensuring transparent stakeholder relations and a robust response to Counterfeit, Fraudulent, and Suspicious Items (CFSI) risks in the production chain. Electronic signatures on control documentation further enhance security and compliance.
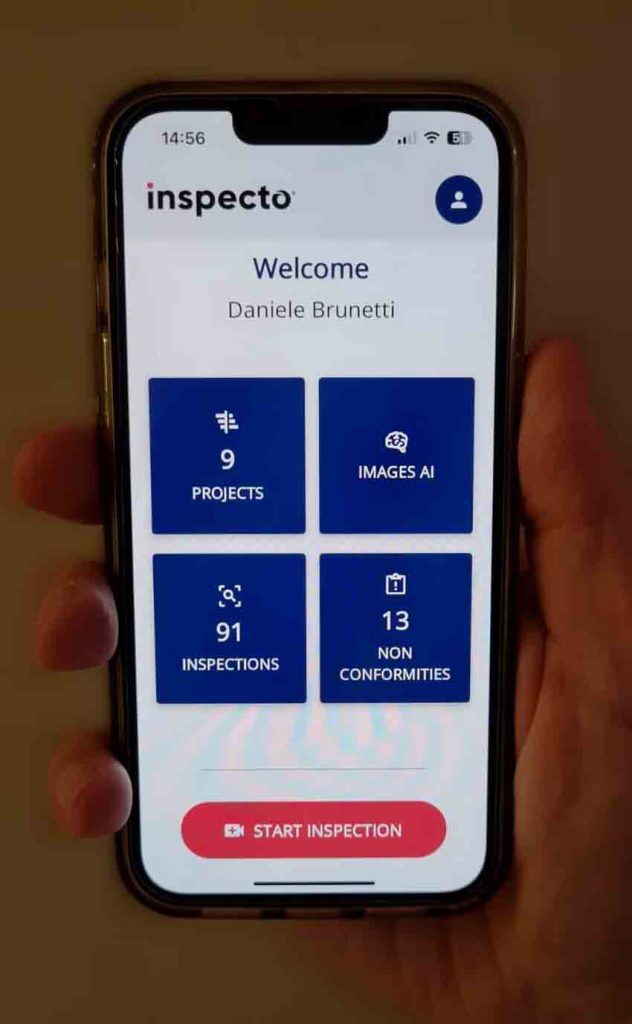
Elevating its capabilities beyond digitization, INSPECTO DQI incorporates artificial intelligence (AI) to support decision-making. The introduction of an AI module, crafted by our PhD in artificial intelligence, specializes in detecting cracks in weld seams and structures. This groundbreaking technology utilizes machine learning and a comprehensive database, allowing part scanning from any camera-equipped device, ensuring accuracy in identifying the presence or absence of cracks. Complementing traditional methods like penetrant testing and magnetic particle testing, INSPECTO DQI’s AI modules cater to diverse industries, meeting the growing demand for technological support.
In essence, INSPECTO DQI transcends conventional digital platforms, becoming an indispensable tool for streamlined and innovative quality management. Inspecto DQI emerges as a robust supporter of ISO standards, especially ISO 9001, ISO 19443, seamlessly incorporating their principles into your operational fabric. This innovative solution aligns with ISO benchmarks through various key facets. In the digital realm, it transforms your Plan-Do-Check-Act (PDCA) cycles and risk management processes, bringing them into the contemporary era. Delivering on the ISO emphasis on measurable objectives, Inspecto DQI provides comprehensive Key Performance Indicators (KPIs). These KPIs offer detailed insights into your performance metrics, promoting a thorough understanding of your operations.
A cornerstone of ISO standards is the commitment to continuous improvement, and Inspecto DQI is crafted precisely to sustain and enhance this endeavor. It becomes the conduit through which you can diligently track and refine your processes over time, fostering a culture of ongoing enhancement. In addressing the critical issue of Counterfeit, Fraudulent, and Suspicious Items (CFSI), Inspecto DQI steps up to support your efforts. It becomes a reliable ally in preventing and managing CFSI issues, safeguarding the integrity of your production chain. Striking a delicate balance between acceleration and security, Inspecto DQI leverages digital technologies to expedite your tasks while upholding the paramount importance of data security. This aligns seamlessly with ISO standards that advocate for efficiency without compromising safety.
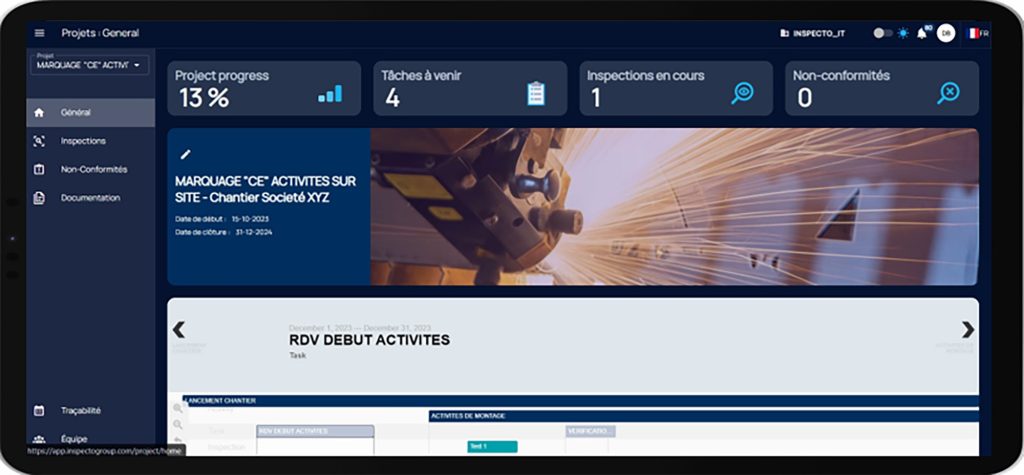
Culturally, Inspecto DQI aligns itself with your organizational ethos and modus operandi, offering a harmonious integration into existing workflows. This strategic alignment ensures a cohesive and standardized work environment, resonating with the cultural expectations set forth by ISO standards.
In essence, Inspecto DQI doesn’t just meet ISO standards; it elevates your operations to a level where they become a shining example of efficiency, security, and a relentless commitment to continuous improvement and 360 sustainability.
E.E: What estimations do you have for the rest of 2023?
D.B: The road ahead in the coming years seems to suggest a growing trend towards the digitization of processes, cost reduction, environmental respect, and consideration for human labor, with an increasing focus on safety aspects. Moreover, all international standards are increasingly guiding us towards a more meticulous management of processes, risk, and opportunities. In this context, we cannot overlook considering our product as a significant support for the company of the future, focusing on continuous improvement, sustainability, and the development of new AI modules. Our commitment to ongoing innovation and expansion into different industries and new applications.