Castellanos y Echevarría – Vitoria, S.A. (CEVISA) designs and manufactures self-feed bevellers for plates and tubes, mainly used in steel working industries and welding activities. As a pioneer in automated bevellers, CEVISA succeeds in manufacturing high performance beveling machines, reliable and fast to optimize production times and costs. We work tirelessly to develop innovative bevellers to meet requirements for the most demanding sectors.
Their priority is to offer the customers efficiency in their productive processes meeting all their requirements. In order to fulfil this promise, CEVISA manufactures and supplies automated bevellers with mechanical chamfering with welding edge milling and chamfering machines with roller shears that enhance productivity, flexibility and profitability saving time and cost reducing almost 90% welding preparation time!
Easy Engineering: How do these products / services differ from other types on the market?
CEVISA: The most important point is that we are real manufacturer and we do the entire production of the machines and cutting tools by our own and we do so with an experience of more than 50 years. We are not a simple assembler. So, we were the pioneers in creating and manufacturing high performance bevelling machines and we are able to guarantee our clients reliable and tested plate bevelling machines. As manufacturer we are also able to provide customized solutions for customer’s needs. Proof of our quality is that we have been tried to be copied many times, but there is only one original. We offer reliable, robust and durable machines for the metal sector, so it’s common to find CEVISA machines working with over 30 years.
The key points of our devices: Self-feed, fastest system: 2 m/min for plates and tubes and high bevel accuracy.
Easy to use: no special training needs, only one worker for several machines.
Plate thick from 3 mm to 100 mm -> No deformation nor steel properties changes, neither material heating.
Only bevelling machine solution which provides bevel length up to 60mm also in resistant materials as Hardox or Duplex.
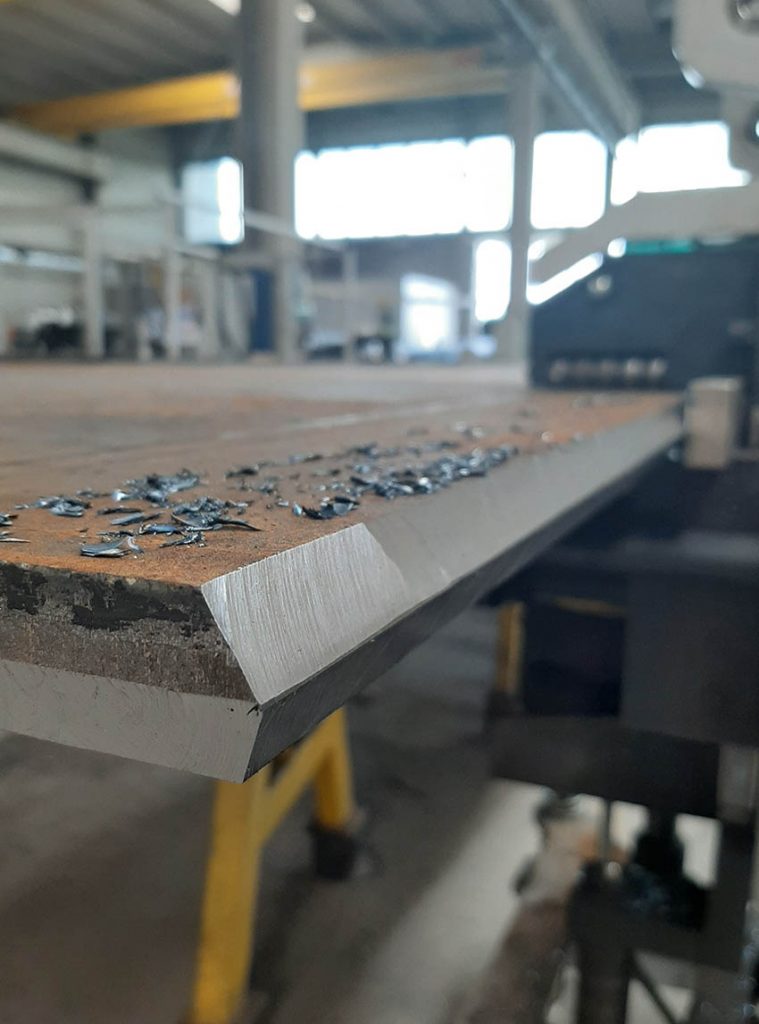
E.E: What customer profiles are you targeting?
CEVISA: We provide solutions for the metal industry and cover this sectors: Civil engineering structures and offshore, industrial boilermaking, maintenance and welding, petrochemistry and nuclear, raw materials, sea and defense, site equipment & large machines, tanks and high pressure vessels, transport and hoisting cranes, wind and thermal energies.
We are learning from our customers, so not everything is welding preparation. Recently we provided also solutions in ramp, excavator buckets and plow blades production.
We are facing that more and more steel producers are requested to provide premium services including the bevelling of their steel plates and tubes.
E.E: What kind of work do users who use these products / services do?
CEVISA: Big companies have special so called bevellers, but the work could be also done by welders or even untrained operators, as the machines are really easy to use. No special training is required.
E.E: How do your products / services improve user work?
CEVISA: Edge milling machines CHP 60G and CHP 60G INV
Mobile bevelling milling machines are increasingly replacing the classic procedures for preparing weld seams, such as roller shears, burning and manually angle grinders. Modern, powerful machines not only ensure greater efficiency, they also impress with their high surface quality. The machine moves to the metal plates or work fix with smaller pieces, so its use is very flexible.
Recently we launched a new machine the CHP 60G INV for lower bevels as it has been in high demand among our customers, since between the two milling machines they achieve a perfect symbiosis: working with the two sister machines allow bevels to be made in K and X without turning the sheets and doubling the production with a single operator. Some of our clients are delighted with the time savings and therefore in production costs of over 50%.
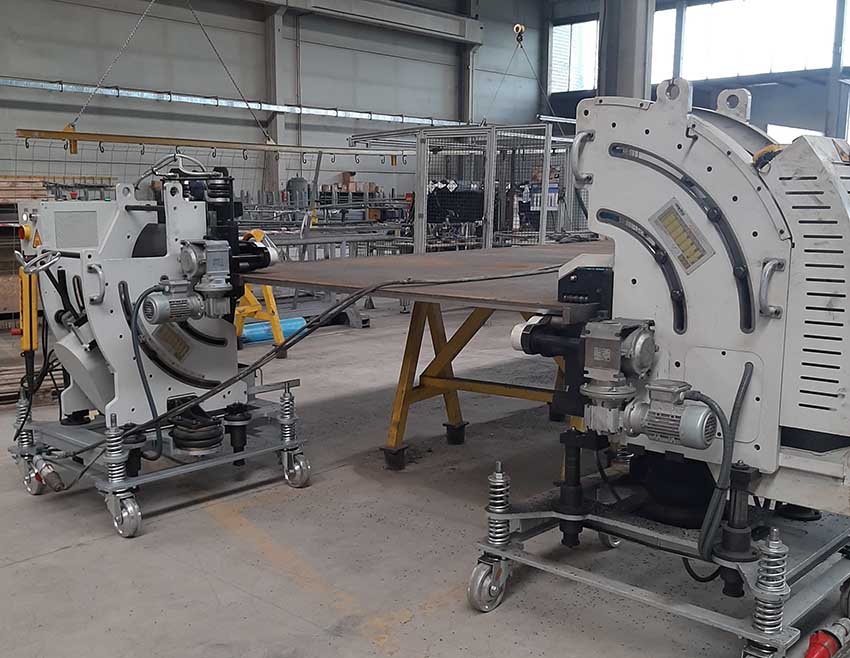
Edge processing with the shear method
The most efficient way of preparing weld seams is with the roller shear machines. These bevelling machines operate using the roller shear method. Here, a long chip is sheared off the sheet edge by means of a slowly rotating cutting wheel or shear wheel. This enables speeds of up to 3 m / min (up to 5 times faster than conventional methods). The costs for the meter chamfer are up to 75% lower than with other processes! Without dust and without noise, since there are no milling chips and no grinding dust.

Advantages of self-feeded bevelling machines (milling and shearing):
- Cutting all conductive materials;
- Cutting thicknesses up to 100 mm;
- Cutting high-alloy steels;
- Low noise;
- High profitability;
- Optimal use of materials;
- Narrow kerf width;
- No thermal stress;
- Cutting thick material;
- Safer for users and the environment;
- No post-processing required;
- Low operating costs;
- High cutting speed;
- Short set-up times;
- No specialized staff required;
- Without large part restrictions.
E.E: What innovative features do the products / services have?
CEVISA: As mentioned before the last launched machine was the CHP 60G INV for lower bevels.
The technical details are as follows:
- •For plate thicknesses from 10 mm to 100 mm *;
- •60 mm chamfer length;
- •Milling finish;
- •Advance and r.p.m. adjustable according to material needs;
- •4 bar pneumatic fixing system;
- •uniform finish, vibration-free and low-noise;
- •Mobile and fix;
- •Adjustable working height with pneumatic lifting system;
- •Maximum bevel in one pass 28 mm;
- •Recommended maximum bevel in several passes: 60 mm;
- •Variable angle from 15º-70º.
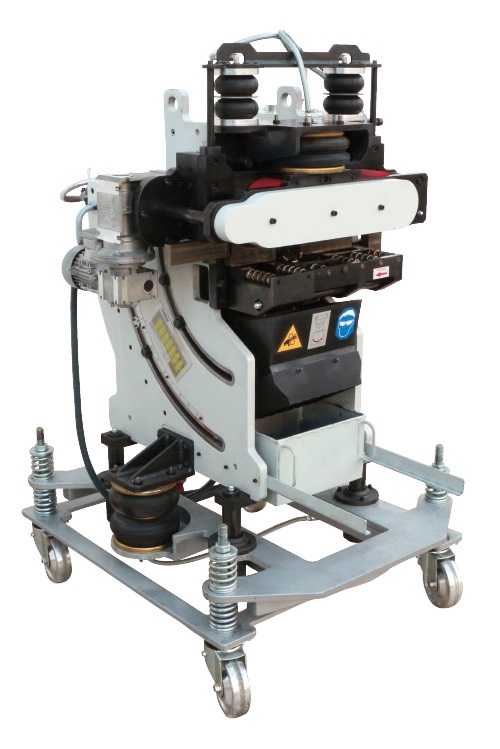
Further, we developed a special device for our CHP 60 G J-Bevels. In view of the growing demand for a solution for the finishing of J-chamfers, the technical team from Castellanos y Echevarría – Vitoria, S.A. got to work. The device is already a reality and tests with the specific requirements of a customer have been successfully completed with a prototype.
The chamfer radius only is applied in J-chamfer or U-chamfer welds. A configuration of a J-bevel or U-bevel weld is usually indicated by a bevel angle and a bevel radius. The CEVISA device offers a constant and unchangeable radius of 8 mm.
The welding designer can choose the one that best suits his needs. Various connection geometries and weld seam types are available. The selection is usually based on considerations such as:
- Accessibility to the welded joint;
- Appropriateness for the design of the structure;
- welding costs.
E.E: What are the most common problems and how did you help solve them?
CEVISA: Poor weld edge preparation is the first and most fundamental cause of improper adjustments resulting in poor quality welds due to inaccurate V-joint preparations. Excessive welding, increased heat input and increased expenditure on consumables and personnel as well as additional hours are the consequences. All of these factors contribute to lower productivity with additional costs that harm today’s cost optimization requirements.
To ensure the best possible connection quality at the weld seam, oils, greases, varnishes, paints and oxide layers on parts to be welded must be removed so that the joint edges on which the work is carried out are metallically clean. When processing, you should also make sure that no oil-containing coolants and lubricants are used so that the preparatory work is not neglected. The mechanized weld preparation avoids this. With this procedure, we resign cooling water containing emulsions, which in most cases is used in the preparation of weld seams by manual methods or CNC milling machines, and instead mill, shear or grind the material completely dry.
If the aim is to make the chamfering process profitable, the decision to use the mechanical chamfering process is obvious. The mechanical processes are gentle on health, economical and handy. Various solutions can be offered for sheet thicknesses from 3 mm to 100 mm. The finishing is very different. Chamfering on chamfering machines with roller shears is very precise with regard to the angular accuracy, but has a rough surface, which is caused by the action of the cutting wheel. However, this corrugated pattern is irrelevant for the subsequent welding process, since the material is completely melted during welding.
If the final processing requirement is high, the welding edge milling machine is a very good alternative. Even very resistant metals such as Hardox and Duplex can be processed and chamfers up to 60mm can be created.
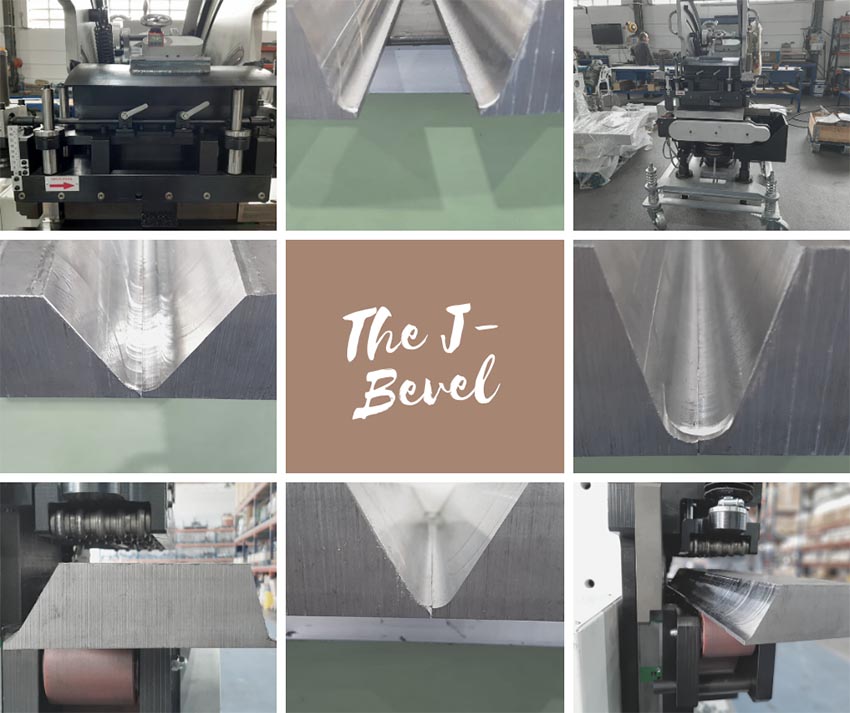
E.E: What products / solutions are you going to launch in the future?
CEVISA: Customers demand goes more and more towards a milling finish. Therefore, our development is working on a smaller solution in the bevelling milling machines. Coming soon, our CEVISA CHP 30G.
The idea is to have the same solution with the same principle, quality and performance but in a smaller size.
E.E: What are your estimations for the end of the year?
CEVISA: Pandemic did affect nearly every business in this world, so we are quite proud that our estimation is that our turnover will decrease 5% in relation with last year.
The real and only bad month was April due to general lockdowns and panic situation all over the world, after that, we experienced a constant recovery that ended with incredibly good months starting in September.