Founded in 1976, Global Shop Solutions is a leading producer of ERP software for manufacturing companies around the globe. The company is a 100% family-owned business headquartered in The Woodlands, Texas, United States, with offices in Mexico, Indonesia, Singapore, Australia, New Zealand and the United Kingdom. Global Shop Solutions supports thousands of manufacturing facilities in over 25 countries and more than 30 industries.
Interview with Dusty Alexander, President & CEO of Global Shop Solutions.
Easy Engineering: What are the main areas of activity of the company?
Dusty Alexander: We are focused on making our ERP software our customers’ most valuable asset and do so by providing them access to the right tools and people. We have a talented R&D department that handles updates and improvements to our core system. In addition, we also have a Continuous improvement Team that create tailored Dashboard and programs and provide ongoing ERP training for our customers.

E.E: What’s the news about new products?
D.A: We are consistently working on new updates to our core software, adding new features, screens, Dashboards, and more. Over the years, we have built new items to support the diverse needs and requests of our manufacturers such as a customer feedback system, a learning management system, a new user interface, mobile CRM, Dashboards and more.
E.E: What are the ranges of products?
D.A: Global Shop Solutions provides all-in-one integrated ERP system available in the cloud or on premise that includes over 30 applications, including shop management, scheduling, inventory, accounting, quality control, CRM and more.
E.E: At what stage is the market where you are currently active?
D.A: To remain competitive, manufacturers must be focused on the next generation of IIoT, automation and the digital factory. ERP software hits all those marks while simplifying their manufacturing.
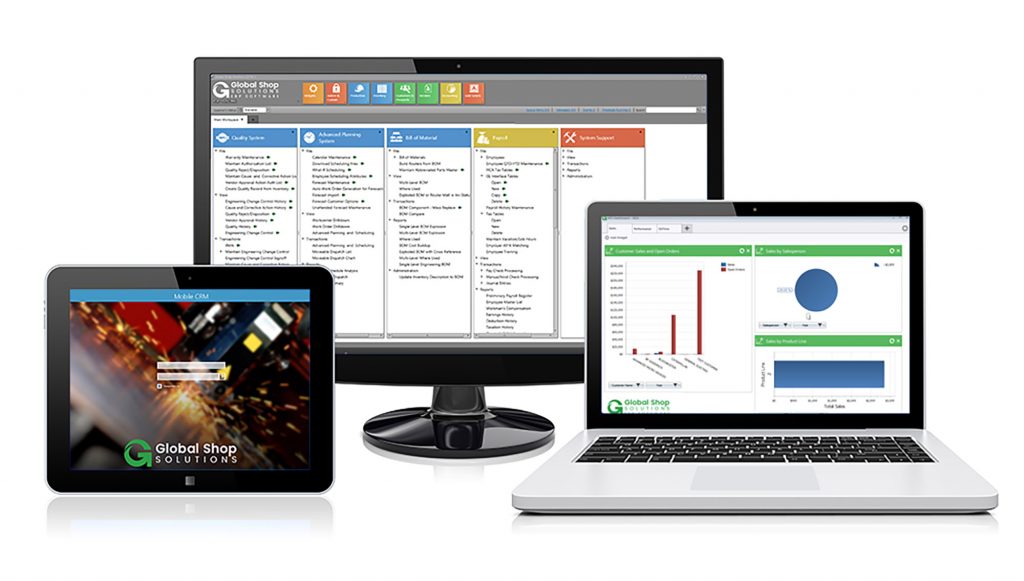
E.E: What can you tell us about market trends?
D.A: In recent years, we have seen the need for data visibility and benchmarking become a necessity and thus seen an increase use in KPIs and Dashboards. Now more than ever with ERP, manufacturers have more data at their fingertips – Dashboards on the shop floor telling employees how they are doing, if they are behind schedule, KPIs for decision-makers. With the help of ERP, manufacturers are identifying leading metrics and using that data to make better short-term and long-term decisions.
E.E: What are the most innovative products marketed?
D.A: TrueViews™ allows manufacturers to see real-time data on their shop floor. The data is displayed throughout the manufacturing facility on mounted TV screens that link directly to the company’s ERP system. These TVs display data that keeps personnel up to date on scheduling, work-in-progress (WIP), and other important production information – without having to log in to a computer, refer to manual spreadsheets, or hunt down a supervisor.
When an individual employee or work center falls behind on a job, the TV or monitor displays red flags identifying the job is late, allowing team members to step in and take appropriate action.
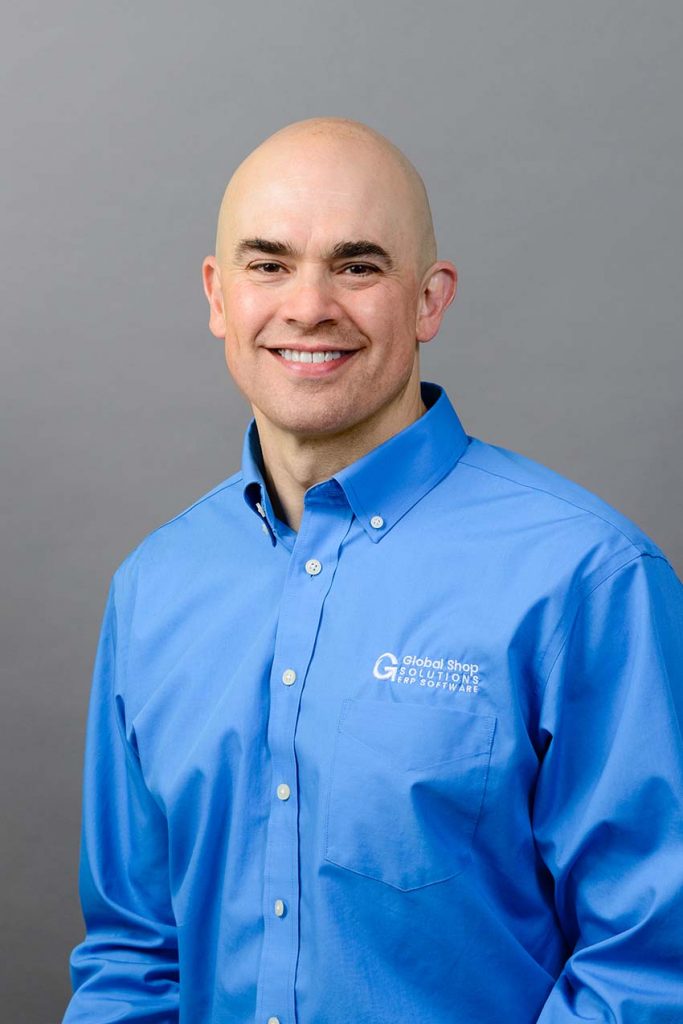
Dusty Alexander
E.E: What estimations do you have for 2022?
D.A: As more and more manufacturers take advantage of the power of ERP, we expect to see an influx of new integrations – import assemblies from a CAD system, communication with nesting software, connected to a tool crib. As manufacturers integrate with these technologies, they are cutting costs, working more efficiently, and simplifying the entire manufacturing process.