HWS CONCRETE TOWERS (HWS) was founded to introduce innovative PRECAST CONCRETE solutions in the wind energy market.
The founders are Civil and Structural Engineers renowned in Spain for their extensive worldwide experience in design and construction of large precast concrete structures, like bridges. For this reason, in 2005, GAMESA wind turbine manufacturer reached us asking for a new design of a 120 m high concrete tower for one of the largest wind turbines in the market (G10-4.5 MW). During that project, they foresaw the upcoming challenges of the wind industry and decided to contribute to the sustainable growth of the wind industry by perfecting this ‘old’ precast technology to fit and enhance various aspects of the construction and maintenance of wind turbines.
Since HWS’ creation in 2015, they have developed several disruptive products related to wind foundations and towers made in precast concrete, as well as climbing cranes for assembly of towers and complete wind turbines. Having 11 patents awarded, HWS has extended 6 to commercialize its products all over the world.
Interview with Mariano Abadia, CEO & Co-founder & Amaia Martínez, CTO at HWS CONCRETE TOWERS.
Easy Engineering: What are the main areas of activity of the company?
Mariano Abadia & Amaia Martínez: HWS offers new solutions for cost-effective construction of wind substructures (foundation and towers) and assembly of new generation wind turbines (>5MW). HWS’ most relevant products are:
- AirCRANE: A self-climbing crane for installation and maintenance of wind turbines at unlimited height.
- AirBASE: Easy to assemble (‘Lego’-like) and very cost-effective precast concrete foundation that can also be used for repowering of wind farms.
- AirTOWER: Several concrete (full or hybrid) tower concepts, including a “supertall” (up to 220 m) precast tower.
In addition, we provide specialized engineering and consultancy services related to design and construction of precast concrete structures for the renewable energy market. This includes studies of industrialization and serialization of manufacturing and assembly processes of the structures.
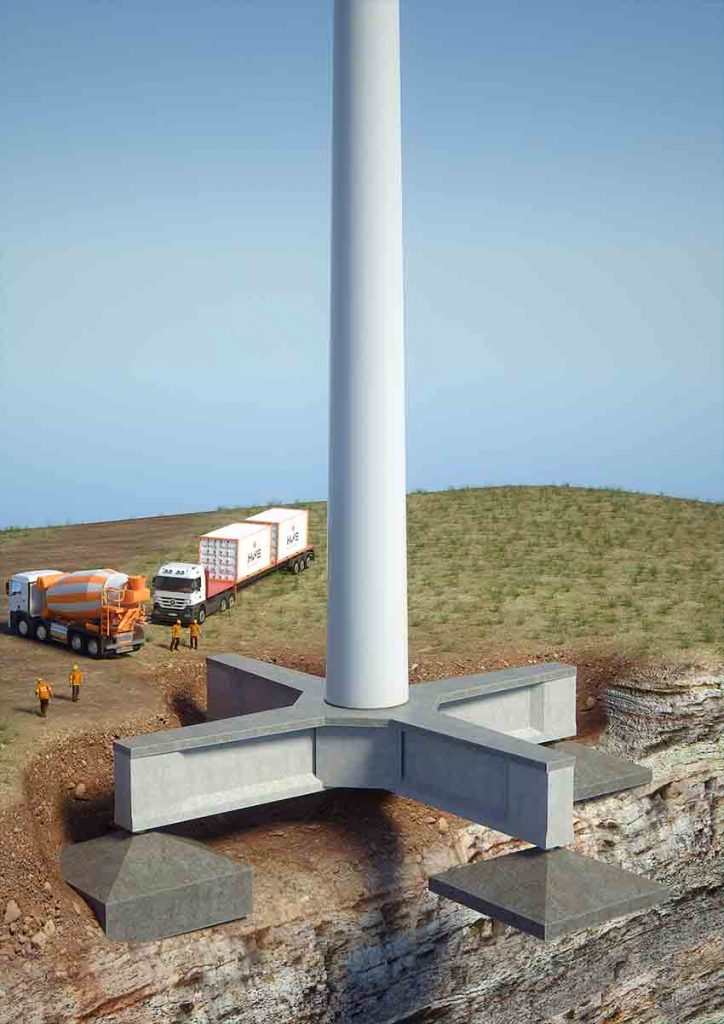
E.E: What’s the news about new products?
Mariano Abadia & Amaia Martínez: HWS’ innovative products defy the technical and economic limitations of traditional construction technologies used in the wind sector by enabling the installation of bigger wind turbines (> 5 MW) at greater heights cost efficiently. This way, we contribute to the reduction of the levelized cost of wind energy (LCOE):
The higher the wind turbine, the more and better-quality wind you can harvest, and the more energy is produced. Our supertall tower combined with our climbing crane allows to build at heights of 220 m and beyond, leading to an increase in the generated energy of ~15%.
Through our foundation, tower, and wind turbine assembly methodology, savings up to 50% can be reached, which leads to CAPEX (capital expenditure) reduction.
Our precast structures require of less maintenance and have longer lifetime, directly impacting on the OPEX (operational expenditure).
Moreover, all our concepts are environmentally friendly and contribute to reducing the carbon footprint of wind farm construction.
E.E: What are the ranges of products?
Mariano Abadia & Amaia Martínez: The range of products that HWS offers cover the whole support structure (foundation and tower), as well as the installation methodology of the wind turbine. Although the products are independent from each other, they could also be implemented together.
In terms of substructure, we have patented and developed a cross-shaped precast concrete foundation, the AirBASE, which is easy and quick to assemble. This structure reduces concrete volumes by 45% and can be applicable to any wind turbine size and soil condition. As for the tower, HWS counts with a portfolio of several full concrete and hybrid (concrete at the bottom and steel at the top) towers. Our latest development is the AirTOWER, the “supertall” tower version that can reach heights of 220 m thanks to an effective arrangement of the post tension cables.
Finally, our AirCRANE system is a brand-new patented technology that can ASSEMBLE any wind turbine at theoretical infinite height. This crane climbs along the exterior of the tower, gaining altitude in parallel to the tower construction. It could also be used in a later stage for MAINTENANCE of the wind turbine.
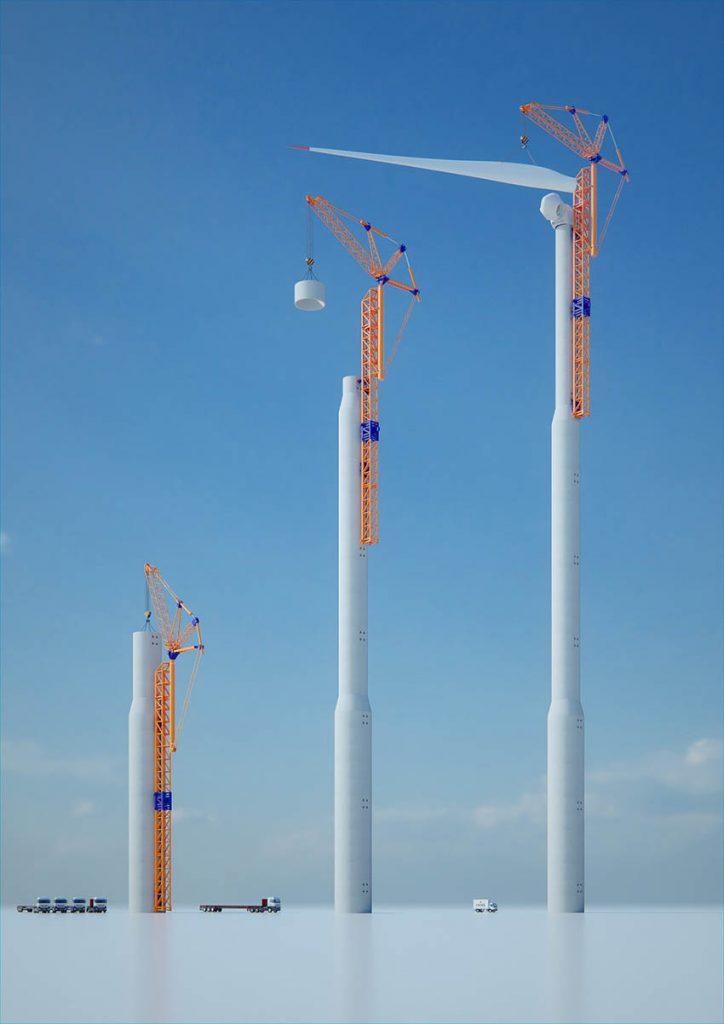
E.E: At what stage is the market where you are currently active?
Mariano Abadia & Amaia Martínez: According to the Global Wind Energy Council (GWEC), total global wind power capacity is now up to 837 GW, helping the world avoid 1.2 billion tons of CO2 annually. Despite the impacts of COVID-19, 2020 and 2021 were the best years in history for the global wind industry with 93-94 GW of new annual capacity installed. And to achieve Paris climate goals, the global cumulative installed capacity of wind power needs to grow ‘x4’ by 2030.
In terms of technology, the most common installed wind turbines have rated powers of 3-4 MW in onshore and ~8 MW in offshore. But every year bigger wind turbines are appearing: 6-7 MW onshore turbines and 15 MW offshore were released in 2022.
Currently the most widely spread tower technology is 100-120 m high tubular steel tower. However, towers of 165 m high are already being offered at commercial scale. To install these towers, 500-800-1,000 t lifting capacity traditional mobile and crawler cranes are being used.
E.E: What can you tell us about market trends?
Mariano Abadia & Amaia Martínez: For reducing wind energy production cost, the market trend is to increase in size the Wind Turbine Generators (WTG), both ON-Shore and OFF-Shore.
This WTG size increase includes:
- Hub Height (HH),
- Rated Power in MW, and
- Blade length or rotor diameter
By 2030, we might see 200 m high 8 MW onshore wind turbines with 220 m rotor diameter. This way, more energy can be generated at a lower cost.
As bigger and heavier wind turbines are appearing in the market, and to ease logistics and assembly constraints, lower cost, and address local content requirements, new tower technologies are gaining prominence. Hybrid towers—with the lower section in concrete and the top part in steel—are becoming the alternative to reach higher, harness greater wind speeds, and lower the cost of scaling up the tower.
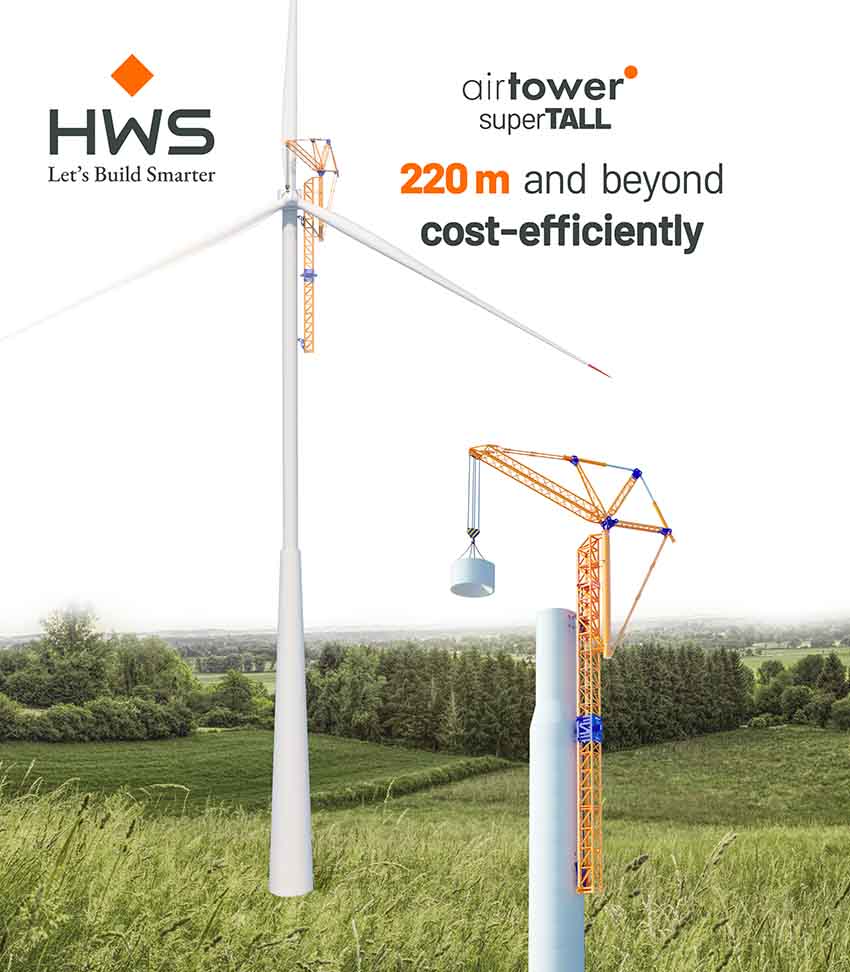
E.E: What are the most innovative products marketed?
Mariano Abadia & Amaia Martínez: Among the most innovative products marketed in the wind industry related to tower structures, we believe that wooden towers and 3D printed towers stand out. However, these technologies are still in a very early stage of development to be used at commercial scale. HWS has received inquiries from both to analyze the applicability of our AirCRANE self-climbing system in these types of towers.
In terms of foundations, we believe that multi-point supported structures, like our AirBASE, are breaking the traditional scheme of building foundations. This innovation is becoming more and more relevant in terms of material volume savings and on-site time reduction as wind turbines get bigger.
On the other hand, several innovative assembly methods are appearing in the market as an alternative to existing expensive, huge, and scarce mobile cranes required to install wind turbines at heights of more than 160 m. Some of the alternatives are: self-climbing cranes, like the AirCRANE, self-erecting systems, telescopic towers, etc. But at the moment only ENERCON’s LCC140 self-climbing crane is in the market at commercial scale.
E.E: What estimations do you have for 2022?
Mariano Abadia & Amaia Martínez: 2022 is shaping up to be a successful year. The market is now demanding new solutions like our AirBASE, AirTOWER, and AirCRANE, to build bigger wind turbines cost-efficiently at heights where traditional technologies cannot reach. Moreover, the drastic steel and logistics price increase has become a powerful catalyst to grow interest in precast concrete structures and local content. On the other hand, our products are all ready, validated, and certified, to be deployed in the market. Hence, we believe that after years of research and development, this year we will be able to step up and bring our products at commercial stage.