The basis of FUHR’s product range is formed by individual components from the area of wire forming. Their customers apply these components in their production lines – whether for the modernizing of existing lines or for the construction of completely new production facilities.
The company is a medium-sized family-owned and managed company in the third generation, which can look back on more than 75 years of know-how in the construction of rolling lines and special machinery. During the course of the past decades, they have become a leading partner of many industry sectors – be it consumer products, logistics, the construction and energy production industries, medical technology, as well as automotive and textile industries.
Easy Engineering: What are the main areas of activity of the company?
FUHR: FUHR develops highly specialized wire rolling mills for the widest range of industrial applications. As a supplier of complete turnkey solutions, we develop and construct tailor-made equipment and systems in close collaboration with our clients – systems that integrate seamlessly into existing processes on site. Whether you are looking for a complete rolling mill or just a component, get in touch and we will find a solution!
From our modular component range, we will build a production line optimally matching your requirements. Here, we perceive ourselves as a system supplier designing, constructing, building, delivering and commissioning your system. We take full responsibility for our system producing your products in the quantity and quality that you require.
The basis of our product range is formed by individual components from the area of wire forming. Our customers apply these components in their production lines – whether for the modernizing of existing lines or for the construction of completely new production facilities.

E.E: What’s the news about new products?
FUHR: The increasing demand on enamelled rectangular copper wires are causing manufacturers to rethink production. In order to avoid even the smallest wire damage caused by winding and unwinding systems, inline production is increasingly becoming the focus of enamelled wire manufacturers.
Due to this market development, FUHR has developed an economical inline profiling unit that combines the rolling and profile drawing processes and combines the advantages of both technologies.
Until recently, measurement systems for measuring the quality of products during the process were used almost exclusively for process control. Process variables were measured, then compared with target values and the settings of the production plant were optimised with the deviations determined.
Conventional laser shadow measurement systems, as typically used in the drawing of round wires, have not proven themselves in profile rolling plants. For one thing, even a slight tilting of the wire changes the size of the shadow. On the other hand, laser systems cannot be used permanently in the wet area of the pre-rolling stages.
FUHR therefore relies on tactile measuring systems in which the wire is scanned with diamond-tipped, high-resolution displacement measuring systems. Alternatively, instead of diamond pins, pin rollers are available that are specially adapted to the wire geometry.

E.E: What are the ranges of products?
FUHR:
Production lines for:
- Rectangular copper wire
- Copper PV-ribbon
- Precision profile wire
Components:
- Uncoilers
- Roll heads
- Rolling devices
- Inline profiling
- Measurement
- Coilers
Individual manufacturing:
- Roll manufacturing
- Contract manufacturing
Consulting services
Research & development
Customer services

E.E: At what stage is the market where you are currently active?
FUHR: There is a lot of things going on in the market. New legal requirements lead to new demands, various incentive programs generate increasing demands e.g. for small rectangular copper wire. A lot of wire manufacturers look for opportunities to optimize their production processes, whereas at the same time new players enter the wire forming market with new ideas. With the knowledge we earned over the last decades, we are able not only to support the demands but specially to help customers to find the right solution for their requirements.
E.E: What can you tell us about market trends?
FUHR: Electromobility is picking up speed. In order to be able to survive in the automotive sector sustainably, cost-effectiveness is just as important a success factor as mature process capability that produces consistent quality over the long term. On this basis, classically wound stators for traction motors have been replaced by hairpin stators for some time.
For this purpose, formed, insulated rectangular copper wires are inserted into the stator slots of laminations to form compact baskets and then welded together. Due to the high precision, greater winding densities can be achieved than by using wound round wires, despite the lower material input. High scalability at low production costs make hairpin stators quite attractive for the automotive industry.
With the IPU320, FUHR has developed an economical inline profiling system that enables enamelled wire manufacturers to meet the high quality and price requirements of the automotive industry. The IPU320 combines rolling and profile drawing processes, whereby large width to thickness ratios can also be achieved due to the driven rollers.
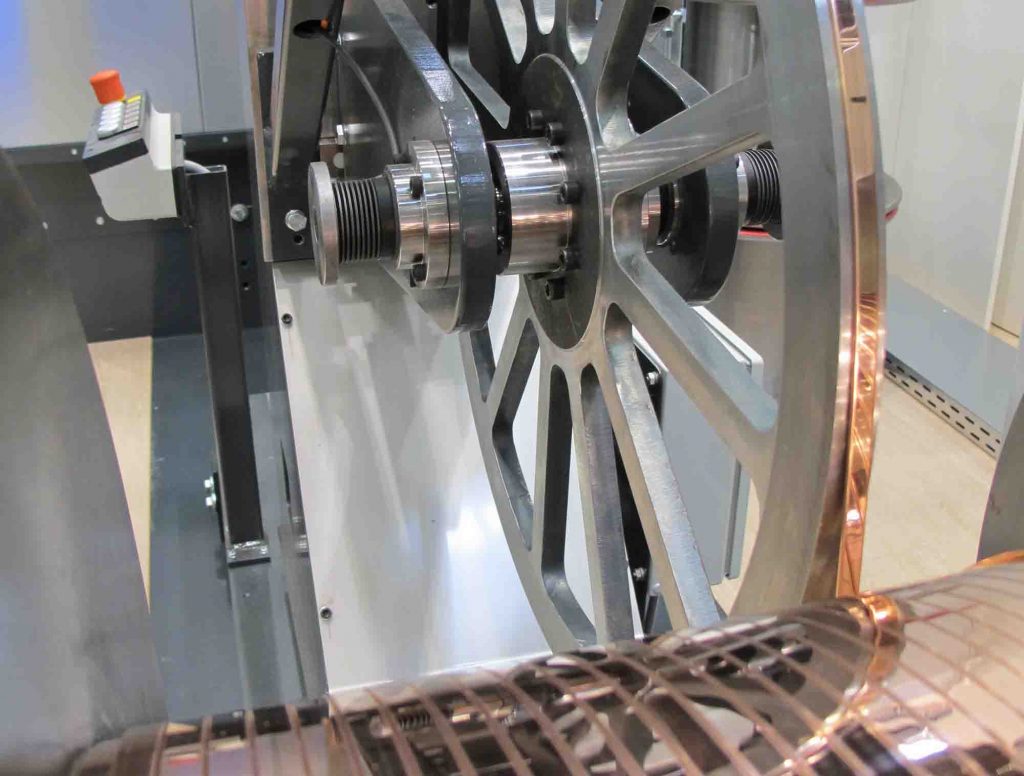
E.E: What are the most innovative products marketed?
FUHR: Over the past 10 years, FUHR has developed a modular machine construction kit. This concept called „special machine construction with standard components“, has now been refined to such an extent that all particular customer requirements can be met with little development effort.
Standardization of our portfolio to the greatest possible extent is essential for us and increases our competitiveness while minimizing the associated technical risk.
Today, FUHR is considered the technology leader in the flat and section cold rolling mill segment. In order to continue to keep pace with the growing technical requirements of our customers and in global competition, continuous innovations in all areas are crucial. In all cases, it is important to maintain the highest quality standards along the entire process chain.
When it comes to classic mechanical engineering with a focus on mechanical solutions and conventional control concepts, FUHR always works to achieve the best possible result under the given conditions in the face of growing customer demands in terms of productivity, quality and flexibility. But of course we will not rest on that achievement in the future.

E.E: What estimations do you have for 2022?
FUHR: In order to be prepared for the challenges of the future, we are focusing on innovations in various areas in the medium to long term, which are outlined below:
- Development of a highly dynamic roll positioning system to compensate for short-wave dimensional fluctuations in the rolled products, which are typically caused by geometric errors in the rolling tools. In addition to the positioning mechanics to be developed for this purpose, the further development of the inline measuring system IMS and the software platform F-MAS is necessary.
- Expansion of the machine portfolio with quarto rolling mills for narrow strip production in order to be able to produce thinner and wider strips than before. Here, too, the focus is on the precision of the rolled strips.
- Further development of the IPU series to offer our customers compact units for integration into existing production processes. Such highly integrated inline processes are increasingly in demand from customers in order to be able to ensure the quality of the products.
- Re-introduction of reduction rolling mills into the product portfolio. This area has been left to the competition in recent years. However, there is still a demand for this machine concept, especially for casting wires made of non-ferrous alloys, in order to achieve high material strengths through cold forming.“
In addition to the main business – the delivery of new, turn-key plants – and the supply of spare parts to our customers, FUHR is already opening up new business areas. Examples entail the general overhaul and modernization of older machines, the regrinding service for customer rolls and an extended range of services.
Reliable, competent after-sales service – on site or via web remote – is becoming increasingly important for our customers, as their own service teams are either overwhelmed by the sometimes highly complex technology or have already been abolished due to cost pressure.
No one can look into the future, but this much can certainly be said: Digitalization and electromobility will be of central importance in practically all industries in the near future – also at FUHR! Our goal is to adapt our services even more flexibly to the needs of our customers and to use the potential of networked communication channels.