Coldsense is a customer-focused, high-tech company with the mission to develop innovative, reliable, and robust system solutions to optimize technical equipment in cold and icing environments. The company is currently focusing on making new and existing cold storage in the food industry and temperature-controlled logistics centers more energy efficient, safer, and environmentally friendly.
Coldsense combines door sensors, environmental sensors, and in-house developed ice sensors with supervised learning methods to control the defrosting of the cold room based on the actual operating condition. For the first time, their system solution enables automated monitoring of ice build-up directly at the evaporator of the refrigeration unit.
Interview with Juan Velandia, Cofounder of Coldsense.
Easy Engineering: What are the main areas of activity of the company?
Juan Velandia: Coldsense is active in several industries, from industrial refrigeration for the food, logistics, and pharma industry to renewable energies. All these branches have a common challenge to overcome: they have to deal with ice and need to be able to operate despite environmental harsh conditions.
Frost formation is inherent to all refrigeration systems. It is considered one of the major problems in the industrial refrigeration industry. Increased power consumption and reduced cooling capacity are some of the consequences of uncontrolled frost on heat exchangers. Current countermeasures include defrosting cycles. A common approach is to set these cycles using timers and define, before or during the installation, how many cycles per day need to be carried out to avoid frost formation. This setup is based on experience or measurements of temperatures, which can not accurately measure frost formation. Nevertheless, completely avoiding frost formation leads to excessive energy heating the cold room, which is, again, wasted energy, additional costs, and CO2 emission. This is the challenge we are currently addressing with our intelligent solutions.
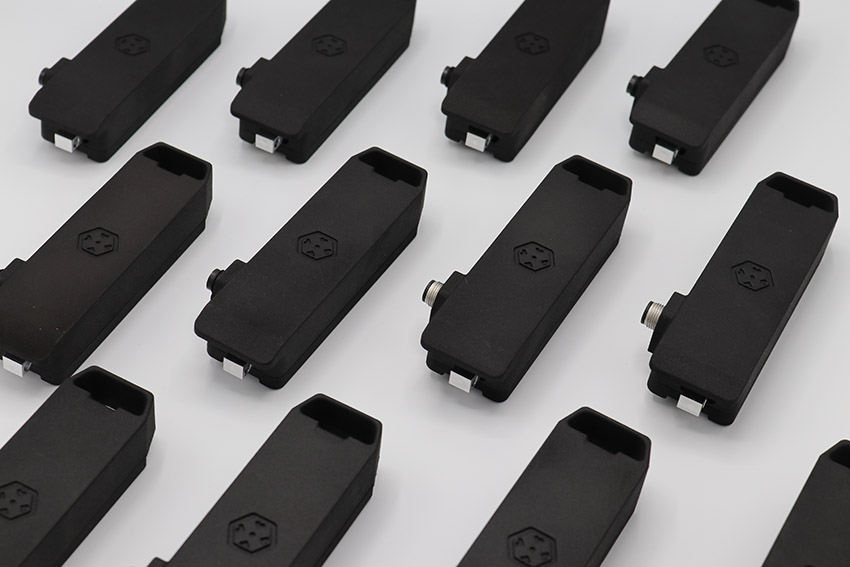
E.E: What’s the news about new products?
J.V: Conventional defrosting methods are based on indirect detection of ice, e.g. via temperature sensors. With our sensors, the measurement of the amount of ice directly at the evaporator of the refrigeration system is now possible for the first time. The sensors combine different measuring principles and build up a narrow electromagnetic field that changes even with minimal ice formation. This allows us to detect precisely the minimal amount of ice on the cooling unit, but also the exact point when the ice is melted. The start and the length of each defrosting process can be precisely controlled.
Complete monitoring of the rooms is possible by combining our sensors with door, temperature, and humidity sensors. Our system evaluates irregular incoming goods, moisture input, door movements, and other environmental factors to further optimize defrosting of the cold room. Using modern algorithms and artificial intelligence, we can set the best defrosting strategies for any cold room, tailor-made to the needs and constraints of our partners.
This means that defrosting only takes place when it is really necessary, allowing huge amounts of energy savings.
E.E: What are the ranges of products?
J.V: Our system solution is based on a combination of hardware and data-based services. The hardware includes all sensors and materials necessary for monitoring and intelligent control of the refrigeration system. The software includes the refinement, analysis and interpretation of the acquired sensor data.
Our technologies are suitable for refrigeration systems of any type – in any industrial context: from the food sector to low-temperature applications in the chemical and pharmaceutical sectors to climate chamber applications in the automotive industry. The measurement principle can be transferred to any application. We realize both the retrofitting of existing plants and the implementation on new plants. Our solutions can also improve the defrosting power consumption, using green energy from photovoltaics systems or other kinds of renewable power generation available at hour partners facility. The integration to a complete energy management system is desired and, in most cases, conducted by our team.
E.E: At what stage is the market where you are currently active?
J.V: Industrial refrigeration is a well-established market, which has been continuously growing in the last decades. The size of the market can be estimated using some figures: around 14% of the whole energy production in Germany is used for cooling. The demand for chilled and frozen goods has also increased in the last few years. Maintaining cold chains is a paramount need of different branches, from frozen food to pharmaceutical products. Refrigeration is a part of our society.
Being a market with such intense energy consumption, the current increase in energy prices affects all stakeholders.

E.E: What can you tell us about market trends?
J.V: The increased pressure on costs is a driving force for innovation in the refrigeration market. Solutions to reduce energy consumption, increase energy efficiency, and even reach independence from the electric grid are currently a trend in the market. Photovoltaic and heat recovery systems are taking a larger share of future investments in energy-intensive industries. Furthermore, the reduction of the CO2 footprint and more sustainable energy sources are also topics that are reaching end consumers and need to be considered by the branches we work with.
Our intelligent defrosting solutions are an active measure, which companies implement, to go a step forward in this direction. We are also currently supporting companies to design and implement complete energy management systems, which are aligned with the before mentioned objectives.
E.E: What are the most innovative products marketed?
J.V: In terms of energy management, innovative storage systems such as hydrogen or battery storage are starting to take a larger share of the market as innovative solutions.
In terms of controlling defrost procedures, some providers are working on control systems, trying to estimate the current frost state of the cooling unit. Their limitation relies on the impossibility to measure reliably and accurately the frost on the cooling unit.
Our solution stands also as the most innovative, because it exploits the benefits of Artificial Intelligence, such that the system learns how the facility operates and improves such operation. This is applied to both, energy fluxes management and controlling of defrosting procedures.
E.E: What estimations do you have for the rest of 2022?
J.V: 2022 was a great year for us, we have supported our partners to save around 90 MWh during the year. This way we avoided the emission of more than 35 tons of CO2 into the atmosphere. We also secured large projects, which will be implemented in the first months of 2023, which will increase our contribution to energy efficiency and CO2 footprint even more.