EconCore, based in Leuven, Belgium, provides technology for the continuous production of honeycomb sandwich materials. The unique ability to produce rigid but lightweight panels within a cost-efficient, integrated high-volume production process is licensed by several companies over the world. The fast, versatile, continuous thermoplastic honeycomb production process allows users to produce sandwich materials for various applications including automotive, transportation, building and construction, industrial packaging/graphical displays, furniture and many others at minimal cost, weight and environmental impact.
Easy Engineering: What are the main areas of activity of the company?
ECONCORE: The EconCore technologies for automated continuous production thermoplastic honeycombs (ThermHex) are protected by granted patents. For specific application areas and material combinations we offer licences for our technology.
The applications for the EconCore technology based sandwich panels range from industrial packaging, automotive, B&C through transportation.
Furthermore, EconCore’s daugher site ThermHex Waben GmbH is a leading producer of PP honeycomb core for composite applications.
E.E: What’s the news for 2021 about new products?
ECONCORE: EconCore decided to invest into a new industrial line for large scale development and production of recycled PET honeycombs and HPT honeycombs. The company has further developed the production technology to make honeycomb materials from recycled PET waste streams and made progress in the next generation of high-performance thermoplastic (HPT) honeycomb materials. These developments started as a result of a pull from the market demanding more sustainable materials and the shift to focus towards thermoplastic solutions with high end applications for the aerospace and automotive markets. The cost-efficient and continuous production of sandwich panels based on the thermoplastic honeycomb technology, is well established within the production facilities of several EconCore customers worldwide.
ThermHex Waben GmbH, EconCore’s daughter company, is currently the leader of PP honeycomb core production thanks to its innovative solutions and patents licensed from EconCore. The success of the patented production technology was therefore taken as a baseline to further enhance the development towards the next generation of the ThermHex process, which can convert recycled and engineered polymers into RPET and HPT honeycomb cores and panels.

E.E: What are the ranges of products?
ECONCORE: PP honeycomb core and honeycomb panels with such core and PP skins are standard and most popular products of the technology.
With the RPET honeycomb core, EconCore sees opportunities in many applications such as the cost sensitive automotive market. Also, other markets have interesting applications where this material can be an excellent fit. The use of RPET honeycomb cores gives a sustainable solution with a good Life Cycle Assessment and low carbon footprint which fits the world-wide sustainability targets.
Additionally, the high-performance honeycomb core can be a sustainable solution for increasing awareness of the benefits regarding thermoplastic composites in high end applications within the automotive, aerospace and mass transportation markets. HPT honeycombs meet the demand for cost-effective, high end thermoplastic composites which are lightweight, strong, fatigue resistant, functionalizable and recyclable. Depending on the chemistry of the thermoplastic material, EconCore’s HPT honeycombs can offer such features as enhanced fire resistance and fire-smoke-toxicity rating or increased temperature resistance.
E.E: At what stage is the market where you are currently active?
ECONCORE: Honeycomb core has been used for many decades to manufacture composite sandwich structures. It provides stiffness to the structure with minimal weight. Among structural core materials, honeycomb core holds distinct market positioning with use in specific applications, demanding lightweighting and excellent mechanical performance. We anticipate to witness growth in demand for honeycomb materials, especially in the automotive and aerospace industries.
Amongst these two, automotive is the market where EconCore’s thermoplastic honeycomb technology is already established. Cost efficiency, sustainability, weight reduction potential, acoustic performance, thermoformability, short cycle convertibility are some of the features which the industry appreciates in view of development of new generation of automotive interior parts and EconCore technology has proven to fit to these needs very well. The presence of EconCore technology in this market is growing.
Aerospace on the other hand is a slow changing market. Thermoplastic composite technology is being incorporated rather slowely and the thermoset composites dominate. However, the call for more sustainable solutions in this market will lead to a change in the coming years. EconCore technology can offer sustainable solution, but first of all, it can help to reduce the production costs. This by adaptation of automated conversion methods, such as continuous lamination for the production of panels and compression moulding for the production of sandwich parts based on thermoplastic honeycombs and thermoplastic composites.
E.E: What can you tell us about market trends?
ECONCORE: Engineers have woken up to the effect plastics and CO2 emissions are having on the world’s ecosystems, wildlife and marine life. EconCore recognizes the challenge to move towards sustainable growth and a more efficient use of resources.
There is now a gradual shift away from thermosets. We are seeing a growing range of thermoplastics validated for use, with a conscious preference for the use of recycled and recyclable thermoplastics.
There is an increased use of honeycomb materials in the aerospace and automotive industries as honeycomb structures provide remarkable mechanical properties are lightweight, thus conserving fuel and reducing the weight of the vehicle.
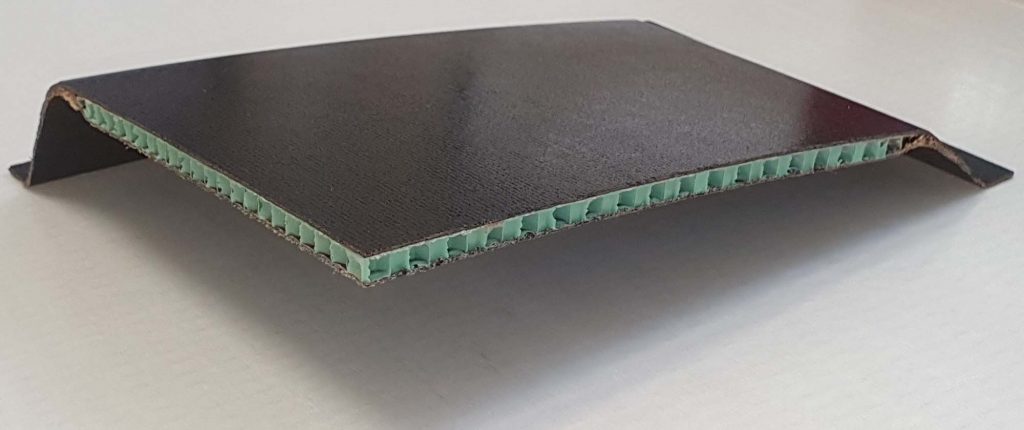
E.E: What are the most innovative products marketed?
ECONCORE: In more recent years, there has been a focus on recycled polyethylene terephthalate (RPET), which is mostly found in the form of granules; which once took the form of a plastic bottle. This recycling of plastics bottles is an important step forward in the pursuit of sustainability, as waste can now be converted into performance-to-weight-optimized honeycomb structures. Beyond RPET from bottles, the technology can also use more RPET waste streams, including consumer and industrial ones, that are otherwise difficult to find recycling applications.
High-Performance-Thermoplastic honeycombs of EconCore are equally innovative. Next to the clear advantages of thermoplastic honeycomb technology with regards to recyclability and sustainability, the combination of performing thermoplastic resins, light-weighting and cost efficient production technology opens up new perspective to the markets that need to adapt to the changes. At the same time, these HPT honeycombs offer the features, such as elevated temperature resistance and enhanced fire-smoke-toxicity rating, being a must-be in high end applications.
E.E: What estimations do you have for 2021?
ECONCORE: EconCore is hoping for a swift economic recovery after the pandemic. We are foreseeing growth for 2021 with the introduction of our new industrial line for large scale development and production of recycled PET and HPT honeycombs. With this scale up EconCore will provide new solutions for sustainable and high-end applications.
At the same time, we envisage in a strong growth of the presence of polypropylene honeycomb technology in the applications that have been mastered already, including industrial packaging and automotive.