In an industrial environment, large production equipment is often tailor-made. When components break down this results in long lead times. Entire installations need to be completely replaced when components have become obsolete, moulds have been lost or suppliers have gone bankrupt. Guaranteed offers a solution to these problems by repairing and rebuilding large metal parts, using wire & arc additive manufacturing. Born from Innovation, they use unique and state of the art simulation, monitoring and inspection tools to guarantee first time right production.
Easy Engineering: A brief description of the company and its activities.
GUARANTEED: Our vision is to keep industrial assets operational by overcoming the pain points in today’s supply chain. We can achieve this by producing spare parts on-demand, reproducing obsolete parts, refurbishing damaged components or optimizing existing ones. Our unique facilities allow us to provide extra-large scale metal wire and arc (WAAM) additive manufacturing services for customers all around the world.
We at Guaranteed, want to contribute to the creation of an eco-friendlier manufacturing future, in which we are recognized for the quality of our service and the innovative spirit of our people. Today, we operate a WAAM manufacturing facility capable of producing parts up to 10 x 6 x 5 meters and weighing up to 20 tons in a broad variety of metals ranging from carbon steels, to stainless steel, Ni-based alloys, titanium, aluminum.
E.E: What are the main areas of activity of the company?
GUARANTEED: Ageing installations are a common issue in many industries. Assets are increasingly used beyond their original design life, which results in parts becoming high-risk for downtime or failure. This can result in significant non-productive time which could cost upwards of hundreds of thousands of euros. Maintaining the integrity of equipment is difficult given that like-for-like replacements of parts are no longer available due to obsolescence of the equipment model or changes in engineering standards.
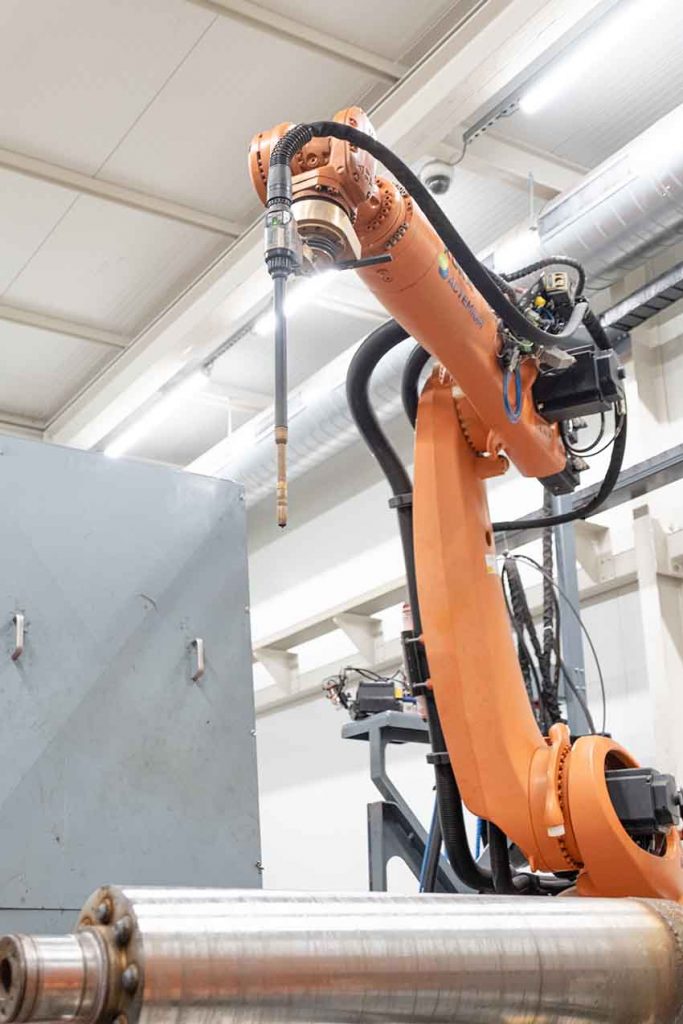
Guaranteed’s WAAM services allow such parts to be reproduced at an affordable cost, even for small series, repaired or refurbished. In the latter case, the original part design or material selection is given an upgrade which allows the refurbished part to have an increased performance or life-time as compared to the original OEM part.
For very large parts or failures occurring in remote areas, the costs and logistics involved in dismantling and transporting the damaged part might become prohibitive. To resolve this issue, Guaranteed can propose a “mobile WAAM additive repair service” which allows on-site or even in-situ repair or remanufacturing.
By focusing on large scale, wire-based, hybrid processes, Guaranteed creates value for its customers in the oil & gas, maritime, steel, mining, aerospace, … industries by lead time reduction, inventory optimization, lifetime extension or even process performance improvement. Our aim is to provide our customers with high quality parts, both on a geometrical and metallurgical level. Our high-quality manufacturing is enabled by data analysis and process monitoring to facilitate qualification and certification. Thanks to our industry leading dimensional capabilities Guaranteed is able to provide a fast, cost-competitive and sustainable alternative to casting or forging as well as hybrid combinations or functionally enhanced cast or forged parts. Our ambition is to grow both in geographical and technological footprint, but never at the cost of the quality of our products and services. Through a high reactivity, structured workflow and project follow-up, we strive to gain and maintain the trust of our customers.
E.E: What’s the news about new products?
GUARANTEED: As guidelines and standards for AM-produced parts have become a reality, Guaranteed will invest in their implementation in 2023, aiming for both the standard ISO9001 as well as AM specific site certification. Along those lines we’ll also keep pushing our efforts when it comes to using process monitoring and process control combined with AI/ML to facilitate qualification and certification processes.
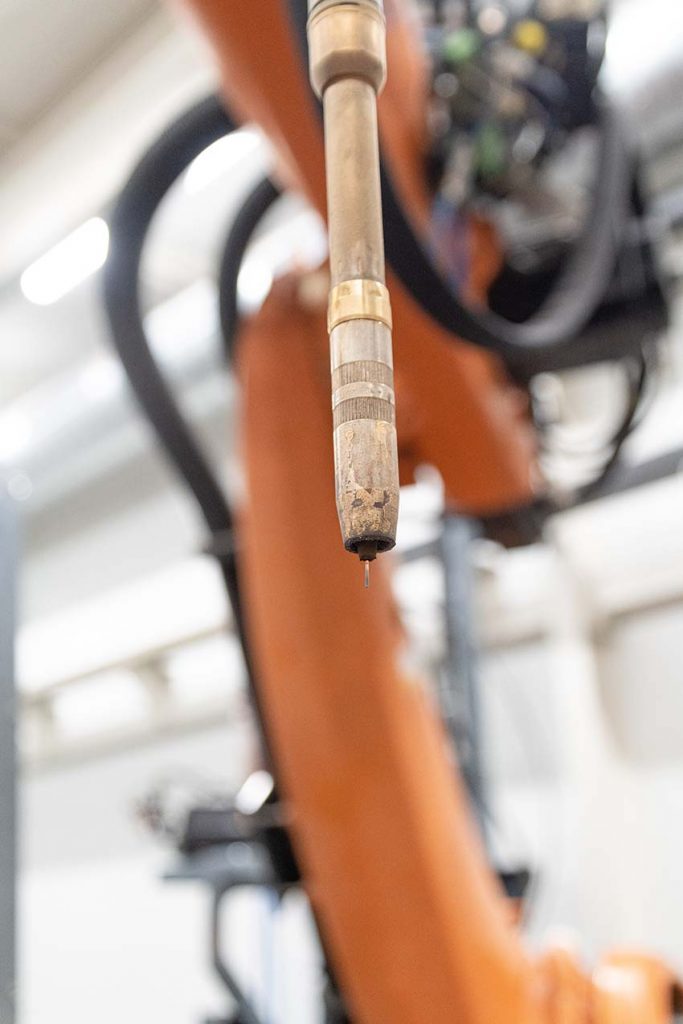
During 2023, we will also implement further enhancements of the technology we use, which will allow to increase deposition speed as well as perform enhanced in-situ microstructure control during deposition.
Driven by the market, we are also exploring several options for expanding both our capacity as well as geographical footprint.
E.E: What are the ranges of products?
GUARANTEED: The combination of component size and functional complexity makes a compelling case for the wire based DED-processes (CMT and plasma) offered as a one-stop-shop manufacturing service by Guaranteed as it allows parts up to 10 x 5 x 6 meters and up to 20 tons to be produced near-net-shape within short lead times at a competitive cost. Currently the material database is already well populated (steel, stainless, Inconel, titanium, aluminium, bronze …), but it can easily be expanded at the request of our customers
E.E: At what stage is the market where you are currently active?
GUARANTEED: As technology evolves, as the quality ensurance framework becomes established and as also the deposition efficiency is increased even further, the tipping point for wire arc additive manufacturing to be a cost and supply-chain efficient solution versus conventional manufacturing is gradually shifting towards larger series sizes. Today we regularly receive RFQ’s for series up to 1000 parts annually and notice more and more customers actively considering WAAM as a viable alternative to conventional manufacturing as a solution to today’s supply chain challenges.
E.E: What can you tell us about market trends?
GUARANTEED: When switching from Conventional Manufacturing (CM) to Additive Manufacturing (AM), the certification requirements imposed by the part’s severe operating conditions obviously need to be considered when assessing the business case. Depending on the criticality level of the component, certification might impose a substantial amount of destructive test samples to be produced alongside the actual part. Through our process control software, Guaranteed is able to ensure part performance which significantly reduces the number of expensive trial-and-error loops. Being involved in various collaborative projects aiming at establishing clear certification guidelines for the use of AM in oil & gas, maritime, rail and mining industries, Guaranteed is driving this further to turn certification into an inherent part of our quality assurance framework. Process qualification, rather than single part qualification, will broaden the portfolio of AM parts and components, to achieve faster qualification and/or certification than nowadays. In close partnership with leading universities, Guaranteed is developing the next generation of WAAM technology. The latter will allow deposition speeds to be increased even further without compromising on quality while dynamic mechanical properties will be enhanced beyond those of forged material by in-process microstructural manipulation technologies

E.E: What are the most innovative products marketed?
GUARANTEED: For very large parts or failures occurring in remote areas, the costs and logistics involved in dismantling and transporting the damaged part might become prohibitive. To resolve this issue, Guaranteed developed a “mobile WAAM additive repair service” which allows on-site or even in-situ repair or remanufacturing to be achieved
E.E: What estimations do you have for 2023?
GUARANTEED: As guidelines and standards for AM-produced parts have become a reality, Guaranteed will invest in their implementation in 2023, aiming for both the standard ISO9001 as well as AM specific site certification. Along those lines we’ll also keep pushing our efforts when it comes to using process monitoring and process control combined with AI/ML to facilitate qualification and certification processes.
During 2023, we will also implement further enhancements of the technology we use, which will allow to increase deposition speed as well as perform enhanced in-situ microstructure control during deposition.
Driven by the market, we are also exploring several options for expanding both our capacity as well as geographical footprint.