Garmo Instruments is a new company, founded in 2020. The Director and cofounder Pablo del Villar came with the experience of being the Meta Vision System group manager and along with with engineers’ team has spent these two years to develop user-friendly laser seam tracking sensors with the main objective to break the traditional difficulty barrier standing between seam tracking sensors.
GarLine is the first robust, technically advanced and easy to use seam tracking laser sensor compatible with welding robots, cobots and other hard automation welding machines. What makes a difference is the Plug&Play connectivity of the sensor, thanks to the minimization of additional devices that are usually required for other welding sensors. With GarLine, only a PoE switch and a standard cat6e cable are necessary for welding.
Garmo Instrument’s main objective to make welding easier, and to develop easy to use welding devices, whilst solving the typical difficulties and deficiencies. The company’s aim is to ensure outstanding welding quality, reduce unnecessary waste, offer a solution for multipass welding and provide a wide range of welding joints, and all with a user-friendly device with minimal maintenance requirements.
Interview with Pablo del Villar, Director and Co-Founder at Garmo Instruments.
Easy Engineering: What are the main areas of activity of the company?
Pablo del Villar: Garmo instruments is specialized in vision system for hard and demanding environments. From big changes in temperature, smoke, dust to high frequency electrical noise… all of it makes welding one of the most demanding environments in a factory. There is a reason why we want to start focusing on welding vision sensor.
The main difference with the other companies offering similar products is the integrators focus point. Our products are focused to cover the most important pains the integration companies suffer when they need to integrate these solutions.

E.E: What’s the news about new products?
P.V: Traditionally, seam tracking sensors were used as the last resource for welding automation, when other technologies could help. The main reason for this is the pricing, the technical difficulty and the maintenance requirements of the sensors.
Garmo Instruments came to change this. We offer user-friendly, technically advanced and easy to maintain laser seam tracking sensors.
We argue that an easy to implement sensor can rival other techniques and will be cost effective in the final run. Example, a company that want to have a robot cell for low to medium runs, might expect large amounts of money and resources in the manufacturing and design of the fixings. Moreover, the programming time of not perfect lineal or circular shapes is significantly reduced by using a seam tracking sensor.
E.E: What are the ranges of products?
P.V: GarLine sensors, has 3 different applications areas.
GarLine C is addressed to cobots with our patented vision programing helps the operator to quick and reliably position the torch.
GarLine PLC, for special purpose machines where a PLC controls the system. The GarLine PLC integrated within the PLC software making it easy for the programmer to integrate it with automated welding systems like column & boom, gantry welding systems or longitudinal / circumferential welding structures.
Our upcoming release, GarLine R, integrates with Fanuc robots. The GarLine sensor connect directly to the robots and can be used and programmed in the robot iPendant. Keeps update with the news about the integration in Fanuc and other robots.

E.E: At what stage is the market where you are currently active?
P.V: We are in the sweet moment for vison systems. We are going to see more new technologies and application coming every day. Nowadays, we are used to unlock the mobile phone with face recognition, which not that long ago was only possible in sci-fi movies. The current developing of the embedded technologies allows to miniaturize more and more processing power giving as the capabilities to increase the speed of complex process in a usable dimension and cost manageable ways.
We have seen this change also integrating in industrial solution from Pick and Place robot to quality controls. Welding will not be out of this.
E.E: What can you tell us about market trends?
P.V: The market is changing – quality is no longer the selling point. If your product doesn’t fulfill the customers’ needs, you are out. The new trends are moving to customization with a very demanding delivery time. This is the new challenges of the automation industry. The welding sector is not out of this with more and more need of automation systems for a low volume high mix of parts.
Adaptive automations solutions are the new needs. The production lines need to be easily reconfigured to adjust to the changes in the products. From the sensor point of view, we will see more and more of line programming where the machine will be programmed at the same time that the product is designed. Vision systems can help to adjust from the 3D model to real production.
Garmo Instruments breaks this barrier with the seam tracking sensors since this system doesn’t require an in-depth technical formation and the full IoT connectivity can be in the line of the new developments
E.E: What are the most innovative products marketed?
P.V: The increasing lack of trained welders is a global problem. New generations are very technical friendly but tend to avoid the welding environment due to the difficult working conditions.
For this reason, we came up with the vision programing for cobots, our patent is process solution. The assisting welding helps the operator to move away of the welding area. The use of those technologies is not more complex than a mobile phone, in such a way that even somebody who had never welded previously would be able to professionally do it in a short period of time.
Garline C is the perfect parent for cobot welding, making it the most advanced and flexible welding system. This approach has a lot more to run and in the future with the integration or artificial intelligence will change the factory approach of welding
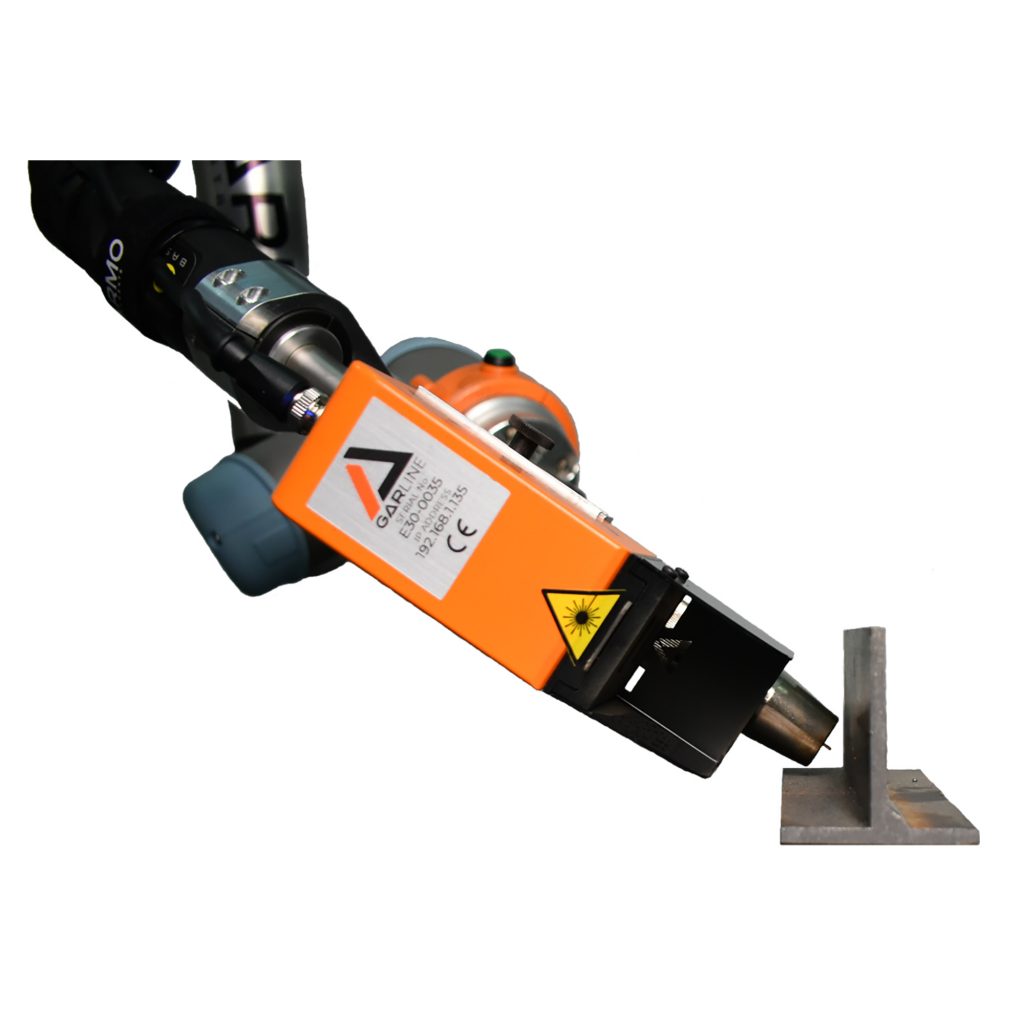
E.E: What estimations do you have for 2022?
P.V: After few years of difficulties, 2022 will be a year of changes. The component shortage is still affecting global market and it will be affecting the whole year. However, the automation is a global trend, and we see that the demand for laser seam tracking sensors is high, so our GarLine sensors are having a good worldwide reception.
Our target for 2022 is to get a complete integration with all the main robot and cobot manufacturers to settle our present and to keep expanding globally.