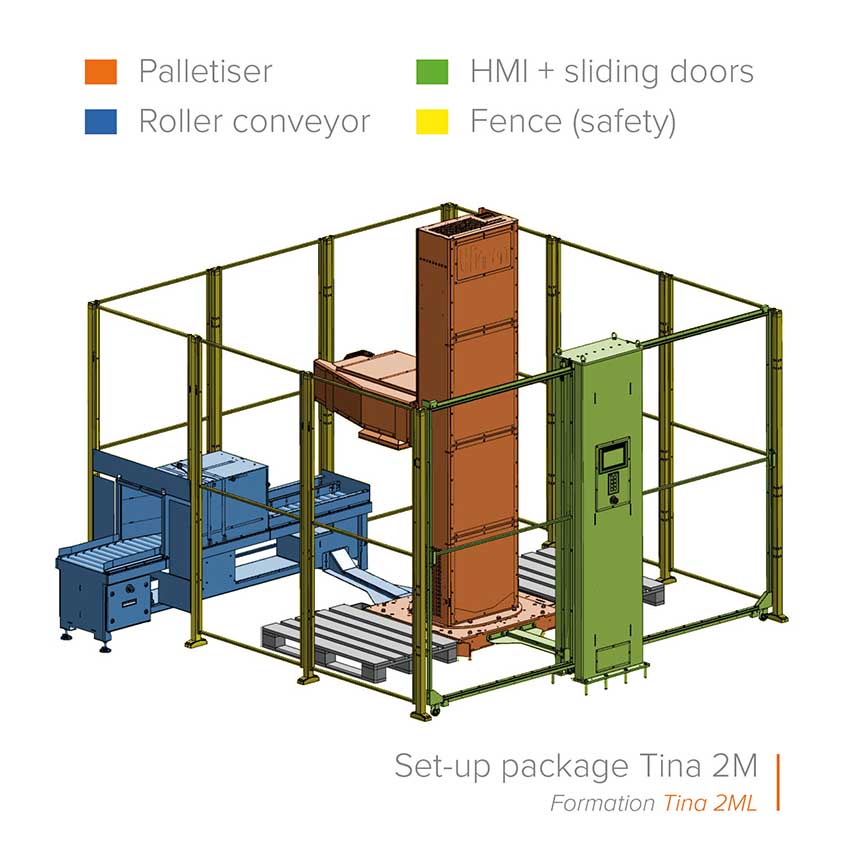
Alphatech Machinebouw stands for three generations of know-how, technical experience and wisdom passed on from father to son. Alphatech guarantees a personal and flexible approach typical for a family business in combination with the thorough knowledge of an experienced technical team.
Making machines is Alphatech’s business. Their employees are experts in the most diverse and innovative techniques. The customer can depend on a team that thinks along and cooperates; from the drawing process to the installation at the customers location. The goal? A unique, fully customized machine that meets all requirements and expectations. A machine built for life!
Interview with Charlotte Lammertyn, Marketing & Graphic Design at Alphatech Machinebouw.
Easy Engineering: What’s the news about new products?
Charlotte Lammertyn: Alphatech’s mechanical engineering is up to its 3rd generation palletiser but the basic innovation was present from model 1 and still remains unique.
The mono – column palletiser Tina has its fully electric cabinet and electric drive on board. This is not only compact, but also ensures the least wear and tear and failures. The palletizer only needs a power supply and a control cable. These connections are immediately contained in a rotating coupling in the base, allowing the palletiser to rotate endlessly. No extra control box, no long control cables that have to make a rotating movement.
Compact, efficient, robust.
E.E: What are the ranges of products?
C.L: In the range of our palletisers we have 3 set-up packages.
- An entry model with manual pallet change (Tina 2ML)
- A fully automatic machine with automatic pallet change (Tina 1A)
- Components for a tailor-made construction kit (modular)
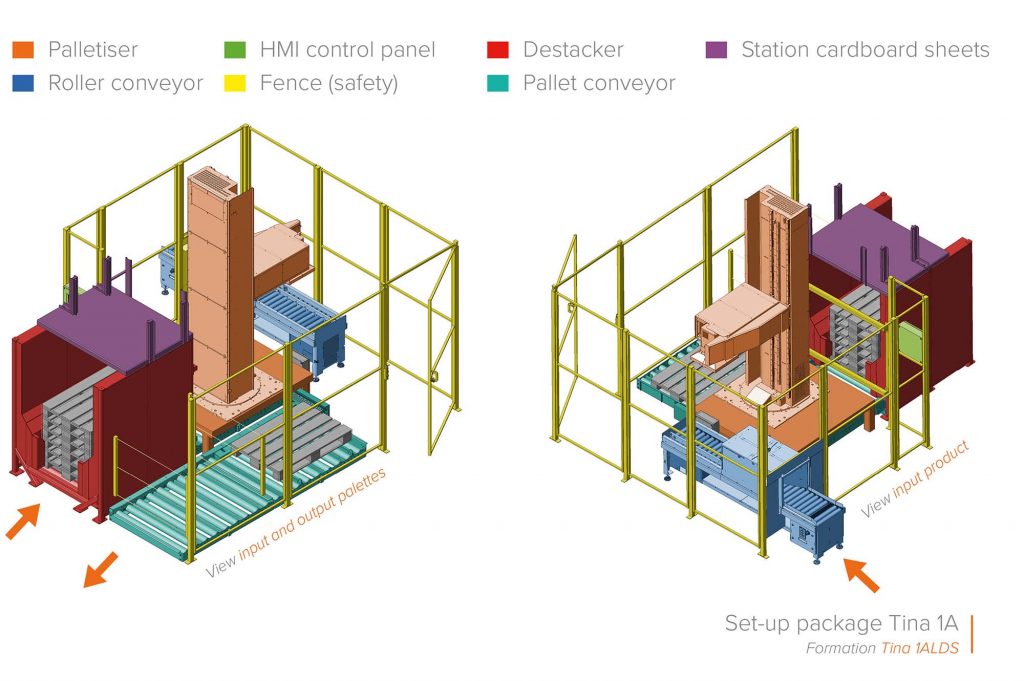
E.E: What can you tell us about market trends?
C.L: Several companies are stepping forward and reaping the benefits of the robotic palletizing system. These standalone machines help keep end goods on pallets for further replenishment or storage. Robots are affordable; even small businesses are seeing the need for palletizers, box erectors, box fillers, carton sealers and other automated packaging equipment. In addition, the demand for healthier and safer working conditions for employees, greater production volume and quality, more flexible production process and space savings is higher. With the growth of virus outbreaks, it is abundantly clear that now is the time to invest in packaging automation.
The food and beverage industry in particular has continually made a significant contribution to increasing the revenue of palletisers.
As competition among distributors continues to increase and government regulations become more stringent, retail demands continue to grow. Thus, the need for palletizing robots has never been greater than it is today in the food and beverage industry.
Compactness is also a very important parameter in customer selection. It is rare that there is space left in a production environment.
The palletizing market is taking into account all the trends and innovations that are taking place worldwide. For example, with the food processing industry implementing selective assembly robots and the manufacturing industry contributing to the decrease in energy costs, it can be concluded that the market is ready for advances in packaging machines in the near future.

E.E: What are the most innovative products marketed?
C.L: Quick-change system for the gripper
The quick-change system consists of 2 components. One component is mounted on the palletizer (on the rotating coupling) and the other component is fixed to the gripper. Together, this assembly forms the quick-change system for grippers.
On the gripper attachment (component on the palletiser) there is a shaft on the left and the side, which makes it possible to mount the gripper on the palletiser.
Because of these 2 connections shafts, the 2 components are always mounted nicely straight to each other. The extra bolts that connect them make sure that there is no chance of incorrect assembly.
The connection between the two components also ensures that 12 signals can be transmitted (depending on the number of movements or detection) This happens through the connection of the gripper with the palletizer true the plug that is provided herein. If more than 12 signals are required, the profinet connection is used.
For changing the gripper, a gripper cart is used. The gripper is bolted to the cart. This is also equipped with springy wheels so that when the gripper is grabbed on the cart, the undercarriage will spring along nicely.
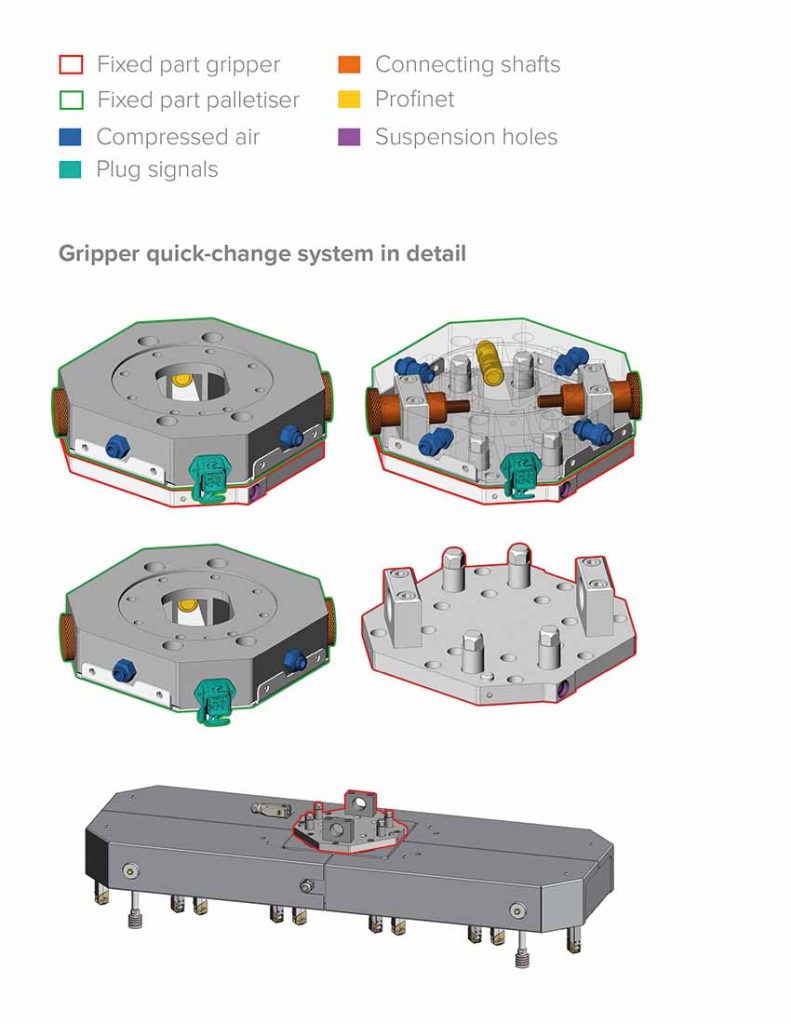
E.E: What estimations do you have for 2022?
C.L: Before 2022 we expect to make contact with the first dealers in Europe.
With our participation at Logimat, we have taken the first steps in our search for partners for the coming years. From 2023 onwards, the first collaborations should start and afterwards the distributor network should be further developed.