Fimic is a family-owned company based in the north-east Italy. The company started 58 years ago (1963) manufacturing customized guillotines for cutting industrial waste bales and rolls, but it was in 1996, when they improved the melt filtration technologies available at the time, with the first FIMIC backflush filter entering into service, followed the year after by the “scraping” system, that they started to make history in the plastics recycling industry and they’ve been known for 25 years as the specialists in automatic self-cleaning melt filters.
Easy Engineerig: What are the main areas of activity of the company?
FIMIC: Fimic acts in the plastics recycling market, with our different types of automatic melt filters we target highly contaminated plastic materials, especially post-industrial and post-consumer plastics. We not only manufacture melt filters, but we also design and develop new technologies which allow us to deliver cutting edge solutions and provide those who choose our technology an ever more efficient line of work and productivity. Also, at FIMIC, we constantly run tests in our internal laboratory to guarantee high results and a supreme quality for end products.
E.E: What’s the news for 2021 about new products?
FIMIC: For 2021 we’ve designed a revolutionary machine, the ideal solution for those seeking to achieve the highest possible quality of the recycling process, significantly lowering maintenance and operational costs. Combining FIMIC’s typical high engineering standards and the highest quality of manufacturing materials, to offer a superior, reliable and high-performance product that guarantees to all players in the recycling industry significant savings in operational costs, as well as an excellent final result.

E.E: What are the ranges of products?
FIMIC: We are specialized specifically in two product lines, designing and manufacturing automatic and continuous melt filters and guillotines for the plastic recycling industry.
Our different types of automatic melt filters target contaminated plastics, especially post-industrial and post-consumer plastics, and had been designed to allow the customer to choose the filter according to the final application, the filtration, the material to be processed and the hourly production.
Based on these parameters, FIMIC is currently able to supply 5 different types of filtration with 5 filter models and it is the only company on the market specialized in filtration with this diverse range of models.
The RAS system is a scraping filter known for its flexibility and strength. Through the use of two blades, is able to scrape very high contaminations and reprocess both, post-industrial and post-consumer materials thanks to the adjustable discharge valve system. Following the success of the RAS filter, the introduction of the ERA filter has responded to the need for double filtration in certain applications, saving on investments and consumption by performing the double filtration step in a single machine with two consecutive filtration chambers.
RAS+REF, the melt filter that made FIMIC technology renowned in the recycling field, enhanced with the possibility to work in backflush mode, can in fact operate in two different ways: in scraping mode or in backflush mode, providing more options to anyone wishing to process materials with mesh filters, representing an ideal option for woven mesh processing with exceptional final results.
The TEN melt filter is the innovation of the first automatic screen changer, and allows continuous filtration on woven mesh, eliminating material build-ups and reduction of output with the additional option of adjusting the mesh output to guarantee regularity and quality of post-industrial waste alongside the chance to avoid constant supervision of the operator, making daily work much simpler.
These days there’s no end to the amount of material to be recycled, and yet is necessary to keep really high-quality standards for the end product. That’s why FIMIC designed a really unique melt filter, representing the culmination of its technology and the expertise that made them the filtration specialists, the largest melt filter on the market: GEM, the twin melt filter that works twice as much with its unmatched filtering surface and using just two parallel filtering screens guaranteeing better results than anything else on the market, an ideal application for high-throughput recycling lines.
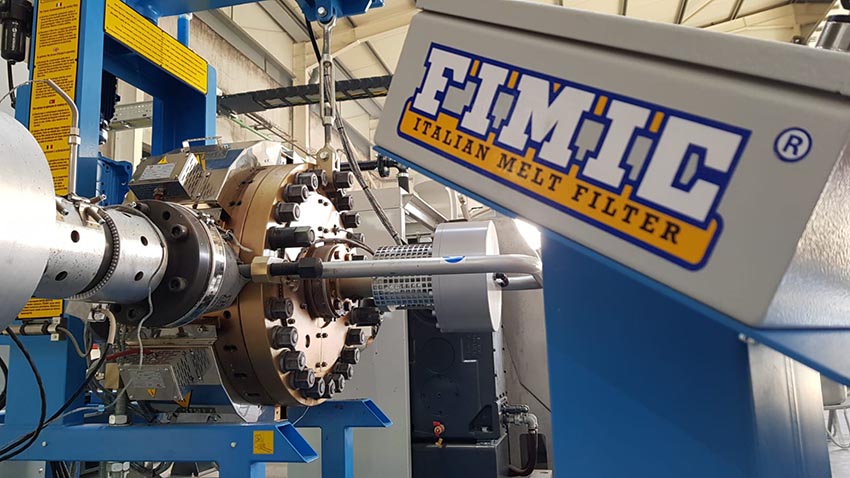
E.E: At what stage is the market where you are currently active?
FIMIC: The plastics recycling market is booming since some years already. This because of a variety of factors acting altogether.
Consumers are getting more and more sensitive to environmental protection as well as the need of a circular economy for plastics, hence the use of more recycled plastics in new plastic products.
The major quantity of waste plastics are post-consumer, i.e. very contaminated. To reach high quality recycled plastics from contaminated waste needs automatic technologies to filter out impurities and contaminations from the plastic flow. That’s where FIMIC’s technology can help more and that’s one of the reasons of our success.
E.E: What can you tell us about market trends?
FIMIC: The trend is finally to design plastic products to be recyclable and produce them in full or in part (depending on the application) with recycled plastics.
This is going to be implemented by law in just a few years from now, as all new plastic products manufactured in the EU will need to contain at least 25% recycled plastics. Therefore, many brand owners and the majority of recycling companies need to implement and improve their technology to satisfy the needs of brand owners (quality, characteristics) and at the same time face the challenges of recycling post-consumer plastics.
FIMIC has been working many years now on improving its filtration technologies in order to meet all of these demands.

E.E: What are the most innovative products marketed?
FIMIC: FIMIC’s most popular machine is the continuous scraping, self-cleaning melt filter called “RAS”, designed for recycling contaminated plastic waste material. The RAS melt filter is based on a self-cleaning system, that continuously collects the contamination stopped on the screen to let the melt pass it through. The contamination is collected by the scraper and it is discharged for an adjustable set time depending on the percentage of the contamination. RAS ability to manage any contamination levels, made FIMIC known across the whole world, and today we’ve delivered and installed more than 300 RAS filter units worldwide, number that consolidates of the current place as key players in this industry.
E.E: What estimations do you have for 2021?
FIMIC: Fimic has set, for 2021, new challenges to create more opportunities not only for itself but also for the entire plastics recycling market, a market in constant growth. As a response to this increase of demand in the plastics recycling industry, Fimic is ready to optimize their internal production processes, with new industrial and production halls designed specifically to suit the most modern production requirements, and equipped with a new production line, and cutting-edge technology, so FIMIC engineers and technicians can devote themselves to the development of new solutions, increasing significantly its production capacity, accelerating manufacturing times to offer an even faster service to its customers and to achieve an increasingly efficient recycling of plastics.