Servus Intralogistics was founded in Austria in 2005 and is the world’s only intralogistics provider for the interface-free automation of the entire warehouse and production logistics. Around the core product, the Autonomous Robotic Carrier (ARC), they develop, plan and implement customized concepts and turnkey solutions for a variety of industries, e.g. for the automotive & supplier industry, food industry, trade & e-commerce, production & logistics, medicine and healthcare. The export rate is 80 %.
The Servus modular assembly kit serves as the basis for customer-specific solutions. It offers all necessary components: from the Servus transport robot to automatic small parts storage (ASRS), route systems, connections to incoming goods, picking station, production connections and outgoing goods, to software, communication and 24/7 service.
Interview with Christian Beer, CEO Heron Innovations Factory GmbH (The parent company of Servus Intralogistics).
Easy Engineering: What’s the news for 2021 about new products?
Christian Beer: The Servus-Cube is one novelty: the warehouse, which can be used both centrally and decentrally, enables simple storage and retrieval processes. The basis is a modular rack, which can be extended in length as required. A Servus-Lifter moves on the top shelf level and simultaneously serves the warehouse as well as the storage and retrieval station. This allows the storage bins to be lined up between the levels with a minimum of space so that no space is wasted. This enables highest storage density in the smallest space. The automated logistics unit functions both completely autonomously as a plug-and-play solution and integrated into a higher-level, already existing intralogistics system. The Servus-Cube can be connected in a variety of ways. Manual storage and retrieval stations, the collection of goods via a pre-zone as well as fully automated variants with the Servus transport robot, the Servus lifter or an AGV are possible.

E.E: What are the ranges of traded products?
C.B: We design and construct fully automated intralogistic systems. These range from Servus transport robots, ASRS, route systems, assistants and load handling devices to software, communication and direct connections. Our systems are designed exactly to the needs of the respective customer and produced in our company. The clou: the Servus System is completely scalable. If, for example, more performance or a higher storage capacity is required or if additional areas are to be connected to the system – Servus Intralogistics enables all these adjustments at any time – today and in the future.
E.E: At what stage is the market where you currently are active?
C.B: The intralogistics market has been on the upswing for years. Intralogistics is becoming increasingly important, especially for production companies, not least because batch sizes are constantly decreasing while at the same time the number of variants is increasing. In recent years, the focus has been primarily on optimizing production processes, which in many cases has led to additional logistics costs. This means that while on the one hand assembly costs have been reduced, on the other hand logistics costs have increased. Automation, Smart Factory and Industry 4.0 are the big issues currently affecting the market. Speed, a high degree of automation and efficiency are in demand. In the coming years, the success of manufacturing companies will be increasingly defined by these factors. Without automated intralogistics it will be increasingly difficult for companies to remain adaptable and thus competitive.

E.E: What can you tell us about market trends?
C.B: The trend is still towards the networked factory, the Smart Factory. Virtual reality, augmented reality, artificial intelligence and machine learning will gain even greater influence here. And not only in production plants: There are other sectors in which fully automated intralogistics solutions will contribute to the efficiency and success of companies: for example, retail and everything to do with medicine and healthcare.
Sustainability is also on everyone’s lips. The aim is to save space, resources and time through automation, not to automate waste.
E.E: What are the most innovative products marketed?
C.B: Our Autonomous Robotic Carrier (ARC) was the first autonomous, intelligent transport robot on the market and is very innovative as an autonomous and intelligent product.
This year we added the Servus-Lifter, another version of our ARC. The world’s first two-part transport robot moves horizontally on one level and can extend its load handling device vertically up to a length of 5 meters. This is the first time that the intelligent transport robot operates all stations in the warehouse and in production fully automatically with totes, cartons or trays on different levels or transports material into the warehouse. And all this without touching the floor. The Servus-Lifter moves “overhead” under the hall ceiling. This saves valuable production space.
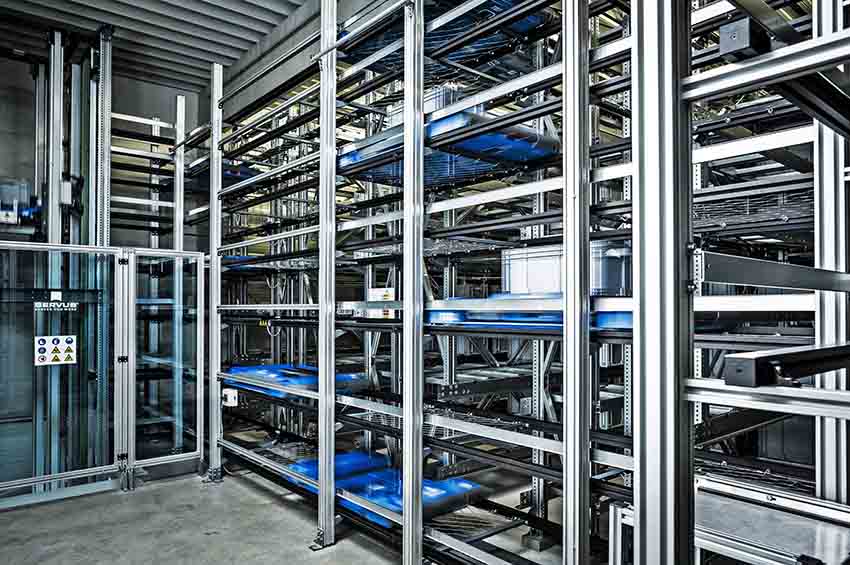
E.E: What estimations do you have for 2021?
C.B: 2021 will be a very successful year for us. The order situation is very encouraging. In addition to our core business, the installation of fully automated logistics systems for warehouse and production logistics, we will also continue to grow in the retail & e-commerce sector with our high-performance automated small parts warehouses. We will also grow strongly, among other things, because of our “very clean and low-noise” technology, also in the medical and healthcare sector, with its high requirements for cleanliness and tidiness.