Fixing, lifting, moving – that’s what AERO-LIFT offers their customers. AERO-LIFT Vakuumtechnik GmbH, from Germany, ensures productivity and ergonomics at the workplace through vacuum lifting devices. Their solutions lift, transport and even rotate a wide variety of transport goods using only the power of vacuum. In this way, productivity at the work place can be increased. Companies also ensure the long-term health of their employees by providing ergonomic working conditions.
Easy Engineering: What are the main areas of activity of the company?
AERO-LIFT: Vacuum lifting technology can be applied to almost any good and thus to any industry. Whether metal parts, sheet metal, wood, glass, paper, plastic or other materials: Almost everything can be lifted and moved efficiently and ergonomically with vacuum lifters.
In the metal industry, for example, vacuum lifters lift, swivel and rotate metal sheets of any format and thus ensure efficient loading and unloading of laser cutting machines. Even prefabricated sheet metal parts with recesses can be easily lifted and moved by combining them with VUSS large-area vacuum gripper technology. Likewise, large and very heavy sheets of up to 60 tons or aerospace workpieces such as rotor blades are no obstacle for our vacuum lifting devices.
Our solutions are also used in the chemical, pharmaceutical and food industries or in the shipping and logistics sector. Vacuum and tube lifters from AERO-LIFT enable an employee to move cartons, drums, sacks, buckets and canisters in an ergonomic and user-friendly manner.
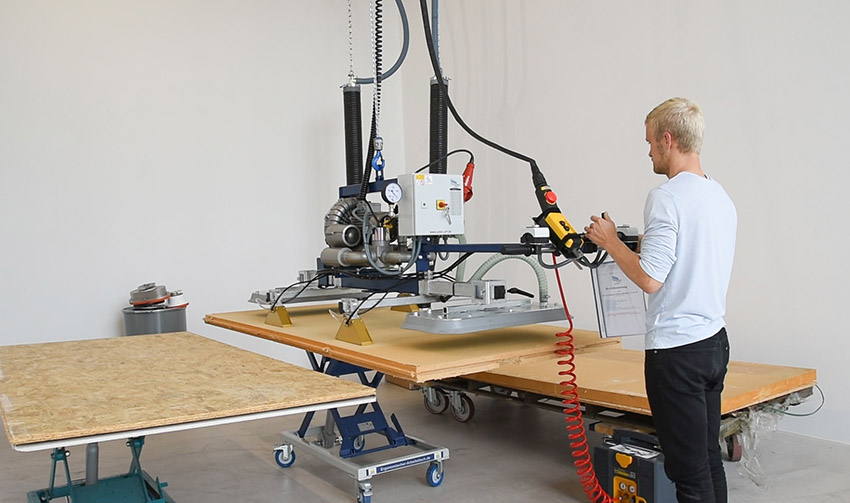
Another large field of application are the construction and trade sectors. Whether in the production of carpenters, joiners, roofers or building contractors or directly on the building site: Our lifting machines ensure a material-friendly and ergonomic movement of wooden boards of any kind, wooden beams and planks, prefabricated wooden parts, furniture parts or building materials. Our famous construction site lifters like the CLAD-BOY install panels and trapezoidal sheets on the roof and walls without damage. Even panels, glass panes and windows can be safely transported and attached using special construction site equipment.
AERO-LIFT is known as an expert for special solutions in the competition: With our experienced engineering team, we are driven to always find suitable solutions for our customer’s individual lifting problem.
E.E: What’s the news for 2020 about new products?
AERO-LIFT: A particularly impressive solution, which we have been successfully selling on the market for years, is the combination of a manual tube lifter with a VUSS large-area gripper as suction foot. With the large-area gripper technology, workpieces with recesses and holes as well as several workpieces can be gently and reliably fixed and moved. A common field of application here is in automation. AERO-LIFT uses the flexibility of large-area grippers for manual handling by means of a tube lifter. This means that a wide variety of goods can be moved with just one device, regardless of shape and surface, e.g. onto processing machines. This combination has proven itself for years. This year we have built the largest large-area gripper module into a tube lifter, which can lift up to 75 kg and move it in a user-friendly way.
Furthermore, we were able to solve a common problem in the construction and timber sector recently. Materials in the construction industry are becoming more and more diverse. Companies are faced with the challenge of transporting workpieces with the most varied properties, e.g. airtight wooden boards, porous wooden boards, plasterboard, but also soft fibre boards, which are very heavy and fragile. AERO-LIFT combined the AERO-PORO, a vacuum lifter for porous boards, with a needle gripper module, which is used for the transport of soft fibre boards and other insulating material elements. The operator can switch between the two applications quickly and without tools, thus remaining flexible. In addition, a material-friendly, safe and ergonomic working method is guaranteed.
A further innovation in our product portfolio is the certification of our equipment for potentially explosive atmospheres. In ATEX areas or clean room areas, specific regulations apply which make the handling of explosive materials safer. Our vacuum lifters and tube lifters can be configured according to these regulations. Especially in the pharmaceutical and chemical industries, heavy sacks, canisters, drums and cartons with hazardous materials must be transported. AERO-LIFT has created the solution to effectively humanise working life even in these extreme zones. In addition, the safety of the employees is extremely increased.
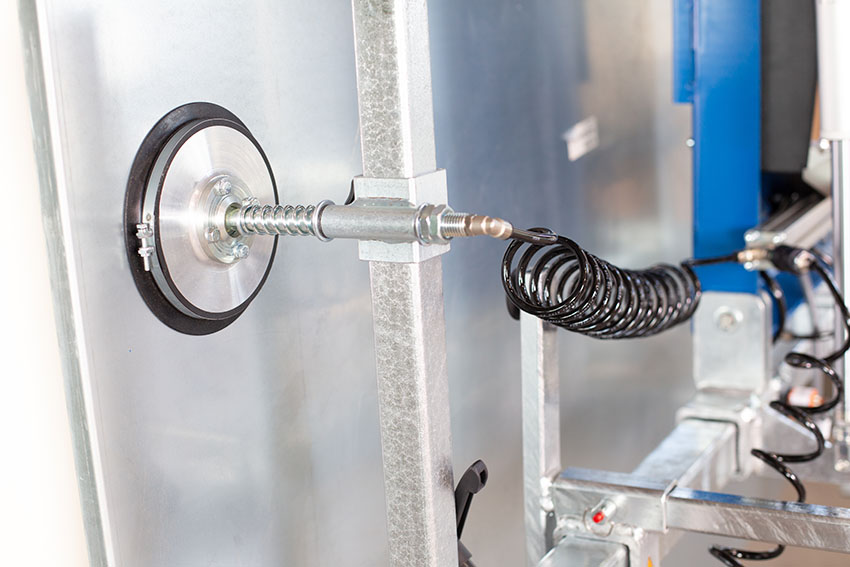
E.E: What are the ranges of traded products?
AERO-LIFT: Our product range extends from manual handling solutions for production or logistics, to mains-independent devices for use on construction sites, to fully automated systems. We offer our customers a complete solution from project planning and development to installation and maintenance of the system. In our new AERO-LIFT ACADEMY, customers receive first-hand tips and tricks and can receive personal training from us.
E.E: At what stage is the market where you are currently active?
AERO-LIFT: The market for handling technology correlates with the awareness of ergonomics, humanisation and health. Incorrect lifting of loads in the workplace is the number one cause of back problems. Vacuum lifting aids reduce the weight to be lifted by the person and avoid unfavourable, bent postures. These preventative measures reduce absenteeism from work due to slipped discs and back problems. Healthy and motivated employees are the result. We therefore recognise continuous growth.
E.E: What can you tell us about market trends?
AERO-LIFT: The use of our handling technologies fits into the trend of the low touch economy. Due to the Covid-19 crisis, processes in companies are being redesigned. To reduce health risks, companies are forced to adapt to strict guidelines, including low touch interactions and limited meetings. Not only industries such as food, medical technology or logistics are particularly challenged. Looking at how long the virus persists on different surfaces, it becomes clear that companies in the sheet metal, plastics and woodworking industries also need to strategically optimise processes to meet the new requirements. This is where our handling solutions help. Almost all of our vacuum lifting devices in the manual handling sector have an operating handle that creates a certain distance, if only for safety reasons. In addition, the ergonomic design means that it is not necessary to touch the actual goods being transported, which is an enormous advantage when it comes to meeting new hygiene standards.
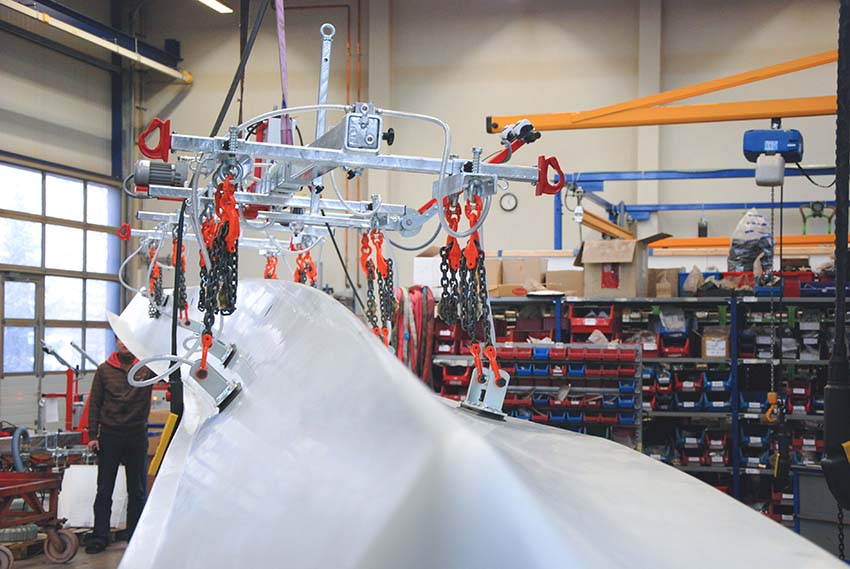
E.E: What are the most innovative products marketed?
AERO-LIFT: Our solutions are becoming more and more intelligent and diverse. Features for IoT can be integrated into the devices, that provide data on, for example, the loading and equipping of processing machines in the metal or wood sector. This data can be used by customers to increase efficiency in production processes and thus ensure higher output.
AERO-LIFT: AERO-LIFT: Like many other industries, we have been affected by the crisis caused by Covid-19. This meant that we had to adjust our annual targets. For many companies, the shock initially led to the decision not to invest in additional machines. Nevertheless, we see a big potential for the market. As already described, AERO-LIFT handling solutions are suitable for the design of hygiene-safe, healthy processes. We are therefore motivated to continue investing our energy in excellent, clever handling solutions for our customers. We look to the future with confidence.
AERO-LIFT Vakuumtechnik GmbH
Marleen Pauli
Adress: Turmstraße 1, 72351 Geislingen, Germany
Tel.: +49 7428 94 514 63