GHI SMART FURNACES is a family-owned company with more than 80 years of experience in customized complete solutions for melting, recycling and heat treatment of metals.
The GHI portfolio combines the design and manufacturing of industrial furnaces, the delivery of turnkey plants as well as after sales service and Industry 4.0 consulting services. With their Industry 4.0 solution, Beyond Alea, GHI is digitizing their customers‘ plants to improve, among others, purchase and operational processes as well as maintenance.
GHI SMART FURNACES additionally focuses on the application of new technologies and green energies in the production and recycling of metals – especially aluminum – with the aim of reducing emissions and thus counteract climate change.
Easy Engineering: What are the main areas of activity of the company?
GHI: Digitalization – with a team of 8 experts fully dedicated to Industry 4.0 we support our customers in optimizing their operational processes with the result of achieving relevant cost advantages.
Decarbonization – a key element for our customers in the next few years. Companies willing to work in markets such us automotive, will be required to reduce drastically their carbon footprint. Our R&D efforts are focused in helping customers to achieve this.
Aluminium Recycling – as our main driving activity, in which we have become an international leader. Our goal is to help our customers in the transition from primary aluminium utilization to recycled material.
E.E: What’s the news about new products?
GHI: We are working on the Aluminum Recycling Plant of the Future and want to show how we envision it. The development of carbon dioxide emission rights prices has increased fivefold in some countries in recent years, and governments are increasing eco-taxes to encourage the use of clean technologies such as renewable energy and green hydrogen, while at the same time launching support programs for R&D and investment in recycling plants that bring additional benefits in terms of resource efficiency, energy consumption and carbon dioxide emissions.

The Plant of the Future must combine decarbonization goals with the principles of the circular economy, which we define as follows:
EMISSION-FREE PLANT – using clean renewable energy that feeds an electrolyzer that produces hydrogen and oxygen. This electrolysis process is particularly suitable for recycling scrap in the Tilting Rotary Furnace as it uses both hydrogen and oxygen.
For post-consumer scrap recycling, Tilting Rotary Furnaces and Vortex Furnaces with Delacquering Systems will be fired with this low-carbon fuel. Hydrogen will replace natural gas. Holding and Alloying Furnaces use renewable electricity as a heating fuel.
ZERO-WASTE SCENARIO – the plant recycles and treats all by-products such as dross, salt slag cakes and generated fumes to create waste-free circular plants through sustainable aluminum alloy production methods.
We use a dross cooler that increases aluminium recovery from dross, reduces oxidation and emissions as well cooling space and time. Dross sorting facilitates the recycling of salts by specialized companies and the use of dross pieces to fill roads.
Total circularity is the clear path to the future, and we are already driving this change.
SMART TO BE PROFITABLE – the Plant of the Future uses machine learning technologies to process Big Data and to propose “end-to-end” solutions with state-of- the-art equipment that improves cast house operations.
Another aspect we have identified is that the largest equipment – we have a record of 65-ton tilting rotary furnace – provides a high economic return. The larger the furnaces, the more profitable they become.
The plant collects more than 10,000 data per second – Real time KPIs – which are stored and processed to simulate and predict performance with a digital twin.
This backflow of smart information enables our customers to optimize their plants.
The Beyond Alea platform, developed by AMV and GHI, is the only one that integrates all plant processes with real-time monitoring. It allows us to simulate from the purchase of the most suitable scrap quality to the cost of each process to achieve higher profitability of the plants. It also allows us to carry out supplier evaluations and reduces non-productive time.
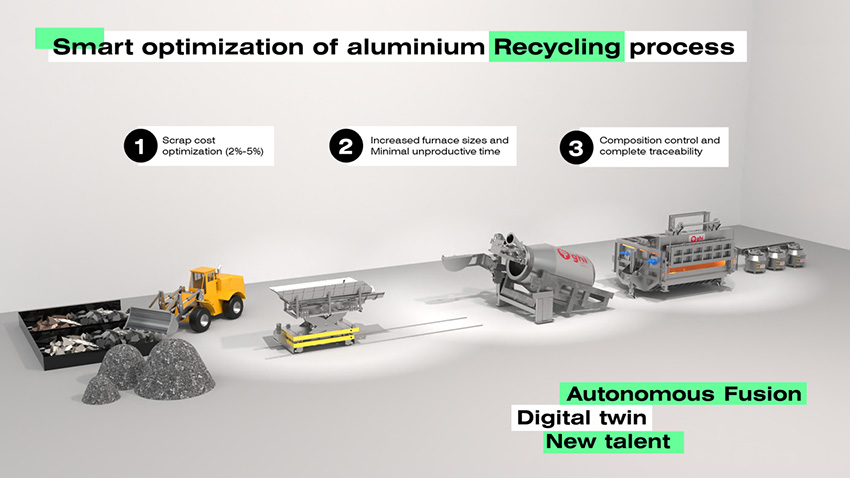
E.E: What are the ranges of products?
GHI: In recent years, we have specialized in complete key plants for melting, recycling and treatment of aluminium. We call them Recycall (recycling of aluminium), Alubillet (manufacturing of aluminium billets) and Recycan (recycling of cans).
In addition, we have a long experience in designing and manufacturing a wide range of furnaces for melting and all kinds of heat treatment of aluminum and steel. With more than 8.000 references of industrial furnaces all over the world, we are a strong partner for our customers in the digitalization of equipment and technical services.
E.E: At what stage is the market where you are currently active?
GHI: We operate in a very developed market of the metallurgical industry, where we have equipped hundreds of companies from different sectors: Aluminium producers, automotive industry, aeronautics, railways, steel mills, renewable energy and more.
Among them there are more than 8,000 references all over the world. Countries such as Germany, Norway, England, China, Iran, Russia, Venezuela, Brazil, Argentina, Mexico, USA are an example of GHI’s international reach.
E.E: What can you tell us about market trends?
GHI: It is clear that in our sector aluminum is growing at a high rate, like other non-ferrous metals.
The whole area of decarbonization will be crucial in the coming months due to new international regulations: The industry needs to switch to renewable energy sources and zero-emission plants to be competitive.
Also, the whole area of digitalization is affected by trends. The market shows that technologies such as machine learning and artificial intelligence are crucial for the industry. We are aware of the impact of these technologies on industrial processes and have been working in the last years to adopt some of them not only internally, but also as an offering to our customers. Companies need to improve their ability to digitalize and leverage data analytics, and redefine their processes and core competencies to adopt these advanced technologies that will have direct impact on future competitiveness. Some of these advanced technologies open up new business opportunities, better productivity, efficiency and new revenue streams for companies by digitalization of products and services or new digital service offerings.

E.E: What are the most innovative products marketed?
GHI: At GHI, we focus on developing innovative solutions to provide the best equipment in terms of process and efficiency to reduce consumption and emissions.
Climate targets are driving companies to take action to have more efficient processes and use clean energy.
All of our furnaces are designed to be integrated into Industry 4.0. This allows customers to control processes and reduce CO2 emissions and energy consumption.
Digital connectivity enables the integration of all processes in a production facility, resulting in process optimization, cost reduction and improvement of operational efficiency. This requires greater integration with customers and suppliers, which can help companies make better decisions to achieve global improvements.
E.E: What estimations do you have for 2022?
GHI: At GHI, we see the coming year as a gradual return to normality in corporate life, a return to travel and a reactivation of the international relations and major projects.
The aluminium industry, boosted by decarbonization and digitalization, will have to tackle major projects to avoid falling behind in an increasingly competitive and demanding market.
We at GHI are ready to support its clients in managing the technological change required to meet the demands of climate change and digitalization.