Delfin is a family-owned company based in Italy, established in 1991 by its founder and current chairman, Antonino Siclari. The company is a global leader in the manufacturing of industrial vacuum equipment, ranging from portable vacuums for industrial cleaning, to central vacuum systems and customized solutions, to pneumatic conveying systems.
Their mission is to create value by designing innovative solutions that improve efficiency, safety, and productivity. With this purpose in mind, they use their expertise to help customers achieving their goals and meeting their cleaning needs.
That’s why the R&D Department is always working on new projects, technologies, and applications, according to the market and customers’ expectations and needs. The year 2022 has been cutting-edge for the implementation of new projects and the development of new, vast solutions.
Interview with Riccardo Soffietti, R&D Manager at Delfin.
Easy Engineering: Can you tell us about the most relevant projects that had an impact on Delfin during the year 2022?
Riccardo Soffietti: During the year 2022, new thrilling projects have led to the engineering and realization of vacuum systems suitable for three different application fields:
- to vacuum dusts generated from floor preparation machinery;
- to match our products with capsule fillers in the pharmaceutical laboratories;
- to optimize industrial processes in the heavy industry to handle high quantities of products and cover long distances.

E.E: The solution for the building and construction industry
R.S: In the first field of application, the building and construction industry, we had to face three main challenges: the dimensions of the vacuum, its robustness and, above all else, the filter cleaning automation inside the vacuum. The models for use in this industry mainly vacuum dust from machinery that smooths the surfaces of construction sites. Consequently, our work was mainly based on the reduction of overall dimensions, so that the vacuum cleaner can be easily moved among the different areas of the construction plant or loaded on a small van for its transfer among different construction plants.
Moreover, in construction plants, vacuums frequently need to deal with bumps, recoils, and differences in heights. That’s why we have engineered solutions in total steel with suitable supports in those parts of the vacuums that, by our experience, incurred the most damage.
The continuous powering on and off and the large quantities of dust in the working environments pushed us to provide the printed circuit board assembly with sturdier components, making it far more long-lasting compared to other systems on the market.
Eventually, we have engineered a new filtration system that avoids the switching off the vacuum for cleaning operations and which doesn’t require compressed air. This system is made of two cartridges, specifically designed to maximize the filter surface, which are automatically cleaned by means of a steady vibration produced by two powerful magnets (selected after several tests), which remain activated during the entire vacuuming process.
The development of the Pharma range
For the second project, we have engineered a compact vacuum system for the removal of powders released from capsule fillers in the pharmaceutical sector. In this case, we had to face several challenges to develop the range at its best. However, the result was very satisfying: the use of AISI316 stainless steel for those parts getting in contact with the material to vacuum and the use of AISI304 stainless steel for the frame, allowed us to guarantee the highest surface finishing and the elimination of any sharp surface. The use of a highly performing cyclone allowed us to reduce the dimensions of the filters while guaranteeing total powder containment. Finally, the new system guarantees the complete isolation of operators that never get in contact with potentially toxic powders during the replacement of the filters.
We have overcome all the challenges on different levels: it all started with the meticulous design of the product to reduce both dimensions and welding as much as possible. Then, we have designed the cyclone, which is the core of the Dust Containment range, aiming at maximizing the filtration efficiency (later tested with several in-house tests). Finally, we have designed a compact filtration system protected by a containment bag which isolates the filter during its replacement. This way, the operator will be totally safe during the entire process. Once the design process was over, we focused on guaranteeing manufacturing quality checks, identifying the best suppliers to provide us with the necessary components and on careful quality checks from the production to the manufacturing and the final assembly.
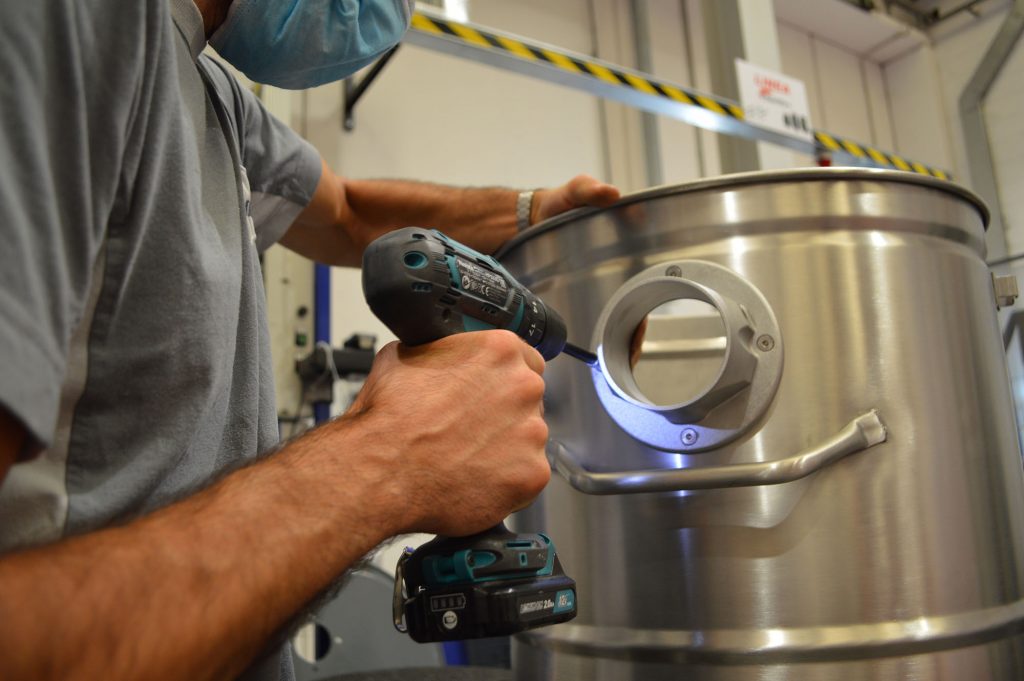
This product has been launched a few months ago and it has already been purchased by several customers who chose Delfin solutions for the quality of the finished products and for the skills we proved to have in meeting their needs, even by customizing the standard product. For example, we have designed a tailor-made solution for a customer of ours by adding the required sensors, thus creating an electrical panel able to manage different vacuum systems simultaneously and to dialogue with the electrical panel at the same time.
The challenges of heavy industry
The last project was related to the heavy industry (including cement factories, steel plants and foundries). The challenge here was to set up a system made of two high central vacuums for the collection of large quantities of dust over very long distances. The R&D department was challenged to design a tailor-made solution because the list price did not include standard pre-separators able to filter the quantity of air generated by the two systems. The new model needed to meet some requirements: big size, resistant up to 0,85 bar of vacuum, easy to disassemble for transport. Once more, we started with a meticulous phase of design and test of the resistance to vacuum. The entire structure has been split into different sections to allow their transport in containers. Eventually, the department studied a way to ease the replacement of the filter sleeves inside the pre-separator. Once this phase was over, we asked the supplier to verify the assembly of the different stages of the structures and then planned periodic inspections to check the quality of the product in use. Once more, the customer chose Delfin for our quality and the ability to adapt our products to a specific need.