Clariter takes plastic waste nobody wants and transforms it into products everybody needs. Its mission is to enable “a clean slate” for the industry and partners.
Clariter’s innovative technology has provided a new alternative for plastic recycling and a large-scale solution for the world’s plastic waste problem. Its unique process transforms the majority of plastic waste streams into high-value, pure, ready-to-use industrial products: oils, waxes, and solvents that would be otherwise made from crude oil.
The formation of Clariter in 2003 was a result of many years of scientific research by Professor Andrzej Bylicki, a leading Polish scientist. Since then, Clariter’s team has been developing and perfecting the technology as well as achieving international recognition backed up with patents. Company’s innovative technology is proven through Research & Development Plant in Gliwice, Poland, operating since 2006, and a 15,000 m² Industrial-scale Plant in East London, South Africa, built in 2018. Its offices are based in Israel, Poland, Luxembourg, and the Netherlands.
Easy Engineering: What are the main areas of activity of the company?
CLARITER: Clariter is active in what can be seen as the next generation in the chemical recycling (upcycling) space. A unique technology where the majority of plastic waste streams are chemically transformed into new pure crude oil-free products. Clariter’s patented continuous process consists of 3-stages. The first step, thermal cracking, then hydro-refining, which removes all double bonds to leave them with a sulphur-free, odourless, highly pure material which they then, in the final phase of distillation and purification, transform into three product families: aliphatic solvents, white mineral oils, and paraffinic snow-white waxes. These products are a global first.
Clariter ends the life of plastic. It produces advanced, high-value products made of 100% plastic waste that are greener, cleaner and offer industry sustainable ingredients to manufacture consumer end-products without having to change formulations.
E.E: What’s the news for 2021 about new products?
CLARITER: Clariter’s oils solvents and waxes are green alternatives to crude-oil made petrochemicals. Revolutionalizing how the industry operates, the company is constantly engaged in negotiations with several partners globally. Their product range will not change. However, the amount of its applications is continuously growing.
Clariter’s oils, waxes and solvents are used as ingredients in a multitude of sustainable consumer end-products that clean the planet and create profitable business opportunities. Its established partnerships cover diverse parts of the industry.

E.E: What are the ranges of products?
CLARITER: While the industry is turning plastic into other forms of plastic, fuels or intermediates requiring further processing and blending, Clariter transforms plastic waste into ready-to-use, pure oils, waxes, and solvents. These are then used as drop-in ingredients in a multitude of consumer end-products, e.g. paints, coatings, leather, wood care articles and even cosmetics. This method ends the life of plastic and creates a clean world with clean products free of crude or fossil resources.
Clariter technology is exceptional for its ability to accept various plastic waste streams, the most problematic ones and those with the lowest value, which cannot be recycled otherwise. Some of the materials they have already successfully upcycled include marine plastic waste (e.g. fishnets and ropes), BOPP laminates, and materials made from ultra-high molecular weight polymers used for bulletproof vests and helmets. These are raw materials that cannot be mechanically recycled due to their structure. Moreover, since they are relatively small in the overall stream of used plastics, little attention is being paid to their processing – they are incinerated or landfilled and so sadly ending in the oceans.
E.E: At what stage is the market where you are currently active?
CLARITER: Clariter plants in Poland and South Africa have been operating for research & development and business purposes. Their current focus is to expand their partners’ portfolio and continue expanding the range of applications. Since 2020, roll-out plans for three full-scale Clariter facilities across Europe and the Middle East has begun. Together, these will transform 180,000 tons of plastic waste and produce over 150,000 tons of pure, clean, high-value products annually.
E.E: What can you tell us about market trends?
CLARITER: As we are being confronted with the painful impact of our consumer society on the planet, attention for a circular economy gained tremendous momentum. Big brands, start-ups (such as Clariter), governments and scientific institutions are working together to find solutions to decrease the environmental pollution.
Since not all plastic waste can be processed mechanically, and this method also has its limitations, chemical recycling solutions such as Clariter’s upcycling technology are now in high demand.
One Clariter’s full-scale plant will upcycle 60,000 tons of plastic waste into 50,000 tons of clean products annually while being net carbon-negative – this represents one of the most promising green initiatives in Europe.
In addition to strengthening recycling efforts, the greening of the petrochemical industry is becoming increasingly essential to meet climate targets. Giant steps can be made in energy consumption and limiting fossil raw materials such as crude oil. Clariter’s breakthrough initiative builds a bridge between the world of recycling and that of the petrochemical industry by replacing crude oil with the use of plastic waste and thus saving significant amounts of CO₂. By combining the challenges of both worlds, the company creates excellent economic opportunities that are now supported by the European Green Deal and its “Fit for 55” implementation program.
E.E: What are the most innovative products marketed?
CLARITER: Clariter is plastic to products.
Clariter technology is exceptional for its ability to accept various plastic waste streams, the most problematic ones and those with the lowest value, which cannot be recycled otherwise. Typically, raw materials suitable for Clariter’s process are polyolefin (PE and PP) films, containers (e.g. non-transparent plastic bottles) and post-production plastic waste (e.g. from plastic moulding plants). In addition to these, we are also able to use all kinds of polyethylene (LDPE, LLDPE, and HDPE) or polypropylene (PP, BOPP). Furthermore, the Clariter process can convert limited amounts of polystyrene (PS). Raw materials are accepted in a single feeding stream, and this means that there is no need to sort plastic waste by its colour (natural/other colours), or polymer categories (PE/PS/PP). The beauty of the wide variety of plastic waste that Clariter uses as raw material is, that it can be sourced locally, ensuring a cleaner environment within the perimeter of a Clariter facility.
The significant advantage of Clariter’s process compared to other chemical recyclers is that they create high-value final products in a continuous process in one plant without additional petrochemical processes. Clariter creates green products directly from 100% recycled plastic waste feedstock and not from crude oil.
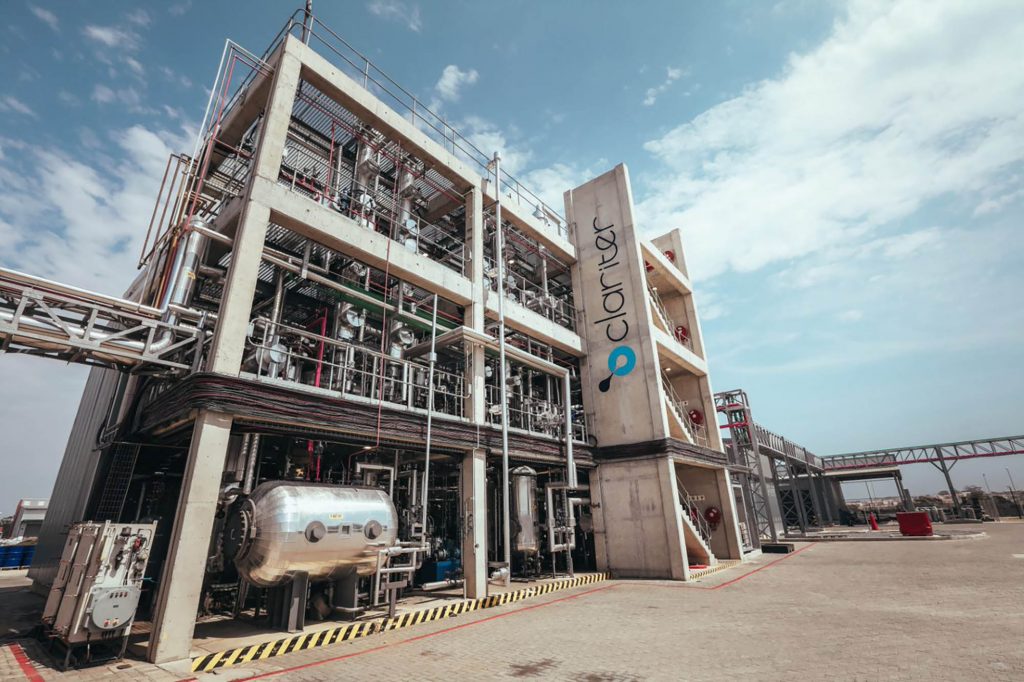
Furthermore, Clariter is unique by making sustainable crude oil-free products while producing net CO₂ savings. Its products are greener and cleaner, as they transform unwanted plastic waste streams, leaving a cleaner planet and providing a radical new paradigm shift in the industry. Clariter is not a typical recycler but rather an upcycler.
E.E: What estimations do you have for 2021?
CLARITER: Clariter is in the process of building 3 full-scale plants, each of which will recycle 60,000 tons of plastic waste and produce 50,000 tons of clean products annually. The countries of focus are Poland, Israel and the Netherlands.
As for the further looking plans, Clariter wants to continue working with strategic international partners and continue its global roll-out. By the end of 2028, their modest goal is to clear the earth of 2 million tons of plastic waste that ordinarily would have been landfilled, leaked, or burnt. Instead, they will upcycle it and produce 1.7 million tons of our pure products to sell to the industry. This not only reduces CO2 by more than 1 million tons, but it will also create numerous much needed new direct jobs.