INTECH3D has been manufacturing adapted solutions in the industrial sector for 7 years and has 12 years of experience with filament extrusion technologies. The biggest change for them has been the introduction of complementary technologies for additive manufacturing, such as 3D scanning and 3DP applications.
After a few years of experience and of thoroughly analyzing the pain points of clients, it was clear that focusing on hardware was not enough, a software ecosystem was highly needed. That is when PRINT&GO, a groundbreaking product that INTECH3D is partners with, was created. It is a 3DP application that lets you plan, monitor and control the entire 3D printing process, increasing efficiency in your production.
Easy Engineering: How important is innovation and R&D for actual and future products?
INTECH3D: In a constantly evolving industry, innovation and R&D are fundamental to stay competitive and unlock the full potential of 3D printing.
If we want to reach higher printing speeds, increased precision, expanded material capabilities, greater sustainability and enhanced reliability, we need to keep pushing towards newer and better hardware, software, and materials.
E.E: What are the needs of the users on the markets that you are active?
INTECH3D: 3D printing technologies are transversal, therefore, needs will be different depending on every company, department and application.
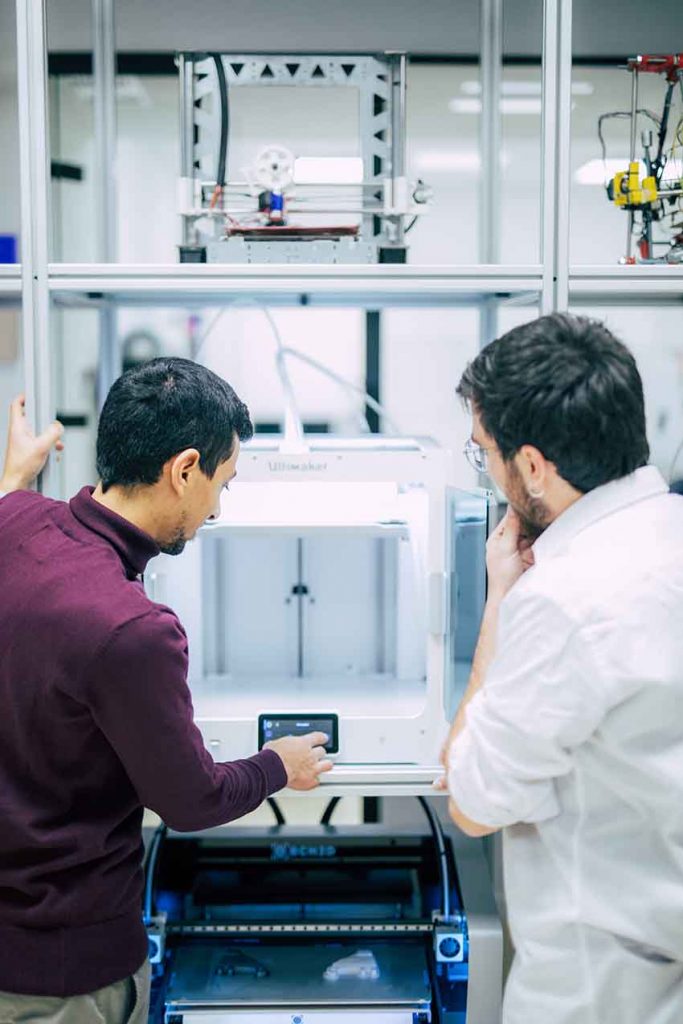
However, our clients mostly want to introduce 3D printing to address the following needs:
- Verification before series production
- Manufacture of control and assembly tooling
- Small-Batch Manufacturing
- Time and cost reduction
- Workflow Integration and Automation
- Material Variety and Performance
- on-demand production
- End Use Part Manufacturing
E.E: What products/solutions does your company bring that are the most innovative?
INTECH3D: At INTECH3D we cover the entire product life cycle: consultancy, validation, commercialization, facility, training and official technical service 24/5. But we are also distributors of a cutting-edge product: PRINT&GO.
PRINT&GO is a workflow software that covers the entire 3D printing process, from the entry of the G-code until the part is completely printed, allowing you to monitor and control it remotely. The platform adapts to what the client needs according to the number of machines and the sector in which it is being used.
Thanks to this solution, you will be able to:
- Control your printers
- Organize your projects
- Get analytics of your impressions
- Assign different users and roles
- Keep track of your printers
- Detect spaghetti thanks to AI
- Produce continuously 24/7

E.E: What are the challenges that users encounter in their line of work?
INTECH3D: Overall, use of traditional methods without complementing them with 3D printing is usually more time-consuming and expensive. It also allows much less versatility, making it difficult to manufacture complex geometries and personalize each product.
E.E: How does innovation help them in these situations?
INTECH3D: Innovation plays an essential role in helping users overcome the difficulties they encounter in their work by harnessing the power of 3D printing.
Thanks to advancements in material science, printed products can be stronger, more durable, flexible or even have unique properties like biocompatibility or heat resistance. A broader range of materials allows users to overcome limitations and meet diverse needs, in addition to being more affordable to traditional materials.
Newer printing technologies and software integrations also address the time-related challenges users encounter. Faster printing, automated processes and optimized workflows make 3D printing more efficient and accelerate product development cycles.
Furthermore, 3D printing has the potential to transform manufacturing by minimizing waste, facilitating local production, optimizing resource usage and promoting sustainable and recycled materials.

E.E: How is digitalization changing your field of activity?
INTECH3D: Digitalization is causing a major transformation in the field of 3D printing, bringing about revolutionary changes in technology, processes, and applications.
One example is on-demand manufacturing. Businesses can now print a wide range of tools or parts in-house and on-demand, simply by consulting an online library that functions as a digital warehouse, eliminating the need for physical inventories.
Digitalization also enables the gathering and utilization of data throughout the entire 3D printing process. Built-in sensors in 3D printers capture real-time data, such as printing parameters, material usage, and machine performance. This data can be analyzed to optimize print settings, keep track of machine condition, and predict maintenance needs.
E.E: What tasks/processes can users do easier and more efficient with your products/solutions because of innovation?
INTECH3D: Innovations in 3D printing technologies, such as advanced support structures, multi-axis movement, and high-resolution printing capabilities, allow users to easily create intricate and organic shapes.
There are also complementary technologies, such as 3D scanning or thermoforming, that are really helpful for duplicating parts without any knowledge of 3D modeling.

Thanks to software like PRINT&GO, users can have their printers or their 3D printer fleet work unassisted, while they monitor the production remotely and in real time, providing cost reduction through an optimized workflow. With this solution, they can also achieve continuous production 24/7, through the integration of cobotics and automation add-ons to 3D printers.
E.E: Tell us some tips & tricks about prevention / maintenance for your products/solutions?
INTECH3D: PRINT&GO is already a solution for your 3D printing process on its own, as it offers you preventive maintenance of your 3D printers, access to diagnostic pieces, help desk integration and chat 24/5.
As for lengthening your 3D printers’ lifespan, it’s always important to perform regular maintenance, follow the manufacturer’s instructions for printer and component cleaning, bed leveling, calibration, software update and material compatibility, and to use high-quality filament.