ELPA operates in a railway sector and is focused on solving challenges of rail and wheel wear as well as high friction noise (HFN) that stems from the wheel-rail interface.
HFN cannot be stopped by wayside barriers because of its penetrating force. Therefore, the only solution is its reduction at the source. There are two main parts of the rail that interacts with the wheel: rail gauge and top of rail (TOR). The main source of HFN is a rolling friction in curves on top of rail.
In theory it could easily be reduced by applying lubricant on top of rail, however lubrication of TOR in its classic sense is strictly forbidden because it reduces traction required for safe traffic. Even standard lubrication materials that are applied to rail gauges are potentially dangerous as they often pass onto TOR where they compromise traction.
ELPA has been resolving this long-standing challenge by developing and improving materials that could “lubricate” the wheel-rail interface both on rail gauge and top of rail without compromising required traction. A whole new class of materials has been developed and it has been named Composite Hardly Fluid Compound (CHFC) that stabilizes friction coefficients within required frames on both parts of the wheel-rail interface. The ability to address both parts of the wheel-rail interface with only one material makes it the safest system on the market. Its outstanding quality is a very high content of solid particles (above 40%) that is instrumental in stabilizing friction coefficient. The “liquid” part of the CHFC primarily acts as a medium to transport solid micro particles along the rails where they fill micro cracks and fissures. These cracks and fissures are instrumental in causing high frequency noise HFN and also promote rolling contact fatigue that reduces viability of rails and their expensive replacing.
Conventional systems of industrial lubrication on the other hand cannot distribute substances with high portion of solid particles. ELPA accepted the challenge and developed its own WONROS technology (Wear and Noise Reduction at Source) to accurately distribute CHFC materials with high content of solid micro particles. The technology has been improved and perfected for over two decades and it is protected with over twenty patents.
Interview with Darja Goltnik ,Co-owner and CEO of ELPA.
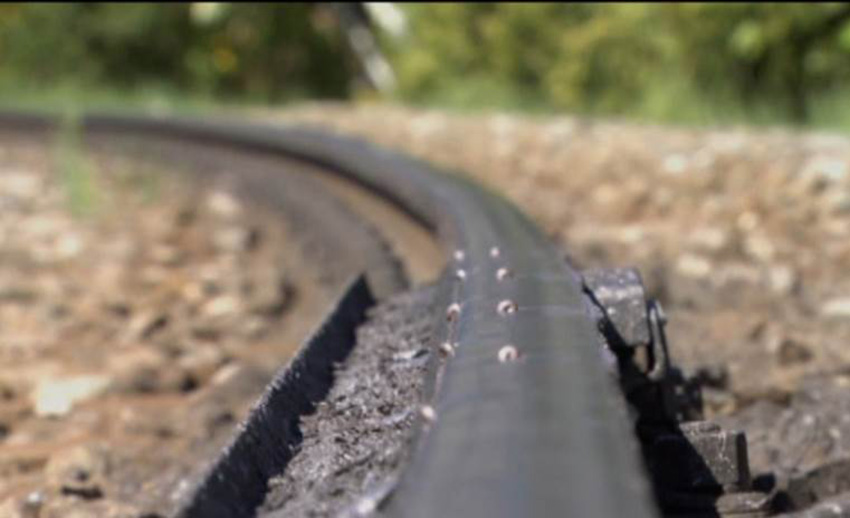
Easy Engineering: What are the main areas of activity of the company?
Darja Goltnik: Railway infrastructure and rolling stock owners are faced with high maintenance costs because of the wear of rails and wheels that takes place mostly in curves. WONROS technology helps reducing life cycle costs of the railway infrastructure as well as the rolling stock. Technology’s ability to reduce high frequency squealing made it particularly useful for tramway and metro infrastructures where there are many tight curves and high population density.
E.E: What’s the news about new products?
D.G: In 2022 ELPA will contribute to the sector with two new patent protected inventions. One is an on-board system that is mounted on rolling stock to “lubricate” wheels with CHFC material. It is mounted on the train locomotives, metros or tramways. Its main advantage is that it requires no compressed air to apply the CHFC onto the wheels. Tramways usually have limited amounts of compressed air available and will probably be the first to embrace this technology.
Second contribution is very much in line with our dedication to protect environment by reducing energy consumption and CO2 emissions. A trackside system that will only utilize kinetic energy of the passing wheels for its functioning. Patented system will be especially valuable where other energy sources are not available such as remote locations, locations with not enough sun exposure, tunnels etc. Its inauspicious construction will prevent it from being vandalized.
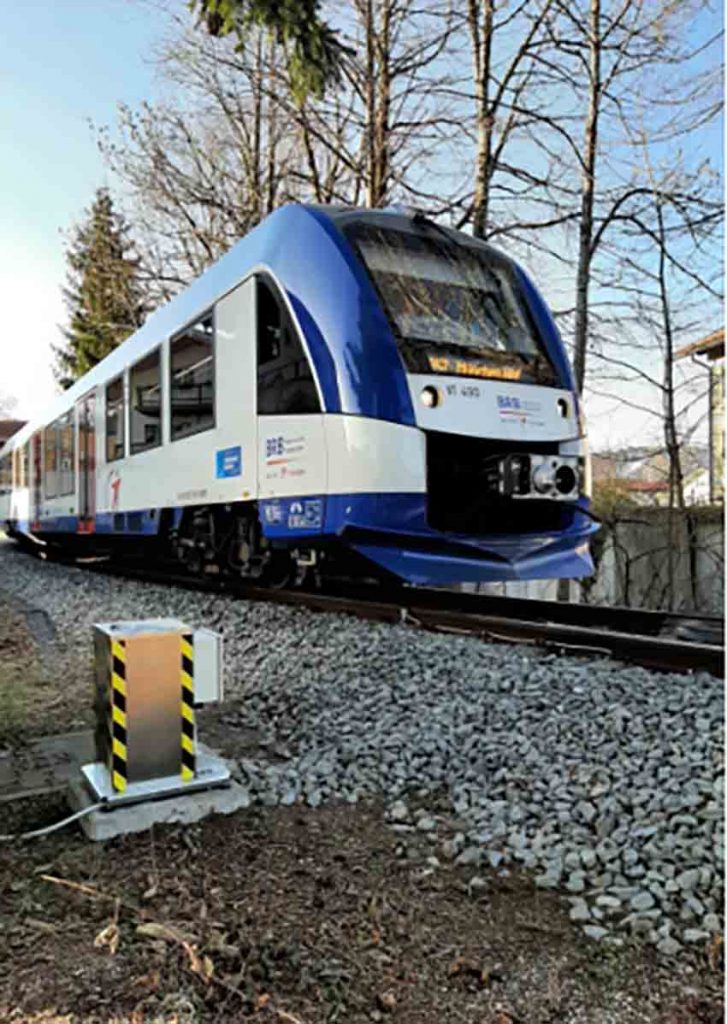
E.E: What are the ranges of products?
D.G: ELPA focuses on track side systems and mobile systems for “lubrication” of the railways and wheels that have been explained above. We need to point out the Bremex Annsys technology that is in the class of its own. It eliminates wear and high frequency noise on marshalling yards by 99,99%. It supplies wheels with CHFC material to reduce wear on all parts of the marshalling system: trackside brakes (8-fold reduction of wear), rails, counter rails, switches as well as the wear of wheels. European Commission granted the technology a European Business Award for the Environment.
E.E: At what stage is the market where you are currently active?
D.G: Wear of rails and wheels has been a persistent challenge for a railway sector since its beginnings and first industrial patents to resolve this problem are over 100 years old. Reducing wear also reduces CO2 emissions related to the production of steel (rails and wheels) – iron and steel industries account for 11% of the global CO2 production.
The HFN associated with wear is increasingly more in the focus of the railway sector as well as the general public because of its proven highly negative effects on health and overall wellbeing.
E.E: What can you tell us about market trends?
D.G: Global concern for carbon emissions will bring into focus more details where the sector could be more environmentally friendly. This will put companies in the business of railway lubrication under pressure to bring results at an acceptable cost. Mainly this can be done with environmentally friendly lubricants and efficient and accurate delivery systems.

E.E: What are the most innovative products marketed?
D.G: (Since it is ELPA’s systems, as the industry combined did not bring forward as many patents as ELPA – so we might skip this question).
E.E: What estimations do you have for 2022?
D.G: Railway sector is a very traditional sector so there should not be any pivotal changes in front of us. Generally private ownership correlates to faster introduction of green and efficient technologies related to wear and squealing on railways. Public sector trails behind with less efficient management. We hope it will start adopting green and effective technologies at a faster pace.