“We give machines the sense of touch”. Bota Systems’ vision is for robots to work and move safely and as naturally and freely as humans. As a developer and manufacturer of multi-axis force-torque sensors, torque sensors, and custom sensors, the company is diligent about providing the best force-torque sensing solutions and user care experience.
Interview with Klajd Lika, CEO of Bota Systems.
Easy Engineering: What are the main areas of activity of the company?
Klajd Lika: Our team of accomplished robotic, software and mechanical engineers continually develops highly integrated and advanced sensors to support a wide range of applications. Whether used for research or industry, we aim to streamline the process.
E.E: What’s the news about new products?
K.L: We have just launched our newest and so far, smallest sensor on the market.
The MiniONE Pro 6-axis Force Torque sensor is an extremely sensitive and compact force-torque sensor developed to enhance micro-robotic systems with haptic feedback.
The compact housing includes embedded electronics, 6 DoF IMU, temperature sensors, and software integration with TwinCAT, ROS, LabVIEW and MATLAB®.
The MiniONE sensor comes in four variations with two connector configurations and two communication options.

E.E: What are the ranges of products?
K.L: Sanding & Polishing
Finishing applications like sanding or polishing are some of the dirtiest and most exhausting tasks in manufacturing. By using force torque sensors and direct force control, it is possible to easily automate this challenging processes. The sensor feedback gives you the flexibility and adaptiveness required even for complex shapes and enables a consistently high surface quality.
Assembly
Sensorized robots can perform assembly processes in a repeatable way even with tight tolerances. By using force feedback during the insertion, it is possible to increase flexibility, reliability, and robustness during this task. The insertion can be done with just the right amount of force, preventing to damage parts and ensure less downtime in your production line.
Hand Guidance & Teach-in
Programming a robot can be time-consuming and complex. Enable more flexibility in your production by integrating an intuitive and easy way to record waypoints and teach positions. This allows to reduce programming effort and enables to even automate tasks with only a few repetition cycles. Make your robot safe and collaborative with high accuracy and reliability by adding a force torque sensor at the wrist.

Telemanipulation & Rehabilitation Devices
Medical robots and rehabilitation devices have the highest requirements in force-torque sensors. The sensors need a high signal bandwidth while being accurate and sensitive to enable high-fidelity force rendering at the robot itself or at a remote device. Compact and lightweight sensors are needed that can be directly integrated into the structure. We can also provide custom solutions for your application, contact us!
Further applications will be developed soon. As we have the know-how of robotic engineering in-house, we are able to customize any demands by clients and program-specific applications for them.
E.E: At what stage is the market where you are currently active?
K.L: The automation market is reaching a new level where robots are becoming more sensitive and, above all, more autonomous. They are also learning faster and artificial intelligence is becoming more and more important, which significantly increases the range of applications for robots.
E.E: What can you tell us about market trends?
K.L: In the process of automation in all areas, i.e. not only in industrial production but also in the medical and service sectors, there is a large market for force sensors in the robotics area. this market is growing daily in parallel with the expanded possibilities of robots today and in the future.
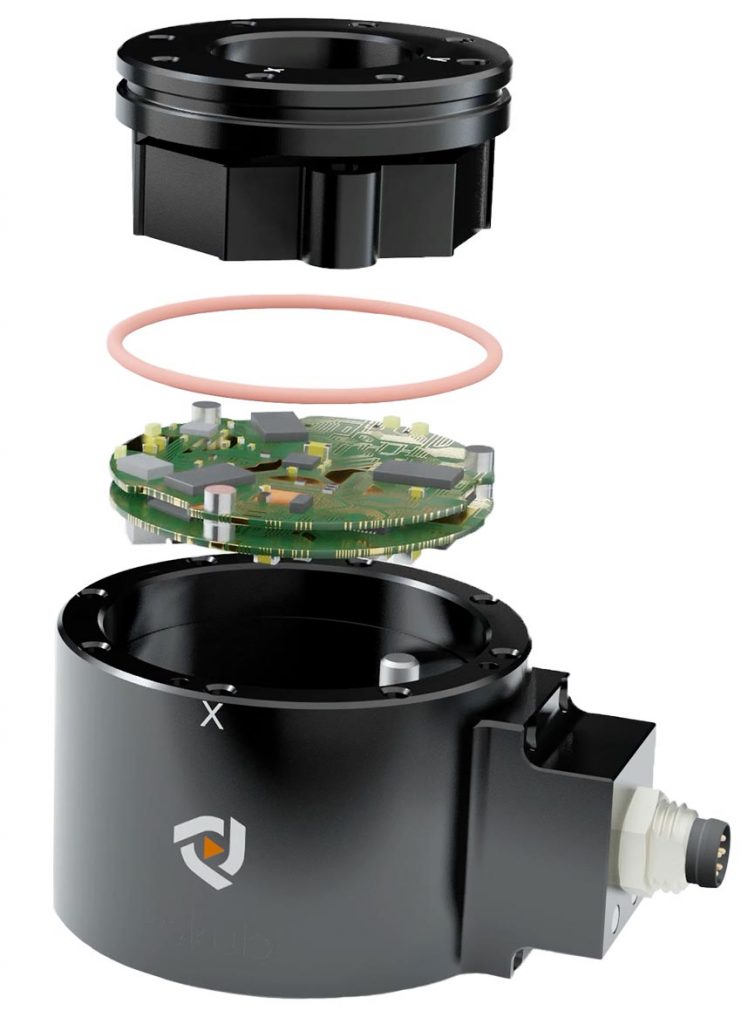
E.E: What are the most innovative products marketed?
K.L: In our industry, the most innovative products are those robots that, thanks to sensitive feedback in use (through our digital 6-axis force sensors, for example), can perform repetitive complex operations autonomously, leaving humans to take care of more high-level work/activities during this time.
E.E: What estimations do you have for 2023?
K.L: We have already successfully sold sensors and applications worldwide in the development and research field, this year we are now striving to gain partners in the industrial environment in robot production, who use our sensors in series and in larger quantities in their production of robots.