Easy Engineering: A brief description of the company and its activities.
BERCELLA: Bercella’s core is first and foremost represented by designing and producing products with Composite Materials, mostly Carbon Fiber, and Fiberglass, but also Kevlar, PrePregs and Honeycomb, just to name a few. Composites manufacturing represents our origins and what we have been doing for the past 25 years.
Furthermore, Bercella vertically integrated several processes such as Autoclave, Filament Winding, Compression Moulding, CNC machining, Painting and, most of all, the Designing, to drastically reduce the time-to-market for our customers.
Up to 2013 we refined and consolidated our deep knowledge of the industrialization process thanks to the countless projects we had acquired until then. Starting then, we matched industrialization with high-end Structural Design to offer a more textured service from the very beginning. In this way our clients can rely on a single company for both study and production of the components, reducing risks, lead-time, and costs.
Our offer became even more integrated in 2018, when we decided to add a Material Testing Lab to our facilities, that now allows us to drastically reduce costs and time, always in the direction for the clients to reduce the risks connected to managing multiple suppliers.
Our activity includes Design and Engineering, and Advanced Manufacturing techniques. The first one for us means advanced designing softwares and performing engineering tools, driven by a deep knowledge and by the capability to listen to the client and understand its needs, supporting it from the beginning until the end. In fact, being a one-stop-shop, allows us to accompany our customer throughout every single phase of the project.
On the other hand, our Advanced Manufacturing processes aim to reduce the delivery time while increasing quality and keeping the budget on track. We are able to achieve this results thanks to the abovementioned integration.
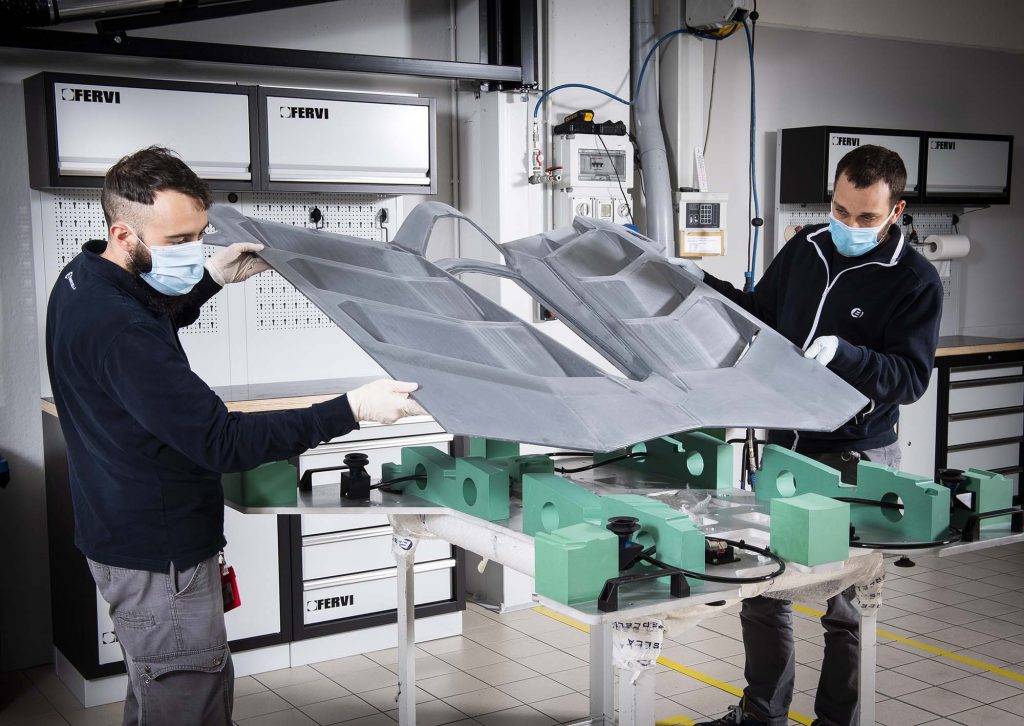
E.E: What are the main areas of activity of the company?
BERCELLA: Bercella is mainly active in the following three business sectors: Automotive, Space and Defense.
Automotive and Racing are at home in the italian Motor Valley (the aemilian territory where we are based). Up to now we count over 1.000 monocoques produced over 25 years for more than 20 championships from F2 to F3, from Indycar to Le Mans. Furthermore, we produced more than 100.000 bodywork and automotive parts, becoming one of the most prominent players worldwide.
Space is the most challenging environment we had the chance and the capabilities to manufacture products for. Every rocket component has to respect incredibly strict protocols and tolerances, and even the environment in which they are produced is completely exclusive for that kind of projects. Bercella counts two Clean Rooms, where temperature and everything else is kept under control to guarantee high production standards that match the space agency’s requirements. Our client’s portfolio goes from the main Governmental Agencies (ESA, ASI) to Large Systems Integrators (Airbus, Thales-Alenia Space Italy, OHB Italy), and many New Space Economy start-ups (Sitael, D-Orbit, GOM Space). What they all have in common is the will to rely on an accountable partner with structured multi-disciplinary teams and state-of-the-art technologies, that grants them the necessary support to successfully finalize their projects.
Defense is a critical sector for us too, because it involves constant dedication, confidentiality and responsibility, that have to be guaranteed for every project and application. Bercella mainly manufactures large radar and radomes with Glass, Kevlar or Quartz, that translates into high-end electromagnetic performances. We are registered on the National Register of Companies, we work under TULPS License and Export Licence for Italian and International clients that choose us as a competent, cooperative, reliable and private partner for their mission-critical equipment.
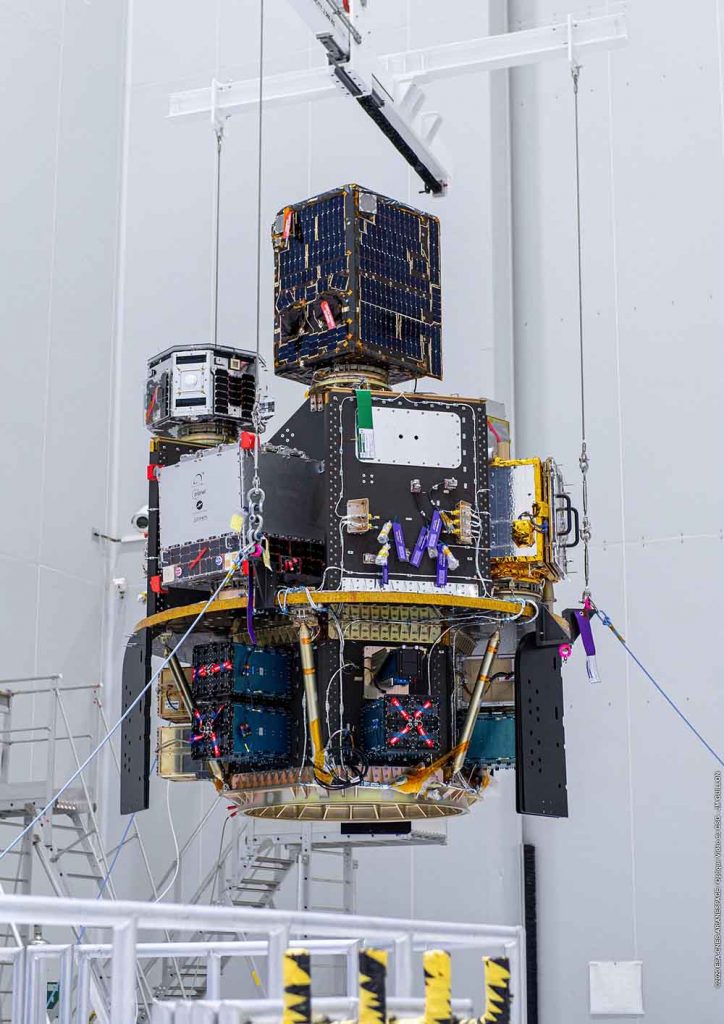
E.E: What’s the news for 2021 about new products?
BERCELLA: Despite of the pandemic, we are glad that 2021 has turned into a year full of projects and new business opportunities for us.
In the Racing industry, we manufactured the carbon fiber bodywork and the FIA approved FIAS and RIAS (Front and Rear Impact Absorbing Structures), for Romeo Ferraris’ Giulia ETCR and for Glickenhaus’ SCG 007 Le Mans Hypercar. It is important to say that these components are crucial for the driver’s safety, and carbon fiber has undoubtedly the best characteristics to fit these needs, since it is light and resistant at the same time.
As for the Space industry, we played an important part in the ESA Vega VV16 and ESA Vega C missions, manufacturing the payload hexagon’s sandwich panels and the monolithic main deck, a huge component manufactured thanks to our biggest autoclave (4000mm in diameter and 6000mm length) that improves overall stiffness, structural continuity and lightness because there are no junctions nor welding.
E.E: What are the ranges of products?
BERCELLA: Well, I would say we are a technology provider that can support products producers by applying 25 years of experience and up-to-date plants for developing and producing a wide range of products.
In the Motorsport industry we are a global leader for Chassis and Monocoques for Racecars such as F2, Indycar, Formula E, LMP/LMH. So far, we produced over 1.000 monocoques and almost a million bodywork product such as bumpers, fenders, wings, bonnets, etc.
In the Space industry we develop both Satellite and Launchers structures, mainly made of sandwich panels, and Solar Array Substrates. If you imagine a typical Satellite picture, we build both the central box and the 2 long wings over which our customers install the Solar Cells for powering the satellite.
The Defence industry is mainly related to the design and production of Antennas, Radomes, and Reflectors. The interesting feature here is that we can build large single-piece Reflectors and Radomes thanks to our huge autoclave!

E.E: At what stage is the market where you are currently active?
BERCELLA: We are an established and growing company, well positioned in the Italian market and currently trying to grow internationally. COVID-19 represented a tough challenge on this point of view, but we’re seeing the market recovering faster than expected.
E.E: What can you tell us about market trends?
BERCELLA: The Composites industry is definitely booming in the last years, and the best is yet to come thanks to the electrification of both Automobiles and Planes! The EU legislators are pushing to reduce emissions and consumption, that requires lighter vehicles: Carbon Fiber is the only way to reach that! We’re seeing tens of project starting now that will be on the market in the next 3-5 years that will have a huge application of Carbon Fiber products, and this will lead to some technological leaps that will influence our industry sensibly.
E.E: What are the most innovative products marketed?
BERCELLA: Bercella is strongly committed to innovation and sustainability. In particular, this year we focused a lot on natural fiber based composite materials and bioresins, and we developed two very interesting products.
Bercella engineered a flax fiber seat for Formula SAE (a university championship for single-seaters) and a flax fiber demonstrative front bump for the Giulia ETCR.
We are particularly proud of them because we recognize that sustainability is playing a growing and growing part in our lives, and we have to keep up with it. Moreover, even if carbon fiber’s performances are still unmatched, flax fiber shows good physical and mechanical features too.

E.E: What estimations do you have for 2021?
BERCELLA: We expect 2022 to be the year in which the industry will return to pre-pandemic levels , while 2021 will be a transition year as the COVID-19 pandemic is still affecting all industries, posing great challenges on getting raw materials (resins, solvents, etc.) and limiting possibilities to reach new customers/markets.