Herbold Meckesheim GmbH is leading manufacturer for plastic recycling machines. Worldwide, their plants and machines contribute to a significant reduction in plastic waste and increase the amount of plastic in circularity. Both production waste and post-consumer plastics are processed. Recycling machines from Herbold Meckesheim are used in fine grinding, raw material recovery and material preparation of various industrial processes. To design the equipment to the customers’ needs the company runs its own pilot plant.
Today, Herbold Meckesheim is managed in the fourth generation by Karlheinz and Werner Herbold. More than 220 employees at the headquarters and the staff of the international agencies accompany machines that are custom-made to fit the requirements from the conception stage through commissioning to the end of their commercial use.
Interview with Achim Ebel, Vice President Sales at Herbold Meckesheim GmbH
Easy Engineering: What are the main areas of activity of the company?
Achim Ebel: Plastic products at the end of its life, whether post-industrial or post-consumer, are often contaminated. To process this valuable resource in quality for reuse is the goal of the equipment produced by Herbold Meckesheim. For this purpose, the company develops and manufactures recycling lines for various plastics. With its modular system solutions for automated plants, the machine builder can quickly and flexibly respond to customer requirements.
E.E: What’s the news about new products?
A.E: Washing lines and hot wash for plastics are in focus of product development. Herbold Meckesheim supplies all substantial machines out of their own production in Germany. Additional equipment, such as automatic flake sorting at the end of the washing lines, can also be added. The modular design allows to conceptualize a plant tailor-made from simple needs up to flake qualities for direct food contact.

E.E: What are the ranges of products?
A.E: Herbold Meckesheim conceives and builds the components of recycling plants. The first process stage of a washing line is often a heavy-duty shredder. Shredders and granulators are usually followed by the multi-stage pre-washing unit, which captures coarse impurities and reduces mineral fraction. Friction washers are used to dewater and clean the ground material, for example from films or rigid plastics. Odors and adhesives can be removed by hot washing with adjustable temperatures and dwell time and with the addition of suitable detergents. Mechanical drying and two-stage thermal dryers complete the process in such a way that only low residual moisture remains. For materials with poor flow properties, a silo is appropriate.
E.E: At what stage is the market where you are currently active?
A.E: The market for recycling equipment is constantly growing. In particular, plants that produce material close to virgin quality and for use in the food sector are in demand. In addition, awareness of the circular economy and product responsibility is increasing. The UN estimates that around 400 million tons of plastic waste are generated annually, of which around ten million tons end up in the oceans. As a result, public pressure to do something about marine littering is also increasing.
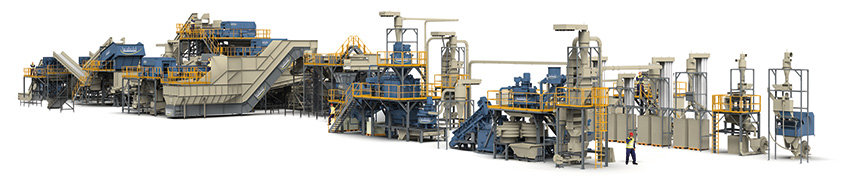
E.E: What can you tell us about market trends?
A.E: Due to public pressure, promotional measures for plastic recycling are more and more widespread. In addition to the industrialized countries, the recycling of plastics is also increasingly becoming the focus of interest in emerging countries. Even companies previously unfamiliar with the subject are entering the recycling market. In particular, washing lines that produce high-quality recyclates are seen as a promising investment for the future. In demand are highly automated plants which, on the one hand, avoid downtimes and keep personal costs low and, on the other hand, can cope with heterogeneous feed materials.
E.E: What are the most innovative products marketed?
A.E: The hot washing system for polyolefins is one of the product innovations of Herbold Meckesheim. Hot washing results in qualities of recyclates that are suitable for use in the food sector. The recycling lines are built around the hydrocyclone stage with its high density separation – due to the strong centrifugal forces in the hydrocyclone, a separation effect is achieved that exceeds conventional processes by a factor of 15.

E.E: What estimations do you have for 2022?
A.E: Herbold Meckesheim’s production capacities for 2022 are already fully booked. Despite rising prices and the global difficulties in the form of interrupted supply chains and bottlenecks of raw materials and precursors, the company also expects growth for 2023. The interest in recycling solutions remains high. Thanks to its modular plant and process step concepts, Herbold Meckesheim is able to flexibly and quickly respond to customer requirements.