IMG Plastec is supplying a compact size of bead foam manufacturing facility specialized in EPP & ETPU to realize in-house bead foam production, leading the paradigm shift in the particle foam raw material production system.
Most of bead foams are foamed and molded at the factory of steam chest molders. On the other hand, particle foam such as EPP and E-TPU is exclusively supplied by some of the world’s largest companies, so the steam chest molders must purchase foamed beads at high price to make their own products. However, implementation of IMG’s direct bead foam production system can make it possible for users to build their own sustainable raw material supply system and, thereby, to save the production cost.
IMG’s production system consists of two lines of process, one is mini pellet extrusion line to make long PP strands and cut into mini pellets, and another is autoclave expansion line to foam those mini pellets by applying heat, steam, and CO2. IMG’s total solution service for EPP bead foam production includes a customized design of the plant considering user’s production environment, installing the equipment, training the operators, providing technical advice for uniform quality of the product, supporting remote controlling service for errors, conducting sample evaluation and quality control, and networking with potential customers. By transferring their technology and know-how, the company supports the user who is even not familiar with EPP bead foam to quickly achieve stabilization in operation and to start massive production of satisfying quality of bead foam.
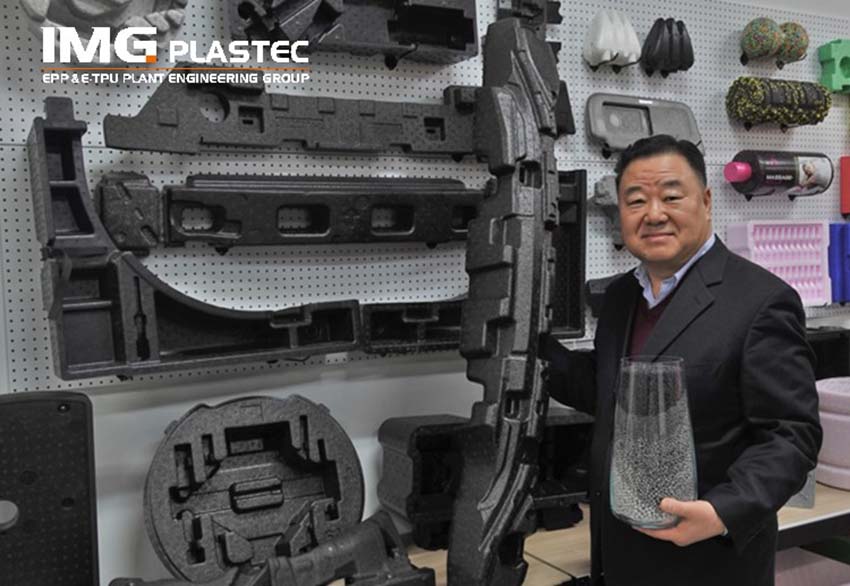
IMG Plastec has both theorical expertise and delicate skills in operation through over 30 years of experiences in particle foam bead industry. Especially, IMG is working with the one of the greatest staffs from each field in a team, including the professors in Microcellular Engineered Plastics, technical advisor and the plant manager who worked as the general director in big corporate in Korea and a business development representative in the United States who was the former president of one of the leading companies SEKISUI.
Currently, IMG Plastec has EPP production plant in China and Russia, and Uzbekistan plant is on the verge of starting mass production in this year.
Interview with Young-guk Song, CEO of IMG Plastec.
Easy Engineering: What are the main areas of activity of the company? What are the ranges of products?
Young-guk Song: EPP bead foams are used in versatile industries such as automotive, insulation, packaging, home application, sporting goods, protective gears, toys and so on. In automotive, typically, reducing weight of car was the problem to be solved as the electric cars became common. EPP is a light weight material that has a great shock absorbing property at the same time, therefore, it is used to replace the existing heavier materials to achieve both lightweight and safety enhancement of the car.
EPP is non-toxic but durable, so it is widely used for packaging products both for food and goods. EPP packaging can keep the temperature of food with an average temperature loss of less than ±1℃ per hour within a range of -40°C to +120°C. Also, EPP package can have customized design that fits the shape of your product that enables to store and transport the goods without damages, and its anti-static feature is good for electronics products.
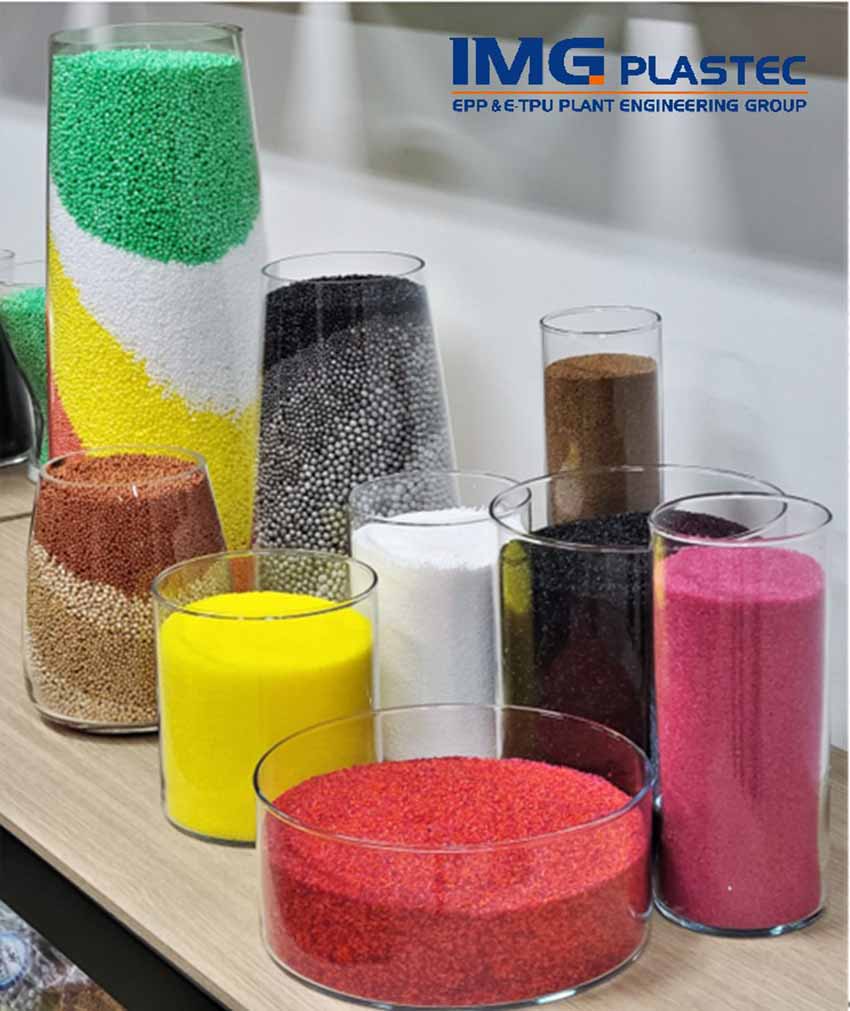
Another main product is NF EPS (Non-flammable) insulation board production system and fire-retardant coating liquid technology. NF EPS insulation board (imgNF) is a perfect substitute for normal EPS board and stone wool in terms of a greater performance to prevent spread of fire and toxic gases in fire accidents, and both safety and workability for workers in construction. In addition, our NF EPS board cooperated with European partner got VKF (Cantonal Fire Insurance Association in Switzerland) approval that the buildings of medium height (up to 30m) can be demonstrably designed without fire barriers(material to prevent spread of fire between floors). Since the government in several countries such as the United States, Israel, Switzerland and so far, have announced strict fire prevention regulations and test standards for building insulation materials, IMG’s NF EPS technology is getting in demand and the market is steadily growing.
E.E: What can you tell us about market trends?
Y.G.S: Localization of EPP bead foam production is no longer a distant future. After covid-19 outbreak, ocean transportation cost has skyrocketed day by day, which is a critical factor that raises the production cost and a great burden to steam chest moulders. Therefore, the users are turning to have their own self supplying system. Under this situation, IMG’s direct production system can help them save their budget significantly by up to 40~60% by eliminating ridiculously high purchasing price and unnecessary transportation cost for bead foam supply. Therefore, the users finally can manage their production without worrying supplying cost and shipping schedule.
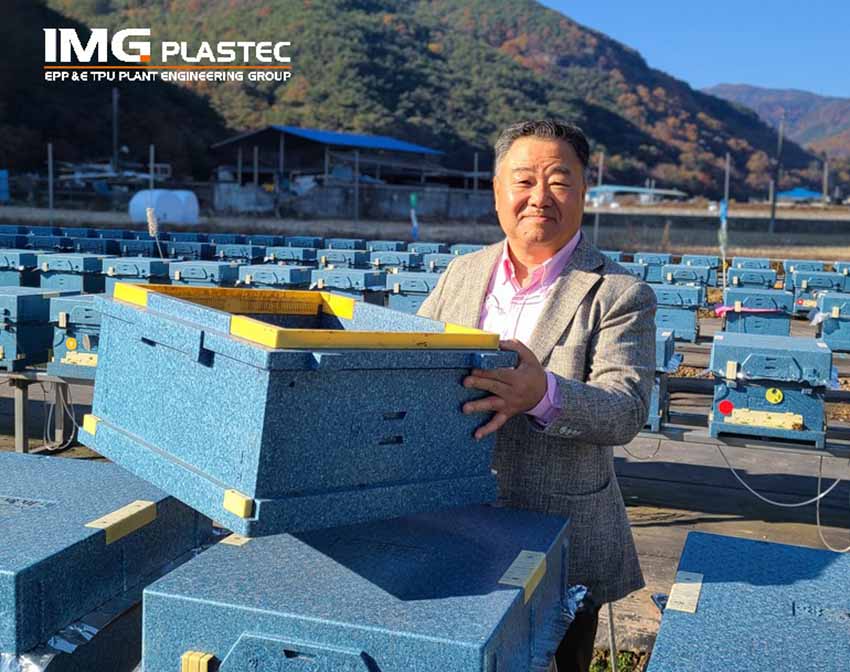
More specifically, one of the promising markets in bead foam industry is EPP sound insulation board, which is deeply related to the global trend to reduce the use of plastics and protect environment. Original sound insulation board is made of Polystyrene (PS) and this material is one of the major causes of soil pollution in terms of one-time use property. Additionally, PS is vulnerable to contamination, easily cracked, and generates the toxic gases for both human and environment when touching with fire. For those environmental and performant reasons, the material for sound insulation board between floors and walls is getting replaced with EPP in building construction. One step ahead of this trend, IMG developed a semi non-combustible EPP sound insulation board by applying fire-retardant technology from imgNF EPS board, preserving the unique and excellent EPP’s mechanical properties.
Environment friendly movement is observed in floating buoy as well. In case of South Korea, the government had announced the plan to replace all of Polystyrene buoys used in fish farm with EPP. EPP floating buoy is durable not like EPS easily rotten or cracked, also it doesn’t contain the heavy metals. The number of the buoys to be replaced is estimated around 55millions in Korea, and related market is growing fast based on this national project.
E.E: What estimations do you have for 2022?
Y.G.S: As pandemic situation that dominated our life for more than 2 years seems coming to an end, IMG Plastec will resume the cooperative projects that have been delayed and spur the introduction of EPP bead foam production system to target countries.
To be more specific, by the end of this year, it is expected to build a domestic autoclave system in lab-scale to research and develop other types of polymer bead foams along with research to improve the quality of bead foam. Meanwhile, overseas, we are working on our new production system in Uzbekistan, aiming for massive production in the end of this year. Furthermore, we will focus on Indian market where the demand for direct bead foam production is as high as dependence on imports of beads to achieve localization of bead foam supply and expand the boundary of our business.
IMG Plastec Co., Ltd.
EPP/ETPU bead production system
imgNF(non-flammable) insulation board
Linkedin: https://www.linkedin.com/in/img-plastec-co-ltd
Email: contact@imgplastec.com
Tel.: +82 70 4281 5502