With the WinMax CNC control system, a Windows-based operating system and an international interface standard, HURCO machining portals have the right technology for the increasing digitalisation of manufacturing. The mechanical engineering company supports its customers with expert advice during custom implementation of automated solutions, data management or remote maintenance.
The Head of HURCO Anwendungstechnik, Sebastian Herr, spoke with us about how customers are meeting the challenges posed by technological evolution.
Easy Engineering: HURCO customers hail from a wide variety of sectors extending from the automotive industry to medical technology. What are you hearing from customers regarding their sentiments in the current atmosphere?
Sebastian Herr: There is no doubt that we are going through an economically challenging period. At the same time, we are currently witnessing a positive trend toward guarded optimism among our customers, who are primarily medium-sized firms and contract manufacturers.
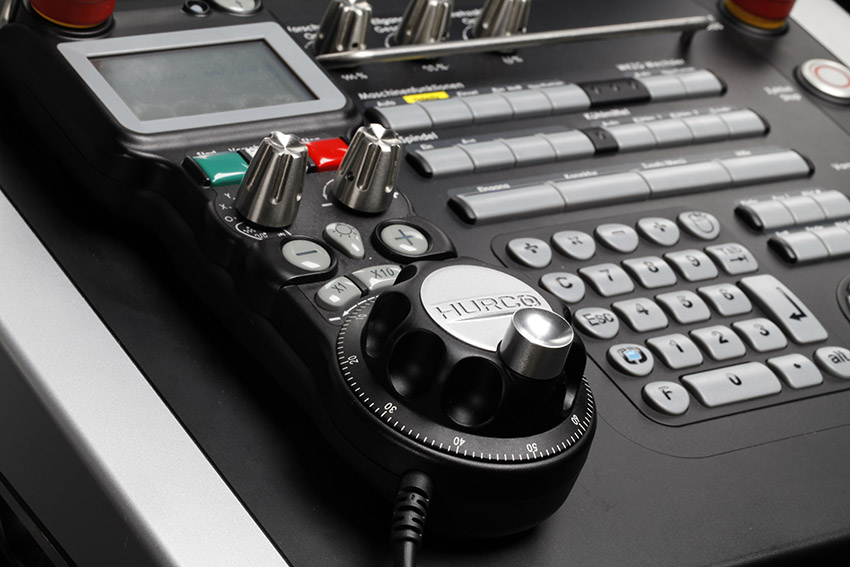
E.E: HURCO is committed to close and collegial customer contact, meaning that its application technology closely reflects the conditions being encountered by manufacturers. What kind of advice are you providing under current conditions?
S.H.: Of course, we are continuing to pursue development work in the automation and Industry 4.0 sectors, and this is reflected in our customer consultations. The HURCO control system fits in extremely well. Our Windows-based control system offers an essentially intuitive experience for everyone who has grown up with computers. This means that programming tasks can be performed by operators with minimal previous experience. Our goal is to show customers how they can enhance the productivity and profitability of their manufacturing processes to effectively encounter more difficult market conditions. Small-scale automated solutions and logical data management concepts are elements in this effort. Example: MDE BDE, which equates with monitoring and evaluating machine and operating data. This allows customers to observe the operating times for components at the individual stations. They have access to documentation, including programming and processing times, downtime data, error messages, etc. This information furnishes manufacturers with substantially enhanced planning precision for more reliable calculations and accurate price quotations. At which we are already diving into Industry 4.0.
E.E: Now that we have mentioned Industry 4.0, how does the WinMax control system perform in this context?
S.H.: Here I can refer to our Windows-based system while also calling attention to the internationally applicable interface standard provided by the WinMax control system. This opens up a wide array of possibilities. For instance, access to something called the “extended shop floor,” affording customers real-time access to their machinery, is available on request. This functionality is available with every WinMax machine and can be used with any mobile device, whether it be a cell phone or a tablet, regardless of its operating system, as well as with all Internet browsers.
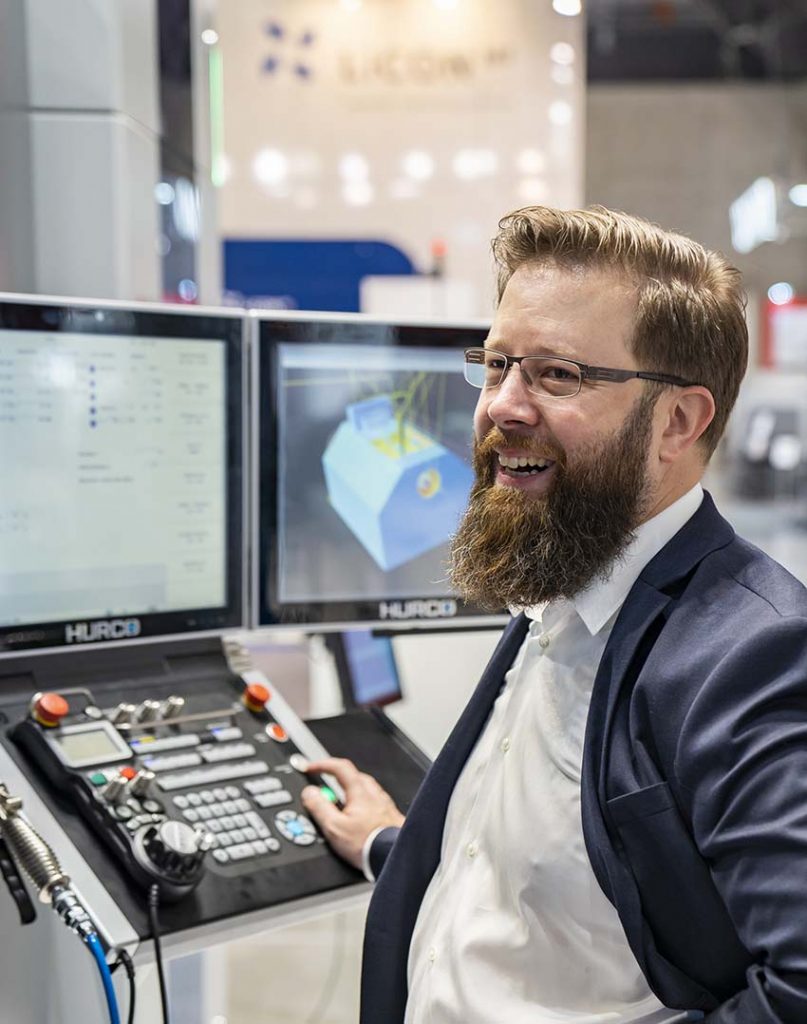
E.E: Application of new information technology can also be used to conduct remote service and remote diagnosis on machines and assemblies. How far along are your customers in this area?
S.H.: Since HURCO machines are factory-equipped with an operational data monitoring system, the remote servicing option is a given. Many of our customers are already exploiting the resulting possibilities to implement Industry 4.0 in their production processes.
E.E: What kinds of technical requests are you still receiving?
S.H.: Components are becoming increasingly complex, even as tolerances continue to shrink. Customers whom we have been supporting for years now need to work to increasingly stringent levels of precision. Thus, the current focus of the demands placed on any machine lies with precision. Key word: 5-axis machining. Whenever possible, the workpiece should be completed in a single processing round. We are collaborating with partners in machining technology to evolve processes in which a 5-axis machine will complete all six sides of a part all the way down to a thin casting tab. The only remaining operation is to break off this casting tab and grind the remainder to a smooth surface. The workpiece is finished. This is our obvious direction.
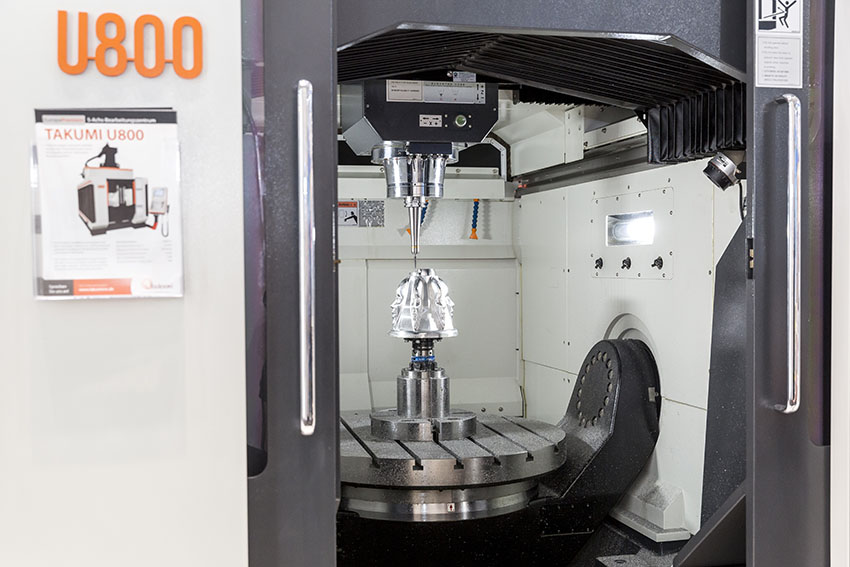
E.E: HURCO is collaborating with machine tool manufacturers as well as robotics firms. What considerations are motivating these moves?
S.H.: Many medium-sized manufacturing firms are still operating exclusively in shifts staffed by employees. This makes it difficult for them to remain competitive in the international arena. At the same time, a great deal of logistical effort is needed to produce parts in low and mid-volume production series. A machining center can only achieve maximum productivity when programming, tool selection, machining conditions and loading technology all flow together to form a single, synergistic whole. This is why we are embarking on strategic partnerships with renowned machine tool manufacturers and robotics firms. This, in turn, allows us to provide our customers with specific solutions for an array of highly variegated manufacturing requirements during consultations on application technology.