Aircrete Europe is the recognized global leading developer and manufacturer of Autoclaved Aerated Concrete (AAC) machinery and technology for the production of AAC panels and blocks with decades of experience and sales of over 100 different AAC plants in over 60 countries worldwide.
The company designs and delivers the most innovative turn-key AAC plants and cutting-edge plant technology around the world, our range of services include:
- Plant solutions
- Consulting & expertise
- Aftercare & maintenance
- Upgrades & modernizations
- Plant scans
https://www.aircrete.com/our-solutions/#plant-solutions
Interview with Wouter Ros, Technical Sales Manager at Aircrete Europe.
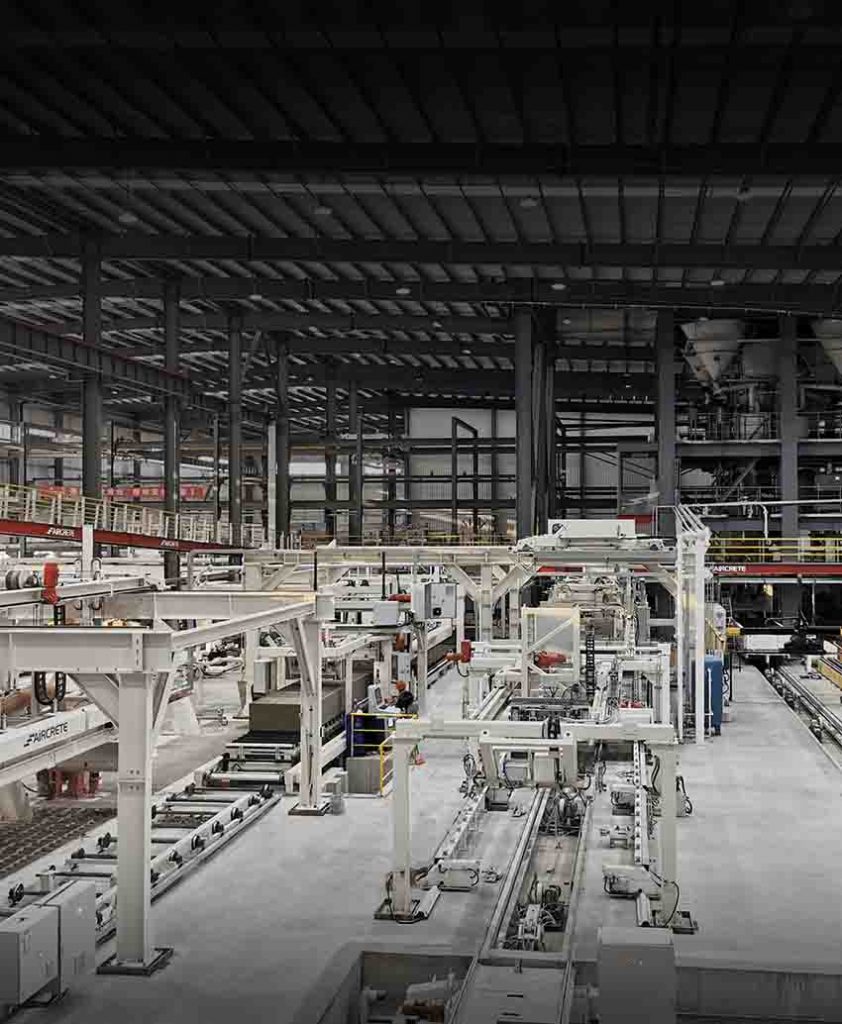
Easy Engineering: Which are the most innovative products / services and what special features do they have?
Wouter Ros: Our innovative services include: extending the level of automation in AAC plants, resulting in higher efficiency and lower labor costs; reuse of energy (by steam transfer throughout the autoclaves, condensate usage for preheating the boiler feedwater); reducing the overall utilities consumption, especially the gas consumption, which is becoming more and more important in today’s environment; reduction of the carbon footprint in cooperation with customers. Providing greener building technologies is incorporated in our values and our mission, so it is very important for us to be a technology partner in producing eco-friendly and sustainable building material.
E.E: How important is innovation in your field?
W.R: Innovation is crucial, as we need to be proactive, listen to the market, reply to the demand of a customer, taking in account laws, regulations, eco-policies, sustainability requirements, therefore constantly improving our equipment for production of AAC. We are also focusing more and more on panel production technology – the future of building construction, as it is faster, prefabricated, requires lower costs and fewer workers on site, allows for higher efficiency and longer lifecycle of buildings.
E.E: How do your products / solutions impact cost effectiveness for the users?
W.R: On the example of our most recent project, Aircrete Europe was engaged as a technology partner by Xella Netherlands (producer of Ytong brand) and helped impacting cost effectiveness for the customer by upgrading the first section of its cutting line with the new generation Aircrete Cross Cutter. This upgrade leads to the quality of the cut product increase, reduction of wire breakage (resulting in production interruptions, capacity loss and waste increase) and energy consumption reduction as well. By creating an inclined cross cut, the wires leave the cake at an angle, thereby minimizing the sling effect and damage to the cake caused by it, helping the optimal top crust removal process.

The installation was realized ahead of schedule, reducing the downtime from few weeks to 14 days.
https://www.aircrete.com/aircrete-news/xella-engages-aircrete-europe-to-improve-a-cutting-line/
Aircrete Europe features the latest innovative technology and solutions in the series of short technical videos on a monthly basis on the official YouTube channel, that includes the Inclined Cross Cutter, that can be viewed below:
E.E: What kind of work do users who use these products / services do?
W.R: Our customers are world’s largest producers of autoclaved aerated concrete (AAC) all around the world, specialists in high-quality building materials for residential, commercial and non-residential construction. Our clients are industry giants such as Xella, H+H, CRH, Holcim, Celco, Forterra, CSR Hebel, Kovalska, Aeroc, and others.
E.E: How do your products increase profitability for users?
W.R: We achieve that by increasing the capacity of plants and decreasing the operational costs, which really helps customers to move forward. We help our clients to optimize their process and recipes, allowing them to save on production costs and binder content as well.
E.E: How do your products / services differ from other types on the market?
W.R: Our UNIQUE FLAT-CAKE PRODUCTION TECHNOLOGY distinguishes us from our competitors, it is based on years of successful experience and innovations, allowing Aircrete plant owners to be pioneers in their respective markets.
Unique Flat Cake Cutting Technology
https://www.aircrete.com/unique-technology/#flat-cake-technology
Limited cake handling and double-wired cutting technology result in superior AAC products. Our technology allows for:
- Producing complex and thinner shapes and structures: reinforced panels of 40mm – 300mm thickness, up to 6m long as well as traditional blocks
- Minimum AAC cake handling (resulting in efficiency, less breakage, and minimum energy usage)
- Higher accuracy (<1mm tolerances)
- Superior SUPER SMOOTH product surfaces (that do not require plastering)

Some of our customers engage us to convert a tilt-cake technology operating plants into the flat-cake technology, as it is designed to produce both panels and blocks, allowing our clients to have wider product portfolio range.
E.E: How do your products help solve users’ problems?
W.R: One of the main goals of Aircrete Europe is to help AAC plants around the world run more efficiently, become more productive and improve their product quality.
We can answer this question by providing the following case study:
A large producer of concrete precast elements for road, electric and water infrastructure, as well as for building the commercial, logistic and production facilities in Romania engaged Aircrete to run a plant scan to address slurry density issues. Aircrete Plant Scan report recommended a load-cell based u-pipe system that would be integrated with the mixer control system. The u-pipes installed after plant scan are integrated with the mixer control system. As a result, three u-pipe systems were installed to measure the fresh slurry, the return slurry and the cutting-pit slurry respectively. The accuracy of the process has drastically improved through automation and the formula changes automatically depending on actual measurement results.
More case studies and information on Aircrete Plant Scan can be found here.
E.E: What products / solutions are you going to launch in the future?
W.R: We are currently integrating digitalization in AAC plants with Aircrete In Control 4.0 Solution: https://www.aircrete.com/aircrete-news/digitalization-in-aac-plants-with-aircrete-in-control-4-0-solution/
In the nearest future we will finalize commissioning of the brand-new factory in Uzbekistan. The Hybrid Plant combines equipment from Aircrete Europe and Aircrete China, resulting in the best investment.
Also, we are going to help our customer in Romania to increase profitability, product quality, capacity, reliability, safety and efficiency by converting an old AAC plant into the state-of-the-art modern facility.
https://www.aircrete.com/aircrete-news/export-finance-for-the-first-aircrete-project/
LinkedIn: https://www.linkedin.com/company/aircrete-europe/
Twitter: https://twitter.com/AircreteEurope
YouTube: https://www.youtube.com/c/AircreteEuropeOfficial