eloprint is a tech startup from Germany that is all about 3D printing and electrical contacting. They are a group of electrical engineers and 3D designers with a lot of experience in these industries.
Interview with Georg Pröpper, CEO of eloprint.
Easy Engineering: What are the main areas of activity of the company?
Georg Pröpper: eloprint is specialized in the development and production of test adapters. Every time an electronic assembly has been manufactured; it needs to be tested before it can be assembled into the final product. For this purpose, test adapters are needed that establish electrical contact at numerous spots. Subsequently, for instance, a firmware can be flashed or electrical voltage of the individual circuit parts can be measured.
Traditionally, such test fixtures are large devices made of milled components. They are very expensive and have long delivery times. At eloprint, we produce the test fixtures almost exclusively from 3D-printed components. The size of the adapters is always precisely matched to the size of the electronics to be tested. Therefore, we are particularly faster and cheaper than conventional suppliers. In addition, our adapters are highly compact, which makes them easier to be integrated into production lines.
E.E: What are the ranges of products?
G.P: Over the last few years, we have developed three methods of design on which most of our products are based. They allow us to electrically contact small, medium and large boards from one or two sides. Individual special features can easily be taken into account as well, since we have many degrees of freedom thanks to additive manufacturing. For example, display elements, switches or sensors can be easily provided.
However, occasionally the requirements are so individual that we create completely new designs according to the customer’s needs. We consider this to be one of our greatest strengths, because here, again, the flexibility of 3D printing works to our advantage.
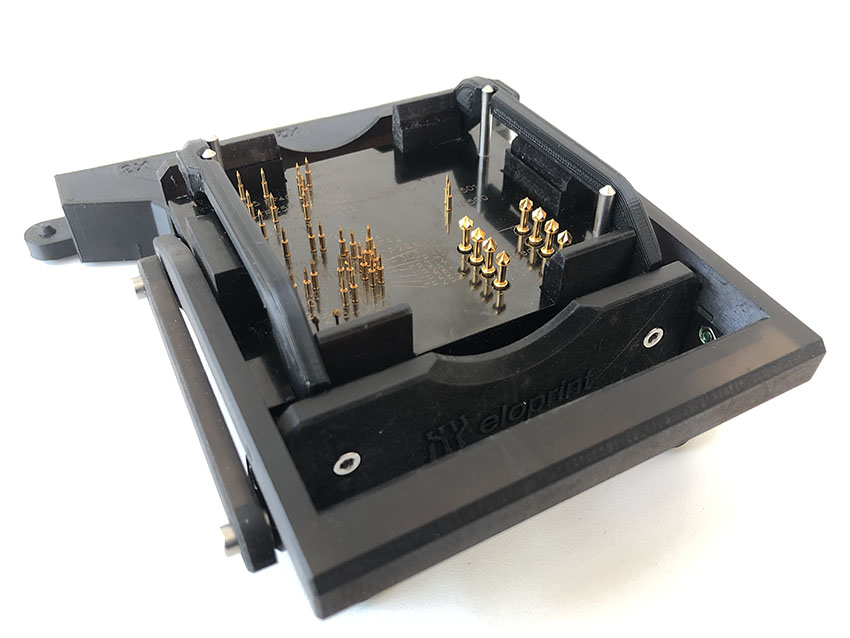
E.E: What’s the news about new products?
G.P: Even though our adapters are extremely durable, some customers are skeptical because they are made of plastic. That is why we are currently developing a design that is largely made of metal to meet the demands of industrial environments.
We are also currently expanding our machine fleet. Until now, we have manufactured the majority of our products using fused deposition modelling (FDM). The process is comparatively inexpensive and offers a wide range of materials. However, it has disadvantages, especially in terms of precision and freedom of geometry. Therefore, we will increasingly use selective laser sintering (SLS) and material jetting (MJP) in production in the future. The SLS process can produce highly stable PA12 components, and the MJP process is very accurate. Both processes offer a high degree of geometrical freedom for the printed models.
E.E: At what stage is the market where you are currently active?
G.P: Test fixtures have been required ever since electronics have existed. This is therefore a well-established market. 3D printing has also become indispensable in many industries. As far as we know, however, we are the first and only manufacturer to use 3D printing on this scale for the production of test fixtures.

E.E: What can you tell us about market trends?
G.P: Electronics are becoming more and more miniaturized. The test fixture market must follow this trend. The size and spacing of the test points that need to be electrically contacted are getting smaller and smaller, which is challenging the test fixture manufacturing processes.
E.E: What are the most innovative products marketed?
G.P: Our innovation consists primarily of manufacturing our products additively. This allows us to implement innovative mechanisms in every project that would traditionally not be possible or very expensive.

E.E: What estimations do you have for the rest of 2022?
G.P: Basically, we are currently experiencing high demand and will continue to implement many customer projects for the rest of the year. In addition, the aforementioned 3D printing technologies SLS and MJP will be implemented in 2022, which will allow us to create even more complex designs. Our industrial metal design is not expected to be ready for use until 2023.